1. What Are the Advantages of PVC Pipe Bagging Machines in Reducing Labor Injuries?
PVC pipe bagging machines are revolutionizing material handling in manufacturing, significantly decreasing workplace injuries. These automated systems streamline packaging processes, moving away from strenuous manual labor to efficient, mechanized operations. This shift dramatically reduces the risks associated with heavy lifting, repetitive motions, and awkward postures common in manual pipe bagging.
PVC pipe bagging machines offer significant advantages in reducing labor injuries by automating heavy lifting, minimizing repetitive tasks, and creating safer working environments. This automation directly addresses common causes of workplace injuries, such as back strains, sprains, and musculoskeletal disorders, leading to a healthier and more productive workforce in pipe manufacturing and handling.
The transition to automated bagging systems marks a crucial step forward in prioritizing worker safety. By understanding the specific advantages these machines offer, businesses can make informed decisions to protect their employees and improve operational efficiency. Let’s explore the key benefits in detail.
2. Minimizing Musculoskeletal Disorders Through Automation
Manual handling of PVC pipes is inherently demanding, often leading to musculoskeletal disorders (MSDs). Workers manually lifting, stacking, and bagging heavy pipes are at high risk of strains, sprains, and chronic back problems. Automation directly addresses these risks.
PVC pipe bagging machines drastically reduce the incidence of musculoskeletal disorders by eliminating the need for manual lifting and repetitive motions. These machines handle the heavy lifting, positioning, and bagging of pipes, thereby significantly decreasing the physical strain on workers and preventing common MSDs associated with manual packaging processes.
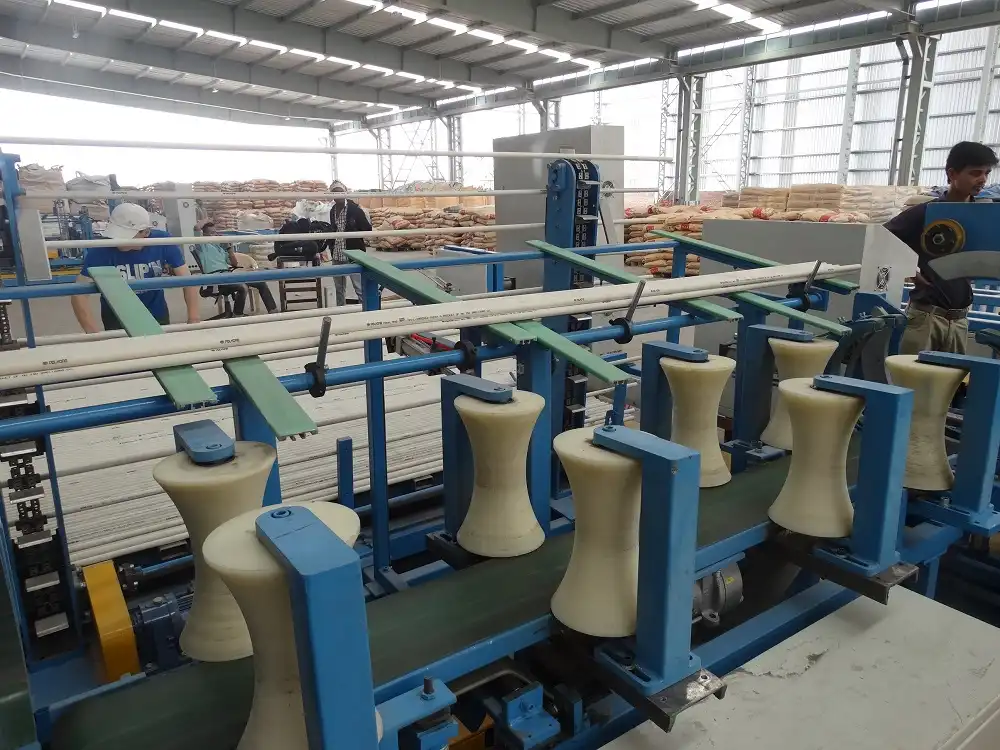
To fully appreciate the impact, let’s examine how automation tackles specific MSD risk factors in pipe bagging:
Addressing Key MSD Risk Factors in Manual Pipe Bagging
Manual pipe bagging is rife with ergonomic hazards that contribute to MSDs. Automated bagging machines are engineered to mitigate these specific risks, creating a safer and more sustainable work environment.
Repetitive Lifting and Bending
The constant need to lift and bend while manually bagging pipes is a primary cause of back injuries and strains. Automated systems eliminate this by using机械手臂 or conveyors to move and position pipes.
Awkward Postures
Manual bagging often requires workers to adopt awkward postures to reach, lift, and position pipes, especially when dealing with larger diameters or bundles. Machines are designed to maintain optimal workflow, ensuring pipes are presented in positions that eliminate awkward reaching or bending.
Excessive Force
Lifting and maneuvering heavy PVC pipes requires significant physical force, leading to muscle fatigue and injury over time. Automated bagging machines utilize powered mechanisms to handle the weight of the pipes, completely removing the need for workers to exert excessive force.
High Frequency of Repetition
The repetitive nature of manual bagging tasks, performed continuously throughout a shift, exacerbates the strain on muscles and joints. Automation reduces the human involvement in repetitive actions, with machines performing these tasks at a consistent pace without causing physical stress to operators.
To illustrate the contrast, consider this comparison:
Risk Factor | Manual Pipe Bagging | Automated Pipe Bagging | Injury Potential |
---|---|---|---|
Lifting & Bending | Frequent, heavy lifting from ground level | Eliminated, pipes moved by machine | High |
Posture | Awkward reaching, bending, twisting | Optimized, machine presents pipes in ergonomic positions | High |
Force Exertion | High, required to lift and maneuver heavy pipes | Minimal, machine handles heavy loads | High |
Repetition Frequency | Very High, continuous bagging throughout shift | Low, operator primarily monitors machine | High |
Overall MSD Risk | Significantly High | Significantly Reduced |
By directly addressing these core ergonomic risk factors, PVC pipe bagging machines are instrumental in preventing MSDs and fostering a healthier workforce.
3. Reducing Strains and Sprains from Manual Handling
Beyond MSDs, manual pipe handling is a major source of acute injuries like strains and sprains. These injuries often occur due to sudden, unexpected movements when lifting or losing grip on heavy or unwieldy pipes.
PVC pipe bagging machines are effective in reducing strains and sprains by providing controlled and stable handling of pipes. Automation minimizes the chances of sudden load shifts, dropped pipes, and uncontrolled movements that typically cause these acute injuries in manual bagging operations.
Let’s delve into the specific ways automated bagging systems mitigate these risks:
Enhanced Grip and Stability
Manual handling relies on human grip strength, which can be compromised by fatigue, sweat, or gloves. Machines utilize specialized grippers and clamps that provide a secure and consistent hold on pipes, preventing slippage and drops.
Controlled Movement and Placement
Automated systems move pipes smoothly and predictably, eliminating jerky or sudden motions that can cause strains. Precise robotic arms or conveyors ensure pipes are placed gently into bags, avoiding impacts and instability.
Elimination of Manual Lifting in Unstable Conditions
Manual bagging is sometimes performed in less-than-ideal conditions, such as uneven surfaces or cramped spaces, increasing the risk of slips and falls while carrying heavy pipes. Machines operate on fixed, stable platforms, removing the environmental instability factor from the handling process.
Consistent Load Management
Manual handling can lead to uneven weight distribution when carrying bundles of pipes, increasing the risk of losing balance and sustaining sprains. Automated systems ensure balanced and controlled load management throughout the bagging process, preventing sudden shifts in weight and potential imbalances.
Consider this comparison of injury scenarios:
Injury Type | Manual Handling Scenario | Automated System Scenario | Risk Reduction Mechanism |
---|---|---|---|
Back Strain | Lifting a heavy bundle of pipes incorrectly | Machine lifts and positions bundle | Elimination of manual heavy lifting |
Wrist Sprain | Twisting wrist while maneuvering a long pipe | Machine rotates and aligns pipes | Controlled, precise movements |
Shoulder Strain | Reaching awkwardly to place a pipe into a bag | Machine places pipe accurately | Optimized workflow and positioning |
Ankle Sprain | Stepping on uneven ground while carrying pipes | Machine operates on a stable, level surface | Stable operating environment |
Overall Strain/Sprain Risk | Significantly High due to varied and uncontrolled movements | Significantly Reduced due to precise and stable handling | Controlled and predictable operation |
By providing stable, controlled, and predictable handling, PVC pipe bagging machines drastically reduce the risk of strains and sprains, contributing to a safer workplace.
4. Creating Safer Working Environments
Beyond reducing specific types of injuries, PVC pipe bagging machines contribute to a generally safer working environment by streamlining processes and minimizing human exposure to hazards.
PVC pipe bagging machines contribute to safer workplaces by reducing clutter, improving workflow, and minimizing human interaction with heavy machinery. These machines create a more organized and controlled environment, decreasing the likelihood of accidents and promoting overall workplace safety.
Let’s examine the broader safety improvements facilitated by automation:
Reduced Workplace Clutter
Manual bagging areas can become cluttered with pipes, bags, and handling equipment, increasing trip and fall hazards. Automated systems streamline the process, reducing the amount of material and equipment scattered around the workspace, leading to a cleaner and more organized environment.
Improved Workflow and Ergonomics
Automated lines are designed for optimized workflow, minimizing bottlenecks and unnecessary movement. This structured environment reduces the chances of collisions between workers and equipment and creates clearer pathways, improving overall safety.
Minimized Human-Machine Interaction Hazards
In manual bagging, workers are in close proximity to heavy machinery like forklifts and cranes used to move pipe bundles. Automation reduces the need for such heavy equipment in the immediate bagging area, minimizing the risk of accidents involving human-machine interaction. PVC pipe bagging machines handle the bagging process within a contained system, separating workers from potentially hazardous operations.
Enhanced Operational Visibility
Automated systems often incorporate safety sensors and alarms that improve operational visibility. These systems can detect malfunctions or obstructions, alerting operators to potential hazards before they escalate into accidents.
Consider this comparison of workplace environments:
Feature | Manual Bagging Area | Automated Bagging Area | Safety Improvement |
---|---|---|---|
Clutter | High, pipes, bags, equipment scattered | Low, streamlined process, minimal loose materials | Reduced trip and fall hazards |
Workflow | Less organized, potential bottlenecks | Optimized, structured, efficient flow | Minimized collisions, clearer pathways |
Human-Machine Interaction | High, workers near forklifts and heavy equipment | Low, workers primarily monitor automated system | Reduced accidents involving heavy machinery |
Hazard Detection | Primarily visual, relies on human observation | Sensor-based, alarms for malfunctions, obstructions | Proactive hazard detection and prevention |
Overall Safety | Lower, due to clutter and human-machine proximity | Higher, due to organization and controlled environment | More controlled and predictably safer environment |
By creating a more organized, controlled, and predictable environment, PVC pipe bagging machines contribute significantly to overall workplace safety, going beyond just reducing specific injury types.
5. Regulatory Compliance and Cost Savings
Investing in PVC pipe bagging machines not only enhances worker safety but also helps companies comply with increasingly stringent safety regulations and realize long-term cost savings.
Implementing PVC pipe bagging machines aids in regulatory compliance by meeting or exceeding safety standards for material handling. Furthermore, the reduction in labor injuries translates to significant cost savings through decreased insurance premiums, fewer compensation claims, and improved workforce productivity.
Let’s examine these aspects in detail:
Meeting and Exceeding Safety Standards
Organizations like OSHA (Occupational Safety and Health Administration) and similar bodies worldwide are increasingly focused on workplace ergonomics and injury prevention. Automated bagging systems are designed to meet or exceed these standards by inherently reducing ergonomic risks and creating safer material handling processes. Compliance minimizes the risk of fines and legal liabilities associated with workplace safety violations.
Reduced Insurance Premiums and Compensation Claims
A demonstrable reduction in labor injuries directly impacts workers’ compensation insurance premiums. Fewer injuries translate to lower claim rates, leading to significant savings on insurance costs over time. A safer workplace also improves employee morale and reduces absenteeism, further contributing to cost efficiency.
Improved Productivity and Efficiency
While the primary focus is safety, automated bagging machines also boost productivity. Faster, more consistent bagging speeds up production cycles and increases throughput. Reduced injury-related downtime further enhances operational efficiency and output.
Long-Term Return on Investment
Although the initial investment in automation may seem substantial, the long-term benefits, including reduced injury costs, regulatory compliance, and increased productivity, deliver a strong return on investment. A safer, more efficient operation contributes to sustained profitability and long-term business success.
Consider this cost-benefit analysis:
Factor | Manual Bagging | Automated Bagging | Benefit of Automation |
---|---|---|---|
Injury Rate | High, frequent MSDs, strains, sprains | Low, significantly reduced injury incidence | Lower insurance premiums, reduced compensation costs |
Regulatory Compliance | May struggle to meet modern safety standards | Designed to meet or exceed safety regulations | Minimized risk of fines and legal liabilities |
Productivity | Lower, slower bagging speeds, potential downtime | Higher, faster, consistent, reduced downtime | Increased throughput, improved operational efficiency |
Long-Term Cost | Higher, due to injury costs, potential fines | Lower, reduced injury costs, increased efficiency | Stronger ROI, sustained profitability |
Overall Financial Impact | Higher operational costs, potential liabilities | Lower operational costs, improved financial outlook | Significant long-term cost savings and financial benefits |
By investing in PVC pipe bagging machines, companies not only prioritize worker safety but also make a sound financial decision that aligns with regulatory demands and contributes to long-term profitability.
6. Conclusion
PVC pipe bagging machines offer a compelling solution to reduce labor injuries in pipe manufacturing and handling. By automating strenuous and hazardous tasks, these systems directly address the root causes of MSDs, strains, sprains, and workplace accidents. The benefits extend beyond injury reduction, encompassing improved safety compliance, cost savings, and enhanced operational efficiency. Embracing automation in pipe bagging is a strategic move towards a safer, healthier, and more productive future for the industry.