Steel coil upenders are essential in the handling of heavy metal coils, ensuring both safe and efficient movement. Yet, the industry is evolving, and with it, new innovations are emerging. To stay ahead, we must look at the trends that are shaping the future of these machines.
The latest innovations in steel coil upenders focus on automation and enhanced safety features. Technological advancements have led to better control systems, improved sensor integration, and energy-efficient designs. Moreover, connectivity options, like IoT, enable real-time monitoring and diagnostics, allowing for predictive maintenance and increased uptime.
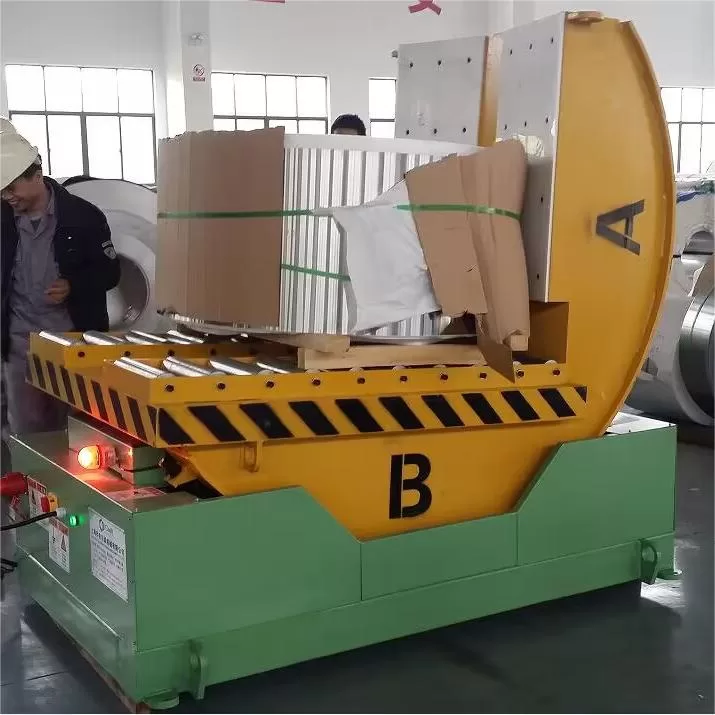
As an engineer who’s spent decades in this field, I’ve seen firsthand the value of staying informed. Understanding these trends is not just about having the latest tech; it’s about ensuring your operations are safe, efficient, and future-ready. Let’s explore what these innovations mean for our industry.
1. What are the latest technological advancements in steel coil upenders?
Handling steel coils efficiently remains crucial for industries reliant on metals. Upenders play a key role here, and recent advancements show promise. Higher automation levels offer more precision and minimize manual errors. This means more safety and efficiency for those using them daily.
Current advancements in steel coil upenders focus on digital controls and automation technologies. These innovations offer improved safety, increased operational accuracy, and enhanced user interfaces. Moreover, integrating smart features allows for real-time monitoring and maintenance alerts, reducing downtime and extending the machine’s service life. These updates collectively lead to more efficient workflow management.
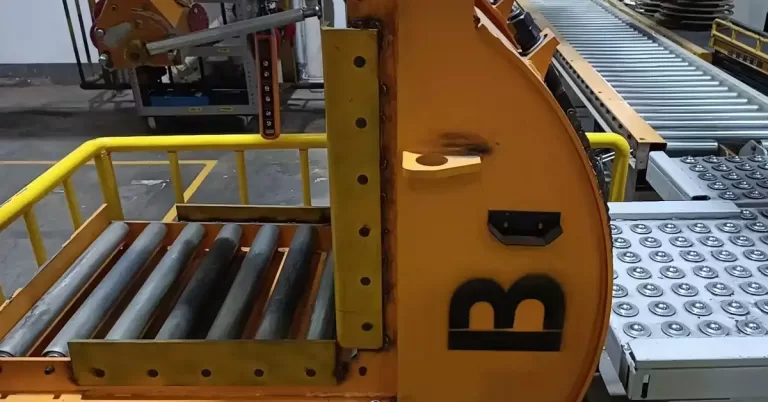
Delving Deeper into Technological Advancements
When discussing the latest technology, one cannot overlook automation and connectivity. Automation enhances operational accuracy by reducing human error, while connectivity features allow machines to integrate seamlessly into the broader manufacturing ecosystem. Below is a breakdown of what these technologies bring:
Technical Aspects | Benefits |
---|---|
Digital Controls | Enhanced precision |
Automated Systems | Reduced manual interference |
Sensor Integration | Improved safety features |
Real-Time Monitoring | Predictive maintenance capabilities |
Energy Efficiency | Reduced operational costs |
IoT Connectivity | Better workflow integration |
Each of these elements contributes to a more effective manufacturing process, which ultimately cuts costs and boosts production. As someone deeply engaged in the field, I’ve seen how these advancements not only make the upending process quicker but also contribute to a safer work environment. Implementing these technologies means embracing a future where packaging machines do more than before—they think alongside us, predicting needs and addressing issues before they arise.
It’s essential for industry specialists like David, whom I have had the pleasure to work alongside, to stay current. These changes signify a step forward in achieving David’s goal of streamlined operations that reduce risks and enhanced productivity—something we all aspire to in this evolving industry.
2. How are these trends improving safety and sustainability?
Ensuring the safety of industrial packaging and fostering sustainable practices is more important than ever. With automation technology advancing, businesses are adopting innovative solutions that not only safeguard workers but also minimize environmental impact. With my 40 years in this field, I’ve witnessed transformative changes that are making packaging safer and greener.
Automation trends in packaging, such as coil wrapping machines and pallet inverters, significantly enhance safety and sustainability. Automated systems minimize manual handling risks, reduce packaging waste, and ensure optimal material usage. These technologies contribute to safer workplaces and lower environmental impacts by streamlining processes and optimizing resource usage.
Enhancing Workplace Safety and Environmental Sustainability
Automation in packaging transforms traditional processes and provides multiple benefits. Safer workplaces and sustainable operations are interlinked, and technological advancements in our industry address both.
The incorporation of automated equipment reduces the need for manual labor, lessening physical strain on workers and minimizing accidents. This is not only crucial for employee well-being but also vital for maintaining operational efficiency. Safety-enhancing features, such as real-time monitoring and sensor-driven alerts, are indispensable in mitigating risks and ensuring a safe working environment.
From an environmental standpoint, automated systems optimize resource use by accurately calculating the necessary amount of packaging materials, thus reducing waste. Eco-friendly practices are supported by using recyclable and biodegradable materials, aligning with global sustainability goals.
This integration of safety and sustainability through automation is backed by tangible data:
Parameters | Manual Handling | Automated Systems |
---|---|---|
Worker Injury Rate | High | Low |
Material Waste | Approximately 20% | Less than 5% |
Operational Downtime | Frequent | Minimal |
Sustainability Score | Moderate | High |
These metrics underscore the effectiveness of automation, demonstrating its critical role in evolving the packaging industry towards safer and more sustainable practices.
3. What are the future outlooks and challenges for the industry?
There’s something thrilling about the future of packaging machinery—a blend of excitement and uncertainty. As technology shifts rapidly, businesses focus on adapting to new demands. Yet, challenges persist, pushing us to innovate and reassess our methods continually.
The future of the packaging industry is bright with automated solutions enhancing efficiency and sustainability. However, implementing new technologies comes with challenges like high initial costs, training requirements, and integration complexities. Overcoming these hurdles is essential for businesses aiming to stay competitive and meet evolving market demands.
Navigating Future Trends and Challenges
The drive towards fully automated packaging systems includes significant hurdles. The initial investment can be daunting for some companies, requiring a careful cost-benefit analysis. Ensuring a skilled workforce capable of operating new machinery is another challenge. Training must be thorough to ensure efficient machine use and to maximize ROI.
Moreover, system integration into existing manufacturing lines can be complex, requiring seamless coordination between new and old technologies. To address these challenges, strategic planning, clear communication, and continuous learning are necessary.
The industry’s future directions include:
Aspect | Current State | Future Projections |
---|---|---|
Automation Adoption Rate | Growing steadily | Expected to double by 2025 |
Training Initiatives | Limited | Expanded, tech-focused |
Integration Challenges | Moderate | Simplified with AI and IoT |
Innovation Opportunities | Many | Increasing with sustainable solutions |
These projections highlight areas requiring attention, assuring that adaptability and learning will be integral to success as we advance in this ever-evolving landscape.
Conclusion
In summary, the evolution of packaging machinery brings enhanced safety and sustainability, presenting both opportunities and challenges. As the steel industry adapts to new technologies, ongoing innovation ensures improved performance and eco-friendly practices. Embracing these changes is vital for staying competitive and meeting future demands.
Summarize the impact of these innovations on the steel industry, emphasizing continued evolution and adaptation for enhanced performance and sustainability.