1. What Labeling and Identification Methods Are Used in Steel Coil Packing?
Labeling and identification are critical processes in steel coil packing, ensuring efficient inventory management, traceability, and clear communication of essential information. These methods range from traditional physical tags to advanced digital systems, each serving specific needs within the steel industry. Proper identification is not just operational necessity but also crucial for maintaining product integrity and logistical efficiency.
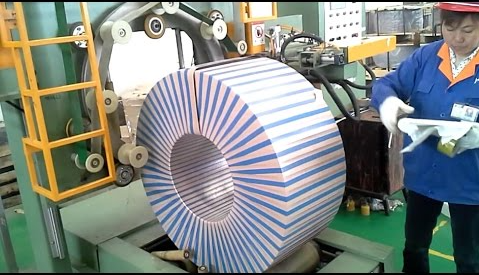
Steel coil packing utilizes a variety of labeling and identification methods, primarily including physical tags for direct visual identification, ink jet printing for applying information directly onto packaging, and digital systems like barcode and RFID for advanced tracking. These methods ensure product traceability, efficient inventory control, and accurate information dissemination throughout the steel supply chain, catering to diverse operational scales and requirements.
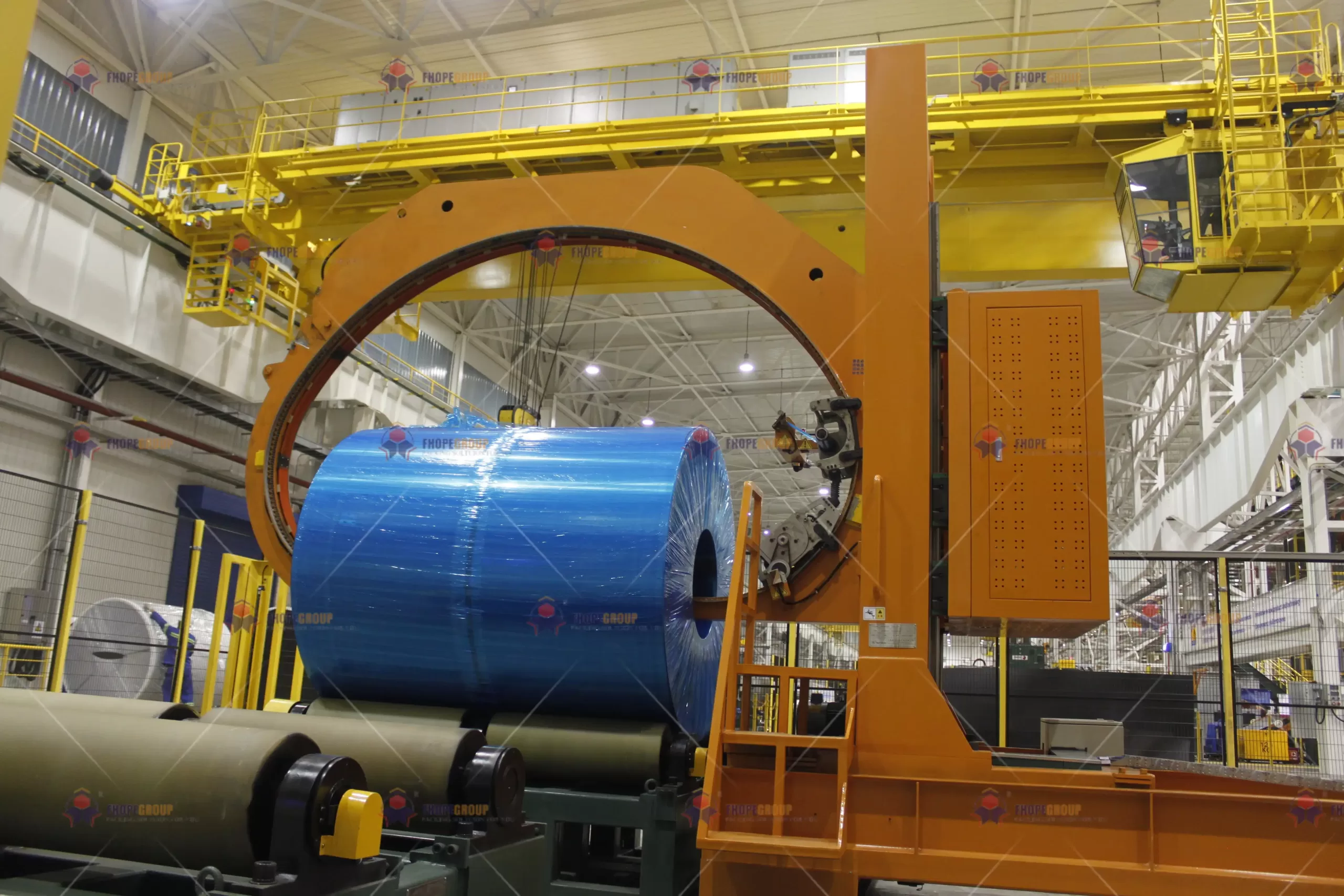
Understanding the diverse labeling and identification methods available for steel coil packing is key to optimizing operations and maintaining a competitive edge in the steel industry. Let’s delve into the specifics of these methods, exploring their applications and benefits in detail.
2. Physical Tagging and Labeling in Steel Coil Packing
Physical tagging remains a cornerstone of steel coil packing, providing a direct and visually accessible identification method. These tags, directly attached to steel coils or bundles, serve as immediate information points for handlers and storage personnel. The effectiveness of physical tags hinges on their durability and the clarity of the information they convey, especially in demanding industrial environments.
Physical tags in steel coil packing typically employ robust materials like metal or plastic, designed to withstand harsh conditions. Information is applied through stamping, embossing, or printing, ensuring legibility even in challenging environments. Secured with steel wire or durable fasteners, these tags commonly display product grade, size, batch number, and origin, facilitating immediate identification and inventory management at the point of handling. While digital methods are advancing, physical tags offer a reliable, instant identification solution, particularly valuable in areas with limited digital infrastructure.
While physical tags offer immediate visual identification, their standalone functionality can be enhanced significantly by integrating them with digital systems. This integration bridges the gap between the tangible and digital realms, creating a more robust and efficient identification process.
Enhancing Physical Tags with Digital Integration
Physical tags, while straightforward, can become labor-intensive in large-scale operations and are susceptible to manual data entry errors. Integrating digital technologies with physical tags creates a hybrid system that capitalizes on the strengths of both approaches. This synergy is primarily achieved by linking physical tags to digital records through unique identifiers.
Barcodes and QR Codes on Physical Tags
Adding barcodes or QR codes to physical tags transforms them into data-rich tools. These codes enable rapid and accurate data capture using scanners or mobile devices, effectively linking the physical tag to digital inventory and tracking systems.
Feature | Barcode | QR Code |
---|---|---|
Data Capacity | Limited, Primarily Alphanumeric | High, Alphanumeric, Numeric, Binary, Kanji |
Readability | Requires Line-of-Sight Scanning | Readable from Various Angles |
Error Correction | Limited | High Error Correction Capability |
Use Cases | Product Identification, Simpler Data Needs | Complex Data, URLs, Versatile Applications |
RFID Integration with Physical Tags
Radio-Frequency Identification (RFID) technology elevates physical tags further by embedding RFID chips within them. These chips can store significantly more data than barcodes and QR codes and can be read wirelessly, even without direct line of sight. This capability is particularly advantageous in large warehouses or outdoor storage areas, where manual scanning of individual tags can be cumbersome and inefficient.
Feature | Barcode/QR Code Tags | RFID Tags |
---|---|---|
Data Capture | Requires Manual Scanning, Line of Sight | Wireless, Can Read Multiple Tags at Once |
Data Capacity | Limited by Tag Size | Higher Data Capacity, Rewritable |
Durability | Dependent on Tag Material | Encapsulated Chip, More Resistant to Damage |
Read Range | Short, Scanner Dependent | Longer Range, Adjustable |
Cost | Lower per Tag | Higher per Tag, Reader Infrastructure Cost |
Best Use Cases | Direct Product Scanning, Retail, Basic Tracking | Automated Inventory, Asset Tracking, Robust Environments |
By combining the immediate accessibility of physical tags with the advanced data management capabilities of barcodes, QR codes, or RFID, steel coil packers can achieve a significantly more efficient and error-resistant labeling and identification process.
3. Ink Jet and Direct Marking Methods for Steel Coil Packing
Ink jet printing and direct marking techniques offer an alternative to traditional tags by applying identification directly onto the steel coil packaging. These methods are particularly effective for adding batch numbers, logos, and variable data during the packing process, streamlining operations and reducing material costs associated with separate tags. The selection of ink and marking method is crucial to ensure legibility and durability in the often-harsh environments of steel handling and storage.
Ink jet printing and direct marking in steel coil packing involve specialized inks and printers that apply labels, codes, and essential information directly onto wrapping films, straps, or even the coil itself. These methods provide real-time customization, enabling on-demand printing of variable data such as batch numbers and dates. Industrial-grade inks are used to ensure resistance to abrasion, UV exposure, and temperature variations, guaranteeing durability. Direct marking enhances efficiency and contributes to sustainability by minimizing the need for additional labeling materials.
Successful implementation of ink jet and direct marking in steel coil packing requires careful consideration of technical details. These include printer and ink selection, seamless integration with packaging lines, and consistent print quality maintenance.
Technical Considerations for Ink Jet and Direct Marking
Implementing ink jet or direct marking successfully in steel coil packing requires attention to several technical details. These considerations ensure the efficiency, cost-effectiveness, and durability of the labeling solution.
Ink and Printer Selection
The choice of ink is paramount and must be compatible with the packaging material and resistant to environmental conditions. Common ink types include:
- Solvent-based inks: Fast-drying and durable with good adhesion on non-porous surfaces.
- UV-curable inks: Extremely durable, with excellent resistance to abrasion and chemicals, cured by UV light.
- Water-based inks: Environmentally friendly, suitable for porous materials like cardboard, but less durable.
Printers must be robust for industrial environments and capable of high-speed operation. Continuous Ink Jet (CIJ) and Thermal Ink Jet (TIJ) printers are commonly used due to their reliability and speed.
Integration with Packaging Lines
Seamless integration into existing coil packing machine lines is essential for efficiency. Printers need to be positioned to mark packaging accurately as it moves along the line. Key integration aspects include:
- Sensors: To detect packaging presence and trigger printing.
- Synchronization: Matching printer speed to line speed for consistent print placement.
- Data Integration: Connecting printers to central databases for variable data input like batch numbers and dates.
Maintaining Print Quality
Consistent and legible printing is crucial for effective identification. Factors affecting print quality include:
- Nozzle maintenance: Preventing clogging for consistent ink flow.
- Regular cleaning: Removing dust and debris from printer heads and sensors.
- Ink monitoring: Checking ink levels and quality to avoid faded or inconsistent prints.
By addressing these technical considerations, steel coil packers can effectively utilize ink jet and direct marking methods to achieve efficient and durable labeling solutions.
4. Digital and Automated Identification Systems in Steel Coil Packing
The increasing demand for traceability and efficiency in steel coil packing is driving the adoption of digital and automated identification systems. These systems, leveraging technologies like RFID and barcode scanning, offer real-time data capture, reduced manual intervention, and enhanced inventory management capabilities. Automation in labeling and identification represents a significant step towards optimizing supply chain visibility and operational efficiency in the steel industry.
Digital and automated identification systems in steel coil packing utilize technologies such as RFID and barcode scanning to streamline data capture and inventory management. These systems enable automatic identification of coil bundles as they move through packing and storage processes, providing real-time data on location, quantity, and status. Integration with warehouse management systems (WMS) and enterprise resource planning (ERP) enhances overall supply chain visibility and responsiveness, moving beyond manual processes to create a transparent and efficient operation.
The shift towards digital identification is not just about efficiency; it’s about creating a more transparent and responsive supply chain, enabling quicker responses to customer demands and tighter control over product flow.
Key Aspects of Digital Identification Systems in Steel Coil Packing
Digital identification systems offer several key advantages, transforming steel coil packing operations through automation and data-driven insights.
Aspect | Description | Benefits |
---|---|---|
Automated Data Capture | RFID readers and barcode scanners automatically capture data without manual scanning. | Reduced labor costs, faster processing times, minimized data entry errors. |
Real-Time Tracking | Systems provide up-to-the-minute information on the location and status of each coil bundle. | Improved inventory accuracy, proactive stock management, enhanced traceability. |
Data Integration | Seamlessly integrate with WMS and ERP systems for comprehensive data management and reporting. | Streamlined operations, better decision-making, improved supply chain visibility. |
Enhanced Traceability | Detailed tracking of each batch from production to delivery. | Faster recall processes, improved product accountability, enhanced customer trust. |
Improved Efficiency | Automating identification processes speeds up packing, warehousing, and shipping. | Increased throughput, reduced bottlenecks, optimized resource utilization. |
Automated systems represent the future of steel coil packing identification, offering scalability and precision that traditional methods struggle to match. The investment in such systems often yields significant returns through operational efficiencies and improved supply chain management.
5. Information Management Systems in Steel Coil Packing
In the steel industry, efficient material handling and packing are paramount. Steel coil packing, a critical final step, necessitates precise coordination and data management to ensure product integrity and logistical efficiency. Information management systems are indispensable tools for optimizing this process, providing the data backbone for effective operations.
Information management systems in steel coil packing are crucial for streamlining operations and enhancing traceability. These systems encompass Warehouse Management Systems (WMS) for inventory tracking, Enterprise Resource Planning (ERP) for resource allocation, and specialized coil packing software. By integrating data from sensors, machinery, and databases, these systems optimize workflows, improve decision-making, and ensure each coil is correctly identified, packed, and dispatched efficiently. The implementation of information management systems transforms coil packing into a streamlined, value-added operation, driving efficiency and reducing potential bottlenecks in the steel supply chain.
To fully understand how these systems revolutionize steel coil packing, let’s delve into the specifics of their importance, components, and benefits.
The Critical Role of Information Management in Coil Packing Efficiency
In today’s competitive steel market, efficient coil packing is not just an operational detail; it’s a strategic imperative. Proper packing ensures coils are protected during transit, reduces damage, and optimizes warehouse space, directly impacting profitability. Effective information management is the backbone of efficient coil packing, providing real-time visibility into inventory, streamlining packing processes, and minimizing errors. Without robust systems, steel manufacturers face increased risks of damage, delays, and dissatisfied customers.
Information management systems offer solutions by automating data collection, analysis, and reporting, leading to optimized workflows and enhanced decision-making at every stage of the coil packing process. These systems ensure each coil is correctly identified, packed according to specifications, and dispatched efficiently, reducing bottlenecks and maximizing throughput. Ultimately, information management transforms coil packing from a potential bottleneck into a streamlined, value-added operation.
Key Components of Information Management Systems
Information management in steel coil packing is not a single solution but a combination of interconnected systems. The core components typically include:
- Warehouse Management System (WMS): For inventory and location control, providing real-time visibility of coil inventory levels, optimized storage strategies, and seamless integration with the packing line.
- Enterprise Resource Planning (ERP) system: For overarching resource management and order processing, integrating coil packing with overall business operations, managing customer orders, resource allocation, and financial integration.
- Specialized Coil Packing System Software: Focused specifically on the packing process, interfacing directly with machinery to control coil wrapping, strapping, and labeling systems, automating packing sequences and ensuring quality control.
- Data Acquisition Systems and IoT Integration: Underpinning all components, collecting real-time data from sensors embedded in machinery, interfacing with PLCs, and storing data for analysis and traceability.
These components work in concert to create a powerful information management ecosystem, enabling automation, optimization, and data-driven control in steel coil packing.
Benefits of Implementing Information Management Systems
Investing in information management systems for steel coil packing yields numerous benefits, including:
- Enhanced Operational Efficiency: Automation significantly speeds up packing processes, reduces manual labor, and optimizes material usage.
- Improved Accuracy and Quality: Error reduction through automated labeling and data entry, consistent packing quality, and enhanced traceability for quality assurance.
- Cost Reduction and ROI: Labor cost savings, material cost savings, reduced damage and rework, and increased throughput and revenue potential.
These benefits translate to significant cost savings, improved customer satisfaction, and a stronger competitive edge for steel manufacturers. By leveraging real-time data and optimized workflows, companies can transform their coil packing operations into a source of efficiency and reliability.
Selecting the Right Information Management System
Choosing the optimal information management system for steel coil packing is a critical decision. Key considerations include:
- Scalability: Ability to handle current and future production volumes.
- Integration Capabilities: Seamless integration with existing ERP, WMS, and machinery.
- Customization: Tailoring to specific coil types, packing processes, and reporting needs.
- User-Friendliness: Intuitive and easy to use for operators and staff.
- Data Security: Robust measures to protect sensitive information.
- Reporting and Analytics: Comprehensive tools for performance monitoring and optimization.
- Vendor Support and Reliability: Reputable vendor offering reliable support and maintenance.
- Cost and ROI: Justifiable return on investment.
Careful evaluation of these factors ensures the selection of an information management system that truly empowers steel coil packing operations for long-term success.
Conclusion
In conclusion, selecting and implementing the right labeling and identification methods are crucial for optimizing steel coil packing operations. From the reliability of physical tags to the sophistication of digital and automated systems, each method offers unique advantages tailored to different operational needs. The integration of information management systems further enhances efficiency, traceability, and decision-making, positioning steel manufacturers for competitiveness in the global market. Embracing these advancements is key to achieving operational excellence and ensuring a robust, responsive, and efficient steel supply chain.