UPVC Pipe Bundling and Strapping: A Showcase of Efficiency and Precision
In the world of modern manufacturing, automation plays a pivotal role in maximizing throughput, maintaining quality, and ensuring worker safety. For the plastic processing industry—particularly those focused on UPVC pipes—reliable bundling and strapping systems can be the linchpin of a streamlined workflow. This showcase highlights a state-of-the-art bundling and strapping machine designed to handle UPVC pipes ranging from Ø21 mm to Ø60 mm in diameter. By leveraging servo-controlled mechanisms, smart PLC (Programmable Logic Controller) integration, and precise force monitoring, this system delivers consistent, high-quality bundles time after time.
Understanding the Challenges of UPVC Pipe Bundling
Bundling UPVC pipes presents unique challenges. Depending on diameter, wall thickness, and production rate, the bundling process must ensure that pipes are counted accurately, arranged neatly, and strapped tightly without compromising pipe integrity. Traditional manual bundling can be slow, prone to miscounts, and inconsistent in tension. Additionally, the slightest misalignment can lead to damage or product waste. These inefficiencies become increasingly apparent when production lines run around the clock at high speeds.
To solve these issues, manufacturers look to advanced bundling and strapping systems that integrate seamlessly with other equipment such as thermoforming machines and automated conveyors. These systems must ensure stable, precise operation over time, while also being flexible enough to handle a range of pipe diameters, lengths, and bundling configurations.
Key Machine Functions and Specifications
Below are some standout features and specifications of the showcased bundling and strapping machine:
-
Diameter Range
-
Capable of handling pipe diameters from Ø21 mm to Ø60 mm.
-
This flexibility ensures a single machine can accommodate multiple product lines without time-consuming changeovers.
-
PLC and HMI Control
-
Both the counting unit and the pipe bundling unit are controlled by a PLC system.
-
A 14 to 17-inch Human-Machine Interface (HMI) touch screen provides real-time feedback, diagnostic messages, and quick-change options for production parameters.
-
Automatic Counting and Weight Verification
-
Sensor-based counting ensures accurate detection of every single pipe.
-
A built-in weighing sensor (scale) verifies the total weight to confirm the pipe count.
-
If the weight or pipe count is off (either too many or too few), the system triggers an alert through indicator lights and an audible alarm.
-
Production Data Logging
-
The machine maintains a log of bundled pipe weights, making it easier for quality control and record-keeping.
-
This feature also aids in traceability, enabling managers to confirm precise production volumes and identify discrepancies in real time.
-
Synchronization with Extrusion Line
-
The bundling speed adjusts automatically to match the current output rate of the extrusion line.
-
This synchrony reduces bottlenecks, ensuring that finished pipes move swiftly from one stage of production to the next.
-
Installation Compatibility
-
The machine’s layout and footprint are designed to be compatible with existing thermoforming stations.
-
This means it can be integrated into an existing line without a massive overhaul or reconfiguration of plant floor space.
-
PP Strap Specifications
-
Uses PP (polypropylene) straps measuring 12–15 mm in width and 0.8 mm in thickness.
-
Chosen for its balance of strength, flexibility, and cost-effectiveness, PP strap is a dependable option for bundling tasks.
-
The system applies tension that can be adjusted to ensure straps are secure according to the customer’s requirements.
-
Two-Point Bundling
-
The pipe bundle is secured at two distinct points along its length, each point receiving two straps.
-
The number of strapping points and their exact positioning can be adjusted if different pipe lengths or customer specifications require it.
-
Servo-Controlled Pipe Stacking
-
Every pipe stacker within this machine is servo-motor driven, allowing for precise movements and placements.
-
This leads to neat, stable bundling and less chance of damage during high-speed operations.
-
Four-Meter Pipe Length
-
Optimized for bundling and strapping pipes at a standard length of four meters, commonly found in UPVC pipe manufacturing lines.
-
The system can also accommodate minor length variations if necessary.
-
Servo-Motor-Driven Strapping Conveyor with Force Sensors
-
The conveyor unit that delivers the PP strap is powered by a servo motor equipped with a load sensor.
-
This approach delivers tight, controlled strapping tension. It also prevents the strap from twisting or jamming.
-
High tension capability is crucial to preventing the bundle from loosening over time or during subsequent handling.
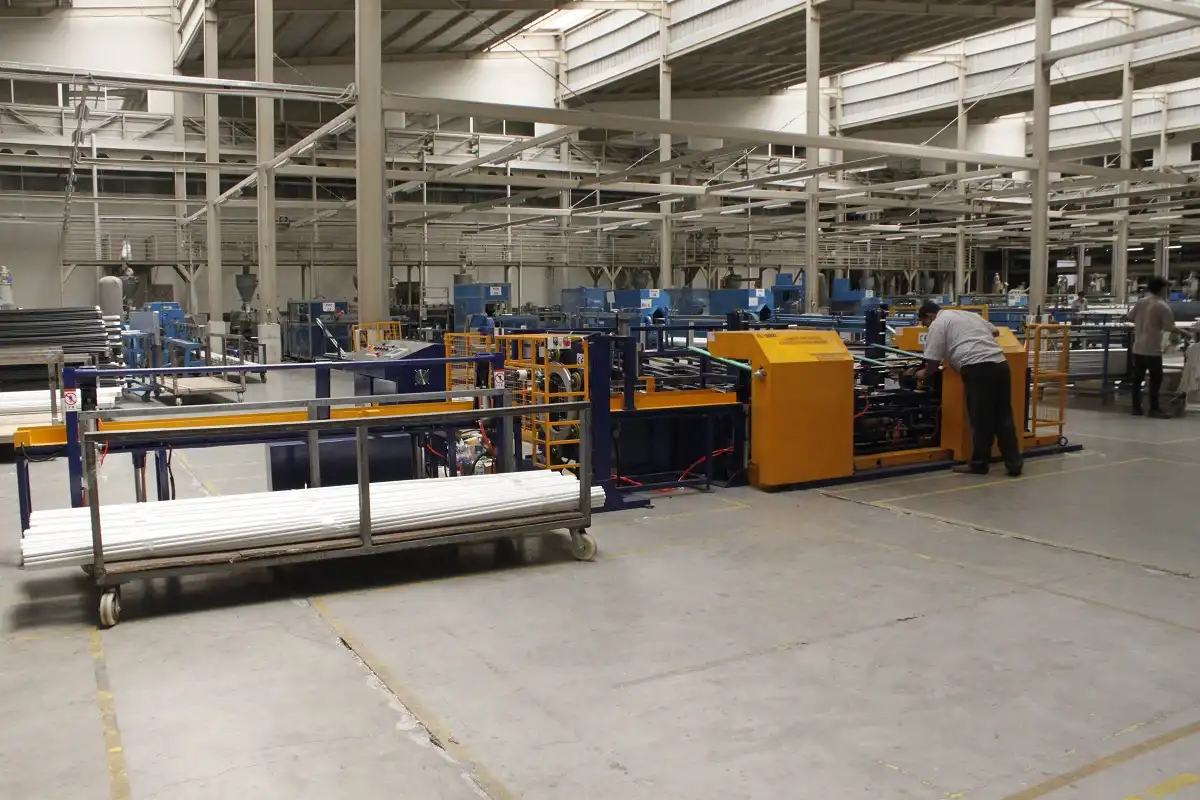
Customizable Bundling Specifications
The showcased system supports multiple bundling configurations based on different pipe diameters. For instance:
-
Ø21 mm
-
50 pipes per bundle
-
PP strap tension is adjustable to ensure the bundle remains tight and secure.
-
Ø27 mm
-
25 pipes per bundle
-
Same secure strapping methodology, with parameters adapted to the larger diameter.
-
Ø34 mm
-
25 pipes per bundle
-
Counting and weighing system ensures no miscounts in the final bundle.
-
Ø42 mm
-
10 pipes per bundle
-
The machine automatically adapts cycle times to avoid inefficiencies or downtime.
-
Ø49 mm
-
10 pipes per bundle
-
Consistent tension across all straps, maintaining bundle stability.
-
Ø60 mm
-
10 pipes per bundle
-
The system’s servo motors handle the increased weight and diameter with ease.
Each bundle is strapped tightly according to the client’s standards, ensuring minimal slack. This adjustability is particularly important when customers have varied packaging specifications for different markets or end uses.
The Fabricator’s Perspective: Why It Matters
From a “The Fabricator” standpoint, a well-engineered bundling and strapping solution is more than a convenience—it’s a strategic asset in a high-volume production environment. By automating the bundling of UPVC pipes, manufacturers minimize the risk of workplace injuries (such as repetitive strain or improper lifting) and ensure consistent product presentation. Additionally, accurate bundling can have a direct impact on downstream operations like shipping and inventory management.
-
Quality Control: When every bundle has a verifiable weight and count, errors can be traced or mitigated quickly.
-
Operational Efficiency: Precise synchronization with extrusion lines prevents pipe buildup and keeps output flow smooth.
-
Cost Savings: Automated solutions reduce labor overhead while also cutting down on waste caused by miscounts or damaged pipes.
-
Scalability: Because the machine adapts to different diameters and bundling requirements, it can serve multiple product lines without needing a separate, dedicated bundling station for each diameter.
Inside the Machine: How It Works
-
Pipe Infeed
-
Pipes exit the thermoforming station and enter the bundling system. The servo-driven mechanism spaces them correctly for counting and stacking.
-
Counting and Verification
-
As pipes move along, sensors detect each pipe’s presence.
-
Weighing sensors provide an additional layer of verification to ensure the pipe count is accurate.
-
Stacking and Bundle Formation
-
A servo-driven stacker gently lifts or positions each pipe layer. For diameters like Ø21 mm, it may place multiple rows side by side until the target count is reached.
-
The system keeps track of how many pipes have been accumulated, comparing that tally with weight measurements.
-
Strapping and Securing
-
Once the target number of pipes is reached, the system secures them in two points (each point uses two straps).
-
Strap tension is carefully monitored via a force sensor, guaranteeing consistency with each cycle.
-
Signal for Discharge
-
The system can incorporate an alert or simply move the completed bundle onto the next stage once strapping is finished.
-
This might be an automated cart, a conveyor, or an area where operators can collect the bundles for storage or shipping.
-
Data Logging
-
Each bundle’s weight, pipe count, time, and possibly even tension values are recorded. This data can be exported to plant-wide systems for further analysis and quality control.
Maintenance and Upkeep
While servo-driven and sensor-monitored systems offer high precision, it’s crucial to follow an outlined maintenance schedule. This typically includes:
-
Routine Sensor Checks: Ensuring that counting sensors and load cells remain free of dust or debris that could compromise readings.
-
Lubrication: Periodically lubricating mechanical components to prevent undue wear.
-
Software Updates: PLC and HMI firmware should be kept current to ensure reliability, security, and new feature integration.
-
Strap Path Inspection: Regularly checking for any strap material buildup or potential obstructions along the strap conveyor.
By committing to these simple maintenance steps, manufacturers can extend the lifespan of their bundling system, avoid unplanned downtime, and maintain consistent product quality.
Future-Proofing and Upgrades
One advantage of using servo motors, PLC controls, and HMIs is the relative ease with which the system can be upgraded. Should production volumes increase or new pipe diameters be introduced, a well-designed machine allows for:
-
Software Parameter Changes: Adjust the stack height, strapping frequency, or tension values through the HMI.
-
Additional Sensor Integration: If higher-level checks—like diameter measurements or surface inspection—are needed, sensor modules can be integrated into the existing PLC program.
-
Extended Strapping Points: The number of strapping points can be adapted if future orders require different bundling patterns.
Such future-proofing considerations make this bundling and strapping machine a worthy investment for fabricators seeking to stay competitive in an evolving market.
Conclusion
The showcased UPVC pipe bundling and strapping system epitomizes efficiency, precision, and adaptability. By combining sensor-based counting with weight verification, servo-controlled stacking, and force-monitored strapping tension, it addresses the core demands of modern UPVC pipe extrusion lines. With configurable strapping points, thorough data logging, and straightforward PLC/HMI interfaces, it fits seamlessly into existing production workflows while offering plenty of room for growth.
From a “The Fabricator” perspective, this solution stands out as an example of how thoughtful engineering and robust automation can transform a potentially error-prone process into a streamlined, cost-effective operation. By protecting product integrity, ensuring bundle consistency, and simplifying record-keeping, manufacturers can focus on scaling production and meeting client demands without compromising quality or reliability.
As global competition intensifies, having a reliable, versatile, and high-throughput bundling system can be the differentiating factor for pipe manufacturers. Whether you’re producing Ø21 mm pipes in massive quantities or handling multiple diameters for custom orders, this strapping solution provides the right balance of performance, durability, and flexibility to keep you at the forefront of the industry.