Static electricity can pose significant challenges during the packaging of steel wire, potentially leading to safety hazards and operational inefficiencies. Implementing effective anti-static measures is crucial to mitigate these risks and ensure a smooth, safe packing process.
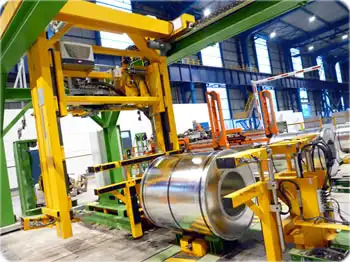
Anti-static measures in steel wire packing primarily involve grounding equipment and using anti-static materials. Grounding ensures static charges are safely dissipated, preventing buildup. Anti-static materials, such as conductive packaging and coatings, minimize charge generation and accumulation during handling and wrapping processes. These measures collectively create a safer and more efficient packing environment.
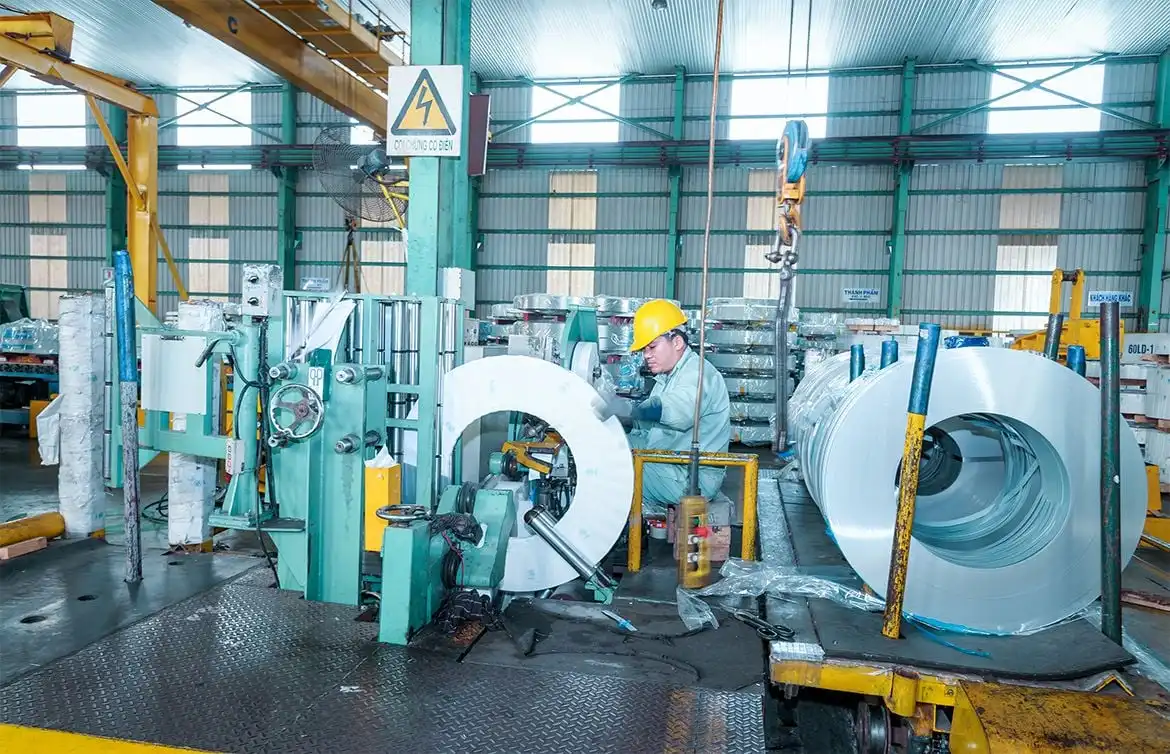
To fully understand the importance and application of these measures, let’s delve deeper into the specific anti-static techniques employed in steel wire packing and explore how they contribute to a safer and more productive operation.
2. Understanding Electrostatic Discharge (ESD) in Steel Wire Packing
In the context of steel wire packing, electrostatic discharge (ESD) refers to the sudden release of static electricity that can accumulate during the handling and wrapping of steel wire coils. This phenomenon is not merely a nuisance; it can have serious implications for both safety and operational efficiency.
ESD in steel wire packing arises primarily from the triboelectric effect, where contact and separation between dissimilar materials – such as steel wire and packaging materials – lead to charge transfer. This charge buildup can result in sudden discharges, posing risks to equipment and personnel. Effective ESD control is therefore essential to prevent damage and ensure a safe working environment.

2.1. The Dangers of Uncontrolled ESD in Wire Packing
Uncontrolled ESD in steel wire packing can lead to a range of problems, from minor inconveniences to significant safety hazards and operational disruptions. Understanding these dangers is the first step in appreciating the importance of implementing robust anti-static measures.
2.1.1. Safety Hazards
The most immediate concern with ESD is the risk of electric shock to personnel. While static discharges from handling steel wire may not always be lethal, they can be painful and startling, potentially leading to secondary accidents. In environments where flammable materials are present, ESD sparks can even pose a fire or explosion risk.
2.1.2. Operational Inefficiencies
ESD can also negatively impact the efficiency of the packing process. Static charges can cause steel wire coils to attract dust and debris, leading to contamination and requiring additional cleaning steps. Furthermore, static can make handling and wrapping materials more difficult, slowing down the packing line and increasing the risk of material waste.
2.1.3. Equipment Damage
While steel itself is robust, the equipment used in wire packing, particularly automated machinery and electronic controls, can be susceptible to ESD damage. Repeated ESD events can degrade sensitive components over time, leading to premature failures and costly downtime for repairs or replacements.
2.1.4. Comparing ESD Risks Across Different Wire Types
The level of ESD risk can vary depending on the type of steel wire being packed and the specific packing process. Thinner wires, for example, may generate less static due to smaller surface area contact, but may be more easily affected by static cling. Similarly, different wire packing machine and packaging materials will have varying triboelectric properties, influencing the overall ESD potential.
To better illustrate these differences, consider the table below:
Wire Type | Packing Material | ESD Risk Level | Contributing Factors | Mitigation Focus |
---|---|---|---|---|
Thick Steel Cable | Plastic Film | High | Large surface area, high friction, insulating material | Robust grounding, anti-static film, ionization |
Thin Steel Wire | Paper Wrap | Medium | Moderate friction, paper less insulating than plastic | Grounding, dissipative paper, humidity control |
Stainless Steel | Conductive Wrap | Low | Stainless steel less triboelectric, conductive wrap | Basic grounding verification, minimal additional measures |
This table highlights that a comprehensive ESD control strategy must be tailored to the specific materials and processes involved in steel wire packing. A one-size-fits-all approach is unlikely to be effective in mitigating all ESD risks.
3. Core Anti-Static Measures in Steel Wire Packing
To effectively combat ESD in steel wire packing, a multi-faceted approach is required. This involves implementing several core anti-static measures that work in concert to minimize charge generation, dissipate existing charges, and protect both personnel and equipment.
The primary anti-static measures include grounding, utilizing anti-static materials, humidity control, and ionization. Grounding provides a safe path for static charges to dissipate. Anti-static materials reduce charge buildup. Humidity control and ionization further minimize static by increasing air conductivity and neutralizing charges, respectively. These measures, when properly implemented, create a comprehensive ESD-safe packing environment.
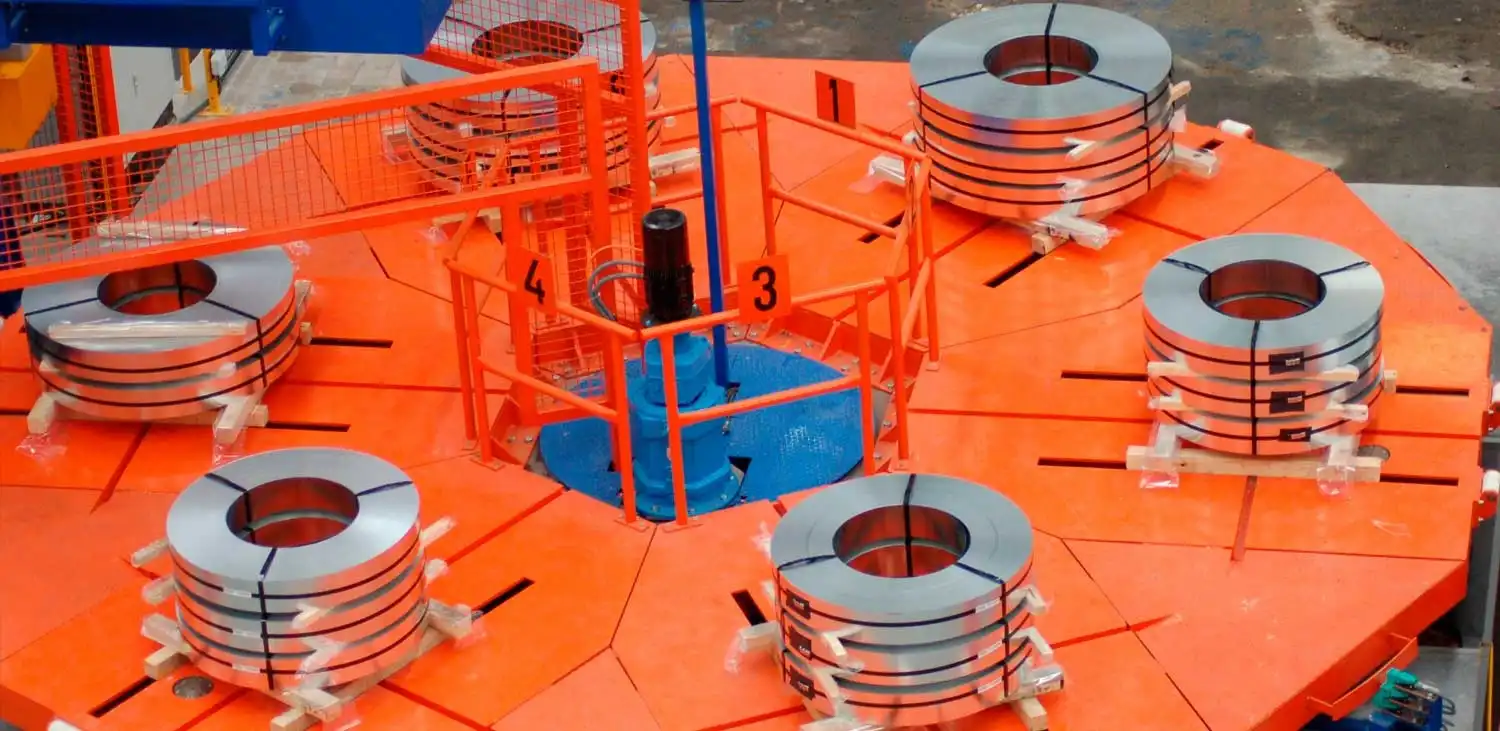
3.1. Grounding Techniques for Steel Wire Packing Equipment
Grounding is the cornerstone of any ESD control program. In steel wire packing, this involves creating a conductive pathway from equipment and materials to the earth, allowing static charges to safely dissipate rather than accumulate.
3.1.1. Equipment Grounding
All conductive components of the packing line, including the wire coil wrapping machine, conveyors, and any metal framework, should be properly grounded. This is typically achieved by connecting these components to a verified grounding point, often the facility’s electrical grounding system. Regular checks are crucial to ensure grounding connections remain secure and effective.
3.1.2. Personnel Grounding
Operators working in the packing area are also potential sources of static charge. Personnel grounding is essential, often achieved through the use of wrist straps and conductive footwear. Wrist straps, when properly worn and connected to a ground point, continuously drain static charges from the body. Conductive footwear, used in conjunction with ESD-protective flooring, provides another pathway for charge dissipation.
3.1.3. Material Grounding (Where Applicable)
While steel wire is conductive and grounding the equipment handles much of the charge, packaging materials, if conductive or dissipative, can also be grounded. For example, if using conductive wrapping films, ensuring these films are in contact with grounded equipment during application can aid in charge dissipation.
3.2. Anti-Static Materials in Wire Packing
Beyond grounding, the choice of materials plays a significant role in ESD control. Utilizing anti-static materials throughout the packing process can drastically reduce charge generation and accumulation.
3.2.1. Anti-Static Packaging Films and Wraps
Traditional plastic films are notorious for generating static. Anti-static packaging films, treated or formulated to be dissipative or conductive, are crucial for wire packing. These films minimize charge buildup during wrapping and handling, reducing the risk of ESD events.
3.2.2. Conductive or Dissipative Coatings
Applying conductive or dissipative coatings to rollers, guides, and other machine components that come into contact with the steel wire can further reduce triboelectric charging. These coatings prevent charge separation by allowing charges to spread more evenly across surfaces.
3.2.3. Anti-Static Strapping and Tapes
Even seemingly minor components like strapping and tapes used to secure wire coils should be anti-static. Standard tapes and straps can generate considerable static when unwound or applied. Anti-static alternatives are readily available and should be standard practice in ESD-sensitive packing areas.
3.3. Humidity Control and Ionization
In addition to grounding and materials, environmental controls can further enhance ESD protection. Humidity control and ionization are two key techniques that can significantly reduce static buildup.
3.3.1. Humidity Control
Static charge generation is exacerbated in dry environments. Maintaining a relative humidity of 40% to 60% in the packing area can significantly reduce static buildup. Humidifiers can be used to achieve and maintain these levels, particularly in drier climates or during winter months.
3.3.2. Ionization
Ionizers are devices that generate balanced ions in the air, neutralizing static charges on non-conductive materials or isolated conductors that cannot be grounded. In wire packing, ionizers can be particularly useful for neutralizing charges on packaging materials or the wire itself before wrapping, providing an extra layer of ESD protection.
4. Implementing and Maintaining Anti-Static Measures
Implementing anti-static measures is not a one-time task but an ongoing process that requires careful planning, consistent execution, and regular monitoring. A successful ESD control program in steel wire packing necessitates a systematic approach.
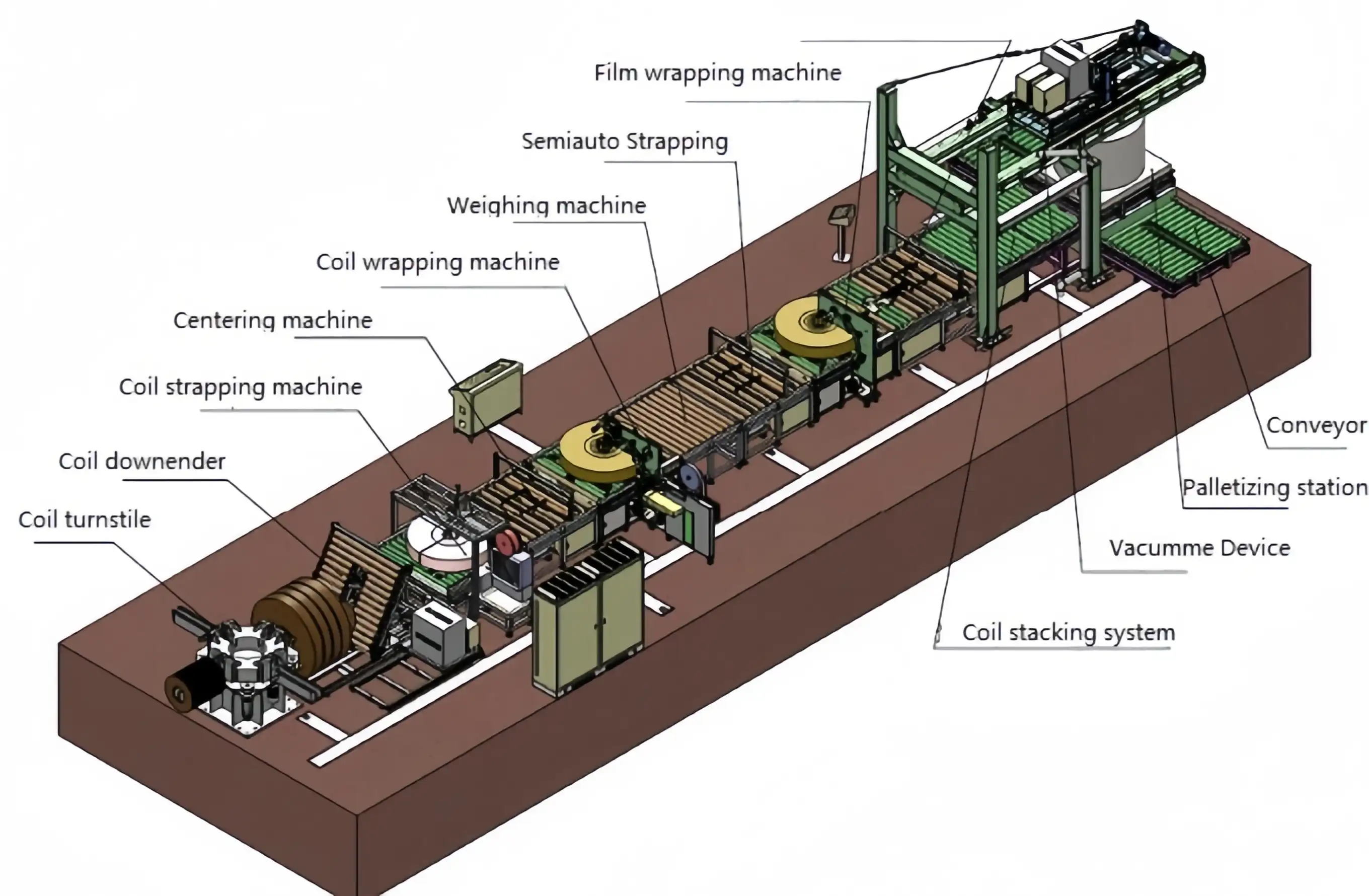
Effective implementation starts with a comprehensive ESD control plan, encompassing grounding verification, material selection, and regular audits. Maintenance involves routine checks of grounding connections, anti-static material integrity, and environmental controls. Training personnel on ESD awareness and proper handling procedures is equally critical for sustained effectiveness. This holistic approach ensures long-term ESD protection and a consistently safe and efficient packing operation.
4.1. Developing an ESD Control Plan
A written ESD control plan is essential for outlining the specific measures to be implemented and maintained in the steel wire packing area. This plan should detail:
- ESD Protected Area (EPA) Definition: Clearly define the boundaries of the EPA where ESD control measures are required.
- Grounding Procedures: Specify grounding methods for equipment, personnel, and materials, including testing frequencies and acceptable resistance levels.
- Material Specifications: List approved anti-static materials for packaging, coatings, and other consumables.
- Training Program: Outline the ESD awareness and handling training for all personnel working in the EPA.
- Compliance Verification: Detail procedures for regular audits and inspections to ensure ongoing compliance with the ESD control plan.
4.2. Regular Audits and Verification
The effectiveness of anti-static measures must be regularly verified through audits and inspections. This includes:
- Grounding Point Checks: Regularly test grounding connections for continuity and resistance to ensure they meet established standards.
- Material Inspections: Verify that only approved anti-static materials are being used and inspect them for damage or degradation.
- Personnel Compliance Audits: Observe personnel to ensure they are following ESD control procedures, such as wearing wrist straps correctly.
- Environmental Monitoring: Regularly monitor humidity levels in the EPA and ensure ionizers are functioning correctly.
4.3. Employee Training and Awareness
Even the best ESD control plan will fail if personnel are not properly trained and aware of ESD risks and control procedures. Comprehensive training should cover:
- Basic ESD Principles: Explain what static electricity is, how it is generated, and why it is a concern in wire packing.
- ESD Control Measures: Detail all anti-static measures in place, including grounding procedures, material usage, and environmental controls.
- Proper Handling Procedures: Train personnel on how to handle steel wire and packaging materials in an ESD-safe manner.
- Importance of Compliance: Emphasize the importance of following ESD control procedures to protect themselves, equipment, and product quality.
5. Conclusion
Implementing robust anti-static measures in steel wire packing is not merely about adhering to safety guidelines; it is a strategic investment in operational efficiency, product quality, and workplace safety. By understanding the risks of ESD and adopting a comprehensive approach encompassing grounding, anti-static materials, environmental controls, and rigorous training, steel wire manufacturers can create a safer, more productive, and more reliable packing process. This proactive approach minimizes potential hazards, reduces operational disruptions, and ultimately contributes to a more successful and sustainable business.