What Are the Safety Risks of Overloading Steel Coil Packing Line Capacity?
Are you pushing your steel coil packing line to its absolute limit, trying to squeeze every ounce of productivity out of it? While maximizing output is crucial, are you aware of the hidden dangers lurking when you overload your packing line capacity? Ignoring these risks can lead to catastrophic equipment failures, severe worker injuries, and significant financial losses.
Overloading a steel coil packing line beyond its designed capacity introduces significant safety risks, including equipment malfunctions, structural failures, increased wear and tear, reduced operational efficiency, and potential worker injuries. These risks compromise both personnel safety and the integrity of the production process.
Understanding and mitigating these risks is not just about compliance; it’s about safeguarding your employees, protecting your investment, and ensuring the long-term efficiency of your steel processing operations. Let’s delve into the critical safety risks associated with overloading steel coil packing line capacity.
Understanding the Immediate Dangers of Overloading
Imagine a critical component in your steel coil packing line suddenly giving way under excessive stress. The chaos, the downtime, the potential for injury – all stemming from a single decision to push beyond safe limits. Overloading isn’t just about reduced efficiency; it’s a direct path to immediate and severe hazards.
The immediate safety risks of overloading a steel coil packing line capacity include sudden equipment failure, structural damage to the line, and increased risk of accidents and injuries to personnel. Exceeding the designed load limits puts undue stress on all components, leading to breakdowns, potential collapses, and dangerous working conditions.
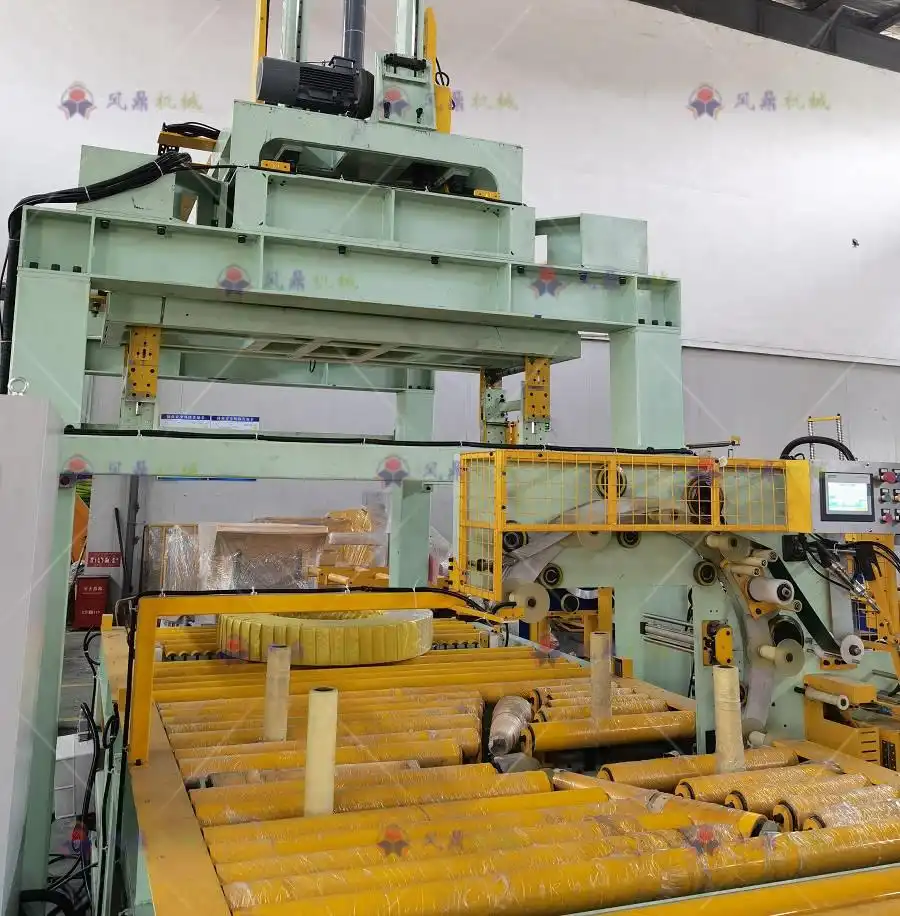
Immediate Consequences of Capacity Exceedance: A Chain Reaction
Overloading a steel coil packing line initiates a dangerous chain reaction, impacting multiple aspects of operational safety and equipment integrity. To truly grasp the magnitude of these risks, we must dissect the immediate consequences:
1. Catastrophic Equipment Failure
- Problem: Packing lines are engineered with specific load limits for each component – conveyors, wrappers, strappers, and handling mechanisms. Exceeding these limits places immense stress on motors, gears, belts, chains, and hydraulic systems.
- Agitation: This stress leads to metal fatigue, component fractures, and outright breakdowns. A conveyor belt can snap under excessive weight, a strapping unit can jam and malfunction, or a critical motor can burn out. These failures are not just inconvenient; they are dangerous. Imagine a heavy coil suddenly dropping from a failed conveyor or a high-speed strapping head malfunctioning due to overload.
- Solution: Adhering strictly to manufacturer-specified capacity limits is paramount. Regular inspections and preventative maintenance are crucial to detect early signs of stress and fatigue before catastrophic failures occur. Implementing load monitoring systems can provide real-time data, preventing accidental overloads.
2. Structural Integrity Compromise
- Problem: The packing line structure itself – the framework, supports, and mounting points – is designed to withstand specific loads. Overloading introduces forces beyond these design parameters.
- Agitation: Continuous overloading can cause bending, warping, and cracking of structural members. Welds can weaken, bolts can shear, and the entire line can become unstable. This structural degradation is often insidious, progressing over time until a critical failure occurs. A structurally compromised line is a collapse hazard, endangering anyone working nearby.
- Solution: Regular structural inspections by qualified engineers are essential, especially for lines that routinely handle heavy loads. Non-destructive testing methods, like ultrasonic testing, can detect hidden cracks and weaknesses. Reinforcing critical structural points and ensuring proper foundation stability are proactive measures to mitigate this risk.
3. Amplified Accident Potential
- Problem: Overloaded lines are inherently less stable and predictable. Increased stress on moving parts elevates the risk of malfunctions and unexpected movements.
- Agitation: This translates directly to a higher likelihood of accidents. Coils can shift or fall during wrapping or strapping, pinch points become more dangerous with increased force, and emergency stops may be less effective under overload conditions. Workers are at heightened risk of crush injuries, lacerations, and impacts from moving machinery or falling coils.
- Solution: Rigorous safety protocols are non-negotiable. Enhanced guarding around pinch points and moving parts, clear and enforced safety zones, and comprehensive worker training on overload risks and emergency procedures are vital. Regular safety audits and risk assessments should be conducted to identify and address potential accident triggers exacerbated by overloading.
By acknowledging and proactively addressing these immediate dangers, operators can significantly reduce the risk of catastrophic events stemming from overloaded steel coil packing lines. It’s not merely about avoiding downtime; it’s about preventing accidents, injuries, and ensuring a safe working environment.
The Long-Term Degradation from Capacity Overload
The immediate dangers of overloading are dramatic, but the insidious long-term consequences can be equally devastating to your operations. Like a slow burn, continuous overloading degrades your equipment, erodes efficiency, and ultimately leads to premature failure and escalating costs.
Long-term risks of overloading steel coil packing line capacity include accelerated wear and tear on components, reduced equipment lifespan, increased maintenance frequency, decreased operational efficiency over time, and a higher total cost of ownership. While immediate failures are dramatic, the cumulative damage from sustained overload erodes the line’s performance and longevity.
The Cumulative Toll of Overloading: A Gradual Decline
The true cost of overloading is often hidden in the gradual decline of your packing line’s performance and the creeping increase in maintenance demands. Understanding this slow degradation is key to justifying capacity adherence and preventative maintenance.
1. Accelerated Wear and Tear
- Problem: Every component in a packing line has a designed lifespan, predicated on operating within specified load limits. Overloading accelerates the wear process exponentially.
- Agitation: Bearings, rollers, belts, chains, gears – all experience increased friction, stress, and heat when overloaded. Lubrication breaks down faster, surfaces wear down more rapidly, and components fatigue sooner. This isn’t just about replacing parts; it’s about increased downtime, more frequent interventions, and a constant battle to keep the line operational.
- Solution: Implementing a proactive maintenance schedule is crucial. Regular lubrication, component inspections, and timely replacements before failure are essential to mitigate accelerated wear. Investing in higher-quality, more robust components designed for heavier duty cycles can also extend component lifespan, although this doesn’t negate the need to adhere to capacity limits.
2. Shortened Equipment Lifespan
- Problem: Continuous overloading doesn’t just wear out individual components; it ages the entire packing line prematurely. The cumulative stress weakens the entire system.
- Agitation: A packing line designed for a 20-year lifespan might see its useful life cut in half, or even less, under consistent overload conditions. This premature obsolescence necessitates earlier and more costly replacements, disrupting long-term capital expenditure planning and impacting overall ROI.
- Solution: Operating within design capacities is the primary strategy for maximizing equipment lifespan. Accurate record-keeping of load history, maintenance logs, and performance data can help track equipment aging and inform strategic replacement planning. Considering future capacity needs when initially selecting equipment can prevent premature aging due to insufficient initial capacity.
3. Escalating Maintenance Demands
- Problem: Overloaded lines require significantly more maintenance – more frequent inspections, more repairs, and more component replacements.
- Agitation: Maintenance costs can skyrocket, eating into profits and diverting resources from other critical areas. Downtime for maintenance becomes more frequent and prolonged, disrupting production schedules and impacting delivery times. The maintenance team becomes reactive, constantly firefighting breakdowns instead of proactively maintaining the line.
- Solution: Shifting from reactive to proactive maintenance is essential. Implementing condition monitoring systems (vibration analysis, thermal imaging) can detect early signs of component degradation, allowing for preemptive maintenance interventions and preventing costly breakdowns. Investing in operator training to recognize and report early warning signs of overload stress can also contribute to proactive maintenance.
4. Diminished Long-Term Efficiency
- Problem: While overloading might seem to boost short-term output, it inevitably leads to decreased long-term efficiency.
- Agitation: Overloaded lines run less smoothly, with increased friction, vibration, and energy consumption. Packing quality can degrade, leading to higher rates of rework or rejected coils. The overall throughput rate, despite the initial push for overload, will eventually decline as the line becomes less reliable and requires more frequent stops for repairs.
- Solution: Focusing on optimizing packing line efficiency within design capacity is more sustainable than chasing short-term gains through overloading. Process optimization, streamlined workflows, and efficient material handling can maximize output without compromising equipment longevity or safety. Regular performance audits and efficiency assessments can identify bottlenecks and areas for improvement within safe operating limits.
By understanding the cumulative toll of overloading, businesses can make informed decisions that prioritize long-term sustainability, equipment longevity, and consistent operational efficiency over the false economy of pushing packing lines beyond their safe capacity limits.
Regulatory and Compliance Factors in Capacity Limits
Beyond the tangible risks to equipment and personnel, overloading steel coil packing lines carries significant regulatory and compliance implications. Ignoring these factors can lead to hefty fines, legal repercussions, and damage to your company’s reputation.
Regulatory bodies and industry standards mandate adherence to equipment capacity limits for steel coil packing lines. Overloading can lead to non-compliance with OSHA regulations, industry-specific safety standards, and insurance policy terms. Such non-compliance can result in fines, operational shutdowns, legal liabilities, and increased insurance premiums.
Navigating the Compliance Landscape: Legal and Financial Repercussions
Compliance isn’t just about avoiding penalties; it’s about demonstrating a commitment to safety and responsible operations. Understanding the regulatory landscape is crucial for mitigating legal and financial risks associated with overloading.
1. OSHA and General Industry Standards
- Problem: OSHA (Occupational Safety and Health Administration) regulations in the US, and similar bodies globally, set comprehensive standards for workplace safety, including material handling and equipment operation. Overloading packing lines directly violates these standards.
- Agitation: OSHA inspections can be triggered by accidents, employee complaints, or routine audits. Violations related to overloading, such as "failure to ensure safe operating conditions" or "improper equipment operation," can result in substantial fines, mandatory corrective actions, and even temporary or permanent operational shutdowns. Repeat violations carry even harsher penalties.
- Solution: Establish a robust safety program that explicitly addresses packing line capacity limits and overload prevention. Conduct regular self-inspections to ensure compliance with OSHA standards. Maintain detailed records of equipment inspections, maintenance, and operator training to demonstrate due diligence in safety management.
2. Industry-Specific Safety Standards
- Problem: Beyond general OSHA regulations, the steel industry often has specific safety standards and best practices related to coil handling and packing. Organizations like ANSI (American National Standards Institute) and industry associations publish guidelines that often go beyond basic legal requirements.
- Agitation: Failure to adhere to these industry-specific standards, even if not explicitly mandated by law, can be seen as negligence in legal proceedings following accidents. Insurance companies may also use these standards to assess risk and determine liability in case of claims. Ignoring industry best practices increases your vulnerability to both accidents and their legal ramifications.
- Solution: Familiarize yourself with relevant industry-specific safety standards and incorporate them into your operational procedures. Participate in industry safety audits and certifications to demonstrate a commitment to best practices. Engage with industry safety experts to ensure your packing line operations are aligned with the highest safety standards.
3. Insurance Policy Implications
- Problem: Business insurance policies, including worker’s compensation and liability insurance, typically include clauses related to safety compliance and responsible operations. Overloading packing lines can be considered a breach of these clauses.
- Agitation: In the event of an accident or equipment failure caused by overloading, insurance claims could be denied or significantly reduced if it’s determined that the incident resulted from negligence or violation of safety protocols. Furthermore, a history of safety violations, including overloading incidents, can lead to increased insurance premiums or even difficulty obtaining coverage in the future.
- Solution: Review your insurance policies carefully to understand the clauses related to safety and equipment operation. Communicate your safety program and capacity management practices to your insurance provider to ensure alignment and demonstrate proactive risk mitigation. Maintain a strong safety record to negotiate favorable insurance terms and minimize the financial impact of potential incidents.
By prioritizing regulatory compliance and adhering to industry safety standards regarding packing line capacity, businesses not only avoid legal and financial penalties but also foster a culture of safety, demonstrating a commitment to responsible operations and employee well-being. Compliance is not just a cost of doing business; it’s an investment in long-term sustainability and risk mitigation.
Implementing Safe Practices and Technology to Prevent Overloading
Preventing overloading isn’t just about knowing the risks; it’s about actively implementing strategies and technologies to mitigate those risks in your daily operations. A proactive approach, combining robust procedures with smart technology, is essential for maintaining a safe and efficient steel coil packing line.
Preventing overloading requires a multi-faceted approach encompassing operator training, strict adherence to load limits, regular equipment inspections, and the integration of technology such as load monitoring systems. These measures work in concert to create a safer operating environment and minimize the risks associated with exceeding packing line capacity.
A Proactive Strategy: Combining People, Processes, and Technology
Effective overload prevention is built on a three-pillar approach: well-trained personnel, clearly defined procedures, and the strategic deployment of technology. These elements work together to create a robust safety net.
1. Comprehensive Operator Training
- Focus: Training is the foundation of any safety program. Operators must be thoroughly trained on the risks of overloading, proper operating procedures, and emergency protocols.
- Key Elements:
- Capacity Limits Education: Operators must understand the specific load limits for each section of the packing line and the consequences of exceeding them.
- Load Estimation Techniques: Train operators to accurately estimate coil weights and dimensions before loading them onto the line. Provide tools and resources for weight calculation and coil identification.
- Safe Operating Procedures: Detailed training on step-by-step procedures for loading, operating, and unloading the packing line within safe capacity limits. Emphasize smooth, controlled movements and avoidance of sudden starts and stops.
- Emergency Stop Procedures: Thorough instruction on the location and proper use of emergency stop buttons and procedures for safely halting the line in overload situations.
- Regular Refresher Training: Safety knowledge degrades over time. Implement mandatory refresher training sessions at regular intervals to reinforce safe practices and update operators on any procedural changes or new safety information.
- Impact: Well-trained operators are the first line of defense against overloading. They are equipped to recognize potential overload situations, operate the line safely, and respond effectively in emergencies.
2. Strict Load Limit Adherence Protocols
- Focus: Establish clear, written protocols for load limit adherence and enforce them rigorously. Protocols must move beyond simply stating limits to outlining practical steps for compliance.
- Key Elements:
- Clearly Posted Limits: Display maximum load capacities prominently at each relevant station along the packing line. Use visual aids like signage and color-coding for easy comprehension.
- Pre-Loading Checks: Implement mandatory pre-loading checks to verify coil weights and dimensions against packing line capacity limits before coils are placed on the line. Use checklists and weight verification systems.
- Load Distribution Guidelines: Provide guidelines for proper load distribution on conveyors and handling mechanisms to prevent concentrated stress points and ensure even weight distribution within capacity limits.
- Supervisory Oversight: Ensure supervisors are trained to monitor load adherence and enforce protocols. Empower supervisors to stop operations if overload risks are detected and provide them with clear escalation procedures.
- Regular Audits: Conduct periodic audits of loading practices to verify compliance with load limit protocols. Use audit findings to identify areas for improvement and refine procedures as needed.
- Impact: Strict protocols create a culture of compliance and ensure that load limits are not just guidelines but enforced operational rules.
3. Technology Integration for Monitoring and Prevention
- Focus: Leverage technology to enhance overload monitoring and prevention capabilities. Technology provides real-time data and automated safeguards that human operators alone cannot achieve.
- Key Technologies:
Technology | Functionality | Benefit |
---|---|---|
Load Cells & Weighing Systems | Real-time weight measurement at critical points on the line (e.g., conveyor infeed) | Immediate overload detection, prevents loading coils exceeding capacity limits |
Programmable Logic Controllers (PLCs) | Automated line control, integration with sensors, overload alarm triggers | Automated line shutdown in overload situations, data logging of load parameters for analysis |
Visual Monitoring Systems (Cameras) | Real-time visual monitoring of coil loading and packing processes | Remote oversight of loading procedures, visual verification of load distribution, incident recording |
Alarm Systems (Audible & Visual) | Immediate alerts to operators and supervisors upon overload detection | Rapid operator response to overload situations, prevents continued operation under unsafe conditions |
- Impact: Technology acts as a force multiplier for safety, providing continuous monitoring, automated safeguards, and data-driven insights for proactive overload prevention.
By strategically combining comprehensive operator training, strict load limit adherence protocols, and the intelligent integration of technology, businesses can create a robust and effective overload prevention system for their steel coil packing lines. This proactive approach minimizes risks, enhances safety, and ensures the long-term reliability and efficiency of their operations.
Economic Advantages of Capacity Adherence
While the focus on overloading risks is often centered on safety and compliance, adhering to steel coil packing line capacity limits also yields significant economic advantages. Operating within design parameters isn’t just safer; it’s smarter business.
Adhering to steel coil packing line capacity limits translates to long-term economic benefits, including reduced maintenance costs, extended equipment lifespan, minimized downtime, improved operational efficiency, and lower overall cost of ownership. While overloading might offer short-term output gains, capacity adherence ensures sustainable profitability and reduces hidden long-term expenses.
By operating within the designed capacity of your steel coil packing line, you directly contribute to reduced maintenance expenses, extend the operational life of your equipment, minimize costly downtime, and enhance overall operational efficiency. These factors combine to significantly lower your total cost of ownership, making capacity adherence a financially sound strategy for sustained profitability. Choosing to operate within capacity is not just a safety measure; it is a smart economic decision that safeguards your investment and ensures long-term financial health.
Dive Deeper into the Economic Payoffs of Capacity Management
The economic benefits of capacity adherence are often less obvious than the immediate safety advantages, but they are just as crucial to long-term business success. Let’s break down the key economic advantages:
- Reduced Maintenance Costs: Operating within capacity significantly reduces wear and tear on packing line components. This translates directly to fewer breakdowns, less frequent component replacements, and lower overall maintenance expenditure. Preventative maintenance becomes more effective, and reactive maintenance costs are minimized.
- Extended Equipment Lifespan: By avoiding overload stress, you extend the useful life of your packing line. This delays costly equipment replacements, reduces capital expenditure over time, and maximizes the return on your initial investment. A longer equipment lifespan also improves depreciation schedules and asset value.
- Minimized Downtime: Overloading is a major contributor to equipment breakdowns and downtime. Adhering to capacity limits reduces the frequency of failures, minimizes production interruptions, and ensures consistent output. Reduced downtime translates to higher throughput, improved delivery schedules, and increased customer satisfaction.
- Improved Operational Efficiency: Packing lines operating within capacity run more smoothly and efficiently. Energy consumption is optimized, packing quality is consistent, and the line operates at its designed throughput rate. This improved efficiency reduces operational costs per coil packed and enhances overall productivity.
- Lower Total Cost of Ownership (TCO): All the above factors – reduced maintenance, extended lifespan, minimized downtime, and improved efficiency – contribute to a significantly lower total cost of ownership over the packing line’s lifecycle. While overloading might seem to offer short-term gains, capacity adherence delivers superior long-term economic value.
Conclusion
The safety risks of overloading steel coil packing line capacity are undeniable and far-reaching, impacting worker safety, equipment integrity, regulatory compliance, and long-term financial stability. Prioritizing safe load handling and adhering to capacity limits is not merely a matter of regulatory compliance; it’s a fundamental aspect of responsible and efficient steel processing operations. By understanding the multifaceted risks of overloading risks and implementing proactive prevention strategies, businesses can create a safer, more productive, and economically sustainable future for their steel coil packing operations.