What Are the Acid Resistance Requirements for Steel Coil Packing?
Steel coil packing is paramount in the metal industry, ensuring that coils arrive at their destination in pristine condition, free from corrosion and physical damage. Acidic environments pose a significant threat, necessitating robust packing solutions with specific resistance requirements. This article delves into the essential considerations for acid-resistant steel coil packing.
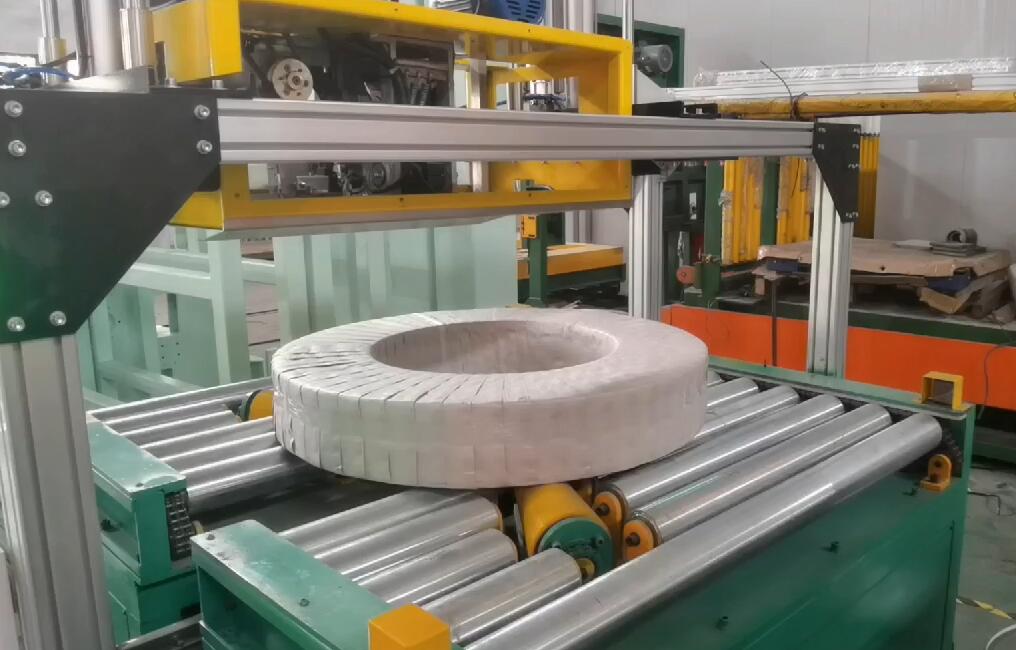
Acid resistance in steel coil packing refers to the ability of packing materials to withstand degradation or chemical reactions when exposed to acidic substances. The key requirements include material inertness to acids, barrier properties to prevent acid ingress, and durability to maintain integrity under acidic conditions, ensuring the steel coil remains protected from corrosion and environmental damage during storage and transport.
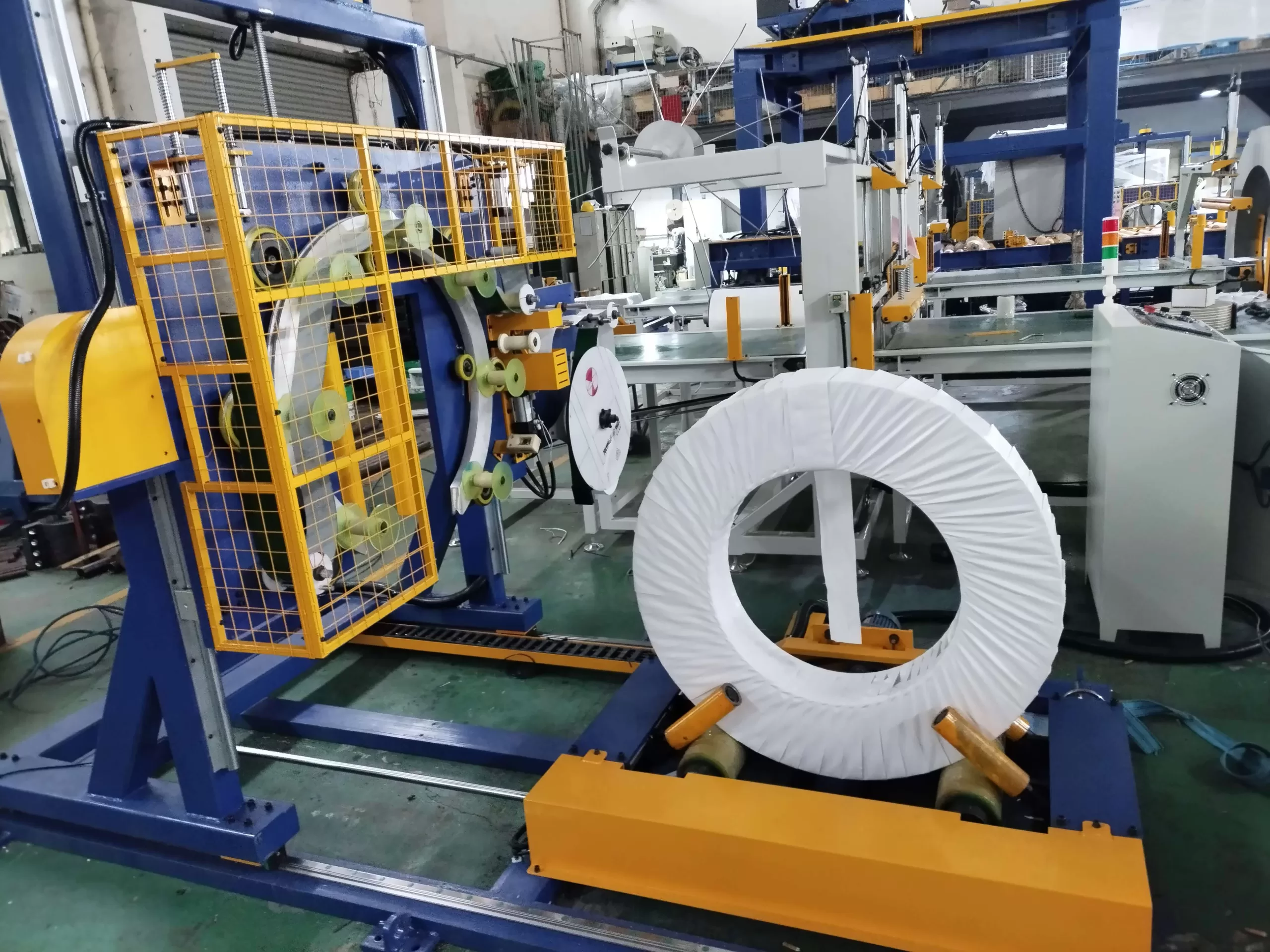
Understanding these requirements is crucial for selecting appropriate packing materials and methods that guarantee the longevity and quality of steel coils. Let’s explore the critical aspects of acid resistance in steel coil packing in more detail.
1. Understanding Acidic Corrosion in Steel Coils
Steel, while robust, is vulnerable to corrosion, especially in acidic environments. Acidic corrosion is an electrochemical process that deteriorates steel when exposed to acids, leading to rust, weakening of the material, and ultimately, product failure. Effective steel coil packing must counteract these corrosive effects.
To effectively combat acidic corrosion in steel coils, packing must act as a robust barrier, preventing direct contact with acidic substances and moisture. This involves selecting materials inherently resistant to acid degradation and designing packing methods that minimize exposure to corrosive elements throughout the supply chain.
Delving Deeper: The Mechanisms of Acidic Corrosion and Material Degradation
Acidic corrosion in steel is primarily driven by electrochemical reactions. When steel comes into contact with an acid, the acid acts as an electrolyte, facilitating the oxidation of iron (Fe) in the steel. This process can be simplified into the following steps:
- Ionization: Acids dissociate in water to form hydrogen ions (H+) and anions.
- Anodic Reaction (Oxidation): At the anode, iron atoms lose electrons and become iron ions (Fe2+ or Fe3+), going into solution. This is the corrosion reaction:
Fe → Fe2+ + 2e-
orFe → Fe3+ + 3e-
. - Cathodic Reaction (Reduction): Electrons released at the anode are consumed at the cathode. In acidic solutions, a common cathodic reaction is the reduction of hydrogen ions to hydrogen gas:
2H+ + 2e- → H2
. - Formation of Corrosion Products: Iron ions react with oxygen and water to form various corrosion products, commonly rust (hydrated iron oxides), which is porous and does not protect the underlying steel, thus allowing corrosion to proceed.
The rate of acidic corrosion is influenced by several factors:
- Acid Concentration and Strength (pH): Stronger acids and higher concentrations accelerate corrosion.
- Temperature: Increased temperature generally speeds up chemical reactions, including corrosion.
- Presence of Oxidizing Agents: Oxidizers can enhance the cathodic reaction, thereby increasing the corrosion rate.
- Exposure Time: Longer exposure to acidic environments leads to more significant corrosion.
- Type of Steel: Different steel alloys have varying degrees of acid resistance. For example, stainless steels with higher chromium and nickel content are more resistant than carbon steels.
Understanding these mechanisms is vital for selecting appropriate packing materials and designing effective packing strategies. Materials used in acid-resistant steel coil packing must be inert or highly resistant to the acids they are likely to encounter. Degradation of packing materials themselves can compromise the protection, leading to acid exposure and subsequent coil corrosion.
To illustrate the varying resistance of common packing materials, consider the following simplified comparison:
Material | Resistance to Strong Acids (e.g., HCl, H2SO4) | Resistance to Weak Acids (e.g., Acetic Acid) | Water Vapor Barrier | Chemical Inertness | Cost |
---|---|---|---|---|---|
Polyethylene (PE) | Poor to Fair | Good | Good | Good | Low |
Polypropylene (PP) | Fair | Good | Good | Good | Low to Med |
PVC (Polyvinyl Chloride) | Fair to Good | Good | Fair | Fair | Med |
PTFE (Teflon) | Excellent | Excellent | Excellent | Excellent | High |
Specialty Barrier Films | Good to Excellent | Excellent | Excellent | Excellent | Med to High |
This table provides a general overview. The specific acid resistance of a material depends on the exact chemical composition of the acid, its concentration, temperature, and exposure duration. Therefore, thorough material testing under anticipated conditions is crucial for selecting the optimal packing solution.
2. Key Material Properties for Acid Resistance
Selecting the right materials is the foundation of acid-resistant steel coil packing. Several key properties dictate a material’s suitability for protecting steel coils from acidic corrosion. These properties ensure the packing maintains its integrity and protective function throughout the coil’s journey.
The essential material properties for acid-resistant steel coil packing are chemical inertness, barrier effectiveness, mechanical strength, and temperature stability. Chemical inertness ensures the packing material itself does not react with acids. Barrier properties prevent acid penetration. Mechanical strength guarantees durability during handling and transport, and temperature stability maintains performance across varying environmental conditions.
Deep Dive into Material Characteristics
- Chemical Inertness/Resistance: This is the most critical property. The packing material must be chemically inert to the specific acids it is likely to encounter. This means it should not react with acids, dissolve, degrade, or become permeable upon acid exposure. Resistance should be considered for a range of acids and concentrations, including potential accidental spills or leaks during storage or transport. Testing standards like ASTM D543 (Standard Test Methods for Resistance of Plastics to Chemical Reagents) can be used to evaluate chemical resistance.
- Barrier Properties: The material must act as an effective barrier to prevent the ingress of acids and corrosive vapors. This includes low permeability to both liquid acids and acidic gases. Barrier properties also extend to moisture resistance, as moisture can exacerbate acidic corrosion. Materials with low water vapor transmission rates (WVTR) are preferred. Standards such as ASTM F1249 (Standard Test Method for Water Vapor Transmission Rate Through Plastic Film and Sheeting Using a Modulated Infrared Sensor) can quantify WVTR.
- Mechanical Strength and Durability: Packing materials must withstand the stresses of handling, storage, and transportation. This includes tear resistance, puncture resistance, and tensile strength. Acid exposure should not significantly compromise these mechanical properties. Materials should remain robust even after potential contact with acids to continue providing physical protection to the steel coil. Tests like ASTM D1004 (Tear Resistance) and ASTM D882 (Tensile Properties) are relevant.
- Temperature Stability: Steel coils may be stored and transported in a wide range of temperatures. The packing material must maintain its acid resistance and mechanical properties across this temperature spectrum. Extreme temperatures should not cause the material to become brittle, lose its barrier properties, or chemically degrade. Consideration should be given to both high and low temperature extremes relevant to the coil’s likely journey.
- Flexibility and Conformability: For coil packing, the material needs to be flexible enough to conform to the coil’s shape and allow for efficient wrapping and sealing. However, this flexibility should not compromise its strength or barrier properties.
- UV Resistance (if applicable): If coils are to be stored outdoors or exposed to sunlight during transport, UV resistance becomes important. UV degradation can weaken some plastics and reduce their chemical resistance over time. UV stabilizers may be required in the material formulation.
- Cost-Effectiveness: While performance is paramount, cost is always a consideration. The ideal material balances robust acid resistance with reasonable cost to ensure overall economic viability of the packing solution.
Selecting a material often involves trade-offs between these properties. For instance, PTFE offers excellent chemical resistance but is very expensive. Polyethylene is cost-effective and has good acid resistance to many weaker acids, but its resistance to strong acids may be limited. Specialty barrier films often provide a good balance of properties but come at a higher cost than standard plastics. Therefore, a careful evaluation of the specific application requirements and potential acid exposure is necessary to make the optimal material selection.
3. Types of Acid-Resistant Packing Materials
The market offers a range of materials suitable for acid-resistant steel coil packing, each with unique characteristics and levels of protection. Choosing the right type depends on the specific acidic environment, the required protection duration, and budget constraints. Understanding the pros and cons of each material type is crucial for informed decision-making.
Common acid-resistant packing materials include polyethylene (PE) films, polypropylene (PP) films, specialty barrier films (often laminates of different plastics and/or aluminum), and vapor corrosion inhibitors (VCIs) integrated into films or papers. PE and PP offer basic acid resistance for less aggressive environments, while barrier films provide enhanced protection against strong acids and harsh conditions. VCIs add an extra layer of corrosion prevention by releasing protective vapors.
Material Options and Their Performance Spectrum
Here’s a closer look at the common types of acid-resistant packing materials:
-
Polyethylene (PE) Films:
- Pros: Cost-effective, good resistance to many weak acids and alkalis, flexible, good water vapor barrier.
- Cons: Limited resistance to strong oxidizing acids and some organic solvents, lower temperature resistance compared to other plastics, can be permeable to some gases over time.
- Typical Applications: Mildly corrosive environments, protection against diluted acids, general-purpose wrapping for coils not exposed to highly aggressive chemicals.
- Variations: Low-density polyethylene (LDPE), high-density polyethylene (HDPE), linear low-density polyethylene (LLDPE) – each offering slightly different property profiles.
-
Polypropylene (PP) Films:
- Pros: Better chemical resistance than PE, especially to organic solvents and stronger acids (though still limited against highly oxidizing acids), higher tensile strength and temperature resistance than PE, good water vapor barrier.
- Cons: Can be susceptible to degradation by strong oxidizing agents, may become brittle at low temperatures.
- Typical Applications: More demanding chemical environments than PE, protection against a wider range of acids and solvents, suitable for coils requiring greater mechanical strength in the packing.
- Variations: Biaxially oriented polypropylene (BOPP) films offer enhanced strength and clarity.
-
Specialty Barrier Films (Laminates):
- Pros: Engineered for superior barrier properties against a wide spectrum of chemicals, including strong acids, solvents, and gases. Can be tailored to specific chemical resistance needs by combining different layers (e.g., PE for bulk, EVOH or polyamide for chemical barrier, aluminum foil for gas and moisture barrier). Excellent water vapor and gas barrier properties. Often offer improved mechanical strength and temperature resistance compared to single-layer films.
- Cons: More expensive than PE and PP films. Cost increases with the complexity of the laminate structure and the performance of barrier layers. Recyclability can be more complex depending on the laminate composition.
- Typical Applications: Highly corrosive environments, protection against concentrated acids, long-term storage in harsh conditions, export packing where coils are exposed to diverse climates and handling. Industries such as chemical processing, mining, and those near heavy industrial pollution often require these films.
- Examples: PE/EVOH/PE laminates, PE/Aluminum Foil/PE laminates, multi-layer films incorporating nylon or other high-barrier polymers.
-
Vapor Corrosion Inhibitor (VCI) Packaging:
- Pros: Provides active corrosion protection by releasing VCIs that form a protective molecular layer on the steel surface, inhibiting electrochemical corrosion reactions. Can be integrated into PE films, PP films, or papers. Offers protection even in areas not directly covered by the film, reaching into crevices and gaps. Reduces or eliminates the need for rust-preventative oils in some cases.
- Cons: Effectiveness depends on proper sealing of the VCI packaging to maintain VCI concentration. VCI type must be compatible with the type of steel being protected and the anticipated contaminants. May add cost compared to standard films. VCI protection is typically more effective against atmospheric corrosion and less so against direct immersion in strong acids, but can still provide a valuable additional layer of protection in acidic environments.
- Typical Applications: Used in conjunction with barrier films or as part of a comprehensive packing strategy in moderately to severely corrosive environments. Especially beneficial for long-term storage and shipment where preventing even minor corrosion is critical. Can be used with PE or PP films for enhanced corrosion protection at a moderate cost increase.
- Forms: VCI films, VCI papers, VCI emitters that can be placed inside packaging.
Choosing the optimal material involves a detailed assessment of the corrosive environment, budget, performance requirements, and sustainability considerations. Consulting with material suppliers and corrosion protection experts is recommended to select the most effective and cost-efficient acid-resistant packing solution for steel coils.
4. Best Practices for Acid-Resistant Steel Coil Packing
Beyond material selection, proper packing techniques are crucial to maximizing acid resistance and ensuring complete protection of steel coils. Even the best materials can fail if not applied correctly. Adhering to best practices in packing methodology is as important as material choice.
Effective acid-resistant steel coil packing involves thorough cleaning of the coil, multi-layer wrapping with acid-resistant materials, secure sealing to prevent acid ingress, proper handling to avoid damage to the packing, and clear labeling for identification and handling instructions. These practices minimize the risk of acid exposure and ensure the coil remains protected throughout its lifecycle.
Ensuring Robust Protection: A Step-by-Step Guide
-
Coil Cleaning and Preparation:
- Importance: Removing any existing contaminants (dirt, oils, fingerprints, processing residues) from the steel coil surface is the first crucial step. Contaminants can trap moisture and accelerate corrosion even if acid exposure is minimized.
- Methods: Cleaning methods depend on the coil’s condition. Options include:
- Solvent Cleaning: Using appropriate solvents to remove oils and grease. Ensure solvents are compatible with the steel and packing materials.
- Alkaline Cleaning: Using alkaline cleaners to remove residues. Rinsing thoroughly with clean water and drying is essential after alkaline cleaning.
- Steam Cleaning: Effective for removing loose dirt and debris. Coil must be completely dried afterward.
- Abrasive Cleaning (for heavily corroded coils): Wire brushing or light abrasive blasting to remove existing rust. This should be followed by a rust-inhibiting treatment if the coil is to be stored for an extended period before packing.
- Drying: After any wet cleaning process, coils must be thoroughly dried before packing. Residual moisture trapped under the packing can promote corrosion. Forced air drying or allowing coils to air dry in a controlled environment is recommended.
-
Multi-Layer Wrapping:
- Rationale: Multi-layer wrapping provides redundancy in protection. If the outer layer is breached, inner layers still maintain a barrier against acid ingress.
- Layer Sequence (Example):
- Inner Layer (VCI Film or Paper): Directly contacting the steel coil. Provides active corrosion inhibition.
- Intermediate Layer (Barrier Film): Primary barrier against acid and moisture penetration. Choose a film with appropriate chemical resistance and barrier properties based on the anticipated acidic environment.
- Outer Layer (Heavy-Duty PE or PP Film): Provides mechanical protection against tears, punctures, and abrasion during handling and transport. Can also offer additional UV protection if required.
- Overlap and Securement: Ensure sufficient overlap of wrapping layers (e.g., 50% overlap) to create a continuous barrier. Secure each layer tightly with acid-resistant tape or banding to prevent shifting and gaps.
-
Sealing and Closure:
- Importance: Proper sealing is critical to prevent acids and corrosive vapors from entering the packed coil. Weak seals are a common point of failure.
- Methods:
- Heat Sealing: For thermoplastic films (PE, PP, barrier films), heat sealing provides the most reliable and airtight closure. Ensure proper heat sealing parameters (temperature, pressure, dwell time) are used for the specific film type and thickness.
- Taping: Acid-resistant tapes (e.g., acrylic or silicone adhesive tapes) can be used to seal overlaps and edges. Ensure the tape is compatible with the packing film and provides a strong, durable seal. Overlap tape generously.
- Banding: For heavy coils, banding (steel or plastic) provides structural integrity to the packing and helps maintain seal pressure. Apply banding over the wrapped coil to compress the layers and enhance sealing.
-
Handling and Storage:
- Careful Handling: Train personnel on proper handling techniques to avoid damaging the packing during loading, unloading, and storage. Use appropriate lifting equipment and avoid dragging or dropping packed coils.
- Storage Conditions: Store packed coils in a clean, dry environment, away from direct sunlight and extreme temperature fluctuations if possible. Elevated storage (e.g., on pallets) can prevent contact with floor moisture. For long-term storage in potentially corrosive environments, consider indoor storage in a controlled environment.
-
Labeling and Identification:
- Clear Labeling: Clearly label each packed coil with product identification, packing date, any special handling instructions, and warnings if the coil is particularly sensitive to specific chemicals or conditions. Include information about the type of acid-resistant packing used.
- Color-Coding: Consider using color-coded labels or packing materials to visually differentiate coils with acid-resistant packing from standard packed coils.
By meticulously following these best practices, manufacturers and suppliers can significantly enhance the acid resistance of steel coil packing and ensure their products arrive at the customer in optimal condition, free from corrosion damage. Regular training of packing personnel and quality control checks of the packing process are essential to maintain consistently high standards of acid protection.
Conclusion
Acid resistance is a critical requirement for steel coil packing, particularly in industries and regions where coils are exposed to corrosive environments. Selecting appropriate materials with inherent chemical inertness, robust barrier properties, and sufficient mechanical strength is paramount. Combining the right materials with best-practice packing techniques, including thorough cleaning, multi-layer wrapping, secure sealing, and careful handling, ensures comprehensive protection against acidic corrosion. By prioritizing acid resistance in coil packing, businesses can safeguard the quality and longevity of their steel products, minimize losses due to corrosion damage, and maintain customer satisfaction. Investing in effective acid-resistant packing is an investment in product integrity and long-term business success.