Are you tired of wrestling with heavy molds, risking worker injury and production delays? Manual mold handling is not just inefficient; it’s a drain on your factory’s bottom line. Imagine a solution that not only makes mold handling safer and easier but also significantly cuts costs.
A mold upender is a crucial piece of factory equipment designed to safely and efficiently rotate heavy molds, dies, and coils. By automating the upending process, factories drastically reduce manual labor, minimize the risk of accidents, and enhance overall workflow efficiency, leading to substantial cost savings and improved ROI.
This article dives deep into the world of mold upenders, exploring how these machines can revolutionize your factory operations and deliver a significant return on your investment. Keep reading to discover the tangible cost-saving benefits and why a mold upender is an essential addition to any modern manufacturing facility.
Streamlining Operations: How Mold Upenders Enhance Efficiency
Frustrated with bottlenecks in your mold handling process? Every minute spent on manual flipping and positioning is a minute lost in production. Imagine a seamless workflow where molds are effortlessly and precisely positioned, ready for the next stage of manufacturing.
Mold upenders dramatically enhance operational efficiency by automating the cumbersome task of rotating heavy molds. This automation reduces manual handling time, speeds up mold changes, and ensures precise positioning, leading to increased throughput and minimized downtime. By optimizing workflow, mold upenders become indispensable tools for boosting productivity in any factory.
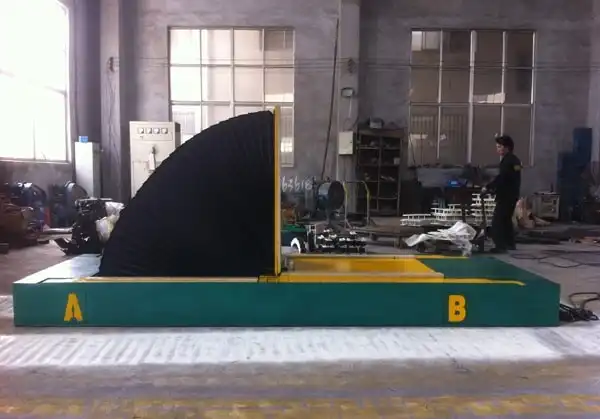
Dive Deeper: Unpacking the Efficiency Gains of Mold Upenders
Mold upenders are more than just convenient pieces of machinery; they are strategic assets that fundamentally transform factory efficiency. To truly understand their impact, let’s break down the key areas where these machines deliver unparalleled improvements.
Reduced Manual Handling Time
Manual mold handling is inherently time-consuming. It often requires multiple workers, specialized lifting equipment like cranes, and meticulous coordination to ensure safety and prevent damage. Mold upenders streamline this process by automating the rotation. Instead of lengthy setups and slow, cautious movements, a mold upender can rotate a mold in minutes, sometimes even seconds, with a single operator. This speed directly translates into faster mold changes, reduced setup times, and more production time available.
Faster Mold Changeovers
In industries that require frequent mold changes, such as injection molding or die casting, downtime for changeovers is a major concern. Traditional manual methods can extend changeover times significantly, impacting overall production schedules. Mold upenders drastically cut down on changeover times by simplifying and accelerating the mold handling aspects. This rapid turnaround minimizes production interruptions, allowing for quicker responses to changing demands and maximizing machine utilization.
Precision and Accuracy in Positioning
Manual handling is prone to human error, which can lead to misalignments, damage to molds, and even safety hazards. Mold upenders offer precise and controlled movements, ensuring accurate positioning every time. This precision is crucial for maintaining mold integrity, ensuring proper fitment in machinery, and preventing production defects caused by misaligned molds. The consistent accuracy provided by mold upenders contributes to higher quality output and reduces the need for rework or scrap.
Comparison of Manual Handling vs. Mold Upender Efficiency
To illustrate the tangible benefits, consider the following comparison:
Feature | Manual Mold Handling | Mold Upender | Efficiency Gain |
---|---|---|---|
Time per Mold Flip | 30-60 minutes (depending on size/weight) | 5-10 minutes | 6x – 12x faster |
Labor Required | 2-4 workers | 1 worker | 50%-75% reduction |
Precision | Variable, prone to human error | Highly accurate and consistent | Significantly improved |
Safety Risk | High | Low | Dramatically reduced |
Downtime Impact | Significant | Minimal | Major reduction |
As the table clearly indicates, the efficiency gains offered by mold upenders are substantial across multiple critical factors. By minimizing time, labor, and errors while maximizing precision and safety, mold upenders provide a compelling solution for factories seeking to optimize their operations. This enhanced efficiency ultimately translates directly into cost savings and a stronger bottom line.
Cutting Labor Costs: The Economic Advantage of Automation
Are your labor costs spiraling out of control due to manual mold handling? Every worker involved in heavy lifting and awkward maneuvering adds to your payroll and increases the risk of costly workplace injuries. Imagine reallocating your valuable workforce to more productive tasks while a machine handles the heavy lifting.
Mold upenders offer significant labor cost savings by automating mold rotation, reducing the need for multiple workers in manual handling. By streamlining operations and minimizing the physical demands on personnel, factories can optimize their workforce, decrease labor expenses, and improve overall profitability. This shift towards automation is a smart economic move for any manufacturing facility dealing with heavy molds.

- Reallocating Workforce for Higher-Value Tasks
Beyond the direct reduction in labor costs, mold upenders offer a strategic advantage by freeing up your workforce to focus on more value-added activities. Instead of dedicating manpower to physically demanding and repetitive mold handling tasks, your skilled employees can be redeployed to roles that require their expertise and contribute more directly to production quality and innovation.
This reallocation can lead to improvements in areas such as:
- Quality Control: More personnel can be assigned to quality inspection, ensuring fewer defects and higher product standards.
- Process Optimization: Employees can focus on analyzing and improving production processes, leading to further efficiency gains.
- Maintenance and Repair: A dedicated maintenance team can ensure equipment is running optimally, minimizing downtime and extending the lifespan of machinery.
- New Product Development: Freeing up skilled labor can allow for greater focus on research and development, driving innovation and future growth.
By transitioning from manual mold handling to automated upending, factories not only save on immediate labor expenses but also unlock the potential of their workforce to contribute to higher-level tasks that drive long-term success. This strategic reallocation of resources is a key factor in maximizing the ROI of a mold upender investment.
Enhancing Workplace Safety: Minimizing Risks and Liabilities
Is workplace safety a top priority in your factory? Manual mold handling poses significant safety risks, from strains and sprains to serious crush injuries. Accidents not only harm your employees but also lead to downtime, compensation claims, and potential legal liabilities.
Mold upenders significantly enhance workplace safety by eliminating the need for manual lifting and flipping of heavy molds. This automation reduces the risk of musculoskeletal injuries, crush hazards, and other accidents associated with manual handling, creating a safer working environment for employees and minimizing potential liabilities for the factory. Investing in a mold upender is a proactive step towards a safer and more responsible manufacturing operation.
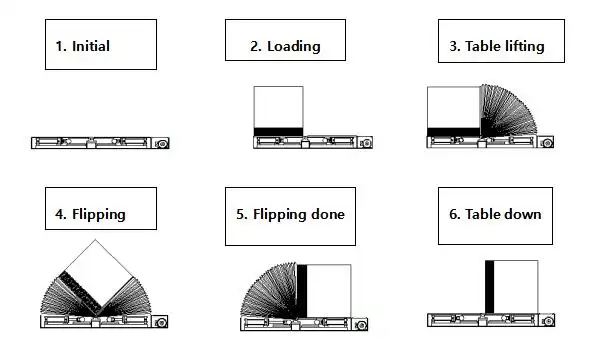
Dive Deeper: A Safer Factory Floor with Mold Upenders
Workplace safety is not just a moral imperative; it’s a critical factor in operational efficiency and financial stability. Manual mold handling is inherently dangerous, but mold upenders offer a robust solution to mitigate these risks. Let’s examine the specific safety improvements these machines bring.
Reduction of Musculoskeletal Injuries (MSIs)
Manual lifting, twisting, and awkward postures involved in mold handling are major causes of musculoskeletal injuries (MSIs), such as strains, sprains, and back injuries. These injuries are not only painful for workers but also lead to absenteeism, reduced productivity, and workers’ compensation claims. Mold upenders eliminate much of the manual exertion, significantly reducing the physical strain on workers and minimizing the risk of MSIs.
Minimizing Crush and Impact Hazards
Heavy molds are inherently dangerous. If mishandled, they can easily slip, fall, or swing unexpectedly, posing serious crush and impact hazards. Manual handling, especially with slings or chains, increases the proximity of workers to these hazards. Mold upenders provide controlled and stable rotation, keeping workers at a safe distance during the upending process and drastically reducing the potential for crush injuries.
Prevention of Dropped Loads and Equipment Damage
Manual handling, particularly with overhead cranes, carries the risk of dropped loads due to operator error, equipment failure, or improper rigging. A dropped mold can cause catastrophic damage to the mold itself, surrounding equipment, and potentially the facility structure. Mold upenders are designed for stable and secure mold handling. They grip and rotate molds in a controlled manner, eliminating the risk of dropped loads and the associated damage and downtime.
Comparison of Safety Risks: Manual Handling vs. Mold Upender
Safety Risk | Manual Mold Handling | Mold Upender | Risk Reduction |
---|---|---|---|
Musculoskeletal Injuries | High risk due to manual lifting | Low risk, automated operation | Significant |
Crush Hazards | Moderate to high risk | Low risk, controlled movement | Substantial |
Dropped Loads | Moderate risk, crane dependency | Minimal risk, secure grip | Near elimination |
Worker Proximity to Hazard | Close proximity during operation | Safe distance maintained | Increased safety |
Liability Exposure | Higher, due to accident potential | Lower, proactive safety measure | Reduced liability |
The data clearly demonstrates that mold upenders offer a significant improvement in workplace safety across all key risk areas. By proactively investing in safety through automation, factories protect their employees, reduce potential liabilities, and create a more responsible and sustainable operating environment. A safer workplace is not only ethically sound but also contributes to improved morale, reduced turnover, and a more efficient and productive workforce.
Ensuring Mold Integrity: Reducing Damage and Repair Costs
Are you constantly battling mold damage from rough handling? Every chip, dent, or misalignment can compromise mold performance, lead to production defects, and necessitate costly repairs or replacements. Imagine handling your valuable molds with the utmost care and precision, extending their lifespan and minimizing downtime.

Mold upenders ensure mold integrity by providing controlled and precise handling, minimizing the risk of damage during rotation and positioning. This gentle and secure handling reduces wear and tear on molds, extends their lifespan, and decreases the frequency of costly repairs or replacements. By protecting your mold investment, upenders contribute to long-term cost savings and consistent production quality.
Mold upenders are an investment in factory equipment that yields substantial cost savings through enhanced efficiency, reduced labor expenses, improved workplace safety, and protection of valuable molds. Embracing this technology positions your factory for increased profitability and long-term success.