Are You Looking for a Pallet Flipping Machine That Significantly Boosts Warehouse Efficiency and Ensures Safety?
The need for efficiency and safety in warehouse operations has never been greater. With increasing pressure to streamline logistics and reduce downtime, companies are turning to innovative solutions like pallet flipping machines to enhance productivity. But how do you determine if a pallet flipping machine is the right fit for your warehouse?
This article explores the key factors to consider when selecting a pallet flipper. From handling diverse pallet sizes to ensuring compliance with safety standards, you’ll find everything you need to make an informed decision. Whether you’re considering a fully automatic pallet flipper or a semi-automatic model, this guide provides valuable insights.
Let’s dive into the essential aspects of pallet flipping machines, focusing on their impact on operational efficiency, safety, and long-term investment value.
1. Can It Efficiently Handle Various Pallet Sizes and Weights?
1.1 Diverse Pallet Dimensions and Why They Matter
In today’s warehouses, versatility is critical.Pallet flipping machines are engineered to handle an extensive range of pallet dimensions and weights, ensuring seamless operation across a variety of industries. From lightweight pallets used in the food industry to heavy-duty pallets designed for construction materials, these machines are built to adapt to your specific requirements, no matter the application.
A reliable pallet flipper is designed to accommodate different pallet versions and sizes, making it a versatile solution for warehouses managing diverse inventory. Whether you’re flipping standardized wooden pallets, durable plastic pallets, or heavy-duty steel pallets, modern machines ensure consistent performance. For example, a pallet flipper with adjustable clamps and customizable settings can efficiently handle materials ranging from lightweight 500 kg loads to massive 2,000 kg industrial pallets without compromising safety or efficiency.
This adaptability extends to unique pallet configurations, such as half pallets, EURO pallets, or custom-sized pallets used in specialized industries. Machines designed with modular features and multi-material compatibility not only ensure operational efficiency but also reduce the need for manual adjustments, saving valuable time and resources.
By choosing a machine capable of working with various pallet sizes and materials, warehouses can streamline operations, enhance productivity, and minimize the risk of product damage—making these machines an indispensable tool in modern logistics.
1.2 Technical Specifications and Weight Capacity
Modern pallet flippers typically accommodate pallets ranging from 800 mm to 1,200 mm in size and weights up to 2,000 kg. Machines with adjustable clamps and modular designs offer flexibility, allowing operators to manage irregularly sized pallets efficiently.
Model | Min Size (mm) | Max Size (mm) | Weight Capacity (kg) |
---|---|---|---|
Standard Flipper 2000 | 800 | 1,200 | 2,000 |
Heavy-Duty Flipper 3000 | 1,000 | 1,500 | 3,000 |
1.3 Enhancing Efficiency with Customizable Features
A machine’s ability to adapt to your operational workflow is equally important. Features like programmable settings and sensor-based adjustments streamline processes, reducing manual intervention. For warehouses with diverse product lines, such customization is a game-changer.
1.4 Two Fact Statement
- True: Modern pallet flippers can adjust automatically to handle irregularly shaped pallets.
- False: All pallet flipping machines are designed for only one standard pallet size.
2. How Does Its Flipping Speed and Throughput Translate into Tangible Benefits?
2.1 Improving Throughput with Faster Flipping
Time is money in logistics, and every second counts. Pallet flipping machines significantly enhance productivity by reducing the time spent on manual flipping. The flipping speed, typically ranging from 15 to 30 seconds per cycle, directly impacts your throughput.
2.2 Real-Life Efficiency Gains
For example, a warehouse operating with a manual flipping process handles 100 pallets per day. By switching to an automatic pallet flipper, the same warehouse can manage 400 pallets daily, increasing throughput by 300%.
Flipping Method | Daily Capacity (Pallets) | Operational Hours | Labor Required |
---|---|---|---|
Manual Flipping | 100 | 8 | 4 |
Automatic Flipper | 400 | 8 | 1 |
2.3 ROI and Long-Term Benefits
The increased speed and reduced labor costs contribute to a faster return on investment (ROI). Businesses typically recover the cost of an automatic pallet flipper within 12-18 months, depending on operational volume.
2.4 Two Fact Statement
- True: Automatic pallet flippers improve operational throughput by over 300% compared to manual flipping.
- False: Flipping speed has no direct impact on ROI for warehouses.
3. Does It Meet Safety Standards and Certifications?
3.1 Safety Features That Protect Your Workforce
Safety is a top priority in warehouse operations, and modern pallet flippers are equipped with advanced features to protect both workers and products. Emergency stop buttons, anti-slip platforms, and enclosed flipping chambers are standard safeguards that minimize risks during operation.
Innovative additions, such as light beam sensors, further enhance safety by halting the machine if an object enters the flipping area. Interlock mechanisms ensure the equipment operates only when all safety barriers are securely in place. Automated systems with programmable logic controllers (PLC) manage precise operations, reducing human error.
Remote control capabilities allow operators to manage the machine from a safe distance, while integrated sensors monitor load balance and positioning, automatically pausing operations if anomalies are detected. These features collectively create a safer, more efficient working environment, preventing accidents and ensuring reliable performance.
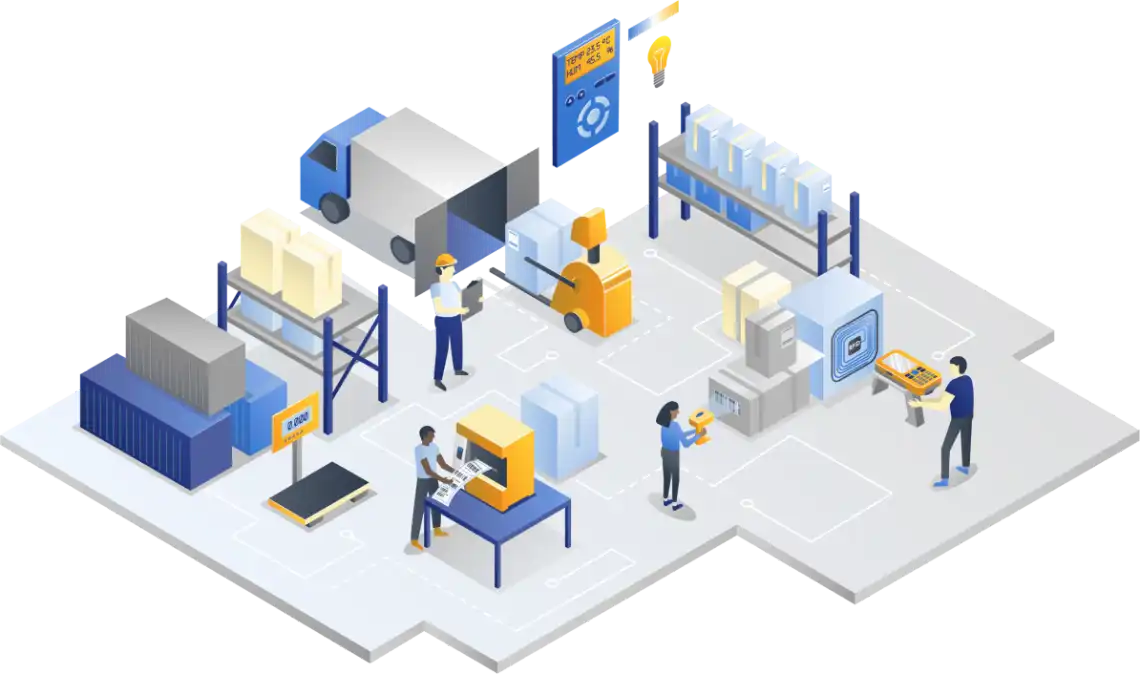
3.2 Certifications and Industry Standards
When choosing a pallet flipping machine, verify compliance with certifications like CE, ISO 9001, or OSHA standards. These certifications ensure that the equipment meets international safety and quality benchmarks.
Certification | Description | Importance |
---|---|---|
CE | Compliance with European safety directives | Ensures the machine meets high safety levels |
ISO 9001 | Quality management certification | Guarantees consistent manufacturing quality |
OSHA | Workplace safety compliance (U.S.) | Reduces workplace hazards |
3.3 Importance of Routine Safety Checks
Even the best machines require regular maintenance to uphold safety standards. Conducting bi-annual inspections and replacing worn-out parts, such as hydraulic seals, ensures long-term reliability.
3.4 Two Fact Statement
- True: Machines with CE and ISO certifications provide a higher level of operational safety.
- False: Regular maintenance is optional for certified pallet flipping machines.
4. What Are the Ongoing Maintenance and Upkeep Costs?
4.1 Understanding Routine Maintenance Requirements
Like any equipment, pallet flipping machines require consistent upkeep to remain efficient. Routine tasks include lubricating moving parts, replacing worn-out clamps, and inspecting hydraulic systems. A well-maintained machine ensures fewer breakdowns and extends the overall lifecycle.
4.2 Estimating Long-Term Costs
Maintenance costs for pallet flipping machines typically range between 5-10% of the machine’s annual operating cost. Key components like hydraulic cylinders and control panels may require replacement every 3-5 years, depending on usage.
Maintenance Activity | Frequency | Average Cost (USD) |
---|---|---|
Lubrication | Monthly | 50 |
Hydraulic Seal Replacement | Every 3 years | 500 |
Control Panel Update | Every 5 years | 1,000 |
4.3 Choosing Machines with Low Maintenance Needs
Advanced models with self-lubricating systems and diagnostic software significantly reduce upkeep efforts. These features provide real-time alerts, enabling operators to address issues proactively.
4.4 Two Fact Statement
- True: Investing in machines with diagnostic features lowers maintenance downtime.
- False: Pallet flipping machines require daily maintenance to function efficiently.
5. Does Our After-Sales Service Network and Response Time Meet Your Expectations?
5.1 The Role of After-Sales Support
Purchasing a pallet flipping machine is a long-term investment, and reliable after-sales service plays a critical role in ensuring its success. From technical troubleshooting to spare parts availability, a strong service network minimizes downtime and protects your operational flow.
5.2 Key Metrics for Evaluating Support
When evaluating after-sales service, consider factors like response time, spare parts delivery, and warranty coverage. For instance, leading manufacturers often guarantee a 24-48 hour response time for technical issues, ensuring minimal disruption.
Service Metric | Industry Benchmark | Importance |
---|---|---|
Response Time | 24-48 hours | Reduces operational downtime |
Warranty Period | 1-3 years | Covers key repair costs |
Spare Parts Availability | Within 7 days | Ensures uninterrupted operation |
5.3 Ensuring Long-Term Support
A robust support system includes remote diagnostics, operator training, and access to updated software. This ensures that the equipment remains functional even as technology evolves. Manufacturers offering extended warranties and maintenance packages often provide better long-term value.
5.4 Two Fact Statement
- True: Fast response times from manufacturers minimize disruptions in daily operations.
- False: After-sales support is only necessary during the first year of machine ownership.
6. Can It Seamlessly Integrate with Your Existing Automation or WMS?
6.1 Why Integration Matters
In modern warehouses, pallet flipping machines rarely operate in isolation. They must integrate seamlessly with existing automation systems such as warehouse management systems (WMS), conveyor belts, or robotic arms. Machines with open interfaces and compatibility with multiple software platforms simplify this process.
6.2 Features That Facilitate Integration
When assessing integration capabilities, look for features such as IoT connectivity and modular designs. These allow easy communication between the pallet flipper and other automation systems, improving efficiency. A well-integrated system can increase throughput by 20-30%.
Integration Feature | Function | Benefit |
---|---|---|
IoT Connectivity | Enables real-time data sharing | Enhances decision-making |
Modular Design | Adapts to different systems and layouts | Simplifies installation |
WMS Compatibility | Direct integration with warehouse software | Improves tracking accuracy |
6.3 Achieving a Fully Automated Workflow
By integrating pallet flipping machines into automated workflows, warehouses can significantly reduce manual intervention. For instance, connecting the machine to an AGV (Automated Guided Vehicle) ensures seamless transportation of pallets, further boosting productivity.
6.4 Two Fact Statement
- True: IoT-enabled pallet flipping machines improve data visibility across warehouse operations.
- False: Integration with existing automation systems is optional for modern pallet flippers.
7. Do We Offer Customization for Your Specific Industry?
7.1 Why Industry-Specific Customization is Crucial
Each industry has unique requirements, and a one-size-fits-all pallet flipping machine may not meet these demands. For example, the food industry requires machines made of stainless steel to comply with hygiene standards, while the pharmaceutical sector prioritizes cleanroom compatibility and precision handling. Tailoring a pallet flipper to your industry's needs ensures maximum efficiency and compliance.
7.2 Customizable Features for Diverse Applications
Manufacturers now offer extensive customization options, such as adjustable flipping angles, specialized clamps, and material coatings. Here’s a breakdown of industry-specific features:
Industry | Customization Option | Purpose |
---|---|---|
Food | Stainless steel build | Meets hygiene standards |
Pharmaceutical | Precision flipping and cleanroom compatibility | Prevents contamination |
Chemical | Anti-corrosive coatings | Handles hazardous materials safely |
Such options allow businesses to invest in a machine that aligns seamlessly with their operational goals.
7.3 Examples of Customization Success
A case study from a chemical manufacturing facility highlights the value of customization. The company integrated an anti-corrosive pallet flipper that reduced product damage by 40%, enhancing both safety and cost-efficiency.
7.4 Two Fact Statement
- True: Customized pallet flippers improve compliance with industry-specific standards.
- False: Standard machines can meet the unique requirements of all industries without modification.
8. Is the Delivery, Installation, and Training Process Efficient?
8.1 The Importance of Smooth Delivery and Installation
A lengthy or disorganized delivery process can delay operations. Reputable manufacturers provide clear timelines for delivery and installation, often completing the process within 7-14 days. Proper installation by certified technicians ensures the machine operates at peak efficiency from day one.
8.2 Comprehensive Training for Operators
Operator training is another critical step in ensuring the machine’s effective use. Manufacturers that offer on-site training programs and detailed user manuals help employees gain confidence in handling the equipment. Studies show that trained operators improve machine efficiency by up to 20%.
Training Component | Details | Benefit |
---|---|---|
On-Site Training | Hands-on guidance from experts | Reduces operational errors |
User Manuals | Comprehensive step-by-step guides | Ensures consistent usage |
Maintenance Tutorials | Proactive maintenance instructions | Extends machine lifespan |
8.3 A Faster Time-to-Value
Efficient delivery, installation, and training processes ensure that your business experiences minimal downtime. A well-organized onboarding phase translates into faster time-to-value, allowing operations to resume quickly.
8.4 Two Fact Statement
- True: Well-trained operators can enhance machine performance and minimize errors.
- False: The installation process of pallet flipping machines is always complex and time-consuming.
9. What Do Other Users Say, and Are There Successful Case Studies?
9.1 The Value of User Feedback
User testimonials and case studies provide valuable insights into the performance and reliability of a pallet flipping machine. They highlight real-world applications and outcomes, helping potential buyers evaluate if the machine aligns with their operational needs. Positive reviews often emphasize benefits like durability, efficiency, and after-sales support, while constructive feedback can reveal potential limitations.
9.2 Analyzing Successful Case Studies
One noteworthy case involves a logistics company that integrated an automatic pallet flipper into its high-volume warehouse. Before the upgrade, the company struggled with damaged pallets and inefficiencies in manual flipping. After implementing the machine, they achieved a 50% reduction in product damage and increased daily pallet handling from 200 to 600 units, significantly boosting productivity.
Key Metrics | Before Implementation | After Implementation | Improvement (%) |
---|---|---|---|
Pallet Handling Capacity | 200 pallets/day | 600 pallets/day | 200% |
Product Damage | 30% of shipments | 15% of shipments | 50% |
Labor Costs | High | Reduced | 40% |
9.3 Learning from Industry Leaders
Leading companies across industries have successfully integrated pallet flipping machines. Examples include food manufacturers improving hygiene compliance and chemical companies ensuring safety while handling hazardous materials. Real-world case studies showcase how these machines address specific challenges and deliver measurable ROI.
9.4 Two Fact Statement
- True: User testimonials and case studies are valuable tools for evaluating the practical performance of pallet flipping machines.
- False: Case studies often exaggerate the results of using pallet flipping machines.
10. How Do We Ensure Continuous Upgrades and Long-Term Operation?
10.1 The Role of Regular Upgrades
Technology evolves rapidly, and pallet flipping machines are no exception. Manufacturers offering regular software and hardware updates help businesses keep up with new features and safety standards. For example, IoT-enabled updates allow for remote diagnostics and predictive maintenance, reducing downtime.
10.2 Preventive Maintenance Plans
Preventive maintenance plans are a cornerstone of long-term reliability. These plans typically include routine inspections, part replacements, and system optimizations to extend the machine's lifecycle. Adhering to these plans reduces the likelihood of unexpected breakdowns by up to 60%.
Maintenance Activity | Frequency | Benefit |
---|---|---|
System Diagnostics | Quarterly | Detects issues proactively |
Software Updates | Semi-annually | Adds new features |
Part Replacement | As needed | Ensures uninterrupted usage |
10.3 Maximizing Lifecycle Value
By combining regular upgrades with robust maintenance plans, businesses can maximize the value of their investment. Machines that are well-maintained and consistently updated often remain operational for 10-15 years, delivering a high return on investment.
10.4 Two Fact Statement
- True: Preventive maintenance and updates significantly extend the operational life of pallet flipping machines.
- False: Once purchased, pallet flipping machines do not require additional upgrades or maintenance.
Conclusion: Making the Right Investment in Pallet Flipping Machines
Selecting the right pallet flipping machine is a critical decision that impacts your warehouse's efficiency, safety, and long-term operational success. From handling diverse pallet sizes to integrating seamlessly with automation systems, these machines offer tangible benefits that improve productivity and reduce costs.
Investing in a machine with advanced safety features, customization options, and robust after-sales support ensures that your operations remain efficient and compliant with industry standards. Regular upgrades and preventive maintenance further enhance the machine's lifecycle, delivering a high return on investment over the years.
Make the right move today—invest in a pallet flipping machine that prioritizes efficiency, safety, and reliability for your growing business.