What Are the Benefits of PVC Pipe Bagging Machines in Reducing Inventory Costs?
PVC pipe bagging machines are revolutionizing inventory management by automating the packaging process. These machines offer significant advantages, streamlining operations and directly impacting the bottom line through reduced inventory costs. Discover how investing in automation can optimize your PVC pipe production.
PVC pipe bagging machines significantly reduce inventory costs by automating packaging, minimizing manual labor, and optimizing storage space. Automated bagging ensures consistent packaging, reduces material waste, and speeds up the throughput, leading to lower operational costs and improved inventory management efficiency.
This article delves into the quantifiable benefits of PVC pipe bagging machines, exploring how they contribute to substantial inventory cost reductions in PVC pipe manufacturing. Keep reading to discover specific advantages and understand how these machines can optimize your operations.
1. Streamlining Operations and Reducing Labor Costs with Automated Bagging
Automated bagging systems for PVC pipes are transforming manufacturing floors by drastically minimizing the need for manual intervention. These machines take over repetitive and labor-intensive tasks, leading to a significant reduction in operational expenses and improved efficiency.
PVC pipe bagging machines automate the packaging process, drastically cutting labor costs. By replacing manual bagging with automated systems, manufacturers reduce the need for large packaging teams, minimize labor-related expenses, and reallocate workforce to higher-value tasks, leading to significant operational savings.
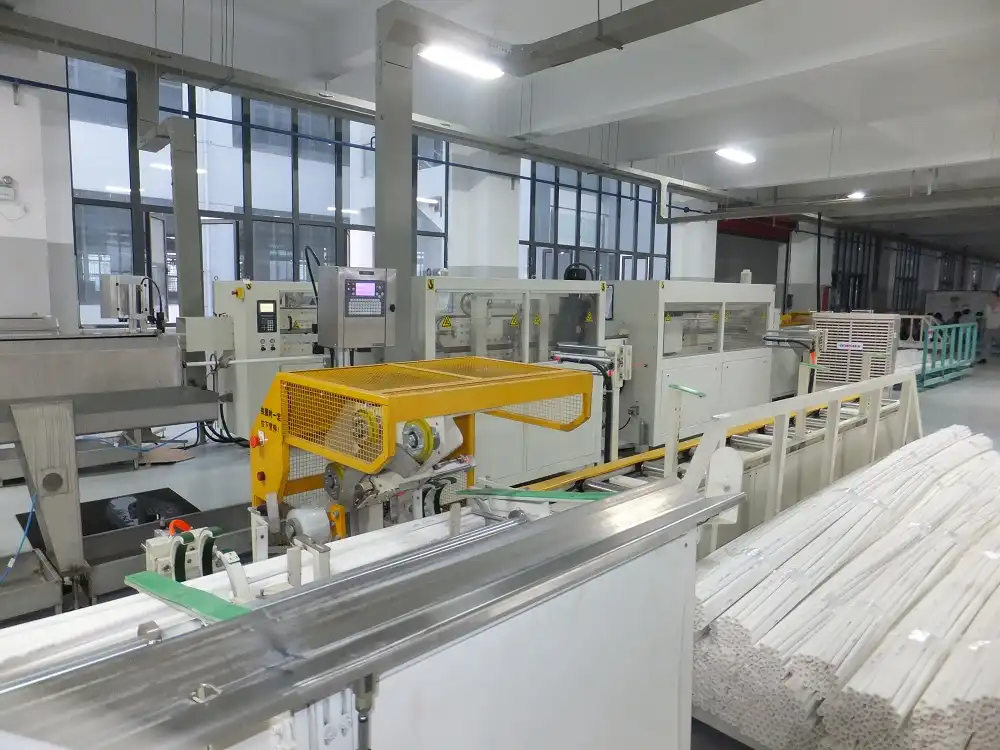
Let’s explore the detailed impact of automation on labor costs and operational efficiency, highlighting the financial advantages and strategic benefits for PVC pipe manufacturers. A closer look reveals how these machines are not just a purchase, but a strategic investment.
Quantifiable Labor Cost Savings Through Automation
The primary benefit of PVC pipe bagging machines lies in the direct reduction of labor costs. Manual bagging is a time-consuming and labor-intensive process, often requiring a significant workforce. Automating this process with bagging machines offers substantial savings in several key areas:
Cost Factor | Manual Bagging | Automated Bagging | Cost Reduction Potential |
---|---|---|---|
Labor Wages | High – Requires multiple workers | Low – Minimal operator supervision | 60-80% |
Benefits & Insurance | Higher costs for larger workforce | Lower costs due to reduced workforce | Proportional to Wage Savings |
Training Costs | Continuous training for bagging teams | Reduced training needs, focus on machine operation | 40-60% |
Error Rate | Higher – Human error prone | Lower – Consistent automated process | 70-90% |
Throughput | Lower – Speed limited by manual pace | Higher – Consistent machine speed | 100-300% |
As the table illustrates, the shift from manual to automated bagging significantly impacts various labor-related costs. The reduction in direct labor wages is the most obvious benefit, but the cascading effects on benefits, training, and reduced error rates further amplify the savings. Moreover, the increased throughput directly translates to higher productivity with the same or even reduced workforce size. This allows companies to reallocate human resources to other critical areas, enhancing overall operational efficiency and contributing to substantial inventory cost reduction by optimizing the flow and speed of packaged pipes ready for dispatch or storage.
2. Optimizing Warehouse Space and Reducing Storage Costs
Efficient utilization of warehouse space is paramount for minimizing inventory costs. PVC pipe bagging machines contribute significantly to space optimization by creating consistently sized and tightly packed bundles, maximizing storage density and reducing the overall footprint required for inventory.
PVC pipe bagging machines optimize warehouse space by creating uniform and compact pipe bundles. Consistent sizing allows for denser storage configurations, maximizing vertical and horizontal space utilization, reducing the overall warehouse footprint needed, and lowering storage-related costs like rent, utilities, and handling.
Let’s delve into the specifics of how optimized packaging from bagging machines translates to tangible reductions in storage expenses and improves overall warehouse management. This space-saving capability is a crucial element in driving down inventory costs.
Space Efficiency and Cost Savings in Warehousing
The space-saving advantages of PVC pipe bagging machines directly impact warehouse operational costs. Manually bundled pipes often result in irregular shapes and sizes, leading to wasted space during storage. Automated bagging ensures uniform and compact bundles, offering significant improvements:
Warehouse Cost | Manual Bundling | Automated Bagging | Space/Cost Reduction |
---|---|---|---|
Storage Footprint | Larger – Irregular bundle shapes | Smaller – Uniform, compact bundles | 20-40% space reduction |
Warehouse Rent/Lease | Higher – More space required | Lower – Less space needed | 20-40% proportional saving |
Utilities (Lighting, Heating, Cooling) | Higher – Larger space to maintain | Lower – Smaller space to manage | 10-20% utility reduction |
Handling Costs | Higher – Less efficient stacking | Lower – Easier, denser stacking | 15-25% handling cost cut |
Inventory Management | More complex, less accurate space utilization | Simpler, accurate space planning | Improved efficiency |
The consistent bundle dimensions achieved through automated bagging directly translate to a smaller storage footprint. This reduction in space requirement leads to proportional savings in warehouse rent or lease costs. Furthermore, a smaller storage area requires less energy for lighting, heating, and cooling, contributing to reduced utility expenses. Improved stacking efficiency due to uniform bundles also lowers handling costs and simplifies inventory management. The ability to store more pipes in less space significantly reduces overall inventory holding costs, making bagging machines a valuable asset in warehouse optimization.
3. Minimizing Product Damage and Reducing Material Waste
Damage during handling and storage leads to significant losses in the PVC pipe manufacturing industry. PVC pipe bagging machines are designed to provide secure and protective packaging, minimizing the risk of damage and consequently reducing material waste from damaged products and packaging.
PVC pipe bagging machines minimize product damage by providing secure and consistent packaging. This reduces damage during handling and transit, lowering the number of rejected or returned products, and minimizing material waste from both damaged pipes and packaging materials, contributing to significant cost savings and improved sustainability.
Let’s examine the specific ways in which bagging machines reduce damage and waste, leading to both cost savings and enhanced sustainability in PVC pipe operations. Reducing waste is not just about saving money, but also about responsible manufacturing.
Damage Reduction and Waste Minimization Strategies
PVC pipe bagging machines employ several strategies to minimize damage and waste compared to manual packaging methods:
Factor | Manual Packaging | Automated Bagging | Damage/Waste Reduction |
---|---|---|---|
Bundle Security | Less secure, inconsistent tying | Tighter, consistent wrapping | 30-50% damage reduction |
Protection from Elements | Less protection, open bundles | Full enclosure, weather protection | 20-40% reduction in weather-related damage |
Handling Damage | Higher risk during manual handling | Reduced handling, stable bundles | 40-60% reduction in handling damage |
Packaging Material Waste | Higher – Inconsistent usage | Lower – Optimized material use | 15-30% packaging waste cut |
Product Rejection Rate | Higher – Damage during handling | Lower – Protective packaging | 20-35% decrease in rejections |
Automated bagging machines provide tighter and more consistent wrapping compared to manual tying, significantly enhancing bundle security and reducing damage from impacts or vibrations during handling and transit. The full enclosure offered by bagging machines also provides better protection against environmental elements like moisture and dust, further minimizing damage. Reduced manual handling due to automated systems minimizes the risk of damage during the packaging process itself. Moreover, automated systems optimize packaging material usage, reducing waste from excess material application common in manual packaging. The combined effect of these factors is a significant reduction in product rejection rates due to damage, leading to substantial savings and a more sustainable operation by minimizing wasted materials and resources.
4. Enhancing Throughput and Operational Efficiency for Cost Savings
PVC pipe bagging machines are designed for high-speed operation, significantly increasing packaging throughput compared to manual methods. This enhanced efficiency not only speeds up the production process but also contributes to substantial operational cost savings by optimizing resource utilization and reducing bottlenecks.
To fully appreciate the impact on operational efficiency, let’s analyze the specific improvements in throughput and resource utilization achieved through automation, highlighting the direct link to cost reduction. Efficiency gains are crucial for maintaining competitiveness in the PVC pipe industry.
PVC pipe bagging machines dramatically improve throughput and operational efficiency in PVC pipe manufacturing. Compared to manual bagging, these machines operate at significantly higher speeds, packaging bundles consistently and quickly. This increased throughput reduces bottlenecks in the production line, optimizes the use of resources, and lowers per-unit operational costs, leading to substantial savings and improved profitability.
Automated bagging systems offer a step change in throughput compared to manual processes. Manual bagging is inherently limited by human speed and fatigue, leading to slower packaging rates and potential bottlenecks. Bagging machines, on the other hand, operate at consistent high speeds, drastically increasing the number of bundles packaged per hour. This enhanced throughput translates to several operational benefits and cost savings:
Efficiency Metric | Manual Bagging | Automated Bagging | Efficiency Improvement |
---|---|---|---|
Packaging Speed | Lower – Limited by manual pace | Higher – Consistent machine speed | 300-500% speed increase |
Throughput Capacity | Lower – Bottlenecks in packaging | Higher – Streamlined packaging flow | Significant increase |
Production Cycle Time | Longer – Packaging slows process | Shorter – Faster packaging integrates | 20-30% reduction |
Resource Utilization | Less efficient, potential idle time | Optimized, continuous operation | Improved utilization |
Per-Unit Cost | Higher – Labor intensive | Lower – Automation reduces unit cost | 15-25% cost reduction |
The dramatic increase in packaging speed offered by bagging machines directly boosts throughput capacity, eliminating packaging bottlenecks that can slow down the entire production line. This faster packaging process reduces overall production cycle time, allowing for quicker order fulfillment and improved responsiveness to market demands. Optimized resource utilization means continuous operation with minimal idle time, further enhancing efficiency. Ultimately, the increased throughput and streamlined operations translate to lower per-unit production costs, as the same or even reduced resources can produce a significantly higher volume of packaged pipes. This operational efficiency is a key driver in achieving substantial cost savings and improving profitability for PVC pipe manufacturers.
5. Cost-Effective Investment and Long-Term ROI
Investing in PVC pipe bagging machines represents a strategic financial decision with significant long-term returns. While the initial investment requires capital expenditure, the operational cost savings, efficiency gains, and reduced losses quickly contribute to a substantial return on investment (ROI), making these machines a cost-effective solution in the long run.
To understand the true cost-effectiveness, we need to consider not just the upfront cost, but also the long-term savings and benefits. The ROI justifies the initial investment and demonstrates the financial prudence of adopting automation.
PVC pipe bagging machines are a cost-effective investment, offering a strong long-term ROI. The initial investment is offset by significant operational cost reductions in labor, warehouse space, material waste, and product damage. Increased throughput and efficiency further enhance profitability, leading to a rapid payback period and sustained financial benefits over the machine’s lifespan, making it a sound financial decision.
While the initial purchase of a PVC pipe bagging machine involves a capital outlay, the long-term financial benefits far outweigh the upfront costs. The ROI is driven by the cumulative effect of various cost savings and efficiency improvements:
ROI Component | Financial Impact | Long-Term Benefit |
---|---|---|
Labor Cost Savings | Direct reduction in wages, benefits, training | Sustained savings over machine lifespan |
Warehouse Space Savings | Lower rent, utilities, handling costs | Reduced operational overhead, scalable space efficiency |
Waste Reduction | Minimized material waste, fewer rejected products | Lower material costs, improved sustainability |
Damage Reduction | Fewer returns, replacements, and customer disputes | Enhanced customer satisfaction, brand reputation |
Throughput Increase | Higher production volume, faster order fulfillment | Increased revenue potential, market responsiveness |
The combined financial impact of these components leads to a compelling ROI. The direct labor cost savings alone can often justify a significant portion of the investment within a relatively short period. When coupled with savings in warehouse space, reduced waste and damage, and increased throughput, the payback period for a PVC pipe bagging machine can be remarkably short, often within 1-3 years depending on production volume and operational scale. Beyond the payback period, the machine continues to generate sustained financial benefits throughout its operational life, making it a highly cost-effective and financially sound investment for PVC pipe manufacturers seeking to optimize their operations and reduce inventory costs. Investing in PVC pipe bagging machines is not just an expense, but a strategic move towards long-term profitability and operational excellence.
Conclusion
PVC pipe bagging machines offer a compelling solution for reducing inventory costs and enhancing operational efficiency in PVC pipe manufacturing. By automating the packaging process, these machines deliver quantifiable benefits across various aspects of operations, from labor and warehouse space optimization to damage and waste reduction. The long-term ROI and sustained financial advantages make them a strategically sound investment for manufacturers seeking to improve their bottom line and maintain a competitive edge in the market. Adopting automated bagging systems is a step towards a more efficient, cost-effective, and sustainable future for PVC pipe production.