What Training Courses Are Available for Mold Flipper Operators?
Operating a mold flipper machine demands specialized skills and comprehensive training. Ensuring operators are well-versed in safety protocols and operational best practices is paramount for workplace safety and efficiency. This article explores the essential training courses available for mold flipper operators.
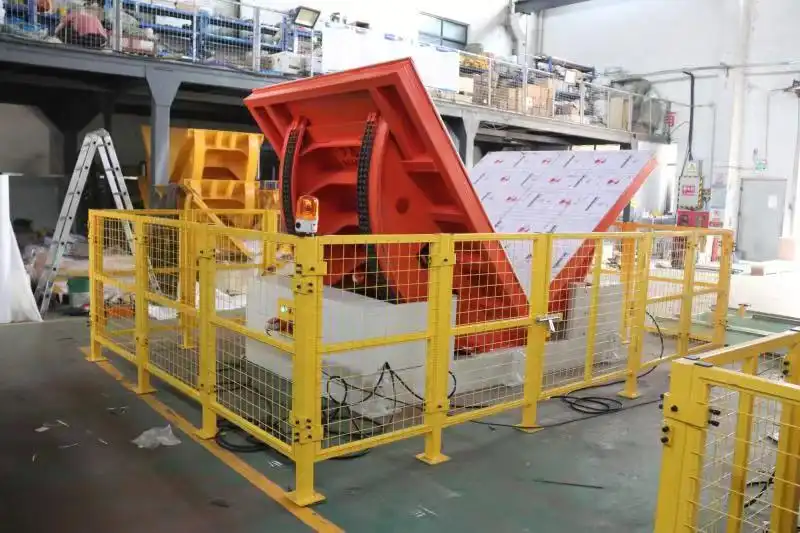
Mold flipper operator training courses typically encompass equipment operation, safety procedures, and routine maintenance. These programs often include hands-on workshops, safety drills, and troubleshooting simulations to equip operators with the knowledge and skills necessary for safe and efficient mold flipping operations. Certification upon completion may also be offered by some providers.
As industries increasingly adopt automated solutions like mold flipping machines, the demand for skilled operators is on the rise. Let’s delve deeper into the specifics of training programs and what they offer to ensure your team is fully prepared.
Essential Safety Protocols for Mold Flipper Operators
In industries utilizing heavy molds, safety is non-negotiable. Proper safety protocols are the backbone of efficient and accident-free mold flipping operations. Understanding and adhering to these protocols is crucial for every operator.
Essential safety protocols for mold flipper operators include pre-operation checks to identify equipment flaws, comprehensive operator training on safe practices, maintaining a clear workspace to prevent accidents, and routine maintenance to ensure machine reliability. Strict adherence to manufacturer guidelines and consistent safety audits are also vital components of a robust safety protocol.
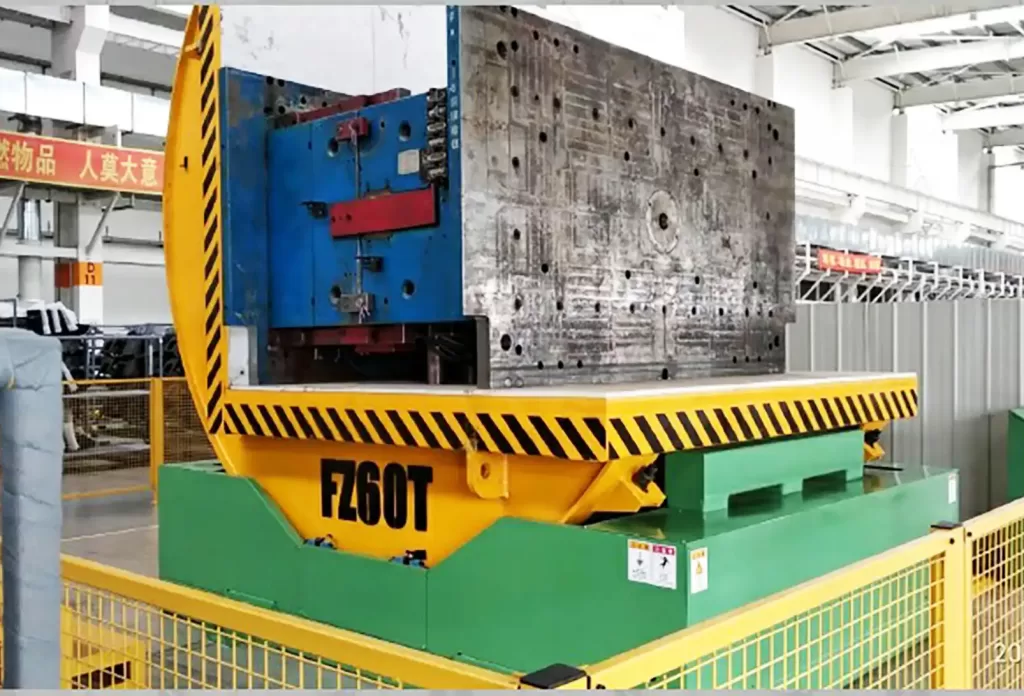
To truly embed a culture of safety, a structured approach is necessary. Let’s break down the key safety protocols into actionable steps and understand their significance in detail.
Deep Dive into Mold Flipper Safety Protocols
Effective safety protocols are more than just a checklist; they are a dynamic system that requires continuous attention and improvement. By dissecting the core elements, we can ensure a safer and more productive working environment. Let’s examine the critical components:
Safety Protocol | Key Actions | Importance |
---|---|---|
Pre-Operation Check | – Inspect for wear and tear on moving parts. – Verify hydraulic oil levels and check for leaks. – Test control panels and emergency stops. |
– Ensures equipment is in optimal condition before operation. – Minimizes the risk of unexpected downtime due to equipment failure. – Proactively identifies potential hazards. |
Operator Training | – Conduct comprehensive training sessions covering machine operation, safety features, and emergency procedures. – Provide hands-on workshops and simulations. – Regularly update training to reflect new safety standards and equipment updates. |
– Empowers operators with the necessary knowledge and skills to operate the machine safely and efficiently. – Fosters a safety-conscious culture within the team. – Reduces human error, a significant factor in workplace accidents. |
Clear Workspace | – Define and maintain a clear zone around the mold flipper. – Ensure no obstacles, tools, or materials are within the operational area. – Implement clear markings and signage to delineate the safe zone. |
– Reduces the likelihood of accidents caused by tripping hazards or collisions. – Provides operators with ample space to maneuver safely. – Ensures unobstructed access for maintenance and emergency response. |
Routine Maintenance | – Establish a schedule for regular machine inspections and maintenance. – Lubricate moving parts and replace worn components promptly. – Keep detailed maintenance logs to track performance and identify trends. |
– Extends the lifespan of the mold flipping machine. – Ensures consistent and reliable performance. – Prevents breakdowns and costly repairs, maintaining operational efficiency. |
By meticulously implementing these protocols and fostering a proactive safety mindset, businesses can significantly mitigate risks associated with mold flipping operations and cultivate a secure environment for their workforce.
Maintenance Training for Mold Flipping Machines
Maintaining a mold flipping machine goes beyond simple upkeep; it’s about ensuring consistent performance, longevity, and most importantly, safety. Proper maintenance training equips personnel with the knowledge to keep these machines running smoothly and reliably.
Mold flipper maintenance training should cover regular checks of moving parts for wear, inspection of hydraulic systems for leaks, and examination of electrical components. Training should also emphasize lubrication, cleaning, and timely repair procedures to maximize machine lifespan and operational efficiency. Hands-on sessions and manufacturer-specific guidelines are essential components.
To truly master mold flipper maintenance, a deep dive into the technical aspects is required. Let’s explore the critical areas and frequencies of maintenance.
Technical Deep Dive into Mold Flipper Machine Maintenance
Effective maintenance is a proactive, detail-oriented process. Overlooking seemingly minor components can lead to significant operational disruptions. Let’s break down the key areas of maintenance and their recommended frequencies:
Key Area | Maintenance Frequency | Action Required |
---|---|---|
Moving Parts | Weekly | – Inspect for wear, cracks, or damage. – Lubricate joints, bearings, and gears with appropriate lubricants. – Tighten any loose bolts or fasteners. |
Hydraulic Systems | Monthly | – Check hydraulic fluid levels and top up if necessary. – Inspect hoses and connections for leaks or damage. – Monitor hydraulic pressure and performance. |
Electrical Components | Quarterly | – Inspect wiring, connections, and control panels for damage, corrosion, or loose connections. – Test safety circuits and emergency stops. – Ensure proper grounding. |
Safety Features | Monthly | – Test all safety stops, emergency controls, and sensors for proper functionality. – Inspect safety barriers and guards for damage or displacement. – Verify interlocking systems are working correctly. |
Load-Bearing Structures | Annually | – Conduct a thorough inspection of the machine’s frame, lifting arms, and load decks for structural integrity. – Check for signs of fatigue, cracks, or deformation. – Consult with a qualified engineer for detailed structural assessments if needed. |
Regular, systematic maintenance, coupled with detailed record-keeping, is the cornerstone of optimal mold flipper performance and longevity. By adhering to these guidelines, businesses can minimize downtime and ensure a safe and efficient operation.
Best Practices in Personnel Training for Mold Flippers
Operating a mold flipper effectively and safely isn’t just about knowing the machine; it’s about comprehensive personnel training. Well-trained operators are your first line of defense against accidents and inefficiencies.
Best practices for training personnel on mold flipper operation involve a blend of theoretical instruction and hands-on practical sessions. Training programs should cover machine controls, safety protocols, emergency procedures, and basic troubleshooting. Regular refresher courses and competency assessments are also crucial to maintain operator proficiency and safety awareness.
To ensure training is truly effective, it needs to be structured and comprehensive. Let’s explore the key components of an ideal training program.
Structuring Comprehensive Mold Flipper Operator Training
Effective training goes beyond simply showing someone how to use the machine. It requires a structured approach that builds competency and instills a safety-first mindset. Here’s a breakdown of key elements for structuring training programs:
Training Objective | Training Method | Expected Outcome |
---|---|---|
Understanding Machine Controls | – Hands-on workshops with machine simulators. – Step-by-step demonstrations on actual equipment. – Interactive quizzes to reinforce learning. |
– Operators can confidently and accurately execute basic and advanced machine operations. – Reduced risk of operational errors due to unfamiliarity with controls. |
Safety Procedure Awareness | – Safety drills and emergency response simulations. – Briefings on potential hazards and risk mitigation. – Case study reviews of past incidents and lessons learned. |
– Enhanced adherence to safety protocols and a significant reduction in incident rates. – Operators are prepared to respond effectively in emergency situations. – Proactive identification and reporting of potential safety hazards. |
Troubleshooting Skills | – Simulations of common machine malfunctions. – Mentorship from experienced technicians. – Access to troubleshooting manuals and online resources. |
– Operators can identify and resolve minor operational issues independently, minimizing downtime. – Improved machine uptime and productivity. – Reduced reliance on maintenance staff for simple problems. |
Routine Maintenance Basics | – Practical sessions on lubrication, cleaning, and basic inspection. – Checklists and guides for daily/weekly maintenance tasks. – Demonstrations of component replacement. |
– Operators contribute to routine maintenance, extending machine lifespan. – Early detection of potential maintenance issues, preventing major breakdowns. – Increased sense of ownership and responsibility for machine upkeep. |
By implementing a well-structured training program that incorporates these elements, companies can cultivate a highly skilled and safety-conscious workforce capable of maximizing the benefits of mold flipping technology. Remember to explore mold flipper solutions to further enhance your operations.
Safe Implementation of Mold Flipping Machines in the Workplace
Introducing a mold flipping machine into your workplace is a significant step towards improved safety and efficiency. However, safe implementation requires careful planning and execution.
Implementing a mold flipping machine safely involves thorough staff training on operation and safety, establishing a schedule for regular maintenance checks, conducting routine safety inspections to identify hazards, and strictly adhering to manufacturer operational guidelines. Continuous monitoring of operations ensures sustained safety and efficiency.
Step-by-Step Guide to Safe Mold Flipper Implementation
Integrating a mold flipper successfully hinges on a phased approach that prioritizes safety at every step. Here’s a practical guide to ensure a smooth and secure implementation:
- Comprehensive Risk Assessment: Before installation, conduct a thorough risk assessment of the intended operating area. Identify potential hazards, including pedestrian traffic, existing equipment, and environmental factors. This assessment will inform safety protocols and workspace design.
- Workspace Redesign (if necessary): Based on the risk assessment, redesign the workspace to accommodate the mold flipper safely. Ensure adequate clearance around the machine, clear pathways for operators and material flow, and consider implementing physical barriers or safety markings to delineate operational zones.
- Professional Installation: Engage certified technicians for the installation of the mold flipping machine. Ensure the machine is installed according to manufacturer specifications and all safety features are correctly configured and functional. Verify proper grounding and electrical connections.
- Detailed Operator Training Program Rollout: Implement the comprehensive operator training program as outlined previously. Ensure all operators who will interact with the machine complete the training and demonstrate competency before being authorized to operate the equipment. Document all training records.
- Establish Maintenance Schedule: Develop a detailed maintenance schedule based on manufacturer recommendations and operational demands. Assign responsibility for maintenance tasks and ensure all maintenance personnel are properly trained. Stock necessary spare parts and lubricants.
- Safety Protocol Implementation and Communication: Formally document all safety protocols and operational guidelines. Communicate these protocols clearly to all relevant personnel through training sessions, safety manuals, and visual aids in the workplace. Conduct regular safety meetings to reinforce safety culture.
- Pre-Operational Safety Checks (Daily/Shiftly): Implement a mandatory pre-operational checklist for operators to complete before each shift or workday. This checklist should include visual inspections, functional tests of safety features, and verification of workspace safety.
- Continuous Monitoring and Audits: Establish a system for continuous monitoring of mold flipper operations and regular safety audits. Track performance metrics, incident reports, and maintenance logs. Use audit findings to refine safety protocols and training programs proactively.
- Emergency Response Plan: Develop and communicate a clear emergency response plan in case of machine malfunction, accidents, or other unforeseen events. Ensure operators are trained on emergency shutdown procedures, evacuation routes, and first aid protocols. Conduct periodic emergency drills.
- Regular Review and Improvement: Periodically review the entire mold flipper implementation process, including safety protocols, training programs, and maintenance schedules. Seek feedback from operators and maintenance personnel to identify areas for improvement and ensure ongoing optimization of safety and efficiency.
By following these steps, businesses can ensure the safe and effective integration of mold flipping machines into their operations, maximizing benefits while minimizing risks.
Conclusion
Investing in comprehensive training for mold flipper operators is not merely an expense, but a strategic investment in workplace safety and operational excellence. By prioritizing safety protocols, robust maintenance, and thorough training programs, industries can harness the power of mold flipping technology while safeguarding their most valuable asset – their workforce. A well-trained team, equipped with the right knowledge and skills, ensures efficient, safe, and productive mold handling operations, contributing to long-term success and a thriving work environment.