Steel wire packing, while essential for protecting products during transit, can contribute significantly to material waste. Businesses are increasingly seeking sustainable solutions to minimize environmental impact and improve efficiency. This article explores practical strategies to reduce waste in steel wire packing, focusing on material optimization, process enhancements, and sustainable alternatives.
To effectively reduce waste in steel wire packing, businesses should focus on optimizing material usage through precise measurement and design, improving process efficiency by automating wrapping and strapping, and transitioning to sustainable packaging materials like recycled or biodegradable options. Implementing these changes can significantly lower environmental impact and operational costs.
This article will delve into actionable methods for minimizing waste in steel wire packing, offering insights into material selection, efficient processes, and technological solutions. By adopting these strategies, businesses can achieve both environmental responsibility and economic benefits in their steel wire packing operations.
1. Optimizing Material Usage for Steel Wire Packing Waste Reduction
Efficient material usage is paramount in reducing waste in steel wire packing. Overpacking or using excessive materials not only inflates costs but also contributes to unnecessary environmental burden. By carefully analyzing material needs and optimizing packing designs, businesses can significantly decrease their waste footprint.
The key to optimizing material usage in steel wire packing lies in implementing precise measurement techniques, adopting right-sized packaging designs, and diligently monitoring material consumption. This involves accurately assessing the required packaging strength, minimizing overlaps in wrapping, and selecting the most appropriate material thickness to ensure adequate protection without excess.
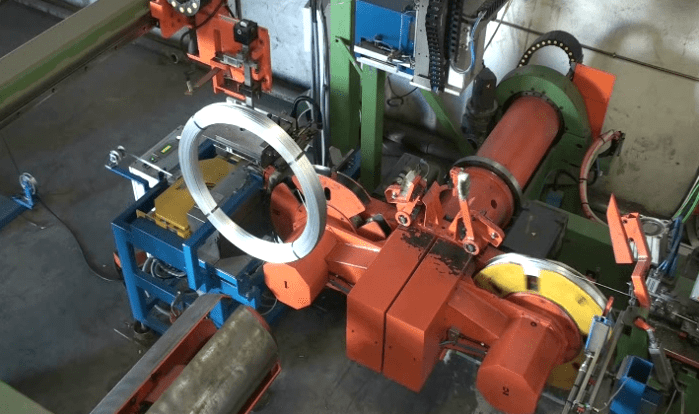
To achieve truly optimized material usage, a critical examination of current practices is necessary. This involves understanding where material waste originates in the packing process and implementing targeted solutions to mitigate these issues. Let’s break down the problem further.
1.1 Overcoming Over-Specification in Steel Wire Packaging Design
One significant source of material waste in steel wire packing stems from over-specification in packaging design. Companies often err on the side of caution, using thicker or more layers of packaging material than actually required. This "better safe than sorry" approach, while seemingly prudent, leads to substantial material wastage over time. To combat this, a data-driven approach to packaging design is crucial.
Analyzing Wire Properties and Transit Conditions
The first step is to thoroughly analyze the properties of the steel wire being packaged. Factors such as wire diameter, coil weight, and surface finish directly influence the required packaging strength. Simultaneously, understanding the typical transit conditions – distance, mode of transport, handling frequency – is equally important. Wire being shipped locally via dedicated trucks will have different packaging needs compared to wire transported internationally by sea and rail.
Right-Sizing Packaging Materials
Once these parameters are defined, businesses can move towards right-sizing their packaging materials. This involves selecting the appropriate gauge of stretch film, the correct width of strapping bands, and the optimal dimensions for any protective interleaving materials. Instead of defaulting to the thickest available option, consider testing thinner alternatives under simulated transit conditions to identify the minimum material requirement for adequate protection.
Data-Driven Material Reduction
Implementing a system to track material usage and damage rates is essential for continuous improvement. By monitoring how much packaging material is used per coil and correlating this with the frequency of transit damage, companies can identify opportunities for material reduction. For example, if damage rates remain consistently low even after reducing stretch film thickness by 10%, this indicates a clear opportunity to further optimize material usage without compromising product integrity.
Comparative Analysis of Material Usage and Waste
Packaging Parameter | Current Practice | Optimized Practice | Potential Waste Reduction |
---|---|---|---|
Stretch Film Thickness (microns) | 25 | 20 | 20% |
Strapping Bands per Coil | 4 | 3 | 25% |
Overlap Percentage in Wrapping | 50% | 30% | 40% |
By systematically analyzing each aspect of packaging and making data-informed adjustments, businesses can significantly reduce material consumption and waste in steel wire packing, leading to both environmental and cost savings.
2. Enhancing Packing Process Efficiency to Minimize Steel Wire Waste
Beyond material optimization, process efficiency plays a critical role in minimizing waste. Inefficient packing processes often lead to material wastage, energy consumption, and increased labor costs. Streamlining these processes through automation and optimized workflows is essential for sustainable waste reduction.
Enhancing packing process efficiency involves automating repetitive tasks like wrapping and strapping, optimizing layout for smooth material flow, and implementing quality control measures to prevent rework. By minimizing manual handling and ensuring consistent application of packaging materials, businesses can significantly reduce waste and improve overall operational effectiveness.

To achieve truly efficient and waste-minimized steel wire packing, focusing on specific areas of process improvement is crucial. Let’s explore how process optimization contributes to sustainability.
2.1 Streamlining Steel Wire Packing Operations for Sustainable Waste Reduction
Inefficiencies in the steel wire packing process manifest in various forms, from material spillage and breakage to inconsistent wrapping and unnecessary steps. Addressing these inefficiencies requires a holistic approach, focusing on workflow optimization, automation, and operator training.
Automation for Consistency and Precision
Manual packing processes are inherently prone to variability. The amount of stretch film applied, the tension of strapping bands, and the placement of protective materials can differ significantly from operator to operator, leading to inconsistent packaging and potential material waste. Automating key processes, such as stretch wrapping and strapping, using specialized wire packing machines, ensures consistent and precise application of materials, minimizing overuse and reducing the likelihood of product damage due to inadequate packaging.
Optimized Workflow and Layout
The physical layout of the packing area and the flow of materials can significantly impact efficiency. Disorganized workspaces, excessive material handling distances, and poorly defined workflows contribute to wasted time and material. Implementing lean principles to optimize the packing line layout, ensuring smooth material flow from storage to packing to dispatch, minimizes unnecessary movement and reduces the risk of material damage or loss.
Waste Reduction through Process Control
Implementing process control measures, such as standardized work instructions and regular quality checks, is crucial for preventing errors and rework. Clearly defined procedures for each packing step, coupled with operator training and ongoing monitoring, ensures that packing is done correctly the first time, minimizing the need to repackage damaged coils or correct improperly wrapped bundles. This reduces material waste and saves valuable time and labor.
Quantifying Process Efficiency Improvements
Efficiency Metric | Manual Packing | Automated Packing | Improvement | Waste Reduction Impact |
---|---|---|---|---|
Stretch Film Usage per Coil | 1.5 kg | 1.2 kg | 20% | High |
Packing Time per Coil | 5 minutes | 2 minutes | 60% | Medium |
Rework Rate | 5% | 1% | 80% | High |
By strategically streamlining packing operations through automation, workflow optimization, and process control, businesses can achieve significant improvements in efficiency and substantial reductions in waste generation in steel wire packing.
3. Embracing Sustainable Materials in Steel Wire Packing
The choice of packaging materials has a profound impact on environmental sustainability. Traditional packaging materials, often derived from non-renewable resources and not easily recyclable, contribute significantly to environmental pollution. Transitioning to sustainable alternatives is a crucial step in reducing the environmental footprint of steel wire packing.
Embracing sustainable materials in steel wire packing involves exploring and adopting eco-friendly alternatives such as recycled plastics, biodegradable films, and paper-based options. This transition not only reduces reliance on virgin resources and landfill waste but also aligns with growing consumer demand for environmentally responsible packaging.

To effectively transition to sustainable packaging, businesses need to understand the various options available and their respective benefits and trade-offs. Let’s compare some sustainable material alternatives.
3.1 Comparing Sustainable Packaging Material Options for Steel Wire
The market for sustainable packaging materials is rapidly evolving, offering a range of alternatives to traditional plastics and non-recycled materials. For steel wire packing, several options deserve consideration, each with its own set of characteristics and suitability.
Recycled Plastics:
Utilizing recycled plastics, such as post-consumer recycled polyethylene (rPE) or polypropylene (rPP), significantly reduces reliance on virgin fossil fuels and diverts plastic waste from landfills. Recycled plastics can be used to produce stretch film, strapping bands, and protective sheets for steel wire packing. While offering a more sustainable option, it’s important to ensure the recycled content meets the required performance standards for wire protection.
Biodegradable and Compostable Films:
Biodegradable and compostable films, often made from plant-based materials like corn starch or cellulose, offer an end-of-life advantage. These materials are designed to break down naturally in composting environments, reducing long-term environmental impact. However, their suitability for steel wire packing depends on their strength, durability, and cost-effectiveness compared to traditional or recycled plastics. Considerations include moisture resistance and performance under varying temperature conditions.
Paper-Based Packaging:
Paper and cardboard, particularly recycled options, are renewable and widely recyclable materials. For certain steel wire packing applications, especially for lighter coils or inner packaging, paper-based alternatives can replace plastic films or wraps. Recycled cardboard edge protectors and paper interleaving offer sustainable cushioning and protection. However, paper’s moisture sensitivity and lower tensile strength compared to plastics need to be considered for heavier or outdoor storage applications.
Material Comparison for Sustainable Steel Wire Packing
Material Type | Sustainability Advantages | Disadvantages | Suitability for Steel Wire Packing |
---|---|---|---|
Recycled Plastics (rPE, rPP) | Reduces virgin plastic use, Diverts waste from landfills | May have slightly lower performance than virgin plastic | Good for stretch film, strapping bands, sheets |
Biodegradable/Compostable Films | Compostable end-of-life, Plant-based resources | Potentially lower strength, Moisture sensitivity, Cost | Suitable for some inner packaging, lighter coils |
Recycled Paper/Cardboard | Renewable resource, Widely recyclable, Biodegradable | Lower moisture resistance, Lower tensile strength | Edge protectors, interleaving, light coils |
Choosing the most appropriate sustainable material requires a careful evaluation of performance requirements, cost considerations, and environmental goals. Often, a combination of sustainable materials, such as recycled plastic stretch film with recycled cardboard edge protection, provides a balanced and effective solution.
4. Leveraging Wire Packing Machines for Waste Reduction
Technology plays a crucial role in achieving waste reduction in steel wire packing. Modern wire packing machines are designed not only for efficiency and speed but also with features that directly contribute to minimizing material waste and promoting sustainable practices.
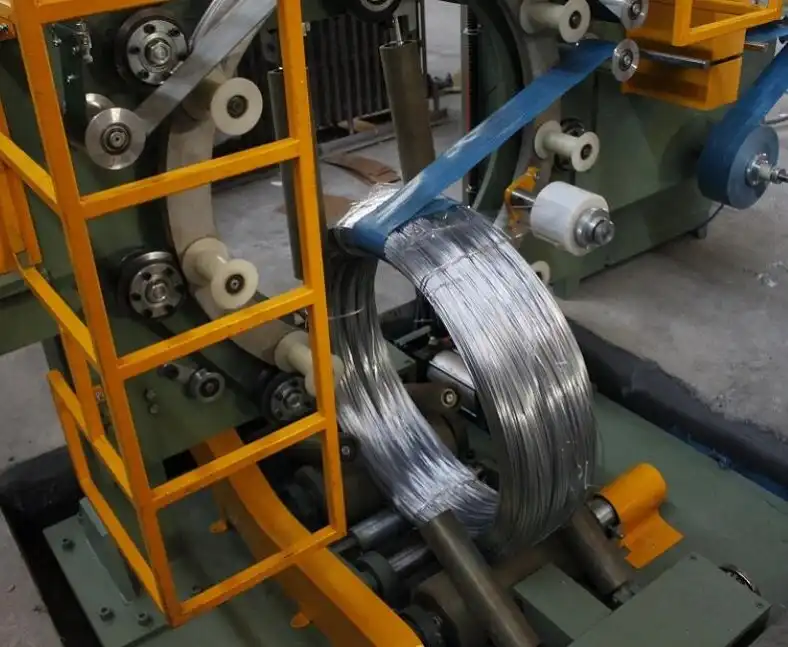
Wire packing machines, particularly automated systems, are instrumental in waste reduction by ensuring precise material application, optimizing wrapping patterns, and reducing material overlaps. These machines can be programmed to use the minimum necessary material while maintaining package integrity, leading to significant savings and environmental benefits.
Modern wire packing machines offer a range of features that directly address waste reduction:
- Precise Material Control: Automated machines apply stretch film and strapping with consistent tension and overlap, eliminating guesswork and minimizing material overuse common in manual packing.
- Optimized Wrapping Programs: Machines can be programmed with specific wrapping patterns tailored to coil dimensions and weight, ensuring optimal load containment with minimal film usage.
- Reduced Material Overlap: Advanced wrapping heads and sensors minimize unnecessary film overlap, further reducing material consumption without compromising package security.
- Integration with Sustainable Materials: Many modern machines are compatible with recycled and thinner gauge films, facilitating the transition to more sustainable packaging options.
- Data Monitoring and Reporting: Some machines offer data logging capabilities, tracking material usage per coil and providing valuable insights for further optimization and waste reduction efforts.
By investing in and effectively utilizing advanced wire packing machines, businesses can make significant strides in reducing waste, improving efficiency, and enhancing the sustainability of their steel wire packing operations.
Conclusion
Reducing waste in steel wire packing is not only an environmental imperative but also a smart business strategy. By focusing on material optimization, enhancing process efficiency, embracing sustainable materials, and leveraging technology like advanced wire packing machines, companies can achieve significant waste reduction and cost savings. Adopting these practices demonstrates environmental responsibility, enhances brand reputation, and contributes to a more sustainable future for the steel wire industry.