What Customized Solutions Are Available for Steel Coil Packing?
In the coil packaging industry, generic solutions often fall short. Businesses require tailored approaches due to varying coil sizes, materials, production volumes, and facility layouts. Customization provides the key to designing coil packing lines that precisely meet unique operational demands. This leads to significant improvements in efficiency and overall productivity.
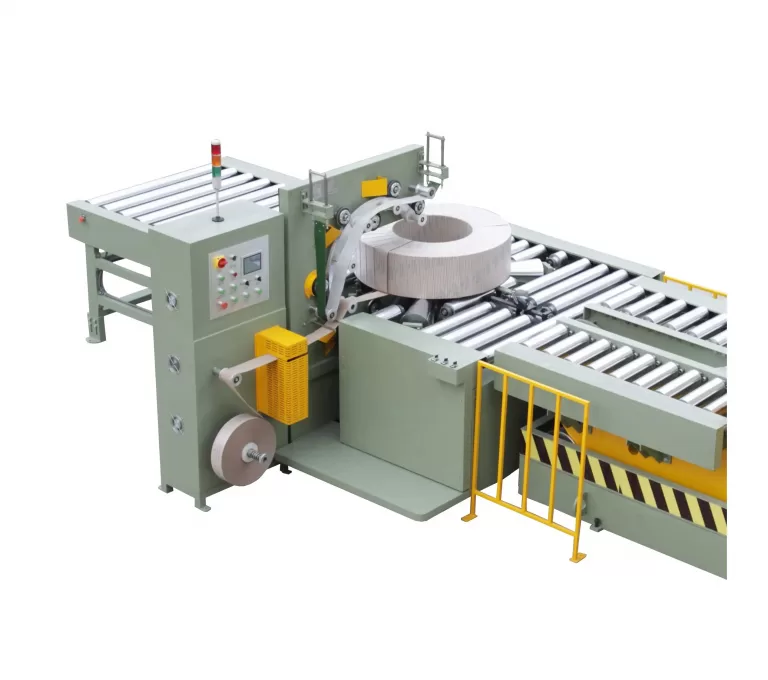
Customized solutions for steel coil packing encompass a range of adaptations, including machinery calibrated for specific coil dimensions and weights, layout configurations optimized for facility space, and automation levels tailored to production volume. These solutions also integrate seamlessly with existing systems, offering flexibility for future scalability and enhanced operational efficiency.
To truly optimize your steel coil packaging process and gain a competitive edge, understanding the breadth of available customized solutions is essential. Let’s delve into the specifics of how tailored approaches can revolutionize your operations.
1. Optimizing for Your Coil Specifications
The cornerstone of effective coil packing lies in addressing the unique specifications of your coils. A universal approach simply cannot guarantee the protection and efficient handling required for diverse coil types and sizes. Customized solutions provide this necessary precision.
Customizing your steel coil packing line to match your specific coil dimensions, materials (steel, aluminum, copper, etc.), and weight is paramount. This ensures coils are properly supported and protected during packaging and transit, minimizing damage. Tailored solutions improve product quality, reduce material waste from damage, and ultimately boost customer satisfaction by delivering pristine products.

Deep Dive: Tailoring Precision for Diverse Coil Types
The variance in steel coil specifications is vast. From narrow slit coils to wide jumbo coils, and from light gauge to heavy gauge steel, each type presents unique packaging challenges. A customized approach meticulously considers these variables, ensuring optimal handling and protection at every stage. Let’s examine how tailored solutions address specific coil characteristics:
Understanding Coil Variability
To effectively customize a packing line, a detailed analysis of coil specifications is the first crucial step. This involves not only understanding the current product range but also anticipating future product diversification. Key factors to consider include:
- Dimensions: Outer Diameter (OD), Inner Diameter (ID), Width, and Thickness. These dimensions directly impact machine size requirements and wrapping material consumption.
- Weight: Coil weight dictates the necessary load-bearing capacity of machinery and material handling systems.
- Material: Steel grade (carbon steel, stainless steel, alloy steel) and surface finish influence the required level of protection against corrosion and surface damage.
- Coil Type: Slit coils, ribbon coils, traverse wound coils, and pancake coils each require different handling and wrapping techniques.
Customized Machine Features for Specific Coil Needs
Based on the coil specification analysis, customized packing solutions incorporate specific features to optimize performance. Here are some examples:
Feature | Standard Machine | Customized Machine | Benefit of Customization |
---|---|---|---|
Wrapping Ring Size | Fixed size, may accommodate a range of coil sizes | Variable or interchangeable rings, sized for specific OD ranges | Optimal wrapping material usage; reduced material waste for smaller coils; secure wrapping for larger coils. |
Tension Control | Generic tension settings | Programmable tension control based on coil material and thickness | Prevents damage to delicate materials; ensures tight and secure wrapping for heavy gauge coils. |
Support Rollers | Standard roller configuration | Adjustable roller positions and materials to match coil ID and OD | Prevents coil deformation; ensures even weight distribution; accommodates coils with varying IDs. |
Material Applicators | Single, fixed applicator | Multiple applicators or interchangeable heads for different materials (stretch film, paper, VCI) | Flexibility to use optimal wrapping materials for different coil types and storage conditions; brand differentiation through varied packaging. |
By meticulously tailoring each component of the packing line to the specific coil specifications, manufacturers can achieve significant improvements in efficiency, product protection, and overall packaging quality. This precision-driven approach minimizes risks and maximizes ROI.
2. Maximizing Throughput and Efficiency
Throughput is the lifeblood of any production line. A bottleneck in coil packing directly impacts overall productivity and profitability. Customized solutions are designed to eliminate these bottlenecks and optimize the flow of coils through the packaging process.
Customization is crucial for maximizing throughput and efficiency in steel coil packing. By analyzing production volumes, facility layout, and staffing, tailored solutions optimize workflow and minimize bottlenecks. This results in higher productivity, faster turnaround times, and improved profitability, giving businesses a significant competitive advantage.
Enhancing Operational Flow: Tailored Systems for Peak Performance
Beyond individual machine customization, optimizing the entire packaging line layout and material flow is critical for maximizing throughput. A holistic approach to customization considers how each stage of the process – from coil infeed to packaged coil outfeed – can be streamlined.
Analyzing Bottlenecks and Optimizing Layout
A thorough assessment of current operations is the starting point for throughput optimization. This involves identifying bottlenecks, analyzing material flow, and evaluating space utilization. Key areas of focus include:
- Current Throughput: Measuring coils processed per hour and identifying peak demand periods.
- Facility Layout: Analyzing space constraints, material handling pathways, and potential for line expansion.
- Manual vs. Automated Processes: Identifying areas where automation can replace manual tasks to increase speed and reduce labor costs.
- Material Handling Systems: Evaluating the efficiency of conveyors, cranes, forklifts, and other material movement equipment.
Customized Line Design for Optimized Workflow
Based on the bottleneck analysis, a customized packing line design can incorporate various strategies to enhance throughput:
- Optimized Machine Sequencing: Arranging machines in a logical flow to minimize coil movement and waiting times. For example, integrating slitting and packing lines for continuous processing.
- Automated Material Transfer: Implementing conveyor systems, robotic arms, or automated guided vehicles (AGVs) to move coils between processing stations without manual intervention.
- Parallel Processing: Utilizing multiple wrapping stations or parallel lines to handle increased volume during peak production periods.
- Buffer Zones: Incorporating buffer zones between machines to absorb fluctuations in processing times and prevent line stoppages.
- Ergonomic Design: Optimizing workstation layouts and equipment heights to minimize operator fatigue and improve efficiency in manual tasks.
By strategically designing the packing line layout and integrating automation where appropriate, customized solutions can significantly boost throughput, reduce cycle times, and improve the overall efficiency of steel coil packaging operations. This leads to increased output and reduced per-coil processing costs.
3. Seamless Integration with Existing Systems
A new coil packing line shouldn’t operate in isolation. Seamless integration with existing facility infrastructure and systems is vital for a smooth transition and maximized efficiency. Customization addresses this integration challenge directly.
Customized coil packing lines offer seamless integration with existing systems and infrastructure. Tailoring solutions to work with current layouts, material handling equipment, and IT systems ensures a smooth transition and minimal disruption. Integration encompasses conveyors, cranes, software, and controls, streamlining data exchange and enhancing process visibility across packaging operations.
Harmonizing New and Existing Infrastructure: A Phased Integration Approach
Integrating a new coil packing line into an existing facility requires careful planning and a phased approach to minimize disruption and ensure compatibility. Customization plays a key role in achieving this seamless integration.
Integration Points and Considerations
Successful integration requires identifying all potential interface points between the new packing line and existing systems. Key integration areas include:
- Physical Layout Integration: Matching the new line’s footprint to available space, connecting conveyors, and ensuring compatibility with existing building structures.
- Material Handling Equipment Integration: Interfacing with existing cranes, forklifts, AGVs, and conveyor systems for efficient coil transfer.
- Control System Integration: Connecting the new packing line’s PLC and control systems with the facility’s central control system for unified monitoring and data acquisition.
- Software and Data Integration: Integrating with existing ERP, WMS, and MES systems for seamless data exchange on production schedules, inventory, and packaging parameters.
- Safety System Integration: Ensuring the new line’s safety features are compatible with and integrated into the facility’s overall safety management system.
Benefits of Seamless Integration
A well-integrated coil packing line offers numerous benefits beyond just operational efficiency. These advantages contribute to a more streamlined and data-driven manufacturing environment:
Integration Aspect | Standard Approach | Customized Integration | Benefits |
---|---|---|---|
Data Management | Isolated data silos for new and existing systems | Unified data platform; real-time data sharing across systems | Improved production tracking; enhanced inventory management; better data-driven decision-making. |
Operational Efficiency | Potential bottlenecks at system interfaces | Streamlined material flow; automated data exchange; reduced manual data entry | Minimized delays; faster response times to production changes; optimized resource utilization. |
Maintenance & Diagnostics | Separate monitoring systems | Integrated system monitoring; centralized diagnostics | Simplified troubleshooting; faster fault identification; reduced downtime; proactive maintenance planning. |
Scalability | Complex integration for future expansions | Modular design; pre-engineered integration interfaces | Easier and faster expansion or modification of the packing line; future-proof investment. |
By prioritizing seamless integration through customization, manufacturers can avoid operational disruptions, maximize data visibility, and create a more cohesive and efficient manufacturing ecosystem. This holistic approach ensures that the new coil packing line becomes a valuable asset that enhances, rather than complicates, existing operations.
4. Flexibility for Future Growth and Changes
Business landscapes are dynamic. A coil packing solution must not only meet current needs but also adapt to future growth, product diversification, and evolving market demands. Customization offers this crucial future-proofing capability.
Investing in a customized coil packing line provides inherent flexibility for future growth and adaptation. These solutions are designed with scalability in mind, allowing for easy modification and expansion as business needs evolve. Whether accommodating new products, increased volumes, or changing market demands, customized lines offer a future-proof investment, avoiding costly replacements and ensuring long-term value. Customization ensures your packaging infrastructure can evolve with your business.
Customized solutions are not static; they are designed to evolve. Scalability and adaptability are built into the core design principles, ensuring that your investment remains relevant and valuable for years to come. This future-proof approach is essential in today’s rapidly changing manufacturing environment.
Conclusion
Customizing your steel coil packing line transcends simply purchasing equipment; it’s a strategic investment in operational excellence. By tailoring solutions to your specific coil specifications, maximizing throughput, ensuring seamless integration, and building in future flexibility, you unlock significant advantages. Customized coil packing drives efficiency, boosts productivity, enhances brand value through tailored packaging, and ultimately delivers a strong return on investment, securing a competitive edge in the steel industry. Embracing customization is the key to transforming your coil packaging from a mere process into a powerful driver of business success.