1. What Are the Waterproofing Requirements for Steel Coil Packing?
Waterproofing in steel coil packing is not just recommended; it’s a critical necessity. Steel, inherently susceptible to corrosion, faces significant risks from moisture during storage and transit. Understanding these waterproofing requirements is crucial for maintaining steel coil integrity.
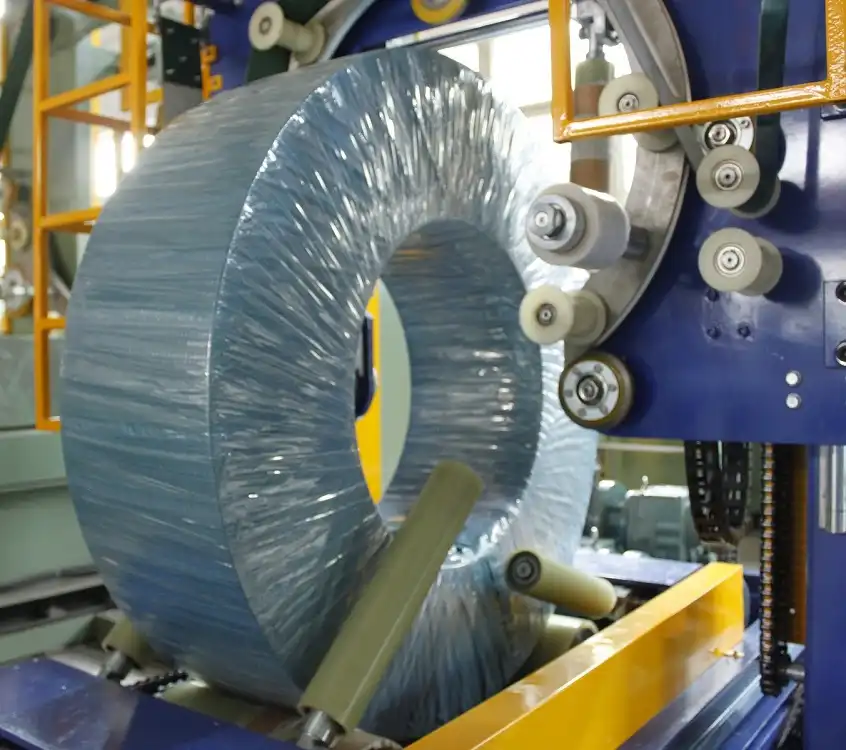
Waterproofing requirements for steel coil packing are centered on preventing moisture ingress. This involves utilizing barrier materials like waterproof films, applying protective coatings, and incorporating desiccants within the packaging. The specific requirements vary based on environmental exposure, storage duration, and steel sensitivity, demanding tailored strategies to ensure effective moisture protection and prevent corrosion.
Therefore, understanding the nuances of waterproofing for steel coil packing is paramount. Let’s delve into the key aspects that define effective waterproofing for steel coils, ensuring longevity and preventing costly damage.
2. Understanding the Critical Need for Waterproofing Steel Coils
Waterproofing is indispensable for steel coil packing due to steel’s vulnerability to moisture-induced corrosion. Without proper waterproofing, steel coils are highly susceptible to rust, leading to structural weakening and significant economic losses.
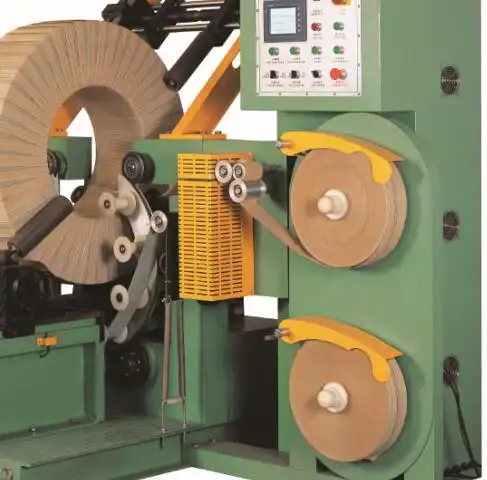
The necessity of waterproofing stems from the inherent properties of steel. Exposure to moisture initiates corrosion, which compromises the steel’s tensile strength and structural integrity. This degradation can lead to premature failure, especially in demanding applications. Waterproofing acts as a crucial barrier, preserving the steel’s properties and ensuring its intended performance throughout its lifespan.
To fully grasp the importance of waterproofing, let’s examine the detrimental effects of moisture on steel coils and explore the different types of corrosion that can occur if adequate protection is not in place.
Delving Deeper: The Science of Corrosion and Steel Coil Degradation
Moisture’s impact on steel coils extends beyond surface blemishes; it initiates electrochemical reactions that corrode the metal from within. This insidious process, often invisible until significant damage is done, requires a comprehensive understanding to combat effectively.
Types of Corrosion Affecting Steel Coil Packing
Different forms of corrosion pose unique threats to steel coils. Understanding these types is crucial for implementing targeted prevention strategies.
Corrosion Type | Description | Impact on Steel Coil Packing | Prevention Methods |
---|---|---|---|
General Rusting | Uniform corrosion across the surface due to humidity and oxygen. | Overall weakening, reduced diameter, diminished tensile strength. | Barrier coatings, waterproof wraps, desiccants. |
Pitting Corrosion | Localized corrosion creating pits or holes, often under debris or contaminants. | Concentrated stress points, localized weakening leading to fracture. | Thorough cleaning before packing, protective films, controlled storage environments. |
Galvanic Corrosion | Accelerated corrosion when dissimilar metals contact in moisture. | Rapid degradation of less noble metal, especially at contact points. | Avoid dissimilar metal contact, insulating barriers, apply coatings. |
Crevice Corrosion | Corrosion in confined spaces where moisture and contaminants accumulate. | Hidden corrosion, difficult to detect, weakens wire within packed coil. | Tight wrapping, desiccants within packaging, sealed containers. |
Comprehensive waterproofing strategies must address these diverse corrosion types to guarantee the long-term preservation of steel coils. This involves selecting appropriate materials and application techniques tailored to the specific environmental risks and storage conditions.
3. Essential Waterproofing Materials for Steel Coil Packing
Selecting the correct waterproofing materials is vital for effective moisture protection of steel coils. These materials must not only repel water but also endure the stresses of handling, storage, and transportation.
Effective waterproofing relies on materials that create a robust barrier against moisture. Common choices include polyethylene (PE) films for basic protection, vapor corrosion inhibitors (VCIs) for chemical defense, and desiccants for moisture absorption. The optimal selection depends on factors like budget, required protection level, and specific environmental challenges.
Let’s explore the properties and applications of these essential waterproofing materials in detail to understand how they contribute to comprehensive moisture protection for steel coils.
Material Breakdown: Choosing the Right Barrier for Steel Coils
The selection of waterproofing materials should be driven by a careful assessment of environmental risks and the desired lifespan of the steel coil packing. Each material offers unique advantages and is suited to different levels of protection.
Material | Description | Advantages | Considerations |
---|---|---|---|
Polyethylene (PE) Films | Cost-effective plastic films providing a basic waterproof barrier. Available in various thicknesses. | Economical, widely available, provides basic waterproof barrier. | Basic protection, may not be sufficient for long-term or harsh environments. |
Vapor Corrosion Inhibitor (VCI) Films/Papers | Materials releasing corrosion-inhibiting vapors, creating a protective atmosphere around the steel. | Prevents rust even in humid conditions, ideal for long-term storage, offers chemical protection. | Can be more expensive than PE films, effectiveness depends on proper enclosure. |
Desiccants (Silica Gel, Clay) | Moisture-absorbing agents placed inside packaging to maintain a low-humidity environment. | Crucial for long-term storage, absorbs moisture that penetrates packaging, cost-effective humidity control. | Requires proper quantity calculation based on package volume and environment, needs replacement when saturated. |
Waterproof Tapes & Sealants | Used to seal overlaps and seams in wrapping materials, ensuring a continuous waterproof barrier. | Ensures complete barrier integrity, essential for sealing gaps and overlaps, enhances overall waterproofing effectiveness. | Correct application is crucial for effectiveness, material compatibility with wraps is important. |
Laminated Woven Fabrics | Strong woven fabrics combined with waterproof coatings for robust protection. | Robust protection against moisture and physical damage, durable for handling and transportation. | Higher cost compared to PE films, may be overkill for less demanding applications. |
Shrink Wrap Films | Plastic films that shrink tightly when heated, creating a secure and waterproof seal. | Secure and conforming waterproof seal, excellent for unitizing and stabilizing coils, provides good tear resistance. | Requires heat application equipment, may not be suitable for heat-sensitive steels. |
The strategic combination of these materials, based on a thorough understanding of their properties and limitations, is key to achieving optimal waterproofing for steel coil packing.
4. Application Techniques and Quality Control in Steel Coil Waterproofing
Even the best waterproofing materials can fail if improperly applied. The effectiveness of moisture protection for steel coils hinges on meticulous application techniques and rigorous quality control.
Effective waterproofing application involves several key steps: pre-cleaning the steel coil, applying primary waterproof wrapping tightly, sealing all seams and overlaps, and incorporating desiccants. Both manual and automated methods exist, each with specific advantages depending on production volume and required consistency. Quality control is equally vital, involving visual inspections, adhesion tests, and humidity monitoring to ensure ongoing protection.
Let’s examine the best practices for applying waterproofing materials and implementing quality control measures to guarantee robust and reliable moisture protection for steel coils.
Best Practices: Manual vs. Automated Waterproofing Application
The choice between manual and automated waterproofing application depends on production scale, budget, and desired consistency. Both methods have their place in ensuring effective moisture protection for steel coils.
Feature | Manual Waterproofing | Automated Waterproofing (using coil packing machines) |
---|---|---|
Consistency | Variable; depends on operator skill. | Highly consistent; machine-controlled application. |
Speed | Slower; labor-intensive. | Faster; higher throughput. |
Material Usage | Can be less efficient; potential for waste. | Optimized material usage; reduces waste. |
Labor Costs | Higher labor costs. | Lower labor costs; automation reduces manpower. |
Seal Quality | Seal quality can vary. | Consistent and reliable sealing. |
Suitability | Lower volume production; customized packing. | High volume production; standardized packing. |
Initial Investment | Lower initial investment. | Higher initial investment in machinery. |
Automated coil packing machines offer superior consistency and efficiency, particularly for high-volume operations. These machines can be programmed to apply wrapping materials with precise tension and overlap, ensuring a consistently robust waterproof seal. However, manual waterproofing remains relevant for lower volume, customized packing needs where operator skill can ensure quality.
Quality Control: Ensuring Long-Term Waterproofing Integrity
Waterproofing is not a one-time process; it demands continuous quality control and testing to guarantee lasting effectiveness. Regular checks and tests are crucial to identify potential weaknesses and prevent costly corrosion-related failures.
Quality Control Method | Description | Purpose |
---|---|---|
Visual Inspection | Checking for tears, punctures, or inadequate sealing in wrapping. | Identifies obvious flaws in the waterproofing barrier. |
Adhesion Tests | Verifying tapes and sealants are properly adhered, ensuring a continuous barrier. | Confirms the integrity of seals and overlaps. |
Humidity Indicator Strips | Monitoring humidity levels inside packaging during storage and transit. | Detects moisture ingress and desiccant saturation. |
Water Spray Tests | Simulating rain or water exposure to assess package water resistance. | Evaluates package resistance to water penetration under simulated weather conditions. |
Immersion Tests | Submerging packaged coils in water to check for water penetration (stringent requirements). | Assesses waterproofing integrity under extreme conditions. |
Accelerated Aging Tests | Simulating long-term storage conditions to evaluate waterproofing durability. | Predicts long-term waterproofing performance and material degradation over time. |
Implementing a robust quality control system, incorporating these testing methods, is essential for validating the waterproofing process and maintaining the integrity of steel coil packing.
5. Conclusion: Investing in Waterproofing for Steel Coil Protection
Waterproofing is not an optional expense but a fundamental investment for steel coil packing. It is essential for preventing corrosion, maintaining structural integrity, and ensuring the reliable performance of steel in diverse applications. By understanding the types of corrosion, selecting appropriate materials, applying them effectively, and implementing rigorous quality control, manufacturers and distributors can safeguard steel coils against moisture damage, guaranteeing product quality, customer satisfaction, and long-term reliability.
Investing in robust waterproofing measures is an investment in product quality, customer satisfaction, and long-term reliability. For businesses seeking to optimize their coil packing process, exploring advanced solutions like [Collection]’s coil packing machine can significantly enhance waterproofing efficiency and consistency. By prioritizing waterproofing, the steel industry can uphold the quality and performance of its products, ensuring they reach end-users in optimal condition, free from the detrimental effects of moisture and corrosion.