What Are the Best Practices for PVC Pipe Bagging Machine Operator Training?
In today’s manufacturing landscape, packaging machinery, including PVC pipe bagging machines, plays a crucial role. Efficient and safe operation hinges on well-trained operators. This article delves into the best practices for training operators, ensuring peak performance and minimizing risks in your PVC pipe production line.
The best practices for PVC pipe bagging machine operator training emphasize comprehensive programs covering machine mechanics, safety protocols, and troubleshooting. Hands-on training, mentorship, and continuous education are crucial. Operators must master routine maintenance, emergency procedures, and quality control to ensure efficient and safe operations, minimizing downtime and maximizing productivity.
Investing in robust operator training is not merely an operational advantage—it’s a cornerstone of a successful and safe PVC pipe manufacturing process. Let’s explore the essential elements of effective training programs that empower your operators and optimize your bagging machine operations.
1. Developing a Comprehensive Training Program
A well-structured training program is the bedrock of operator competency. For PVC pipe bagging machines, the training should extend beyond basic operation to encompass a holistic understanding of the machinery and its role in the production line.
A comprehensive PVC pipe bagging machine operator training program should include theoretical knowledge of machine mechanics, in-depth safety training covering lockout/tagout and emergency stops, hands-on practical sessions, and detailed instruction on routine maintenance and troubleshooting. It must also incorporate quality control procedures to ensure consistent packaging standards and minimize product damage.
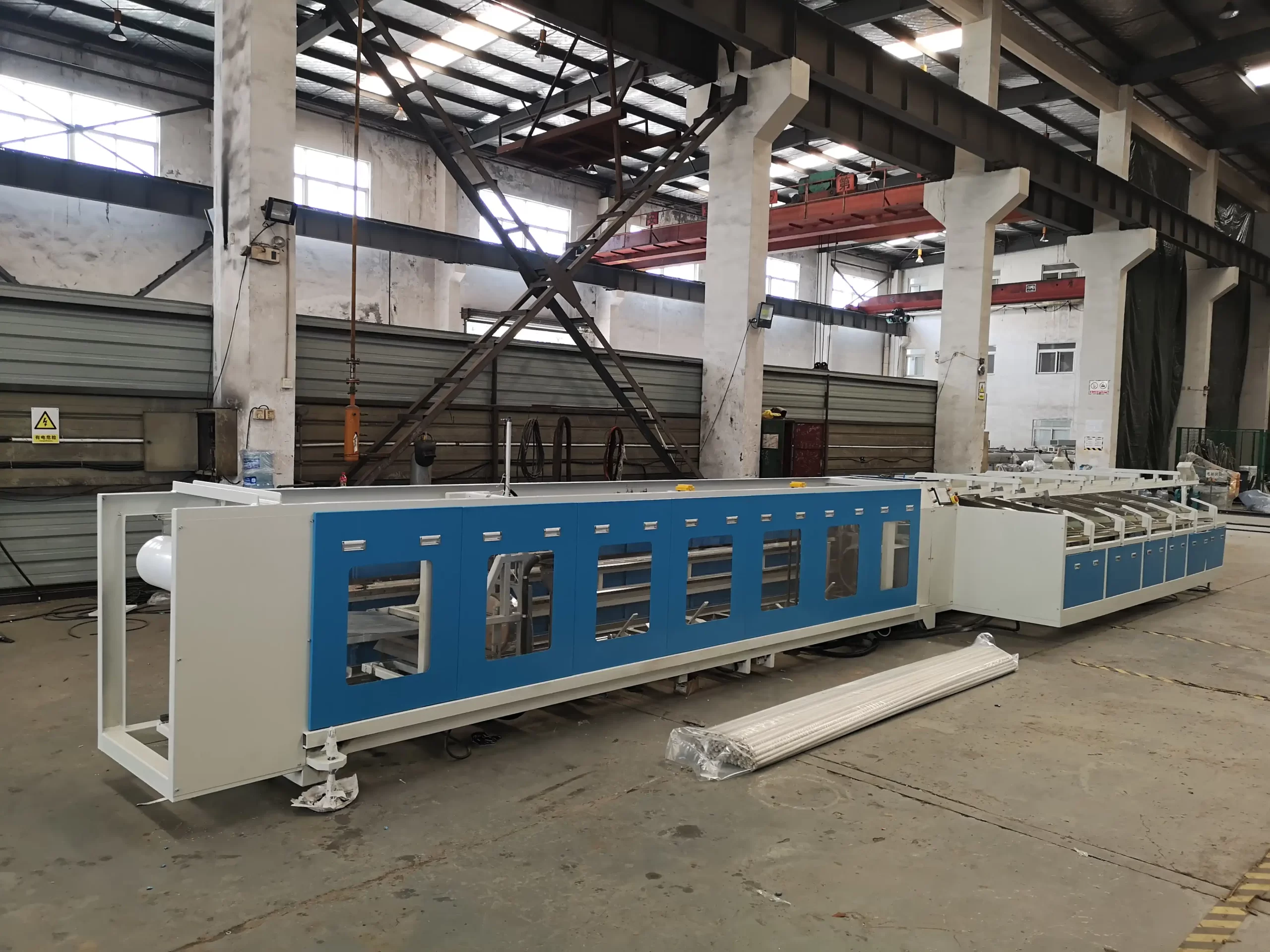
To build a truly effective program, consider these key components:
1.1 Foundational Knowledge: Understanding the Machine
Operator training must start with a solid foundation of knowledge about the PVC pipe bagging machine itself. This includes:
- Machine Components and Functions: Trainees need to understand each part of the machine, from the infeed system to the sealing and discharge mechanisms. Diagrams and visual aids are invaluable here.
- Operational Cycle: A step-by-step breakdown of the bagging cycle, from pipe feeding and wrapping to sealing and output, is essential. Operators should visualize the entire process.
- Control Systems: Training must cover the machine’s control panel, including buttons, indicators, and HMI (Human Machine Interface) if applicable. Understanding how to navigate and interpret the controls is critical.
- Material Specifications: Operators should be aware of the specifications of PVC pipes and bagging films used, and how these materials interact with the machine.
To ensure knowledge retention and practical application, incorporate different learning methods:
Training Method | Description | Benefits |
---|---|---|
Classroom Sessions | Lectures and presentations covering machine theory, safety, and procedures. | Provides a structured introduction and foundational knowledge. |
Manual Review | In-depth study of the machine’s operation and maintenance manuals. | Detailed understanding of machine specifics and manufacturer guidelines. |
Visual Aids | Diagrams, videos, and animations demonstrating machine operation. | Enhances understanding of complex mechanisms and processes. |
Hands-on Practice | Supervised operation of the machine, performing various tasks. | Develops practical skills and muscle memory in a safe, controlled environment. |
2. Emphasizing Safety Protocols and Emergency Procedures
Safety is paramount when operating industrial machinery. PVC pipe bagging machines, while automated, still present potential hazards if not handled correctly. Training must instill a strong safety culture and equip operators to prevent accidents.
Safety training for PVC pipe bagging machine operators must be rigorous and repetitive. It should cover lockout/tagout procedures in detail, emphasize the correct use of PPE, identify all potential hazard zones on the machine, and train operators on emergency stop procedures and evacuation plans. Regular safety drills are crucial to reinforce learning and ensure quick, effective responses in emergencies.
Key areas for safety training include:
- Lockout/Tagout (LOTO): Detailed instruction on LOTO procedures is non-negotiable. Operators must understand how to properly de-energize the machine for maintenance and prevent accidental start-ups.
- Personal Protective Equipment (PPE): Training should specify required PPE, such as safety glasses, gloves, and ear protection, and explain why each item is necessary.
- Hazard Identification: Operators need to be trained to recognize potential hazards, including pinch points, moving parts, and electrical risks. Machine guarding and safety interlocks should be thoroughly explained.
- Emergency Stop Procedures: Operators must know the location and function of all emergency stop buttons and how to use them effectively in various scenarios.
- Emergency Response: Training should include procedures for fire emergencies, machine malfunctions, and personnel injuries. First aid basics and evacuation routes should be covered.
To reinforce safety learning, implement these practices:
- Regular Safety Drills: Conduct drills that simulate emergency scenarios to test operator response and identify areas for improvement.
- Safety Audits: Regularly audit operator adherence to safety protocols and provide feedback and retraining as needed.
- Safety Refresher Courses: Annual or semi-annual refresher courses keep safety knowledge fresh and updated with any procedural changes or new equipment features.
3. Hands-on Training and Practical Skill Development
Theoretical knowledge is essential, but practical, hands-on training is where operators truly develop the skills needed to operate PVC pipe bagging machines efficiently and effectively. Simulation and real-machine practice are crucial components.
Hands-on training for PVC pipe bagging machine operators should involve supervised operation on actual machines, starting with basic functions and progressing to more complex tasks like changeovers and troubleshooting. Simulation exercises can be used to practice emergency procedures and fault diagnosis in a safe environment before real-world application. The focus should be on developing muscle memory and practical problem-solving skills.
Effective hands-on training should include:
- Machine Startup and Shutdown Procedures: Step-by-step practice on safely starting and shutting down the machine under normal and emergency conditions.
- Routine Operation: Supervised operation of the machine for extended periods, performing typical bagging tasks and monitoring performance.
- Changeover Procedures: Training on how to safely and efficiently change settings for different PVC pipe sizes or bagging film types. This is critical for minimizing downtime.
- Troubleshooting Common Issues: Hands-on practice in diagnosing and resolving common machine faults, such as film jams, sealing problems, or sensor errors.
- Preventive Maintenance Tasks: Operators should be trained to perform basic preventive maintenance tasks, like lubrication, cleaning, and visual inspections, under supervision.
To maximize the effectiveness of hands-on training:
- Use Simulation: Where possible, utilize machine simulators to allow operators to practice in a safe, no-risk environment, especially for emergency scenarios and complex procedures.
- Progressive Learning: Start with basic tasks and gradually increase complexity as operators gain confidence and skill.
- Experienced Mentors: Pair new operators with experienced personnel who can provide guidance, answer questions, and offer real-world insights.
4. Continuous Education and Skill Enhancement
The technology of plastic packaging machines is constantly evolving. To maintain peak efficiency and adapt to new machinery or processes, operators need continuous education and opportunities for skill enhancement.
Continuous education is vital for PVC pipe bagging machine operators to stay updated with new technologies, safety protocols, and machine upgrades. Regular refresher courses, manufacturer training on new equipment, and cross-training on different machine types are essential. Encouraging operators to share feedback and participate in improvement initiatives fosters a culture of continuous learning and operational excellence.
Ongoing training initiatives should encompass:
- Refresher Courses: Regularly scheduled refresher courses on safety, operating procedures, and maintenance best practices to reinforce initial training.
- Manufacturer Training: When new machines are introduced or significant upgrades are implemented, manufacturer-provided training is crucial for operators to learn specific features and procedures.
- Cross-Training: Training operators on different types of packaging machines or across various roles within the production line enhances flexibility and skill diversification.
- Advanced Troubleshooting: Offer advanced training in diagnostics and repair for experienced operators to develop in-house expertise and reduce reliance on external technicians.
To foster a culture of continuous improvement:
- Feedback Mechanisms: Establish channels for operators to provide feedback on training programs, safety protocols, and machine performance.
- Performance Monitoring: Track key performance indicators (KPIs) related to operator efficiency and safety, and use this data to identify training needs and areas for improvement.
- Incentive Programs: Recognize and reward operators who demonstrate excellence in safety, efficiency, and proactive problem-solving, encouraging continuous skill development.
Training Aspect | Initial Training Emphasis | Continuous Education Focus |
---|---|---|
Safety | Foundational safety rules, LOTO, PPE, emergency stops. | Refresher drills, updates on regulations, incident reviews. |
Operation | Basic startup, operation, shutdown, routine tasks. | Advanced techniques, optimization, new feature training. |
Maintenance | Basic preventive maintenance, cleaning, lubrication. | Advanced diagnostics, component replacement, predictive maintenance. |
Troubleshooting | Common fault identification, basic error resolution. | Complex diagnostics, advanced repair, root cause analysis. |
5. Measuring Training Effectiveness
Training isn’t complete until you can measure its impact. Assessing the effectiveness of your PVC pipe bagging machine operator training program is crucial to ensure it delivers the desired results in terms of safety, efficiency, and quality.
Effective training programs are measurable and demonstrably improve operator performance and machine output. Key metrics include:
- Reduced accident rates: A well-trained operator is less likely to be involved in accidents. Track incident reports before and after training implementation.
- Increased machine uptime: Efficient operators contribute to smoother operations and fewer breakdowns. Monitor machine uptime and downtime.
- Improved product quality: Proper operation leads to consistent and high-quality packaging. Track product defect rates and packaging consistency.
- Enhanced operator proficiency: Assess operator skills through performance evaluations and feedback from supervisors.
To comprehensively evaluate training effectiveness:
- Pre- and Post-Training Assessments: Use written tests and practical evaluations before and after training to measure knowledge and skill gains.
- Performance Reviews: Regularly review operator performance on the job, focusing on safety adherence, efficiency, and problem-solving abilities.
- Feedback Surveys: Collect feedback from operators on the training program itself. Identify what worked well and areas for improvement.
- KPI Monitoring: Track relevant KPIs such as machine efficiency, downtime, accident rates, and product defect rates over time to assess the overall impact of training.
Effective training programs for PVC pipe bagging machine operators are not just a cost, but a strategic investment. By prioritizing comprehensive training, hands-on practice, continuous education, and rigorous safety protocols, manufacturers can cultivate a skilled and 안전한 workforce that drives operational excellence and maximizes the return on their machinery investments.
Conclusion
Implementing best practices in PVC pipe bagging machine operator training is essential for optimizing production, ensuring safety, and maintaining product quality. A comprehensive program that includes theoretical knowledge, hands-on skills development, a strong safety focus, and continuous learning opportunities will empower operators to excel. By investing in robust training initiatives and consistently measuring their effectiveness, companies can create a highly competent workforce that drives efficiency, minimizes risks, and contributes to the overall success of their PVC pipe manufacturing operations.