What Is the Difference Between Electric and Hydraulic Mold Upenders?
Are you struggling with the cumbersome and risky task of flipping heavy molds in your manufacturing facility? Mold upenders offer a safer and more efficient solution, but understanding the differences between electric and hydraulic models is crucial for making the right choice.
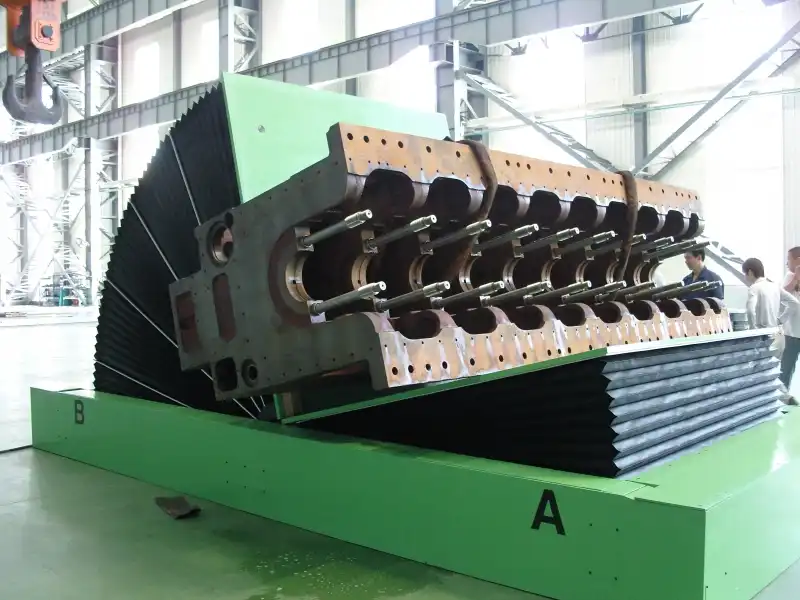
Electric mold upenders utilize electric motors for precise control and cleaner operation, ideal for lighter loads and environments sensitive to hydraulic leaks. Hydraulic mold upenders, on the other hand, employ hydraulic cylinders to provide greater power and lifting capacity, making them suitable for very heavy molds and demanding industrial applications. The choice depends on your specific weight requirements, precision needs, and operational environment.
This article will delve into the key distinctions between these two types of mold upenders, providing you with the knowledge to select the best option for your specific needs and optimize your mold handling processes.
Hydraulic Mold Upenders: Power and Precision for Heavy Lifting
When dealing with exceptionally heavy molds, power and controlled movement are paramount. Hydraulic mold upenders are engineered to meet these demands, providing the strength and precision necessary for handling the heaviest and most valuable molds in manufacturing environments.
Hydraulic mold upenders are characterized by their use of hydraulic cylinders, which generate immense force to lift and rotate heavy molds. This technology excels in applications requiring significant lifting capacity and precise control over movement. They are particularly advantageous when handling molds exceeding several tons, offering a robust and reliable solution for heavy-duty operations.
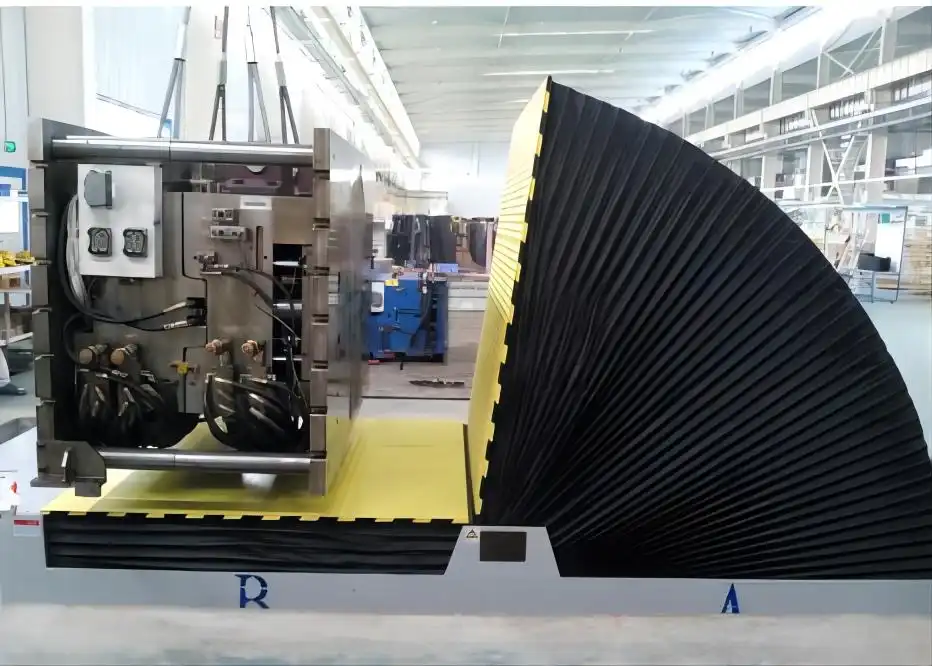
Delving Deeper into Hydraulic Mold Upender Technology
Hydraulic mold upenders are sophisticated systems designed for heavy lifting with controlled precision. Their advantages stem from the fundamental principles of hydraulics, offering benefits in power, control, and safety.
The Power of Hydraulic Systems
Hydraulic systems operate on Pascal’s law, which states that pressure applied to a confined fluid is transmitted equally in all directions. In hydraulic mold upenders, this principle is harnessed to generate immense force using hydraulic cylinders. These cylinders convert hydraulic pressure into linear motion, providing the lifting and rotating power required for heavy molds.
Precision and Smooth Operation
One of the key advantages of hydraulic systems is their ability to provide smooth and precisely controlled motion. The flow of hydraulic fluid can be easily regulated, allowing operators to adjust the speed and force of the upender. This level of control is crucial when handling delicate or unbalanced molds, minimizing the risk of damage during flipping. This precise control is essential for tasks where even slight jerking motions could compromise the mold’s integrity or operator safety.
Safety Features in Hydraulic Design
Safety is a critical consideration in heavy machinery, and hydraulic mold upenders incorporate several features to ensure safe operation:
- Overload Protection: Pressure relief valves are integral to hydraulic systems, preventing overloading by releasing pressure if the load exceeds the machine’s capacity. This safeguards both the upender and the mold from damage.
- Emergency Stop Mechanisms: Strategically located emergency stop buttons allow for immediate halting of the upender’s operation in emergency situations, enhancing operator safety.
- Holding Valves for Load Security: These valves prevent the load from unintentionally dropping in the event of hydraulic pressure loss, providing an extra layer of safety during operation.
- Controlled Descent Systems: Hydraulic systems can be engineered for slow and controlled descent, preventing sudden drops and potential damage to the mold or the surrounding environment.
Maintenance Considerations for Hydraulic Upenders
While offering numerous advantages, hydraulic systems require regular maintenance to ensure optimal performance and longevity. This includes:
- Regular Fluid Checks and Changes: Hydraulic fluid needs to be checked for contamination and replaced periodically to maintain system efficiency and prevent wear.
- Inspection of Hoses and Seals: Hydraulic systems rely on hoses and seals to contain pressurized fluid. Regular inspection and timely replacement of worn components are crucial to prevent leaks and system failures.
- Pump and Valve Maintenance: The hydraulic pump and valves are critical components that require periodic inspection and maintenance to ensure smooth and reliable operation.
Feature | Hydraulic Upender |
---|---|
Lifting Capacity | Very High (10+ tons) |
Control | Precise, Smooth, Variable Speed |
Speed | Adjustable, Controlled |
Maintenance | Moderate, Regular Fluid/Component Checks |
Initial Cost | Generally Higher |
Automation | Easily Integrated |
Noise Level | Relatively Quiet |
Best Suited For | Heavy Molds, Precision Applications |
Electric Mold Upenders: Clean, Precise, and Energy-Efficient
For applications where cleanliness, precision, and energy efficiency are priorities, electric mold upenders present a compelling alternative. These systems offer distinct advantages, particularly for lighter to medium-weight molds and sensitive operating environments.
Electric mold upenders utilize electric motors and drives to perform the lifting and rotating functions. This design offers benefits such as cleaner operation due to the absence of hydraulic fluids, enhanced precision through digital controls, and improved energy efficiency. They are an excellent choice for facilities prioritizing environmental considerations or handling molds in cleanroom environments.
Exploring the Strengths of Electric Mold Upenders
Electric mold upenders offer a different set of advantages compared to their hydraulic counterparts. Their strengths lie in precision, cleanliness, and efficiency, making them well-suited for specific applications.
Precision and Control with Electric Drives
Electric motors, especially servo motors, offer exceptional precision and responsiveness. In electric mold upenders, these motors are coupled with sophisticated digital control systems, allowing for highly accurate positioning and movement. Operators can program precise flipping angles and speeds, ensuring consistent and repeatable operation, which is particularly beneficial for delicate molds or automated processes.
Clean and Environmentally Friendly Operation
A significant advantage of electric mold upenders is their clean operation. Unlike hydraulic systems, they do not rely on hydraulic fluids, eliminating the risk of leaks and potential contamination. This makes them ideal for cleanroom environments, such as those in the pharmaceutical or electronics industries, where even minor fluid leaks can be detrimental. Furthermore, the absence of hydraulic fluid reduces environmental concerns related to disposal and potential spills.
Energy Efficiency and Reduced Operating Costs
Electric mold upenders are generally more energy-efficient than hydraulic systems. Electric motors consume power only when they are actively operating, whereas hydraulic systems often require continuous operation of pumps to maintain pressure. This on-demand power consumption of electric systems leads to significant energy savings over time, reducing operating costs and contributing to a more sustainable manufacturing operation.
Lower Maintenance Requirements
Electric mold upenders typically require less maintenance compared to hydraulic systems. The absence of hydraulic fluids eliminates the need for fluid checks, filter replacements, and hose inspections. Maintenance primarily focuses on the electric motors, drives, and mechanical components, which often have longer service intervals and are easier to maintain.
Feature | Electric Upender |
---|---|
Lifting Capacity | Moderate (Up to ~5-10 tons typically) |
Control | Highly Precise, Digital Control |
Speed | Programmable, Adjustable |
Maintenance | Lower, Primarily Mechanical/Electrical |
Initial Cost | Moderate to Higher |
Automation | Excellent Integration, Precise Control |
Noise Level | Generally Quieter |
Best Suited For | Lighter Molds, Clean Environments, Precision |
Choosing Between Hydraulic and Electric Mold Upenders: Key Considerations
Selecting the right mold upender is a critical decision that impacts operational efficiency, safety, and cost-effectiveness. The choice between hydraulic and electric systems depends on a careful evaluation of your specific needs and priorities.
The selection between hydraulic and electric mold upenders hinges on factors like load weight, precision needs, budget, and operating environment. Hydraulic upenders are superior for heavy loads and high power demands, while electric models excel in precision, cleanliness, and energy efficiency. A thorough assessment of your specific application is essential for making the optimal choice.
A Detailed Comparison: Hydraulic vs. Electric Mold Upenders
To make an informed decision, consider these key comparison points:
Lifting Capacity: Matching the Upender to Mold Weight
The primary factor in choosing between hydraulic and electric mold upenders is the weight of the molds you need to handle.
- Hydraulic: Unmatched in lifting capacity, hydraulic upenders are the clear choice for very heavy molds, often exceeding 10 tons. They can handle extremely large and heavy tooling with ease and stability.
- Electric: Electric upenders are suitable for lighter to medium-weight molds, typically up to 5-10 tons. While capable for many applications, they are generally not designed for the extreme loads that hydraulic systems can manage.
Precision and Control: Accuracy in Mold Handling
The level of precision required for your mold handling process is another crucial consideration.
- Hydraulic: Offer good control, especially with proportional valves, allowing for adjustable speed and force. However, achieving extremely fine movements can be more challenging compared to electric systems.
- Electric: Excel in precision due to servo motor technology and digital controls. They provide highly accurate positioning and repeatable movements, ideal for delicate molds and automated processes.
Energy Efficiency and Operating Costs: Long-Term Savings
Energy consumption and long-term operating costs should be factored into your decision.
- Hydraulic: Can be less energy-efficient as pumps often run continuously. Energy consumption is generally higher, leading to increased operating costs over time.
- Electric: More energy-efficient due to on-demand power consumption. Lower energy consumption translates to reduced operating costs and a smaller environmental footprint.
Maintenance: Ensuring Uptime and Longevity
Maintenance requirements and ease of maintenance are important for minimizing downtime and ensuring the longevity of your equipment.
- Hydraulic: Require more regular and specialized maintenance, including fluid checks, hose and seal inspections, and potential repairs of pumps and valves. Maintenance can be more complex and may require specialized technicians.
- Electric: Generally require less maintenance. Maintenance is primarily focused on mechanical and electrical components, which are often easier to access and maintain. The absence of hydraulic fluid simplifies maintenance and reduces potential issues like leaks.
Initial Investment and Budget: Balancing Cost and Performance
The initial purchase price and your budget constraints are always important considerations.
- Hydraulic: Typically have a lower initial purchase price compared to electric upenders, especially for basic models.
- Electric: Often have a higher initial cost due to the more advanced servo motors and control systems. However, the long-term energy savings and reduced maintenance can offset the higher initial investment over time.
Feature | Hydraulic Upender | Electric Upender | Key Consideration |
---|---|---|---|
Lifting Capacity | Very High | Moderate | Mold Weight |
Control | Good, Adjustable Speed | Highly Precise, Digital Control | Precision Requirements |
Energy Efficiency | Lower | Higher | Operating Costs, Environmental Impact |
Maintenance | More Complex, Regular Fluid Checks | Simpler, Primarily Mechanical/Electrical | Downtime, Maintenance Expertise |
Initial Cost | Generally Lower | Moderate to Higher | Budget |
Best For | Heavy Molds, High Power Demands | Lighter Molds, Precision, Cleanliness | Application Needs |
Mold Upender Applications: Enhancing Safety and Efficiency
Mold upenders are versatile pieces of equipment with applications across various industries where heavy molds and dies need to be safely and efficiently handled. Their use significantly improves workplace safety and streamlines mold handling processes.
Mold upenders are used across diverse industries, including plastic injection molding, die casting, and metal stamping. They facilitate safe and efficient mold handling, reducing manual labor and the risk of injury. Whether hydraulic or electric, mold upenders offer a significant improvement over manual methods, enhancing both safety and productivity in mold handling operations. The choice between hydraulic and electric models depends on the specific demands of the application, with hydraulic excelling in heavy-duty scenarios and electric favored for precision and clean environments.
Mold upenders find applications in:
- Plastic Injection Molding: For flipping and rotating molds for maintenance, repair, and storage.
- Die Casting: Handling heavy dies for die casting machines.
- Metal Stamping: Rotating and tilting dies for stamping presses.
- Manufacturing and Machining: Any industry requiring the manipulation of heavy and bulky molds, dies, or workpieces.
Conclusion
Choosing between electric and hydraulic mold upenders involves carefully considering your specific operational needs. Hydraulic systems provide unmatched power for heavy molds, while electric systems excel in precision, cleanliness, and efficiency for lighter applications. By evaluating your load requirements, precision needs, budget, and long-term operational goals, you can select the mold upender that best optimizes your mold handling processes, ensuring both safety and productivity in your manufacturing environment. Consider exploring mold upender solutions to further enhance your facility’s efficiency.