How to Select the Right Mold Flipper for Different Weight Molds?
Selecting the correct mold flipper is crucial for ensuring safety and efficiency in manufacturing processes involving heavy molds. Understanding the weight capacity and operational needs is paramount for choosing the right machinery.

To select the right mold flipper, consider the maximum weight and dimensions of your molds, the frequency of flipping operations, and the available space in your facility. Prioritize models with robust construction, adequate safety features like locking mechanisms and emergency stops, and user-friendly controls. Assess whether you need a standard model or a customized solution for unique mold shapes or handling requirements.
Choosing the appropriate mold flipper doesn’t have to be daunting. By breaking down the key considerations and understanding the different types of flippers available, you can make an informed decision that optimizes your workflow and safeguards your team. Let’s delve into the essential factors.
1. Understanding Mold Weight and Capacity Requirements
When selecting a mold flipper, the first and most critical step is to accurately determine the weight of the molds you’ll be handling. This weight directly dictates the required capacity of the mold flipper to ensure safe and effective operation.
The primary factor in selecting a mold flipper is its weight capacity. Ensure the flipper’s maximum load capacity significantly exceeds the heaviest mold you plan to handle. This buffer is crucial for safety and to prevent machine overload, which can lead to breakdowns and workplace accidents. Consider future needs and potential increases in mold weight as well.
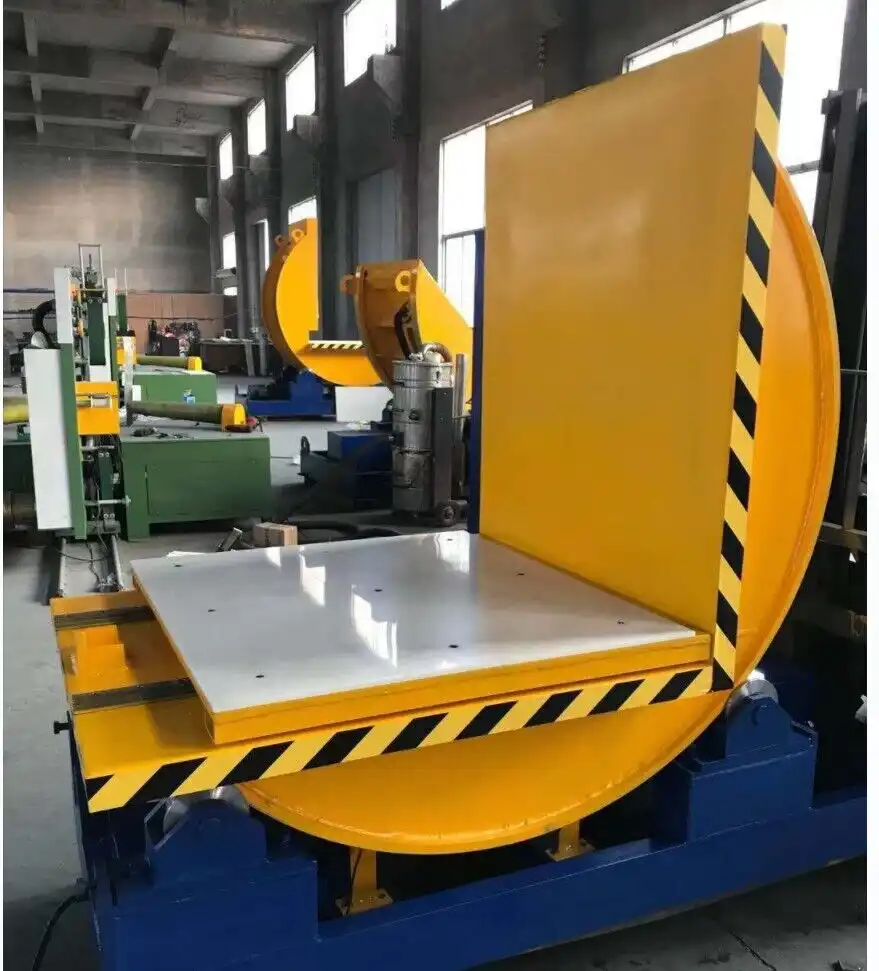
To accurately assess your needs, it’s essential to go beyond just the maximum weight. Let’s explore the nuances of weight considerations and how they impact your selection.
Critical Weight Considerations for Mold Flipper Selection
Choosing a mold flipper isn’t just about matching the maximum weight. It’s about understanding the full spectrum of weight-related factors that can impact performance and safety. Failing to account for these nuances can lead to operational inefficiencies and potential hazards.
1. Maximum Mold Weight vs. Safe Working Load (SWL)
It’s crucial to differentiate between the maximum advertised capacity and the Safe Working Load (SWL) of a mold flipper. The maximum capacity might represent the absolute limit under ideal conditions, while the SWL is the manufacturer-recommended safe operating limit under normal working conditions, often with a safety factor built in. Always prioritize selecting a mold flipper where your heaviest mold weight falls comfortably within the SWL, not just under the maximum capacity.
2. Center of Gravity (CG) of Molds
The weight distribution within a mold, or its center of gravity, significantly affects the load on the flipper. Off-center loads can create uneven stress and reduce the effective capacity of the machinery. For molds with irregular shapes or uneven weight distribution, it’s vital to consult with the mold flipper manufacturer to ensure the chosen model can handle the off-center load safely and effectively. Customization options, like adjustable platforms or specialized clamping mechanisms, might be necessary.
3. Dynamic vs. Static Load
Mold flippers handle dynamic loads during the flipping motion, which are different from static loads when the mold is stationary. Dynamic loads can exert greater stress on the machinery due to inertia and momentum. Ensure the mold flipper is designed to handle the dynamic forces generated during operation, especially for heavier molds or faster flipping cycles. Robust construction, powerful motors, and smooth start/stop mechanisms are crucial for managing dynamic loads effectively.
To illustrate the importance of these factors, consider the following scenarios:
Factor | Scenario 1: Miscalculation | Scenario 2: Correct Assessment | Outcome |
---|---|---|---|
Mold Weight | Heaviest mold: 8 tons. Flipper chosen: 10-ton max capacity. | Heaviest mold: 8 tons. Flipper chosen: 15-ton SWL (20-ton max). | Scenario 1 risks overload and failure. Scenario 2 ensures safety margin. |
Center of Gravity | CG ignored for irregularly shaped mold. | CG analyzed. Custom platform designed for balanced support. | Scenario 1: Unstable flipping, potential tipping. Scenario 2: Stable operation. |
Load Type | Flipper rated for static load only, used for frequent flips. | Flipper designed for dynamic loads, suitable for high-frequency use. | Scenario 1: Premature wear and tear, potential breakdown. Scenario 2: Durable performance. |
By carefully considering these weight-related factors and engaging with manufacturers to assess specific mold characteristics, you can confidently select a mold flipper that meets your operational demands and ensures long-term safety and reliability.
2. Types of Mold Flippers and Their Suitability
Different types of mold flippers cater to varying weight capacities and operational needs. Understanding these types is crucial for making the right choice for your specific application.
Mold flippers come in various designs, broadly categorized by their lifting and rotating mechanisms. Common types include hydraulic upenders, mechanical upenders, and specialized tilt tables. Hydraulic models are known for their high lifting capacity and smooth operation, ideal for very heavy molds. Mechanical upenders are robust and reliable for medium to heavy loads. Tilt tables offer versatility for lighter molds and can sometimes incorporate additional features like lift and transfer capabilities.
Let’s explore the most common types of mold flippers in more detail, outlining their strengths and weaknesses to guide your selection process.
Exploring Different Mold Flipper Technologies
The market offers a range of mold flipper technologies, each with unique characteristics that make them suitable for specific applications and weight ranges. Choosing the right technology is key to optimizing performance and cost-effectiveness.
1. Hydraulic Mold Flippers
Hydraulic mold flippers are characterized by their use of hydraulic cylinders to generate lifting and rotating force. Strengths: They excel in handling very heavy molds, often exceeding 20 tons or more. Hydraulic systems provide smooth, controlled motion and precise positioning. They are generally robust and durable for heavy-duty industrial applications. Considerations: Hydraulic systems can be more complex to maintain and may have higher initial costs. They also require a hydraulic power unit, which adds to the footprint and energy consumption.
2. Mechanical Mold Upenders
Mechanical upenders typically utilize a combination of motors, gears, and chains or screws to achieve the flipping motion. Strengths: Mechanical upenders are known for their reliability and simplicity in design, often requiring less maintenance than hydraulic systems. They are well-suited for medium to heavy molds, typically ranging from a few tons up to 10-20 tons. They can be more energy-efficient than hydraulic systems in some applications. Considerations: Mechanical systems might offer less smooth motion compared to hydraulics, especially at very high weights. Their lifting capacity might be limited compared to the largest hydraulic models.
3. Tilting Tables and Lift Tables with Tilting Functionality
Tilting tables, and lift tables with integrated tilting, offer a more versatile approach, especially for lighter to medium molds. These may use hydraulic, pneumatic, or electromechanical systems. Strengths: Tilting tables can often be integrated with other functions, such as lifting and horizontal transfer, providing a multi-functional solution. They are often more compact and can be easier to integrate into existing workflows. Some models offer precise tilt angle control. Considerations: Their weight capacity is generally lower than dedicated hydraulic or heavy-duty mechanical upenders. The tilting motion might be slower compared to dedicated flippers.
To help you visualize the best fit for each type, here’s a comparative table:
Feature | Hydraulic Mold Flippers | Mechanical Mold Upenders | Tilting/Lift Tables |
---|---|---|---|
Weight Capacity | Very High (20+ tons) | Medium to High (up to 20 tons) | Low to Medium (up to 10 tons) |
Motion Control | Smooth, Precise | Robust, Reliable | Versatile, Adaptable |
Maintenance | Higher Complexity | Lower Complexity | Moderate Complexity |
Cost | Higher Initial Cost | Moderate Cost | Varies, can be lower |
Best Suited For | Very Heavy Molds, Heavy Duty | Medium to Heavy Molds | Lighter Molds, Multi-function |
Energy Efficiency | Can be less efficient | Generally more efficient | Varies |
Choosing the right type depends heavily on your mold weights, operational frequency, budget, and desired level of automation and integration with other equipment. Careful evaluation of these factors is essential.
3. Key Features and Customization Options
Beyond weight capacity and type, specific features and customization options significantly impact the usability, safety, and efficiency of a mold flipper. Selecting a model with the right features tailored to your needs is crucial for optimal performance.
Essential features to look for include robust safety mechanisms like emergency stops, secure locking systems during rotation, and overload protection. Consider the control system – is it user-friendly? Does it offer precise positioning? Customization can range from platform size adjustments to specialized cradles for unique mold shapes, motorized adjustments, and integration with conveyor systems for automated workflows. Evaluate your specific needs for features like variable speed control, remote operation, and data logging for maintenance.
Let’s dive into the critical features and customization possibilities that can elevate a mold flipper from simply functional to truly optimized for your operations.
Optimizing Mold Flippers with Key Features and Customization
Standard mold flippers provide a baseline functionality, but the real gains in efficiency and safety come from carefully selecting models with the right features and exploring customization options tailored to your specific needs.
1. Safety Features: Non-Negotiable Essentials
Safety should be paramount. Essential safety features include:
- Emergency Stop Buttons: Strategically placed, easily accessible e-stops are critical to halt operation immediately in case of any issue.
- Locking Mechanisms: Secure mechanical or hydraulic locking systems to prevent unintended rotation or movement during loading, unloading, and maintenance.
- Overload Protection: Sensors and systems to prevent operation beyond the Safe Working Load, protecting the machine and preventing accidents.
- Proximity Sensors & Light Curtains: To detect obstructions or personnel in the operating zone and automatically stop or prevent motion.
- Safety Interlocks: Ensuring safety gates or barriers are in place and functional before operation can commence.
2. Control Systems and User Interface: Enhancing Operability
The control system directly impacts ease of use and precision. Consider:
- Intuitive Controls: Simple, user-friendly controls for operators with clear labeling and logical layout.
- Variable Speed Control: Allows for adjusting the flipping speed to match the mold size and sensitivity, ensuring smooth and controlled motion.
- Programmable Logic Controllers (PLCs): For more complex operations and integration with automated systems, PLCs offer programmability and data logging capabilities.
- Remote Operation: Pendant controls or remote wireless controls can enhance operator safety and visibility, especially for large molds.
- Positioning Accuracy: For applications requiring precise alignment after flipping, look for models with accurate positioning systems and indicators.
3. Customization for Specific Needs: Tailoring to Your Workflow
Standard models might not perfectly fit every application. Customization options to consider:
- Platform Size and Shape: Adjusting platform dimensions to perfectly match your mold sizes, or designing specialized cradles for unique mold geometries (e.g., V-saddles for cylindrical molds).
- Motorized Adjustments: Motorized V-saddles or pallet adjusters to gently position and secure molds before flipping, especially useful for coils or irregularly shaped items.
- Integration with Conveyor Systems: Adding rollers, ball transfers, or powered conveyors to the flipper platform for seamless loading and unloading in automated lines.
- Pit Mounting: Recessing the flipper into a pit to make the platform flush with the floor, simplifying loading with forklifts or pallet jacks.
- Weighing Systems: Integrating load cells for real-time weight monitoring, enhancing safety and inventory management.
To illustrate the impact of features, consider this feature comparison across different hypothetical models:
Feature | Model A (Basic) | Model B (Advanced Safety) | Model C (Customized) |
---|---|---|---|
Emergency Stop | Yes | Yes | Yes |
Locking System | Basic Manual | Hydraulic & Mechanical | Enhanced Hydraulic |
Overload Protection | No | Yes | Yes |
Variable Speed | No | Yes | Yes, Programmable |
Remote Control | No | Optional | Yes |
Custom Platform | No | Limited Options | Fully Customizable |
Conveyor Integration | No | No | Yes |
By carefully evaluating your operational needs and exploring available features and customization, you can select a mold flipper that not only meets your weight requirements but also enhances safety, efficiency, and integration within your manufacturing environment.
4. Installation, Maintenance, and Long-Term Considerations
Choosing the right mold flipper extends beyond initial specifications. Installation requirements, maintenance needs, and long-term operational considerations are equally vital for ensuring a smooth integration and maximizing the lifespan of your investment.
To guarantee the longevity and reliability of your mold flipper, factor in these crucial aspects from the outset. A proactive approach to installation and maintenance will pay dividends in the long run.
Proper installation is crucial for the safe and effective operation of a mold flipper. Consider factors like floor loading capacity, power supply requirements (electrical or hydraulic), and space for operation and maintenance access. Regular maintenance is essential, including lubrication of moving parts, inspection of hydraulic hoses or chains, and checks of electrical connections and safety features. Factor in the availability of spare parts and the manufacturer’s support and warranty. A well-maintained mold flipper will provide years of reliable service and minimize downtime.
Selecting a mold flipper is a significant investment, and ensuring its long-term performance requires careful planning beyond the initial purchase. Let’s explore the key considerations for installation, maintenance, and overall lifecycle management.
Installation:
- Site Preparation: Assess the floor’s load-bearing capacity to handle the flipper and maximum mold weight. Ensure a level and stable foundation.
- Power Requirements: Verify electrical power supply compatibility (voltage, phase) or hydraulic power unit requirements.
- Space Planning: Allocate sufficient space for flipper operation, mold loading/unloading, and safe access for operators and maintenance personnel.
- Professional Installation: Engage qualified technicians for installation, especially for hydraulic and electrical connections, to ensure compliance with safety standards and proper functionality.
Maintenance:
- Regular Inspection Schedule: Establish a routine inspection schedule covering mechanical components (chains, gears, rollers), hydraulic/pneumatic systems (hoses, cylinders), electrical wiring, and safety devices.
- Lubrication: Regularly lubricate moving parts (bearings, gears, chains) as per manufacturer recommendations to minimize wear and ensure smooth operation.
- Hydraulic System Checks: For hydraulic models, periodically inspect hoses, fittings, and fluid levels for leaks or damage. Change hydraulic fluid at recommended intervals.
- Electrical System Checks: Inspect wiring, connections, and control panels for damage or loose connections. Test safety circuits and emergency stops.
- Calibration and Adjustments: Periodically calibrate sensors, adjust limit switches, and ensure all safety features are functioning correctly.
Long-Term Considerations:
- Spare Parts Availability: Inquire about the availability and lead time for critical spare parts. Consider stocking essential spares to minimize downtime.
- Manufacturer Support and Warranty: Choose a reputable manufacturer with a solid warranty and readily available technical support, including documentation, training, and troubleshooting assistance.
- Operator Training: Provide thorough training to operators on safe operation, basic maintenance, and troubleshooting procedures.
- Lifecycle Cost Analysis: Beyond the initial purchase price, consider long-term operating costs (energy consumption, maintenance, repairs) and factor these into your selection process.
- Upgrades and Refurbishment: Explore options for future upgrades or refurbishment to extend the lifespan of the mold flipper and adapt to evolving needs.
By proactively addressing installation, maintenance, and long-term considerations, you can maximize the return on your investment in a mold flipper, ensuring reliable performance, minimizing downtime, and maintaining a safe working environment for years to come.
Conclusion
Selecting the right mold flipper is a critical decision impacting safety, productivity, and cost-effectiveness in mold handling operations. By carefully evaluating mold weights, understanding different flipper types, prioritizing essential features, and planning for installation and maintenance, you can make an informed choice. Remember to prioritize safety, choose a machine with adequate capacity and robust construction, and consider customization options to optimize the flipper for your specific molds and workflow. Investing in the right mold flipper is an investment in efficiency and a safer workplace.