Mold upenders are essential in the industrial sector for efficient handling of heavy molds. Companies benefit from optimized safety and productivity. Discover which parts play a critical role.
Mold upenders consist of key components such as frame, motor, control system, safety features, and more. These parts work together to flip and position molds efficiently. Understanding these components ensures optimal operation, safety, and longevity in mold handling applications.
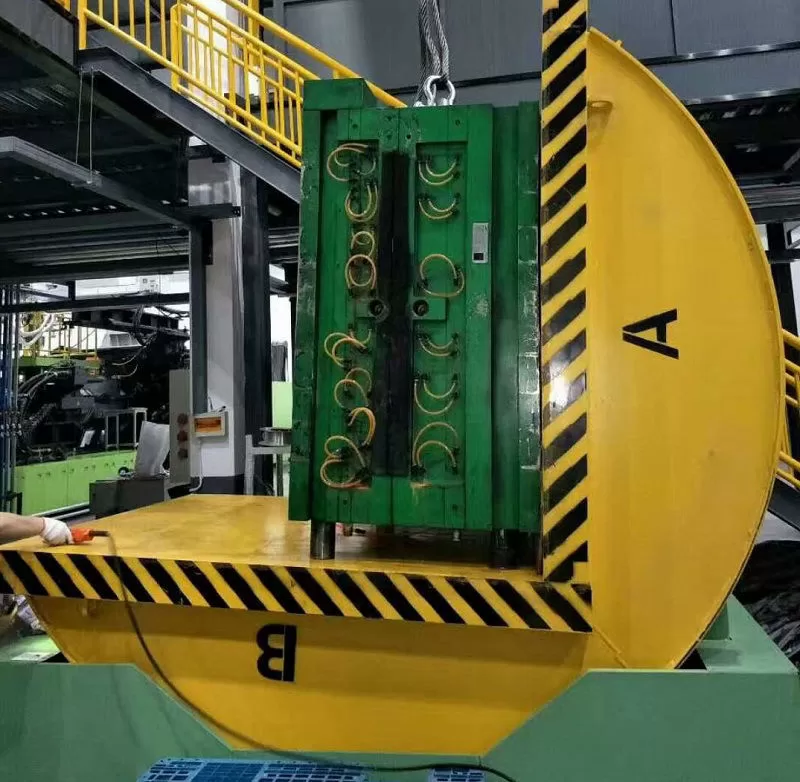
In the ever-evolving manufacturing landscape, investing in quality mold upenders is crucial. These machines enhance operational workflow and ensure worker safety. Delving into the mechanics behind these upenders could significantly boost your industrial productivity and safety. Let’s explore the details.
1. What is the Frame and Its Importance?
In every industrial setting, robust equipment is key to efficiency. Mold upenders with a solid frame ensure reliable performance. Let’s uncover what makes a frame indispensable.
The frame of a mold upender provides structural integrity, allowing it to hold substantial weights safely. A durable frame withstands wear and tear, reducing maintenance needs and ensuring longer machine lifespan. It’s the backbone for operating under high-stress conditions in an industrial environment.

The Backbone of Mold Upenders: Frame Analysis
The frame is the primary structural element that supports the entire mold upender. It is constructed using high-strength materials, typically steel, designed to hold heavy molds during operations. The robustness of the frame directly influences safety and operational efficiency.
Key Attributes of Frames | Description |
---|---|
Material | Constructed with high-grade steel for maximum durability. |
Design | Engineered to evenly distribute weight, preventing strain on specific areas. |
Load Capacity | Frames are rated to handle loads significantly heavier than average mold weights. |
Maintenance | Requires minimal maintenance, typically only periodic inspections for rust or stress. |
Frames are the unsung heroes in the world of mold upenders. They ensure everything from load-bearing efficiency to operational safety. When selecting a mold upender, always prioritize those with a proven durable frame. A robust frame relates directly to the machine’s stability and usage longevity, reducing downtime and enhancing productivity. As I recall from my extensive career, placing emphasis on the platform’s reliability is the cornerstone for any industrial device’s success.
The strategic selection and maintenance of a mold upender’s frame play a pivotal role in driving both safety and efficiency, safeguarding the long-term investment in your operations.
2. How Does the Electrical System Drive Efficiency in Mold Upender?
The efficiency of mold handling machinery is essential for competitive businesses. By leveraging advanced electrical systems, companies can enhance operational performance, reduce downtime, and maximize profit margins. Let’s explore how electrical systems in mold upenders and mold tipper upenders can transform your workflow.
Electrical systems empower mold upender and mold tipper upender machines by providing precise control and seamless integration. These systems maximize operation speed, accuracy, and energy efficiency, drastically reducing human error and enhancing overall reliability.
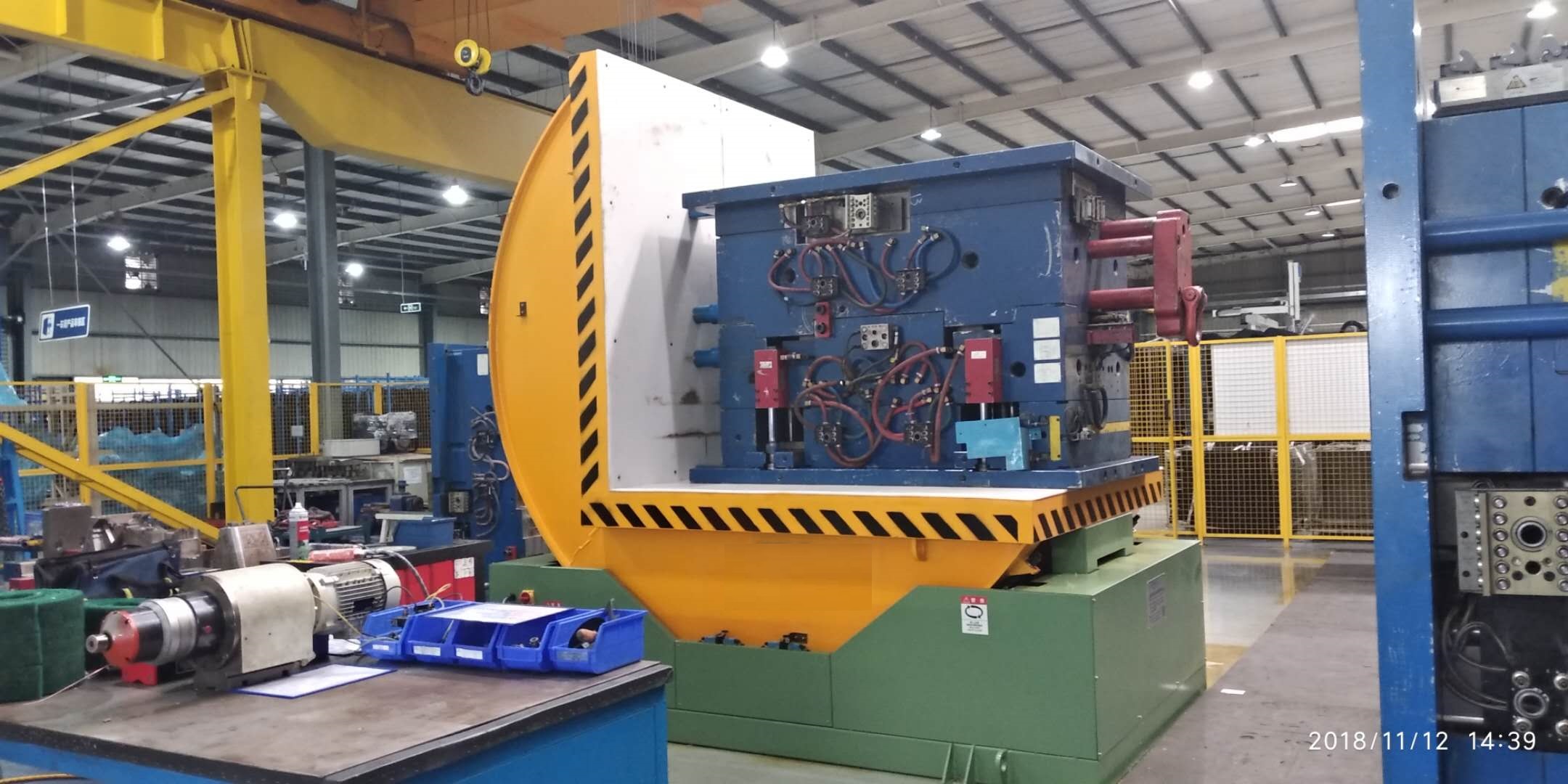
Advanced Electrical Systems for Mold Upenders and Mold Tipper Upenders
Electric-driven mold handling machines are reshaping industries, but what makes them so crucial? The secret lies in their ability to manage machinery operations with exceptional precision and energy efficiency, resulting in noticeable productivity gains.
Advantages | Description | Impact on Efficiency |
---|---|---|
Precise Control | Electric systems allow for fine-tuned adjustments. | Reduces operational errors and waste. |
Seamless Integration | Easily integrates into existing production systems. | Reduces setup time and enhances adaptability. |
Energy Utilization | Maximizes energy efficiency during operation. | Lowers overall energy costs, improving sustainability. |
I recall a project where we installed a high-performance electrical system in a mold tipper upender at a client’s facility. They experienced a 30% improvement in operational efficiency within just the first three months. This real-world example underscores the transformative power of optimized electrical systems in enhancing productivity and minimizing downtime.
3. Why are Safety Features Crucial in Mold Upender and Mold Turning Machines?
Automation in mold handling brings unmatched efficiency, but it also comes with certain risks. Protecting both machinery and personnel through safety features is essential. Let’s dive into why safety is crucial in the operation of mold upenders and mold turning machines.
Safety features are critical in reducing the risks associated with automated mold handling machinery. These features ensure the safety of operators, prevent accidents, and protect both equipment and the workforce. Investing in robust safety systems is key to maintaining business continuity.

Essential Safety Features in Mold Upender and Mold Turning Machines
Understanding the importance of safety in mold upender and turning machine operations is essential for manufacturers. Safety features are not only there to prevent accidents but also enhance productivity by ensuring safe and smooth operations. Below, we’ll look at the types of safety features that are necessary for mold handling machines.
Safety Features | Functionality | Operational Benefit |
---|---|---|
Emergency Stop | Immediate shutdown when unsafe conditions are detected. | Prevents accidents and damages. |
Light Curtains | Sensors that prevent intrusion in the operation zone. | Safeguards operators from injury. |
Safety Interlocks | Prevents machine operation under unsafe conditions. | Ensures safe, predictable operations. |
Overload Protection | Detects and stops the machine if it’s operating beyond safe limits. | Prevents equipment damage and extends machine lifespan. |
A few years ago, I witnessed the dire consequences of failing to implement proper safety features when a malfunction in a mold turning machine resulted in substantial damages at a colleague’s facility. Since then, I’ve been a staunch advocate for the inclusion of comprehensive safety systems in all mold handling operations. The peace of mind, reduced risk of accidents, and long-term savings they offer are invaluable.
Conclusion
Understanding the main components of packaging machinery helps optimize manufacturing workflows, ensuring safety, stability, and efficiency. This knowledge is essential for engineers and technicians involved in packaging operations.
Understanding the main components of mould upenders helps optimize manufacturing workflows, ensuring safety, stability, and efficiency. This knowledge is essential for engineers and technicians involved in mould handling operations.