What Are the Applications of Mold Flippers in the Automotive Industry?
Mold flippers are indispensable pieces of equipment within modern manufacturing, and their utility is particularly pronounced in the automotive industry. These machines provide a safe and efficient method for rotating heavy and cumbersome molds, which are essential for producing vehicle components.
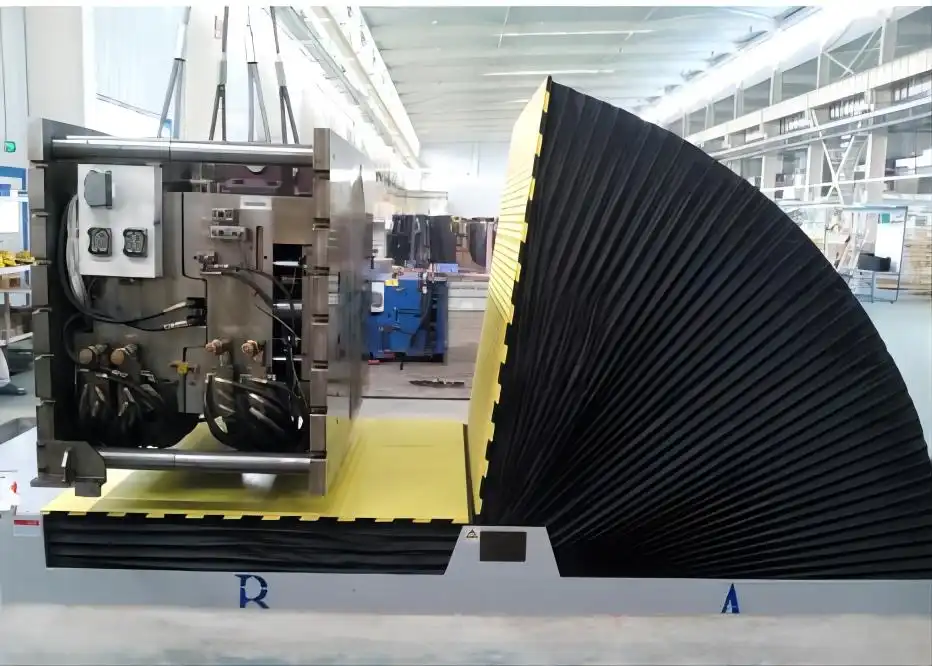
Mold flippers in the automotive industry are primarily used for mold maintenance, repair, and efficient handling during production processes. They facilitate easier access to all mold sides for cleaning, inspection, and part replacement, significantly reducing downtime and enhancing workplace safety. Furthermore, mold flippers are crucial for integrating molds with die spotting presses, ensuring precise alignment and improving the overall quality of automotive part manufacturing.
This article will explore the diverse applications of mold flippers within the automotive sector, highlighting their structural advantages, efficiency gains, safety benefits, and the different types tailored to meet the industry’s demanding needs. Continue reading to understand how these powerful machines are revolutionizing automotive manufacturing processes.
1. Understanding the Structure and Key Components of Mold Flippers in Automotive Applications
The robust structure of a mold flipper is critical for its effective operation, especially when handling the heavy molds common in automotive part production. These machines are engineered to provide stability and precision throughout the mold flipping process.
Mold flippers typically comprise four main structural sections: the upper support, lower base, the core flipping mechanism, and an advanced control system. The upper section securely holds the mold, while the lower section provides a stable foundation. The flipping mechanism, powered by hydraulics or motors, ensures smooth and controlled rotation. Finally, the control system allows for precise operation and integration with automotive production lines, enhancing both efficiency and safety.

Deep Dive into Mold Flipper Components and Their Automotive Benefits
To fully appreciate the role of mold flippers in the automotive industry, it is essential to understand the function of each key component and how they contribute to the overall efficiency and safety of mold handling. Breaking down the structure reveals why these machines are so vital for modern automotive manufacturing.
The Upper and Lower Sections: Foundation of Stability
The upper and lower sections of a mold flipper work in tandem to provide a secure and stable platform for heavy automotive molds. The upper section is typically constructed from high-strength steel to withstand the considerable weight of molds, ensuring no deformation or failure during operation. Its design is often customized to accommodate various mold sizes and shapes, offering versatility for different automotive components.
The lower section mirrors the upper section in robustness, providing a solid base that anchors the entire machine. Adjustable height features in the lower section are crucial for adapting to different mold heights and integrating seamlessly with existing automotive production line setups. This adjustability enhances the flipper’s adaptability and utility across diverse manufacturing needs.
Flipping Mechanism: The Heart of the Operation
The flipping mechanism is the core of a mold flipper, responsible for the controlled rotation of molds. In automotive applications, precision and reliability are paramount. These mechanisms generally employ a combination of motors, reducers, and transmission systems. Hydraulic systems are also common, particularly for heavier molds, offering smooth and powerful rotation.
Key design considerations for the flipping mechanism include the degree of rotation (often 90° or 180°), rotational speed, and overall stability during movement. The mechanism must ensure smooth, jerk-free motion to prevent damage to expensive automotive molds and ensure operator safety.
Control System: Ensuring Precision and Safety
The control system acts as the brain of the mold flipper, governing all operational aspects from rotation speed to safety protocols. Modern mold flippers utilize Programmable Logic Controllers (PLCs) and user-friendly Human-Machine Interfaces (HMIs). These systems allow operators to precisely set parameters, monitor the flipping process in real-time, and ensure consistent and safe operation.
Advanced control systems in automotive settings often include features like overload protection, emergency stop functions, and integration capabilities with factory management systems. This level of control is essential for maintaining high throughput and minimizing downtime in automotive manufacturing environments.
Component | Function | Automotive Industry Benefit |
---|---|---|
Upper Section | Securely holds and supports the mold | Adaptability to various mold sizes, stability during flipping |
Lower Section | Provides stable base, often with height adjustability | Versatility in production line integration, foundational support |
Flipping Mechanism | Rotates the mold smoothly and precisely | Controlled and safe mold movement, prevents damage |
Control System | Manages operation, safety, and integration | Precision, safety, and seamless integration with factory systems |
By understanding these key structural components, automotive manufacturers can better appreciate how mold flippers enhance their production processes, contributing to greater efficiency, safety, and overall manufacturing excellence.
2. Enhancing Efficiency in Automotive Mold Maintenance
Efficient mold maintenance is crucial in the automotive industry to ensure consistent production quality and minimize downtime. Mold flippers play a pivotal role in streamlining these maintenance processes, making them faster, safer, and more effective.
Mold flippers significantly enhance the efficiency of automotive mold maintenance by providing easy and safe access to all parts of the mold. Rotating molds with flippers allows technicians to perform cleaning, repairs, and component replacements without strenuous manual handling. This not only speeds up maintenance tasks but also reduces the risk of damage to the molds and injuries to personnel, ultimately boosting productivity and reducing operational costs.
A Detailed Look at Efficiency Gains in Automotive Mold Maintenance
The implementation of mold flippers in automotive maintenance facilities brings about a paradigm shift in operational efficiency. By eliminating the cumbersome and time-consuming manual methods of mold handling, these machines unlock significant improvements in workflow and resource utilization.
Faster Turnaround Times
Traditionally, mold maintenance in automotive plants involved manual labor and overhead cranes to rotate and position heavy molds. This process was not only slow but also posed significant safety risks. Mold flippers automate the rotation process, reducing the time required to access different mold faces from hours to minutes. Faster access translates directly to quicker maintenance cycles and reduced downtime for production lines.
Optimized Accessibility
Mold flippers provide 360-degree access to molds, allowing technicians to work on all surfaces and internal components without repositioning the mold multiple times. This enhanced accessibility is particularly beneficial for complex automotive molds that require intricate cleaning and repair procedures. Technicians can perform tasks more efficiently, leading to higher quality maintenance and fewer errors.
Reduced Labor Costs
By automating mold rotation, mold flippers reduce the reliance on manual labor for heavy lifting and maneuvering. This not only decreases labor costs but also frees up personnel to focus on more skilled maintenance tasks. The reduced physical strain on workers also leads to a healthier and more productive workforce.
Improved Preventative Maintenance
The ease of access provided by mold flippers encourages more frequent and thorough preventative maintenance. Regular inspections and cleaning can be performed quickly and efficiently, preventing minor issues from escalating into major problems that could cause significant production delays. This proactive approach to maintenance extends the lifespan of automotive molds and ensures consistent part quality.
In summary, mold flippers are not just about making maintenance easier; they are about fundamentally transforming the efficiency of automotive mold maintenance, leading to faster turnaround times, optimized accessibility, reduced labor costs, and improved preventative maintenance practices.
3. Safety Advantages of Mold Flippers in Automotive Manufacturing
Safety is paramount in the automotive industry, especially when dealing with heavy machinery and molds. Mold flippers significantly enhance workplace safety by automating the hazardous task of mold rotation, minimizing risks to personnel and preventing damage to valuable equipment.
The primary safety advantage of mold flippers in automotive manufacturing is the reduction of manual handling of heavy molds. These machines eliminate the need for workers to physically rotate or maneuver molds, thereby decreasing the risk of back injuries, strains, and accidents caused by dropped molds. Advanced safety features integrated into mold flippers, such as secure clamping mechanisms and controlled rotation speeds, further ensure a safer working environment.
Quantifying Safety Improvements with Mold Flippers in Automotive Plants
The integration of mold flippers into automotive manufacturing facilities translates to tangible improvements in safety metrics. By mitigating key hazards associated with manual mold handling, these machines contribute to a significantly safer operational environment.
Reduction in Manual Handling Injuries
Manual handling of heavy molds is a major source of workplace injuries in automotive plants. These injuries range from musculoskeletal disorders to acute injuries from accidents. Mold flippers drastically reduce manual handling, leading to a significant decrease in these types of injuries. Studies have shown a direct correlation between the implementation of automated handling equipment and a reduction in workplace injury rates.
Minimized Risk of Mold Damage
Accidental drops or mishandling during manual mold rotation can cause severe damage to molds, leading to costly repairs and production delays. Mold flippers provide controlled and stable rotation, minimizing the risk of such accidents. Secure clamping systems and smooth rotation mechanisms ensure that molds are handled with utmost care, preventing damage and preserving their integrity.
Enhanced Operational Control and Emergency Preparedness
Modern mold flippers are equipped with sophisticated control systems that include multiple safety features. Emergency stop buttons, overload protection, and automated safety protocols ensure that operations can be halted immediately in case of any anomaly. These features provide an added layer of safety, ensuring that potential hazards are quickly addressed and controlled.
Safety Aspect | Risk with Manual Handling | Benefit with Mold Flipper |
---|---|---|
Manual Handling Injuries | High risk of strains, back injuries, accidents | Significantly reduced due to automation |
Mold Damage Risk | High risk from drops and mishandling | Minimized through controlled and stable rotation |
Operational Control | Limited control, potential for human error | Enhanced control, automated safety protocols |
Emergency Preparedness | Slower response in emergencies | Immediate stop functions, faster response |
By quantifying these safety improvements, automotive manufacturers can clearly see the value of mold flippers not only in terms of efficiency but also in creating a safer and more responsible working environment for their employees.
4. Diverse Types of Mold Flippers Used in the Automotive Sector
The automotive industry utilizes a variety of mold flippers, each designed to meet specific needs based on mold size, weight, and operational requirements. Understanding these different types is crucial for selecting the right equipment to optimize automotive manufacturing processes.
Automotive mold flippers range from standard 90-degree and 180-degree rotation models to customized designs for specific applications. Common types include hydraulic mold flippers for heavy loads, motorized flippers for precise control, and tilting flippers for versatile mold positioning. The selection depends on the scale of operations, the types of molds used, and the integration requirements within the automotive production line. Customized solutions are often developed to address unique manufacturing challenges.
Mold flippers come in various configurations to suit the diverse needs of the automotive industry. Here are some common types:
-
90-Degree Mold Flippers: These are designed to rotate molds by 90 degrees, typically used when molds need to be tilted for maintenance or integration with vertical die spotting presses. They are ideal for scenarios where molds need to be accessed from the side.
-
180-Degree Mold Flippers: These flippers provide a full 180-degree rotation, allowing molds to be completely inverted. This is particularly useful for thorough cleaning, repair, and modifications that require access to both halves of the mold.
-
Hydraulic Mold Flippers: Powered by hydraulic systems, these flippers are capable of handling extremely heavy molds, often exceeding 50 tons. They offer robust and reliable performance for the large molds used in automotive body panel and chassis component production.
-
Motorized Mold Flippers: Using electric motors for rotation, these flippers offer precise control over speed and positioning. They are well-suited for applications requiring delicate handling and accurate alignment, often used for molds producing intricate interior parts and electronic components.
-
Customized Mold Flippers: Many automotive manufacturers require tailored solutions to address specific challenges. Customized mold flippers can be designed with unique dimensions, load capacities, and rotation angles to perfectly integrate into existing production lines and handle specialized molds.
The choice of mold flipper type is a critical decision, impacting efficiency, safety, and the overall effectiveness of automotive manufacturing operations. Manufacturers must carefully consider their specific needs and operational context to select the most appropriate mold flipper technology.
Conclusion
Mold flippers are essential assets in the automotive industry, providing significant enhancements in efficiency, safety, and maintenance operations. From facilitating faster mold turnaround and improving workplace safety to enabling more effective maintenance and offering diverse types for varied applications, their impact is profound. By investing in and leveraging advanced mold flipper technology, automotive manufacturers can achieve higher productivity, reduce operational costs, and ensure a safer working environment, ultimately driving progress and maintaining competitiveness in a demanding global market.