1. What Are the Innovative Trends in Steel Wire Packing?
Steel wire packing is undergoing a transformative phase, driven by demands for efficiency, safety, and sustainability. Modern innovations are rapidly changing how steel wire coils are handled, protected, and prepared for transport and storage in various industries.

The steel wire packing industry is seeing innovative trends like automation for increased efficiency, sustainable material usage to reduce environmental impact, enhanced safety features to protect workers and products, and smart technologies for optimized operations and tracking. These advancements are crucial for businesses aiming to improve productivity and meet modern industry standards.
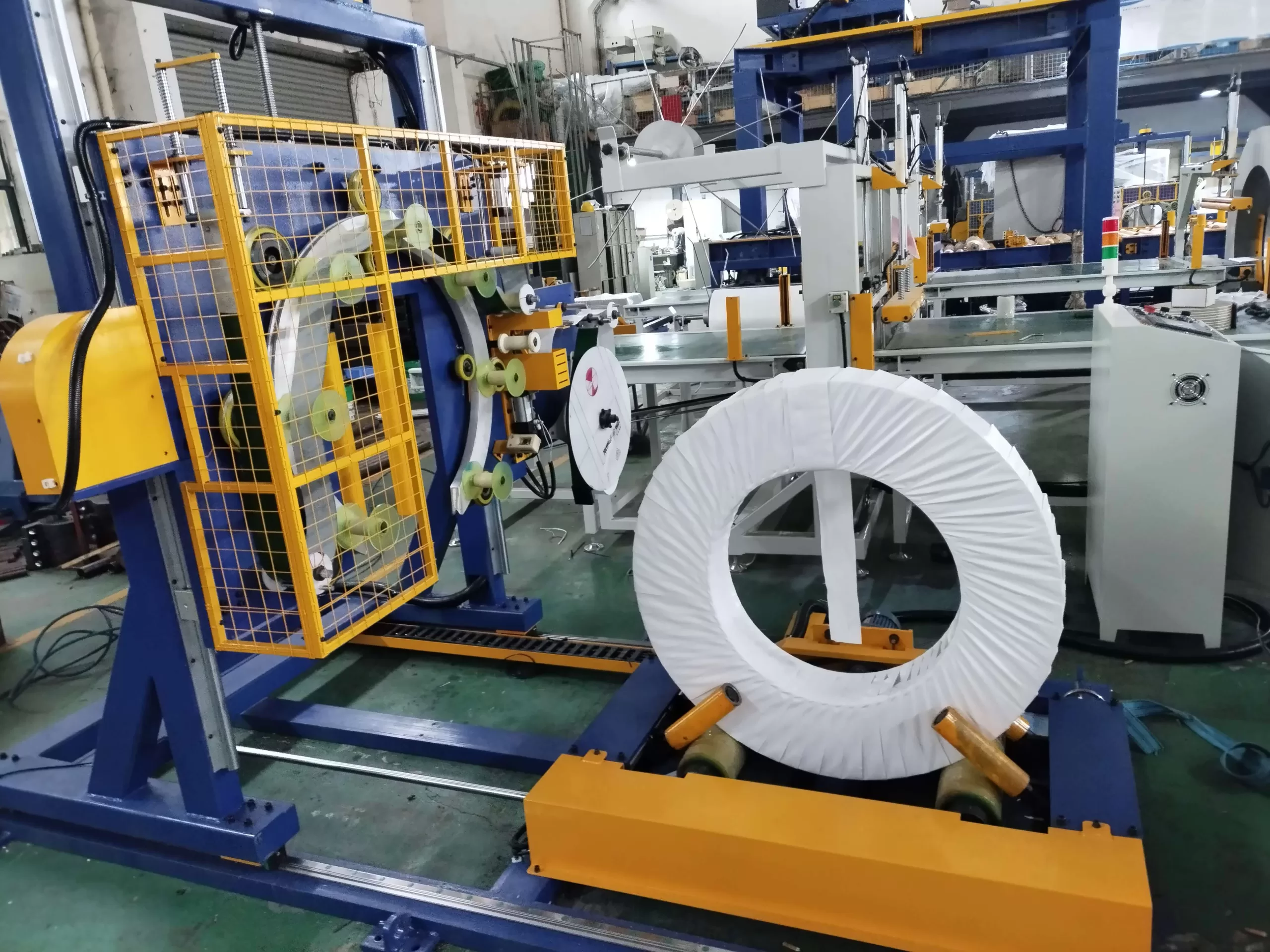
Keep reading to explore the specific trends and technological advancements that are reshaping steel wire packing, ensuring your operations are at the cutting edge of industry best practices.
2. Automation and Efficiency in Steel Wire Packing
Automation is revolutionizing numerous industries, and steel wire packing is no exception. Integrating automated systems is crucial for boosting productivity and reducing manual labor in demanding packing environments.
Automated wire packing systems are leading the charge in efficiency. These systems utilize robots and programmed sequences to streamline the entire packing process, from material handling to wrapping and securing coils. This minimizes human intervention, reduces errors, and significantly speeds up production cycles, making operations more consistent and cost-effective.
To truly understand the impact of automation, let’s delve deeper into how different facets of automation enhance steel wire packing operations.
The Multifaceted Benefits of Automated Steel Wire Packing
Automating steel wire packing extends beyond simply replacing manual labor. It encompasses a range of sophisticated technologies that contribute to a more efficient, safer, and higher-quality output. Let’s break down the key benefits:
Enhanced Productivity and Throughput
Automated systems operate continuously and consistently, drastically increasing throughput compared to manual methods. Machines work at a steady pace, without breaks or fatigue, leading to higher production volumes in less time.
Reduced Labor Costs and Dependency
By automating repetitive tasks, businesses can significantly reduce their reliance on manual labor. This not only lowers labor costs but also mitigates the challenges associated with workforce shortages and variability in human performance.
Improved Consistency and Quality
Automated systems perform tasks with precision and repeatability, ensuring consistent packing quality for every coil. This reduces the chances of errors, damage during handling, and variations in packing standards, leading to higher customer satisfaction.
Enhanced Safety in Operations
Automating heavy lifting and repetitive motions reduces the risk of workplace injuries associated with manual steel wire packing. Machines handle the physically demanding aspects, creating a safer environment for human workers who can then focus on supervision and maintenance.
To illustrate the impact, consider a comparison between manual and automated steel wire packing across key operational metrics:
Feature | Manual Steel Wire Packing | Automated Steel Wire Packing | Improvement with Automation |
---|---|---|---|
Packing Speed | Slow, variable | Fast, consistent | 3x – 5x faster |
Labor Cost | High | Low | 50% – 70% reduction |
Packing Consistency | Variable, error-prone | Highly consistent, precise | Up to 99% accuracy |
Worker Safety | Higher risk of injury | Lower risk of injury | 60% – 80% reduction in injuries |
Material Waste | Higher due to errors | Lower due to precision | 15% – 25% reduction |
These figures highlight the substantial advantages of adopting automation in steel wire packing. The investment in automated systems translates to long-term gains in productivity, cost savings, and operational excellence.
3. Sustainable Materials and Practices in Steel Wire Packing
Sustainability is no longer a niche concept but a core business imperative. The steel wire packing industry is actively embracing eco-friendly materials and practices to minimize environmental impact and meet growing green demands.
Sustainable trends in steel wire packing focus on using recyclable and biodegradable wrapping materials, optimizing material usage to reduce waste, and implementing energy-efficient packing processes. This includes transitioning from traditional plastics to paper-based wraps, utilizing thinner yet durable films, and adopting packing machinery with lower energy consumption.
Let’s explore the specific sustainable materials and practices that are making a difference in the steel wire packing sector.
Driving Sustainability Through Material Innovation and Process Optimization
Sustainability in steel wire packing is achieved through a dual approach: innovative material selection and optimized operational processes.
Eco-friendly Wrapping Materials
The shift towards sustainability is significantly driven by the adoption of environmentally friendly wrapping materials. This includes:
- Recycled Plastics: Utilizing films made from recycled polyethylene (rPE) and other recycled plastics reduces reliance on virgin materials and lowers the carbon footprint.
- Biodegradable Films: Biodegradable or compostable films made from plant-based polymers offer an end-of-life solution that minimizes plastic waste in landfills.
- Paper-based Wraps: Paper and cardboard wraps, especially those from recycled sources, are gaining popularity as a readily recyclable and biodegradable alternative to plastic films for certain applications.
Material Optimization and Waste Reduction
Sustainable practices also involve optimizing material usage to minimize waste:
- Thin Film Technology: Advancements in film technology allow for the production of thinner, high-strength films that use less material without compromising on protection.
- Precision Wrapping: Automated wrapping machines with precise control systems ensure optimal film tension and overlap, reducing excess material usage.
- Recycling Programs: Implementing in-house recycling programs for wrapping materials and encouraging customers to participate in return or recycling schemes further closes the loop on material usage.
Energy-Efficient Packing Processes
Sustainability extends to the energy consumption of packing machinery and operations:
- Energy-Efficient Motors: Modern wrapping machines are equipped with energy-efficient electric motors that consume less power, reducing operational costs and environmental impact.
- Optimized Machine Design: Machine designs focused on minimizing energy use during operation, such as reduced cycle times and efficient heating systems for heat-shrink wrapping, contribute to sustainability.
- Renewable Energy Integration: Factories are increasingly integrating renewable energy sources like solar or wind power to power their packing operations, further reducing their carbon footprint.
By embracing these sustainable materials and practices, the steel wire packing industry is moving towards a more environmentally responsible future.
4. Enhanced Safety Features in Steel Wire Packing Machinery
Safety is paramount in industrial environments, and steel wire packing machinery is evolving to incorporate advanced safety features, protecting both operators and the integrity of the packed products.
Modern steel wire packing machines are equipped with a range of safety mechanisms designed to prevent accidents and ensure a secure working environment. These features are critical for minimizing risks associated with heavy machinery and materials handling.
Modern steel wire packing machines integrate advanced safety features such as emergency stop mechanisms, light curtains, safety scanners, and overload protection systems. These technologies ensure operator safety by preventing accidental contact with moving parts and protecting machinery from damage due to incorrect loading or operation. Enhanced safety contributes to a more secure and productive work environment.
Let’s delve into the specific safety features that are becoming standard in advanced steel wire packing machinery.
Key Safety Technologies in Modern Steel Wire Packing Equipment
Safety in steel wire packing machinery is achieved through a combination of proactive and reactive safety systems designed to mitigate potential hazards.
Proactive Safety Measures
These features are designed to prevent accidents before they occur:
- Light Curtains and Safety Scanners: These optical sensors create safety zones around the machine. If an operator inadvertently enters a hazardous area, the machine automatically stops, preventing potential injuries.
- Two-Hand Operation Controls: For certain operations, requiring operators to use both hands to activate machinery ensures that their hands are safely away from moving parts during critical phases.
- Safety Interlocks: Guards and access panels are equipped with interlocks that automatically shut down the machine if they are opened during operation, preventing access to hazardous areas while the machine is running.
Reactive Safety Systems
These systems are designed to respond quickly and effectively in emergency situations:
- Emergency Stop Buttons (E-Stops): Strategically placed E-stop buttons allow for immediate machine shutdown in case of any emergency or unsafe condition.
- Overload Protection: Sensors monitor the load on motors and drive systems. If an overload is detected, the machine automatically shuts down to prevent damage to the machinery and potential hazards.
- Audible and Visual Alarms: Machines are equipped with alarms that provide warnings during startup, malfunction, or emergency stops, alerting operators to potential hazards.
Safety Enhancements through Design and Ergonomics
Beyond specific safety devices, machine design and ergonomics play a crucial role:
- Ergonomic Design: Control panels and access points are designed for ease of use and accessibility, reducing operator strain and fatigue, which can contribute to accidents.
- Clear Visual Indicators: Machines are designed with clear visual indicators, such as warning lights and safety signage, to communicate machine status and potential hazards effectively.
- Robust Machine Construction: Solid and stable machine construction minimizes vibrations and ensures stability during operation, reducing the risk of machine malfunction and accidents.
By incorporating these advanced safety features, steel wire packing machinery is becoming significantly safer, protecting operators and contributing to a more secure and productive working environment.
5. Smart and Connected Steel Wire Packing Solutions
The integration of smart technologies and connectivity is transforming steel wire packing, enabling optimized operations, real-time monitoring, and data-driven decision-making.
Smart steel wire packing solutions leverage IoT, cloud computing, and data analytics to enhance efficiency, traceability, and predictive maintenance. These systems provide real-time insights into machine performance, material consumption, and packing status, enabling proactive adjustments and optimized workflows. Connectivity allows for remote monitoring and control, enhancing operational flexibility and responsiveness.
Modern steel wire packing is moving towards intelligent, connected systems. Let’s explore the key aspects of this technological evolution.
The Rise of Intelligent and Connected Packing Systems
Smart technologies are not just about automation; they are about creating intelligent, self-optimizing systems that enhance every aspect of steel wire packing operations.
Internet of Things (IoT) Integration
Integrating IoT sensors and connectivity into wrapping machines enables real-time data collection and monitoring of various parameters, including:
- Machine Performance Metrics: Data on cycle times, throughput, uptime, and downtime is continuously collected, providing insights into machine efficiency and productivity.
- Material Consumption Tracking: Sensors track film usage, allowing for precise monitoring of material consumption and identification of potential waste.
- Environmental Conditions: Sensors monitor temperature, humidity, and vibration levels, providing data for optimizing packing conditions and identifying potential environmental impacts on materials or machinery.
Cloud Computing and Data Analytics
Collected data is transmitted to cloud platforms for storage, processing, and analysis:
- Real-time Dashboards: Cloud-based dashboards provide operators and managers with real-time visibility into machine performance, production status, and key operational metrics.
- Predictive Maintenance: Data analytics algorithms analyze machine data to predict potential failures and schedule maintenance proactively, minimizing downtime and extending machine lifespan.
- Performance Optimization: Data analysis identifies areas for process improvement and optimization, leading to increased efficiency, reduced waste, and enhanced overall productivity.
Remote Monitoring and Control
Connectivity enables remote access and control of packing systems:
- Remote Diagnostics and Troubleshooting: Technicians can remotely access machine data and diagnostics to troubleshoot issues, reducing the need for on-site visits and minimizing downtime.
- Remote Parameter Adjustments: Authorized personnel can remotely adjust machine parameters, optimizing performance and responding to changing production needs.
- System Integration: Smart packing systems can be integrated with other enterprise systems, such as ERP and MES, for seamless data flow and streamlined operations management.
By embracing smart and connected technologies, the steel wire packing industry is moving towards a future of optimized, data-driven, and highly efficient operations.
Conclusion
The steel wire packing industry is experiencing a wave of innovation, driven by automation, sustainability, safety, and smart technologies. These trends are not just about improving efficiency; they represent a fundamental shift towards more responsible, safer, and intelligent manufacturing practices. By embracing these innovative trends and technological advancements, businesses can ensure they remain competitive, efficient, and aligned with the evolving demands of the modern industrial landscape. The future of steel wire packing is smarter, greener, and safer than ever before.