What Anti-Static Measures Are Used in Steel Coil Packing?
Static electricity can be a significant and often underestimated challenge in various industrial processes, including the packing of steel coils. The generation and discharge of static can lead to safety risks and operational inefficiencies. Therefore, implementing effective anti-static measures is crucial in this sector.
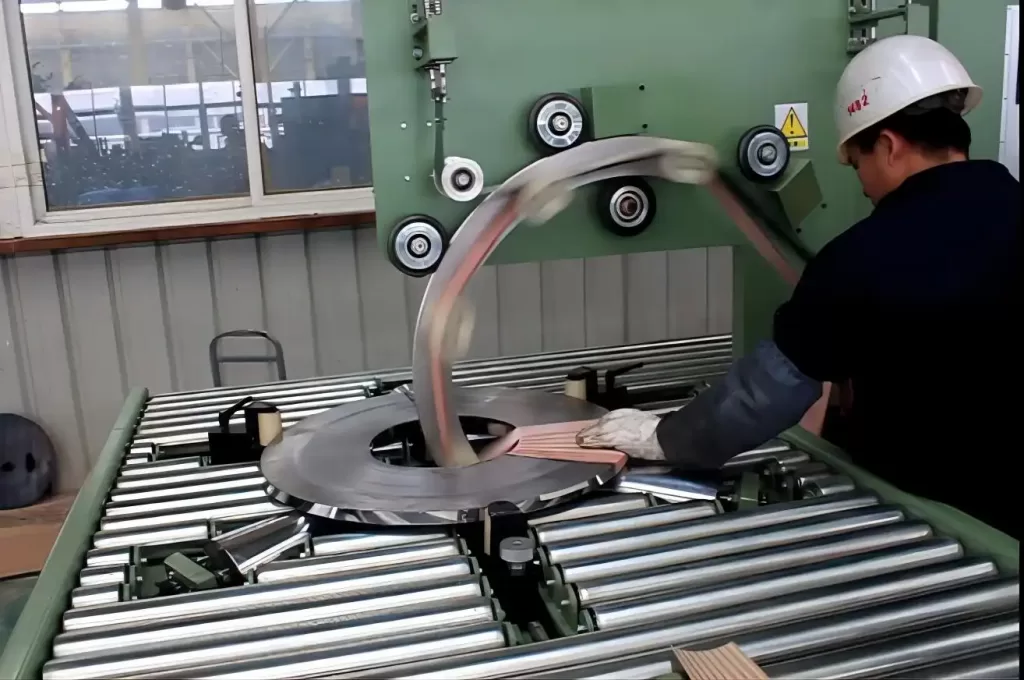
Anti-static measures in steel coil packing primarily involve grounding all conductive equipment, utilizing anti-static packaging materials, controlling humidity levels, and in some cases, employing ionization systems. Grounding dissipates static charges safely, while anti-static materials minimize charge accumulation. Humidity control and ionization further reduce static by altering air conductivity and neutralizing charges.

To fully appreciate the importance and application of these measures, it’s essential to delve into the specific techniques used to combat static electricity in steel coil packing. Understanding these methods will reveal how they contribute to a safer and more productive operation. Let’s explore the core anti-static strategies employed in this industry.
1. Understanding Electrostatic Discharge (ESD) in Steel Coil Packing
Electrostatic discharge (ESD) in steel coil packing refers to the sudden release of static electricity that accumulates during the handling and wrapping of steel coils. This phenomenon is not merely a nuisance; it presents tangible risks to safety and operational efficiency within packing facilities.
In steel coil packing, ESD primarily originates from the triboelectric effect, which occurs when dissimilar materials like steel and packaging films come into contact and then separate. This interaction leads to charge transfer and buildup. Uncontrolled ESD can result in electric shocks to personnel, attract contaminants to the steel coils, damage sensitive equipment, and even pose a fire hazard in certain environments. Implementing robust anti-static measures is therefore crucial for mitigating these risks and ensuring a safe and efficient packing process.
1.1. The Critical Dangers of Uncontrolled ESD in Wire Packing
Uncontrolled electrostatic discharge (ESD) in steel wire packing can trigger a cascade of problems, ranging from minor annoyances to serious safety hazards and disruptions in operations. Recognizing these dangers is the first step in understanding why implementing strong anti-static measures is so vital.
1.1.1. Safety Risks to Personnel
The most immediate and critical concern with ESD is the potential risk of electric shock to personnel. While discharges from handling steel wire are unlikely to be lethal, they can be painful and startling. These shocks can lead to involuntary reactions, increasing the risk of secondary accidents, such as dropping heavy coils or falls from platforms. In environments where flammable materials like certain lubricants or packaging components are present, ESD sparks pose a significant fire or explosion hazard. Ensuring worker safety is paramount, making ESD control a critical element of workplace safety protocols.
1.1.2. Impact on Operational Efficiency
ESD can significantly hamper the efficiency of the steel coil packing process. Static charges act like magnets, attracting dust, dirt, and other airborne contaminants to the surface of the steel coils. This contamination necessitates additional cleaning steps before packing or shipping, adding time and labor costs. Furthermore, static cling can make handling and applying packaging materials, such as plastic films or wraps, considerably more difficult. Materials may stick to themselves or the coils unevenly, leading to material waste, rework, and slowdowns on the packing line. These inefficiencies directly impact productivity and increase operational costs.
1.1.3. Potential for Equipment Damage
While steel itself is robust and not susceptible to ESD damage, the sophisticated equipment used in modern wire packing facilities is often vulnerable. Automated machinery, including electronic sensors, control systems, and robotic arms, are integral to efficient packing lines. These components contain sensitive electronics that can be damaged or degraded by repeated ESD events. Latent damage, where equipment continues to function but with reduced lifespan or reliability, is a particularly insidious problem. Over time, ESD-induced equipment failures lead to unexpected downtime for repairs or replacements, resulting in production losses and increased maintenance expenses. Protecting these assets from ESD is crucial for maintaining operational continuity and minimizing long-term costs.
1.1.4. Varied ESD Risks Across Different Steel Types and Packing
The level of ESD risk is not uniform across all steel wire packing scenarios; it varies significantly depending on the type of steel wire being processed and the specific packing methodologies employed. Thinner gauge wires, while having less surface area for charge accumulation, can be more susceptible to static cling, making them harder to handle and wrap neatly. Conversely, thicker cables, with their larger surface areas and greater contact during handling, may generate higher static charges.
The choice of coil packing machine and packaging materials also plays a critical role. Different materials possess varying triboelectric properties, influencing the propensity for charge generation during contact and separation. For instance, plastic films, widely used for their cost-effectiveness and protective qualities, are known for high static generation. In contrast, paper-based wraps, while potentially less durable, may exhibit lower static buildup.
To illustrate these variations, consider the following table that compares ESD risk levels for different combinations of wire types and packing materials:
Wire Type | Packing Material | ESD Risk Level | Contributing Factors | Mitigation Focus |
---|---|---|---|---|
Thick Steel Cable | Plastic Film | High | Large surface area, high friction, insulating material | Robust grounding, anti-static film, ionization |
Thin Steel Wire | Paper Wrap | Medium | Moderate friction, paper less insulating than plastic | Grounding, dissipative paper, humidity control |
Stainless Steel | Conductive Wrap | Low | Stainless steel less triboelectric, conductive wrap | Basic grounding verification, minimal additional measures |
Coated Steel Wire | Standard Plastic | High | Coating surface properties, plastic film insulation | Anti-static coatings, grounding, ionization |
Galvanized Steel | Anti-static Film | Medium | Galvanized surface may reduce friction, anti-static film | Grounding, anti-static film verification |
This table underscores the necessity for a customized ESD control strategy tailored to the specific materials and processes in use. A generic, one-size-fits-all approach is unlikely to effectively address the diverse ESD risks encountered in steel wire packing. A comprehensive strategy must consider the nuances of wire type, packing material, and operational environment to ensure optimal ESD protection and process efficiency.
2. Core Anti-Static Measures in Steel Wire Packing
Effectively managing ESD in steel coil packing demands a comprehensive, multi-layered approach. This involves implementing a suite of core anti-static measures that synergistically work to minimize charge generation, safely dissipate existing charges, and provide robust protection for both personnel and sensitive equipment.
The primary anti-static measures deployed in steel coil packing encompass several key strategies: grounding of equipment and personnel, the strategic use of anti-static materials in packaging and machine components, precise humidity control within the packing environment, and the deployment of ionization systems to neutralize static charges. Grounding establishes safe pathways for static charges to dissipate. Anti-static materials inherently reduce charge buildup. Humidity control enhances air conductivity, diminishing static accumulation, and ionization actively neutralizes charges, particularly on non-conductive surfaces. When meticulously implemented and maintained, these measures collectively create a comprehensive ESD-safe packing environment, minimizing risks and optimizing operational efficiency.
2.1. Grounding Techniques for Steel Wire Packing Equipment
Grounding is the foundational element of any effective ESD control program. In the context of steel wire packing, grounding involves creating reliable conductive pathways that safely channel static charges from equipment and materials to the earth. This prevents the accumulation of static electricity, which is the root cause of ESD events.
2.1.1. Equipment Grounding Protocols
Comprehensive equipment grounding is paramount in steel wire packing facilities. All conductive components of the packing line must be systematically grounded. This includes the steel coil wrapping machine itself, conveyor systems, any metallic framework supporting the machinery, and control panels. Grounding is typically achieved by securely connecting these components to a verified grounding point, often the facility’s main electrical grounding system. These connections must be robust and regularly inspected to ensure they remain secure and effective over time. Regular checks, such as continuity testing and resistance measurements, are crucial to verify the integrity of grounding connections and confirm that they meet established standards. Improper or degraded grounding can render other anti-static measures less effective, highlighting the critical importance of a well-maintained grounding infrastructure.
2.1.2. Personnel Grounding Strategies
Operators working in steel wire packing areas are significant potential sources of static charge generation. Human movement, particularly friction between clothing and surfaces, can readily generate static electricity. Personnel grounding is therefore an indispensable aspect of ESD control. The most common methods for personnel grounding include the use of wrist straps and conductive footwear. Wrist straps, when correctly worn snugly against the skin and connected to a designated ground point, continuously dissipate static charges accumulating on the body. Conductive footwear, used in conjunction with ESD-protective flooring, provides an alternative or supplementary pathway for charge dissipation, especially for personnel who are mobile or standing. The effectiveness of personnel grounding devices relies on proper usage and maintenance. Regular training and compliance checks are necessary to ensure that wrist straps are worn correctly and that conductive footwear is in good condition and compatible with the flooring.
2.1.3. Material Grounding Considerations
While steel wire itself is conductive, and grounding the equipment effectively addresses much of the static charge concern, packaging materials also warrant consideration for grounding, especially if they are conductive or dissipative. For instance, if conductive wrapping films or tapes are used, ensuring these materials are in continuous contact with grounded equipment during the application process can significantly enhance charge dissipation. This approach prevents charge buildup on the packaging materials themselves, further reducing the overall ESD risk. The specific grounding method for materials will depend on their nature and how they are integrated into the packing process, but the principle of providing a path to ground remains consistent.
2.2. Anti-Static Materials in Wire Packing
Beyond grounding, the strategic selection and implementation of anti-static materials constitute a crucial layer of defense against ESD in steel wire packing. Utilizing these specialized materials throughout the packing process can dramatically reduce the generation and accumulation of static charges at their source.
2.2.1. Anti-Static Packaging Films and Wraps
Traditional plastic films and wraps, widely used in packaging due to their cost-effectiveness and protective qualities, are notorious for their high propensity to generate static electricity. As steel coils are wrapped and handled, the friction between standard plastic films and the steel surface can lead to significant charge buildup. To counteract this, anti-static packaging films and wraps are essential. These specialized films are either treated with anti-static agents or formulated from inherently dissipative or conductive polymers. These properties minimize charge generation during the wrapping and handling processes, significantly reducing the risk of ESD events. The choice of anti-static film should be based on the specific requirements of the steel wire being packed, considering factors like gauge, coating, and sensitivity to surface contamination.
2.2.2. Conductive or Dissipative Coatings for Equipment
Applying conductive or dissipative coatings to machine components that come into direct or frequent contact with the steel wire represents another effective strategy for reducing triboelectric charging. This includes rollers, guides, tensioning devices, and any other parts of the coil packing machine that interact with the wire during processing. These specialized coatings, formulated with conductive or dissipative materials, prevent or minimize charge separation by facilitating the even distribution of charges across surfaces. By reducing the localized buildup of charge, these coatings contribute to a lower overall ESD potential in the packing environment. The coatings must be durable and compatible with the operating conditions, including potential abrasion and chemical exposure.
2.2.3. Anti-Static Strapping and Tapes
Even seemingly minor components like strapping and tapes, used to secure steel coils after wrapping, can contribute to ESD if they are not carefully selected. Standard tapes and strapping materials, particularly plastic-based ones, can generate considerable static charge when unwound from rolls or applied under tension. To mitigate this often-overlooked source of static, anti-static strapping and tapes should be employed in ESD-sensitive packing areas. These alternatives are treated to reduce their charge generation potential and are readily available in various widths and strengths to match different packing requirements. Switching to anti-static versions of these consumables is a simple yet effective measure to enhance overall ESD control.
2.3. Humidity Control and Ionization Techniques
In addition to grounding and the strategic use of anti-static materials, environmental controls play a crucial role in enhancing ESD protection in steel wire packing facilities. Humidity control and ionization are two key techniques that can significantly reduce static buildup by modifying the environment itself.
2.3.1. Precise Humidity Control Management
The generation and accumulation of static charge are significantly exacerbated in dry environments. Low humidity reduces the natural conductivity of air, allowing static charges to persist for longer durations and build up to higher potentials. Maintaining a relative humidity level within the range of 40% to 60% in the steel wire packing area can substantially reduce static buildup. This level of humidity increases the moisture content in the air, making it more conductive and facilitating the dissipation of static charges. Industrial humidifiers can be effectively used to achieve and consistently maintain these optimal humidity levels, particularly in drier climates or during winter months when indoor humidity tends to drop. Regular monitoring of humidity levels is essential to ensure the system is functioning correctly and providing consistent ESD protection.
2.3.2. Strategic Ionization Deployment
Ionizers are sophisticated devices designed to generate a balanced stream of positive and negative ions in the air. These ions actively neutralize static charges present on non-conductive materials or isolated conductors that cannot be effectively grounded. In steel wire packing, ionizers can be particularly beneficial for neutralizing charges on packaging materials, such as plastic films, or even on the surface of the steel wire itself before wrapping. By reducing the surface charge on these materials, ionization provides an extra layer of ESD protection, particularly in areas where grounding or material changes alone may not be sufficient. Ionizers can be strategically placed overhead or at workstations to provide targeted charge neutralization. Regular maintenance and testing of ionizers are crucial to ensure they are operating within their specified performance parameters and effectively neutralizing static charges.
3. Implementing and Maintaining Anti-Static Measures
Implementing anti-static measures in steel wire packing is not a one-time setup but an ongoing process. It requires meticulous planning, consistent execution, and diligent regular monitoring to ensure sustained effectiveness. A successful ESD control program in this environment necessitates a systematic approach encompassing planning, verification, and continuous improvement.
Effective implementation of anti-static measures begins with the development of a comprehensive, written ESD control plan. This plan should meticulously detail grounding procedures, specify approved anti-static materials, and outline regular audit protocols. Maintenance is equally critical, involving routine checks of grounding connections, verification of anti-static material integrity, and monitoring of environmental control systems like humidity and ionization. Crucially, training personnel on ESD awareness and proper handling procedures is essential for the program’s long-term success. This holistic approach, encompassing planning, maintenance, and training, ensures continuous ESD protection, creating a consistently safe and efficient steel coil packing operation.
3.1. Developing a Robust ESD Control Plan
A well-documented ESD control plan serves as the blueprint for all anti-static activities within the steel wire packing facility. This plan should be a comprehensive document outlining specific procedures, responsibilities, and verification methods. Key elements of an effective ESD control plan include:
3.1.1. ESD Protected Area (EPA) Definition
Clearly defining the boundaries of the ESD Protected Area (EPA) is the first step. The EPA is the designated space where stringent ESD control measures are implemented and enforced. The plan must explicitly specify the physical limits of the EPA, whether it’s an entire packing line, a specific section, or individual workstations. Clear demarcation using floor markings, signage, and physical barriers helps ensure that all personnel are aware when they are entering or working within an EPA and must adhere to ESD control protocols.
3.1.2. Detailed Grounding Procedures
The ESD control plan must include detailed procedures for grounding all equipment, personnel, and applicable materials within the EPA. This section should specify the methods for grounding different types of equipment, the types of grounding hardware to be used, and the designated grounding points. Crucially, the plan must define the frequency of grounding system testing, the test methods to be employed (e.g., continuity testing, resistance measurements), and the acceptable resistance levels for grounding connections. Regular testing and record-keeping are essential to demonstrate ongoing compliance and identify any degradation in grounding effectiveness.
3.1.3. Material Specifications and Approvals
The plan should include a comprehensive list of all approved anti-static materials to be used within the EPA. This encompasses packaging films, wraps, tapes, coatings, and any other consumables that come into contact with steel wire or sensitive equipment. For each material, the plan should specify the required anti-static properties (e.g., dissipative, conductive), relevant material standards, and approved suppliers. A process for verifying the conformity of incoming materials to these specifications should also be outlined, ensuring that only compliant materials are used in the packing process.
3.1.4. Comprehensive Training Program Outline
Employee training is the cornerstone of a successful ESD control program. The plan must detail a comprehensive training program for all personnel working within the EPA. The training curriculum should cover fundamental ESD principles, the specific ESD control measures in place within the facility, proper handling procedures for steel wire and packaging materials, and the correct use of personal grounding equipment like wrist straps and conductive footwear. The plan should specify the frequency of training, methods for verifying employee understanding, and procedures for refresher training to maintain ongoing awareness and compliance.
3.1.5. Compliance Verification and Auditing Protocols
To ensure the ESD control plan is effectively implemented and consistently followed, the plan must define procedures for regular compliance verification and audits. This section should detail the frequency of audits, the scope of audits (e.g., grounding system checks, material inspections, personnel compliance observations), and the responsible personnel for conducting audits. The plan should also outline the process for documenting audit findings, identifying corrective actions for any non-compliance issues, and tracking the implementation of these actions. Regular audits provide valuable feedback on the effectiveness of the ESD control program and identify areas for improvement.
3.2. Regular Audits and Verification Processes
The effectiveness of implemented anti-static measures cannot be assumed; it must be regularly verified through systematic audits and inspections. These verification activities ensure that the ESD control program is functioning as intended and identify any areas where performance may have degraded or drifted from established standards. Key aspects of regular audits and verification include:
3.2.1. Grounding Point Integrity Checks
Regularly testing grounding connections is paramount to ensure their continued effectiveness. Audits should include routine checks of all grounding points for continuity and resistance. Continuity testing verifies that a complete conductive pathway to ground exists, while resistance measurements confirm that the resistance is within acceptable limits as defined in the ESD control plan and relevant standards (e.g., ANSI/ESD S20.20). Testing should be performed using calibrated instruments, and records of test results should be meticulously maintained. Any grounding connections found to be faulty or outside of acceptable limits must be promptly repaired or replaced and re-verified.
3.2.2. Anti-Static Material Compliance Inspections
Verification must extend to the materials used in the packing process. Regular inspections should be conducted to confirm that only approved anti-static materials are in use within the EPA. This includes verifying packaging films, wraps, tapes, and coatings against the approved materials list in the ESD control plan. Inspections should also assess the condition of these materials, checking for any damage, degradation, or contamination that could compromise their anti-static properties. Material certifications from suppliers should be periodically reviewed to ensure continued compliance with specifications.
3.2.3. Personnel Compliance Monitoring and Audits
Even with well-defined procedures and equipment, personnel compliance is critical. Regular audits should include observation of personnel working within the EPA to ensure they are consistently following ESD control procedures. This includes verifying the correct wearing of wrist straps, use of conductive footwear (if required), and adherence to handling protocols for ESD-sensitive materials. Feedback should be provided to personnel as needed, and any recurring non-compliance issues should be addressed through retraining or procedural adjustments.
3.2.4. Environmental Parameter Monitoring
For facilities utilizing humidity control or ionization systems, regular monitoring of these environmental parameters is essential. Humidity levels within the EPA should be checked against the target range defined in the ESD control plan. Ionizers should be tested periodically to ensure they are functioning correctly and producing a balanced ion output within specified limits. Calibration and maintenance schedules for environmental control equipment should be adhered to, and records of monitoring data should be maintained to demonstrate consistent environmental control.
3.3. Employee Training and ESD Awareness Programs
Even the most meticulously designed ESD control plan and robust technical measures will fall short if personnel are not adequately trained and consistently aware of ESD risks and control procedures. A comprehensive and ongoing employee training and awareness program is indispensable for sustained ESD protection.
3.3.1. Foundational ESD Principles Training
Training programs must start with educating employees on the fundamental principles of ESD. This includes explaining what static electricity is, how it is generated (particularly through triboelectric charging), and why it poses a significant concern in steel wire packing and handling of sensitive equipment. Demonstrations and real-world examples can effectively illustrate the invisible nature of static electricity and its potential impact. Emphasizing the costs associated with ESD damage, both in terms of safety risks and operational inefficiencies, helps to underscore the importance of ESD control.
3.3.2. Detailed Training on ESD Control Measures
Training must thoroughly detail all specific anti-static measures implemented within the steel wire packing facility. This includes step-by-step instructions on grounding procedures, proper usage of anti-static materials, and the function of environmental controls like humidity and ionization. Hands-on training, where employees practice grounding techniques and handling anti-static materials, is far more effective than purely theoretical instruction. Employees should be trained to recognize ESD control equipment, understand its purpose, and perform basic checks to ensure it is functioning correctly (e.g., wrist strap self-testing).
3.3.3. Proper Handling Procedures for ESD Safety
Training should specifically address proper handling procedures for steel wire and packaging materials within the EPA. This includes guidelines on minimizing friction and contact that can generate static, maintaining appropriate distances from non-ESD-safe materials, and procedures for transporting and storing ESD-sensitive items. Employees should be trained on how to identify ESD-sensitive components or areas and the specific precautions to take in those zones. Visual aids, such as posters and diagrams, within the EPA can reinforce these procedures.
3.3.4. Emphasizing the Importance of Consistent Compliance
Crucially, training must emphasize the importance of consistent compliance with ESD control procedures. Employees need to understand that ESD control is not a voluntary activity but a mandatory requirement for safety, quality, and operational efficiency. Training should highlight the individual and collective responsibility of each employee in maintaining an ESD-safe environment. Regular refresher training and awareness campaigns help reinforce these messages and maintain a culture of ESD consciousness within the workplace. Positive reinforcement and recognition of good ESD control practices can further enhance employee engagement and compliance.
4. Conclusion
Implementing robust anti-static measures in steel wire packing transcends mere adherence to safety guidelines; it represents a strategic investment in operational excellence, product quality, and the creation of a safer working environment. By comprehensively understanding the inherent risks of ESD and proactively adopting a multi-faceted approach that encompasses meticulous grounding, the strategic deployment of anti-static materials, precise environmental controls, and rigorous, ongoing training, steel wire manufacturers can establish a packing process that is not only safer but also demonstrably more productive and consistently reliable. This proactive and holistic approach effectively minimizes potential hazards, significantly reduces operational disruptions stemming from ESD-related issues, and ultimately contributes to a more successful, sustainable, and resilient business operation in the competitive steel industry.