1. What Are the Alkali Resistance Requirements for Steel Coil Packing?
Steel coil packing is essential for protecting coils from environmental damage during storage and transportation. This packing must withstand various conditions, and alkali resistance is a critical requirement to prevent degradation and maintain the integrity of both the packing and the steel coil itself. Understanding these requirements is crucial for industries relying on steel coils.
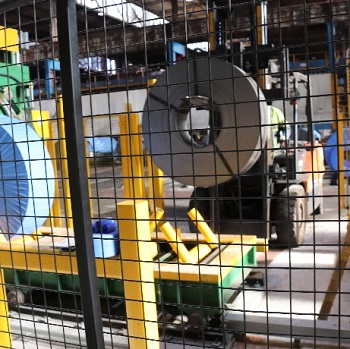
Alkali resistance in steel coil packing refers to the ability of the packing materials to withstand degradation or damage when exposed to alkaline substances. This is vital to prevent the packing from weakening or failing, ensuring the steel coil remains protected from corrosion, physical damage, and environmental contaminants throughout its journey from production to end-use.
Protecting steel coils effectively requires a multi-faceted approach, and understanding alkali resistance is a key component. Let’s delve deeper into the specific requirements and considerations for robust steel coil packing.
2. Understanding Alkali Resistance in Coil Packing Materials
Alkali resistance is not merely a desirable trait but a fundamental necessity for steel coil packing. The environments in which steel coils are stored and transported often present alkaline challenges, from cleaning agents to industrial byproducts. Therefore, the packing materials must be inherently resistant to alkaline substances to maintain their protective properties.
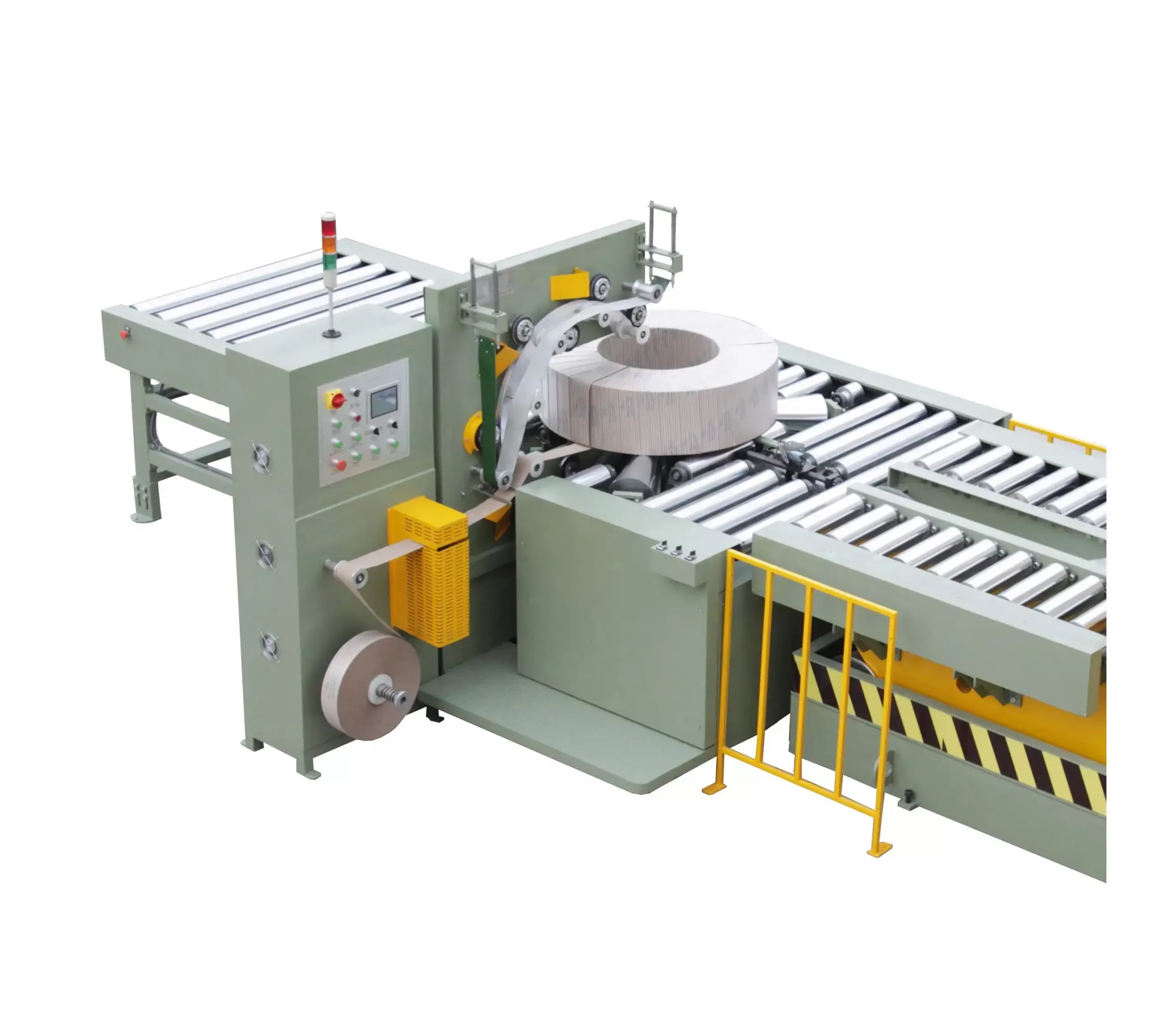
For steel coil packing, alkali resistance is paramount. Materials must resist chemical degradation, maintaining structural integrity and barrier properties upon exposure to alkaline substances. Key requirements include minimal weight or strength loss, no significant surface damage, and sustained flexibility to ensure long-term coil protection against corrosion and physical damage in alkaline environments.
To fully grasp the alkali resistance requirements, we must consider the nature of alkaline environments and how they interact with packing materials.
2.1. Defining Alkali Exposure and its Impact on Packing
Alkaline substances, also known as bases, have a pH level greater than 7. Common examples include sodium hydroxide (caustic soda), potassium hydroxide (caustic potash), calcium hydroxide (lime), and ammonia. Exposure to these substances can occur in various forms:
- Cleaning Solutions: Alkaline cleaners are frequently used in industrial settings and during coil processing, and residue may come into contact with the packing.
- Industrial Environments: Certain industrial environments, such as those involving cement production or some chemical processing, can have airborne alkaline dust or vapors.
- Natural Environments: While less common, certain soil types or geological formations might expose coils to alkaline conditions if stored directly on the ground without proper barriers.
The impact of alkali exposure on packing materials can be detrimental:
- Chemical Degradation: Alkaline substances can react with certain polymers or coatings, leading to hydrolysis, saponification, or other forms of chemical breakdown. This weakens the material structure.
- Loss of Strength and Flexibility: Degradation weakens the packing material, reducing its tensile strength, tear resistance, and puncture resistance. This compromises its ability to physically protect the coil.
- Barrier Failure: Alkali-induced damage can compromise the barrier properties of the packing, making it less effective at preventing moisture ingress, corrosion, and contamination.
To mitigate these risks, specific alkali resistance requirements must be met by the packing materials.
2.2. Quantifying Alkali Resistance: Key Material Properties
Alkali resistance is not a single property but a combination of several material characteristics. To ensure effective steel coil packing, manufacturers and users must consider these key aspects:
Property | Description | Importance for Alkali Resistance | Testing Method |
---|---|---|---|
Chemical Stability | Resistance to chemical reactions with alkaline substances. | Prevents material degradation, maintains structural integrity and barrier function. | Immersion tests in alkaline solutions, followed by property evaluation (tensile, weight change). |
Hydrolysis Resistance | Ability to withstand breakdown in the presence of water and alkaline conditions. | Crucial for preventing polymer chain scission and material weakening in humid, alkaline environments. | Accelerated aging tests in humid environments with alkaline exposure, property retention analysis. |
Tensile Strength Retention | Maintenance of mechanical strength after alkali exposure. | Ensures the packing can still withstand stresses during handling and transportation after exposure. | Tensile testing before and after alkali exposure, expressed as percentage retention. |
Barrier Properties Retention | Ability to maintain impermeability to moisture and contaminants. | Critical for preventing corrosion even after alkaline exposure. | Water vapor transmission rate (WVTR) testing, gas permeability testing before and after exposure. |
These properties must be evaluated through rigorous testing to confirm the suitability of packing materials for alkaline environments.
3. Selecting Coil Packing Machines for Alkali Resistance
The choice of coil packing machine is intrinsically linked to alkali resistance. While the packing materials provide the primary barrier, the machine ensures consistent and effective application, minimizing vulnerabilities and maximizing protection. Machines designed for alkali resistance incorporate features that complement the material properties and enhance overall performance.
Coil packing machines contribute significantly to alkali resistance by ensuring uniform and secure application of protective materials. Machines designed for this purpose often feature specialized tension control, overlap mechanisms, and material compatibility to optimize the alkali barrier and prevent weak points in the packing that could be vulnerable to chemical ingress.
Beyond material selection, the coil packing process itself plays a critical role in achieving alkali resistance.
3.1. Machine Features Enhancing Alkali Resistance
Specific features in coil packing machines are essential for maximizing alkali resistance:
- Consistent Tension Control: Proper tension during wrapping is crucial. Excessive tension can stretch and weaken some materials, reducing their barrier properties and alkali resistance. Consistent tension ensures uniform material thickness and integrity.
- Overlap Precision: Adequate overlap during spiral wrapping creates a layered barrier, enhancing protection. Precise overlap control by the machine ensures no gaps or weak points where alkaline substances could penetrate.
- Material Compatibility: Machines should be designed to handle alkali-resistant packing materials without causing damage or compromising their properties. This includes smooth rollers, adjustable settings, and material-specific tension adjustments.
- Sealing Mechanisms: For certain packing types like heat-sealed wraps, the machine’s sealing mechanism must create robust, alkali-resistant seals that maintain their integrity over time and under alkaline exposure.
- Automated Application: Automation minimizes human error in the packing process, ensuring consistent application quality across all coils and reducing the risk of flaws that could compromise alkali resistance.
By selecting machines with these features, manufacturers can optimize the application of alkali-resistant packing materials and create a robust protective system for steel coils.
3.2. Optimizing the Packing Process for Alkali Environments
Beyond machine features, the entire packing process should be optimized for alkali resistance:
- Material Selection Based on Alkali Type: Identify the specific alkaline substances the coils are likely to encounter. Select packing materials specifically tested and certified for resistance to those alkalis. Refer to chemical resistance charts and material data sheets.
- Proper Material Handling and Storage: Store packing materials in a clean, dry environment, away from potential alkaline contaminants. Handle materials carefully during loading into the packing machine to avoid damage.
- Regular Machine Calibration and Maintenance: Ensure the coil packing machine is properly calibrated for tension control and overlap. Regular maintenance prevents malfunctions that could lead to inconsistent packing and compromised alkali resistance.
- Quality Control Checks: Implement quality control checks to verify the integrity of the applied packing. This includes visual inspections for proper overlap and tension, and periodic testing of packed coils for barrier properties and alkali resistance after simulated exposure.
- Layered Packing Systems: Consider using layered packing systems, combining materials with different strengths. For example, an inner layer with high alkali resistance and an outer layer with robust physical protection. This provides redundancy and enhanced overall protection.
Optimizing both the machine and the process is essential for achieving reliable alkali resistance in steel coil packing.
4. Chemical Resistance Beyond Alkalis: A Holistic Approach
While alkali resistance is paramount in many scenarios, a holistic approach to chemical resistance is crucial for comprehensive steel coil protection. Steel coils may encounter a wide array of chemicals during their lifecycle, from acidic cleaning agents to industrial solvents. Packing materials must therefore exhibit broad chemical resistance to ensure consistent protection across diverse environments.
Comprehensive chemical resistance for steel coil packing extends beyond just alkali resistance. It encompasses the ability to withstand acids, solvents, oils, and other industrial chemicals without degradation. Selecting materials with broad chemical inertness ensures robust protection in diverse and unpredictable environments, safeguarding the steel coil from a range of chemical threats.
To achieve truly effective protection, consider the broader spectrum of chemical challenges steel coils might face.
4.1. Understanding the Chemical Spectrum: Acids, Solvents, and More
Steel coils can be exposed to various chemical categories:
- Acids: Acids, with a pH below 7, are common in cleaning solutions (e.g., hydrochloric acid, sulfuric acid), pickling processes, and some industrial environments. Acidic exposure can corrode steel directly and degrade certain packing materials.
- Solvents: Organic solvents, such as toluene, xylene, acetone, and various hydrocarbons, are used in cleaning, degreasing, and industrial processes. Solvents can dissolve or swell certain polymers, weakening packing materials.
- Oils and Greases: Lubricating oils, hydraulic fluids, and greases are prevalent in industrial and transportation settings. While often less chemically aggressive, prolonged oil/grease exposure can degrade some packing materials and attract dirt and contaminants.
- Salts: Salt solutions, particularly chlorides, are highly corrosive to steel and can be present in marine environments, de-icing salts, and certain industrial processes. Packing must resist salt penetration to prevent corrosion.
- Specialty Chemicals: Depending on the industry, coils might encounter specific chemicals like plating solutions, specialized cleaning agents, or process chemicals. Packing selection must consider these unique exposures.
A packing material effective against alkalis might not necessarily resist acids or solvents equally well. Therefore, broad chemical resistance is paramount.
4.2. Material Selection for Broad Chemical Resistance
Choosing packing materials with inherent broad chemical resistance is the most effective strategy. Consider these material properties:
Material Type | Chemical Resistance Strengths | Chemical Resistance Limitations | Common Coil Packing Applications |
---|---|---|---|
Polyethylene (PE) Films | Good resistance to alkalis, acids, and many solvents. Cost-effective. | Limited resistance to strong oxidizing agents and some hydrocarbons. Lower temperature resistance. | General purpose wrapping, moisture barrier. |
Polypropylene (PP) Films | Excellent resistance to many solvents and chemicals, including acids and alkalis. Higher temperature resistance than PE. | May be susceptible to degradation by strong oxidizing acids. Can be brittle at low temperatures. | High-temperature applications, demanding chemical environments. |
Fluoropolymers (e.g., PTFE, FEP) | Exceptional resistance to virtually all chemicals, including strong acids, alkalis, and solvents. High temperature resistance. | Very expensive. Can be difficult to process and seal. | Highly corrosive environments, specialized applications. |
VCI (Vapor Corrosion Inhibitor) Films | Combines barrier properties with corrosion inhibiting chemicals. Good alkali and general chemical resistance depending on base polymer. | Chemical resistance depends on the base polymer. Can be more expensive than standard films. | Long-term storage, demanding environments requiring corrosion protection. |
Note: The chemical resistance data provided earlier for borosilicate glass and PBT is illustrative of chemical resistance concepts, but these materials are not typically used directly as coil packing films. The table above focuses on common polymer types used in flexible coil packing.
When selecting materials, always consult chemical resistance charts and material compatibility guides specific to the chemicals of concern.
5. Material Properties: The Foundation of Alkali and Chemical Resistance
Ultimately, the alkali and broader chemical resistance of steel coil packing hinges on the inherent properties of the materials used. Understanding these properties allows for informed material selection and ensures the packing system is robust enough to withstand the intended environment.
The material properties of steel coil packing are fundamental to achieving alkali and chemical resistance. Key properties include chemical inertness, impermeability, tensile strength, and tear resistance. Selecting materials with optimal combinations of these properties ensures long-lasting protection against chemical degradation and physical damage, maintaining coil integrity throughout the supply chain.
Let’s explore the material properties that underpin effective chemical resistance in coil packing.
5.1. Key Material Properties for Chemical Resistance
Several material properties are crucial for achieving alkali and chemical resistance:
- Chemical Inertness: The material’s inherent resistance to reacting with a wide range of chemicals. Inert materials minimize degradation and maintain their original properties.
- Impermeability: Low permeability to liquids, vapors, and gases. This prevents chemicals from penetrating the packing and reaching the steel coil surface.
- Density and Crystallinity: Higher density and crystallinity in polymers often correlate with improved chemical resistance. Tightly packed molecular structures are less susceptible to chemical ingress.
- Tensile Strength and Elongation: Sufficient tensile strength to withstand mechanical stresses during handling and transportation, even after chemical exposure. Elongation allows for some stretching and deformation without tearing.
- Tear and Puncture Resistance: Resistance to tearing and puncture prevents breaches in the packing barrier, maintaining chemical protection.
- Temperature Resistance: The material’s ability to maintain its properties over the expected temperature range of storage and transportation. Chemical reactions often accelerate at higher temperatures.
- UV Resistance (if applicable): For outdoor storage, UV resistance prevents degradation from sunlight, which can exacerbate chemical attack and weaken the material.
These properties must be balanced to achieve optimal performance and cost-effectiveness.
5.2. Balancing Properties for Optimal Performance
Material selection involves trade-offs and optimization:
Material Property | Benefit | Potential Trade-off | Optimization Strategy |
---|---|---|---|
High Chemical Inertness | Broad protection against diverse chemicals, long-lasting protection. | Can be more expensive materials, potentially lower mechanical strength in some cases. | Selectively use higher-cost, highly inert materials for critical applications or inner layers in layered packing systems. |
High Impermeability | Excellent barrier to moisture and chemical ingress, prevents corrosion effectively. | Can be less flexible or more prone to puncture in some materials, potentially higher cost. | Optimize material thickness and consider multi-layer structures to balance barrier properties with flexibility and cost. |
High Tensile Strength | Robust physical protection, withstands handling stresses, reduces risk of tearing during application. | Can sometimes compromise flexibility or tear resistance in certain materials. | Choose materials with balanced tensile strength and tear resistance. Consider reinforcement layers for extreme stress. |
Cost-Effectiveness | Economical packing solutions, suitable for large-volume applications. | May compromise on extreme chemical resistance or longevity in highly demanding environments. | Match material cost to the specific environmental risks and required protection level. Use cost-effective materials where risks are lower. |
The optimal material choice depends on a thorough risk assessment, considering the specific chemicals, environmental conditions, handling requirements, and budget constraints.
6. Conclusion
Ensuring alkali resistance is a critical, but not isolated, requirement for effective steel coil packing. It is part of a broader need for robust chemical resistance and material performance to protect steel coils throughout their lifecycle. By understanding the specific alkali resistance requirements, selecting appropriate coil packing machines, considering the spectrum of chemical threats, and focusing on key material properties, industries can safeguard their steel coil investments and ensure product integrity from production to final use. A holistic and informed approach to coil packing is essential for long-term reliability and cost-effectiveness in steel handling and transportation.