What Are the Environmental Impact Reduction Strategies for PVC Pipe Bagging Machines?
The PVC pipe industry relies on bagging machines for efficient packaging, but these machines can pose environmental challenges. Understanding and mitigating these impacts is crucial for sustainable operations. This article explores effective strategies to minimize the environmental footprint of PVC pipe bagging machines, focusing on practical and innovative solutions.
Strategies to reduce the environmental impact of PVC pipe bagging machines include transitioning to sustainable packaging materials like biodegradable films, optimizing packaging design for minimal material use, implementing efficient recycling programs, and adopting energy-saving technologies in machinery operations. These efforts collectively contribute to a greener and more responsible PVC pipe manufacturing process.
This article will delve into each of these strategies, providing a comprehensive guide for PVC pipe manufacturers seeking to enhance their environmental performance. By exploring material innovations, process optimizations, and circular economy principles, we can pave the way for a more sustainable future in PVC pipe packaging.
1. Understanding the Environmental Footprint of PVC Pipe Bagging
PVC pipe bagging machines, while essential for streamlining packaging processes, contribute to environmental concerns through material consumption and energy use. A thorough understanding of these impacts is the first step towards implementing effective reduction strategies and fostering a more sustainable approach.
The environmental footprint of PVC pipe bagging machines primarily stems from plastic waste generation, greenhouse gas emissions from production and operation, and potential pollution of water resources due to plastic leakage. Addressing these key areas through targeted strategies is crucial for minimizing the overall environmental impact.

Deconstructing the Environmental Impact: A Closer Look
To effectively tackle the environmental challenges, we need to break down the impact into specific categories and analyze their contributions. This allows for targeted interventions and optimized solutions.
1.1 Plastic Waste Generation: A Major Concern
The most visible environmental impact is the generation of plastic waste. Traditional PVC bagging often employs single-use plastic films that end up in landfills or, worse, the environment. The sheer volume of plastic used in packaging, coupled with its slow degradation rate, makes this a significant issue.
1.2 Greenhouse Gas Emissions: From Production to Disposal
The life cycle of PVC bagging materials and machine operation involves greenhouse gas emissions at various stages:
- Material Production: Manufacturing PVC films requires energy, often from fossil fuels, releasing CO2.
- Machine Operation: Bagging machines consume electricity, contributing to emissions depending on the energy source.
- Waste Disposal: Incinerating plastic waste releases greenhouse gases, while landfills can generate methane, a potent greenhouse gas.
1.3 Water Resource Pollution: The Leakage Problem
Plastic waste improperly managed can find its way into water bodies. This leads to:
- Microplastic Pollution: Degradation of larger plastics into microplastics contaminates water sources and harms aquatic life.
- Physical Pollution: Plastic films can entangle wildlife and disrupt aquatic ecosystems.
To quantify these impacts, consider the following comparative data for different packaging materials used in pipe bagging:
Environmental Impact Category | Traditional PVC Film | Recycled Polyolefin Film | Biodegradable Film (PLA) | Paper-based Wrap |
---|---|---|---|---|
Global Warming Potential (kg CO2e) | Highest | Medium | Low | Medium |
Fossil Fuel Depletion (MJ) | Highest | Medium | Low | Medium |
Water Consumption (L) | Medium | Medium | Low | Highest |
Waste Generation (kg) | Highest | Medium | Low | Medium |
Biodegradability | No | No | Yes | Yes |
Note: Data is indicative and varies based on specific production processes and materials. Consult Life Cycle Assessments for precise figures.
This table highlights that while PVC film has significant drawbacks, alternatives like recycled polyolefin, biodegradable films, and paper-based wraps offer varying degrees of environmental improvement, each with its own set of trade-offs to consider.
2. Sustainable Packaging Material Alternatives
Transitioning to sustainable packaging materials is a cornerstone strategy for reducing the environmental impact of PVC pipe bagging machines. This involves exploring and adopting materials that minimize waste, reduce reliance on fossil fuels, and promote circularity.
Moving away from traditional PVC films towards alternatives like recycled polyolefins, biodegradable plastics, and paper-based solutions offers significant environmental advantages. These materials address key concerns such as plastic waste accumulation and reliance on virgin fossil resources, paving the way for more eco-conscious packaging.
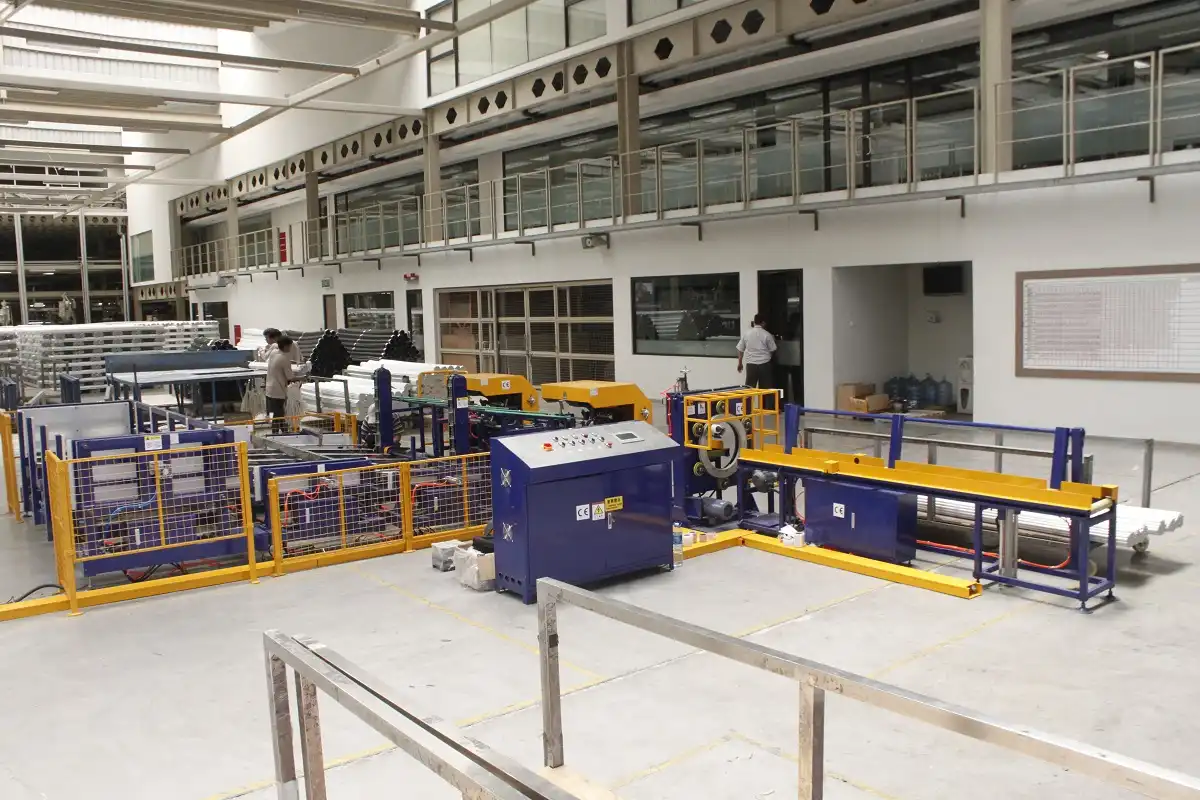
Exploring Viable Alternatives: Material Innovations in Bagging
The packaging industry is witnessing rapid innovation in sustainable materials. For PVC pipe bagging, several promising alternatives are emerging:
2.1 Recycled Polyolefin Films: Closing the Loop
Recycled polyolefin films, made from materials like polyethylene (PE) and polypropylene (PP), offer a significant step towards sustainability. These films:
- Reduce Virgin Plastic Use: Utilize post-consumer or post-industrial recycled plastics, decreasing the demand for new plastic production.
- Lower Carbon Footprint: Recycling processes generally consume less energy than producing virgin plastics.
- Maintain Performance: Recycled polyolefins can offer comparable strength and protection to virgin PVC for many applications.
2.2 Biodegradable and Compostable Films: Nature-Friendly Disposal
Biodegradable and compostable films, often made from plant-based materials like polylactic acid (PLA) or cellulose, are designed to decompose in specific environments. Key benefits include:
- Reduced Landfill Burden: Biodegradable films break down over time, minimizing long-term waste accumulation.
- Compostability (for some): Certain films are certified compostable, allowing for disposal in industrial composting facilities.
- Renewable Resources: Often derived from renewable resources, reducing reliance on fossil fuels.
2.3 Paper-Based Wraps and Alternatives: Back to Basics
Paper-based wraps and cardboard alternatives offer a more traditional yet increasingly relevant sustainable option. Advantages include:
- Renewable Resource: Paper is derived from wood, a renewable resource (when sustainably managed).
- Recyclability: Paper is widely recyclable in most regions.
- Biodegradability: Paper decomposes relatively quickly in landfills or compost.
However, paper production can be water and energy-intensive, so responsible sourcing and efficient production are crucial.
The choice of sustainable material depends on factors like cost, performance requirements, disposal infrastructure, and specific environmental goals. A comparative overview is provided below:
Material Type | Sustainability Advantages | Potential Limitations | Best Suited For |
---|---|---|---|
Recycled Polyolefin Films | Reduces virgin plastic use, lower carbon footprint | May have slightly lower strength than virgin PVC | General pipe bagging where high strength PVC is not vital |
Biodegradable Films | Reduces landfill waste, compostable options, renewable resources | Can be more expensive, require specific disposal conditions | Short-term packaging, applications prioritizing end-of-life |
Paper-Based Wraps | Renewable resource, recyclable, biodegradable | Can be less water-resistant, production can be resource-intensive | Bundling and wrapping of pipes, protective layering |
3. Optimizing Bagging Processes for Efficiency
Beyond material changes, optimizing the bagging process itself offers significant opportunities to reduce environmental impact. This involves minimizing material usage, conserving energy, and improving overall efficiency.
Optimizing bagging processes is crucial for minimizing material waste and energy consumption. Strategies like down-gauging film thickness, right-sizing packaging, and implementing energy-efficient machinery contribute to a leaner and more environmentally sound operation.
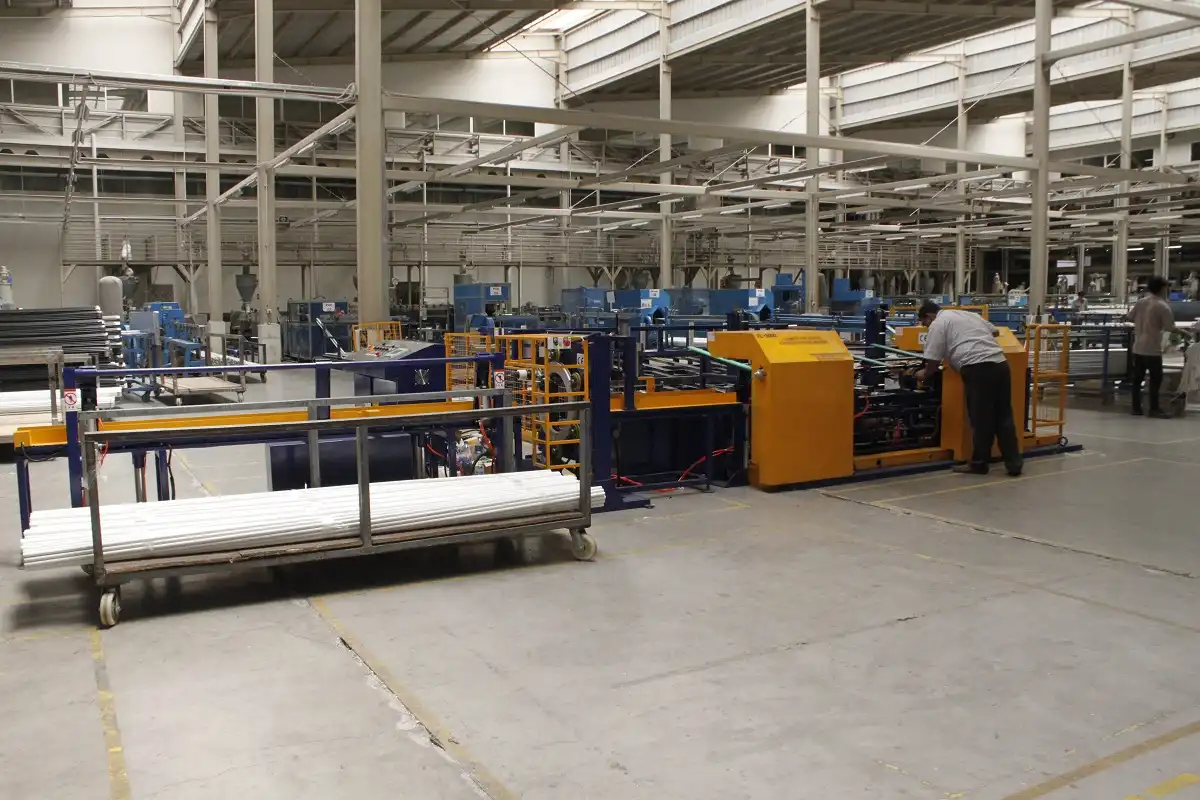
Efficiency in Action: Process and Technology Improvements
Several process and technology improvements can significantly enhance the environmental performance of PVC pipe bagging operations:
3.1 Down-Gauging Film Thickness: Less Material, Same Protection
Down-gauging involves reducing the thickness of plastic films while maintaining necessary strength and protection. This seemingly small change can lead to substantial material savings over time. Modern film technology allows for thinner yet stronger films, achieving material reductions of up to 20-30% in some applications.
3.2 Right-Sizing Packaging: Tailoring to Product Needs
Avoiding oversized packaging is crucial. Right-sizing packaging ensures that only the necessary amount of material is used to securely bag the pipes. This can be achieved through:
- Variable Bag Size Machines: Machines that adjust bag size based on pipe dimensions.
- Optimized Bundle Configurations: Arranging pipes in tighter bundles to minimize bag volume.
3.3 Energy-Efficient Machinery: Reducing Operational Footprint
Investing in energy-efficient bagging machines can significantly reduce electricity consumption. This includes:
- Servo-driven Systems: More precise and energy-saving compared to pneumatic systems.
- Standby Modes and Smart Controls: Minimizing energy use during idle periods.
- Regular Maintenance: Ensuring machines operate at peak efficiency and avoid energy waste due to malfunctions.
3.4 Waste Reduction Technologies: Pellet and Vacuum Packing
Advanced technologies can further minimize packaging material usage:
- Pellet Packing: Using loose pellets instead of films for certain applications, reducing material waste.
- Vacuum Packing: Removing air from packages to reduce volume and material needed for secure bundling.
Consider the impact of down-gauging on material consumption:
Film Gauge (Thickness) | Material Usage per 1000 Bags | Material Reduction vs. 60 Gauge | Cost Reduction vs. 60 Gauge |
---|---|---|---|
60 Gauge | 100 kg | – | – |
50 Gauge | 85 kg | 15% | 10% |
45 Gauge | 75 kg | 25% | 18% |
Note: Data is illustrative and depends on film type and bag dimensions. Real-world savings can vary.
This data demonstrates that even a seemingly small reduction in film gauge can lead to significant savings in material usage and cost, directly translating to a lower environmental footprint.
4. Embracing Circularity and Recycling
Implementing robust recycling programs and embracing circular economy principles are essential for long-term sustainability in PVC pipe bagging. This involves collecting, processing, and reusing packaging materials, minimizing waste and resource depletion.
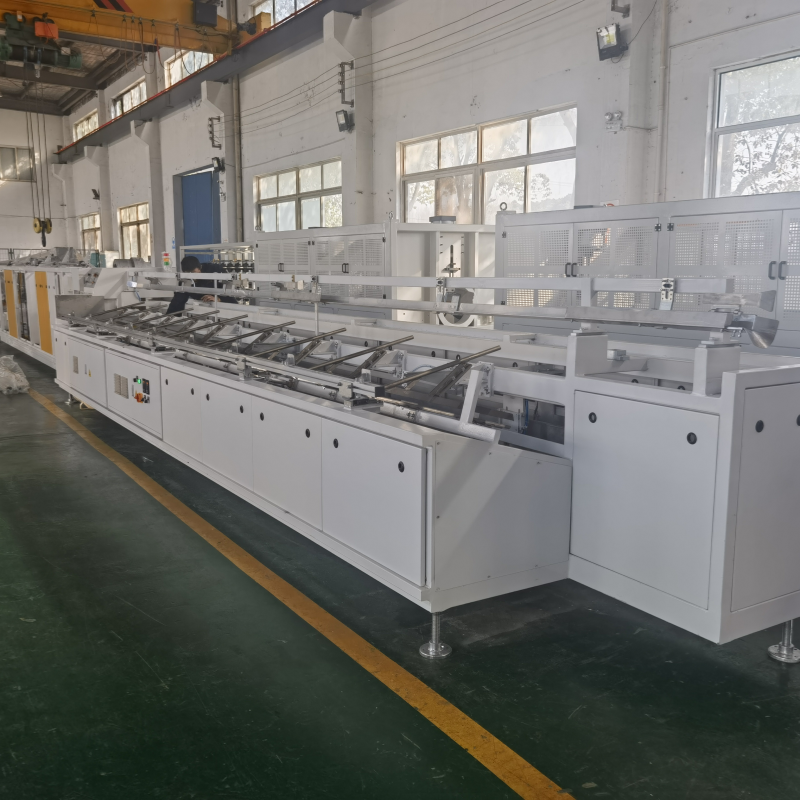
While PVC itself has recyclability challenges, focusing on recycling alternative bagging materials and exploring innovative PVC recycling technologies is crucial. Establishing closed-loop systems for polyolefin films, maximizing paper recycling, and supporting research into PVC recycling technologies are key strategies for promoting circularity in PVC pipe packaging.
For polyolefin films, well-established recycling infrastructure exists in many regions. Collecting used bagging films and channeling them back into the recycling stream ensures material reuse and reduces reliance on virgin plastics. Paper-based wraps are also widely recyclable, contributing to a circular flow.
PVC recycling, while more complex, is gaining traction. Mechanical and chemical recycling methods are being developed to process PVC waste and create new products. Supporting these advancements and exploring opportunities to incorporate recycled PVC content in bagging films (where feasible and without compromising performance) are important steps towards circularity.
Recycling Infrastructure and Initiatives:
- Establish Collection Programs: Partner with recycling facilities and implement collection systems for used bagging films.
- Material Sorting and Processing: Ensure proper sorting and processing of collected materials for efficient recycling.
- Closed-Loop Systems: Explore opportunities to create closed-loop systems where recycled materials are directly reused in pipe packaging.
- Industry Collaboration: Collaborate with industry partners and organizations to promote recycling initiatives and share best practices.
Conclusion
Reducing the environmental impact of PVC pipe bagging machines is a multifaceted challenge that requires a holistic approach. By strategically implementing sustainable material alternatives, optimizing bagging processes for efficiency, and embracing circular economy principles through robust recycling programs, the PVC pipe industry can significantly minimize its environmental footprint. These combined efforts are not only environmentally responsible but also contribute to long-term cost savings and enhanced brand reputation in an increasingly eco-conscious market. Embracing these strategies is a vital step towards a more sustainable and responsible future for PVC pipe manufacturing and PVC pipe bagging machines.