How to Reduce Waste in Steel Coil Packing?
Steel coil packing, while essential for protecting products during transit, often generates significant waste, contributing to environmental concerns and increased operational costs. Industries are now under pressure to adopt more sustainable practices that minimize material usage and reduce their environmental footprint. Discover effective strategies to streamline your coil packing process and achieve substantial waste reduction.
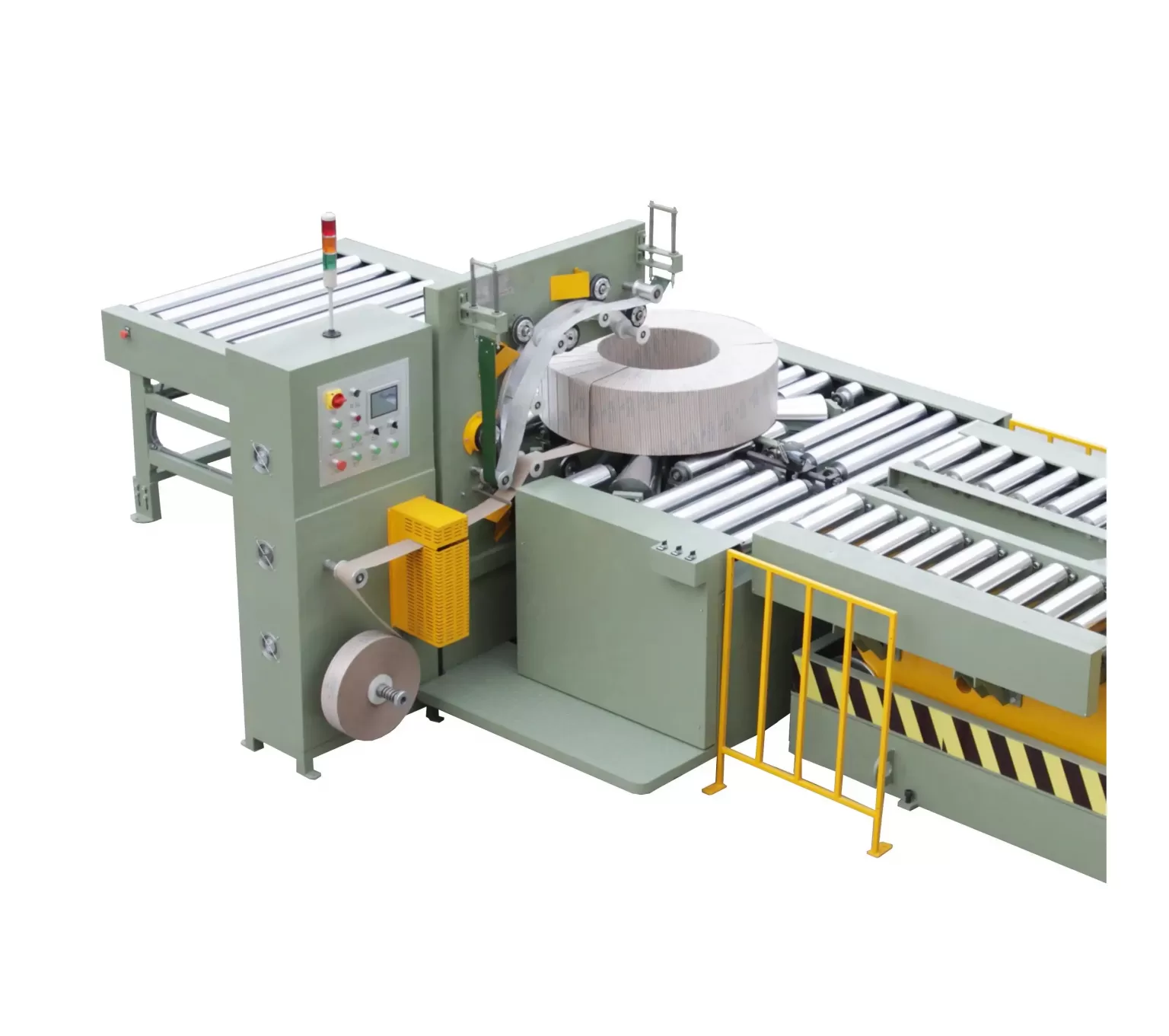
To reduce waste in steel coil packing, focus on optimizing material usage, selecting eco-friendly materials like recyclable polyethylene and polypropylene, and implementing efficient packing techniques such as ring-type wrapping. Proper tension control during wrapping is crucial to prevent over-wrapping and material breakage. Adopting automated coil packing machines further minimizes waste by ensuring consistent and precise application of packing materials, leading to significant reductions in both material consumption and environmental impact.

In today’s environmentally conscious and economically challenging landscape, reducing waste in steel coil packing is not just an ethical choice—it’s a strategic imperative. Let’s delve into actionable methods and innovative technologies that can help businesses minimize waste, enhance sustainability, and improve their bottom line.
1. Optimizing Material Usage in Coil Packing
Effective material usage is the cornerstone of waste reduction in steel coil packing. By carefully evaluating and adjusting how packing materials are applied, businesses can significantly decrease waste and lower costs. This involves moving away from wasteful practices and embracing methods that maximize efficiency without compromising protection.
Optimizing material usage in coil packing involves several key strategies, including employing ring-type wrapping machines that precisely apply materials, ensuring proper tension control to prevent over-wrapping, and selecting materials like polyethylene and polypropylene that are recyclable and minimize environmental impact. Automated systems further enhance material optimization by consistently applying the exact amount of wrapping needed, reducing variability and waste compared to manual methods. These focused approaches not only cut down on material costs but also contribute significantly to sustainable coil packing machine practices.
Deep Dive into Material Optimization Techniques
To achieve truly optimized material usage, a deeper understanding of specific techniques and technologies is essential. This involves not only choosing the right materials but also implementing advanced machinery and precise operational controls. Let’s explore these aspects in detail to uncover how businesses can minimize waste effectively.
Ring-Type Wrapping for Precision Application
Ring-type coil wrapping machines are designed to apply wrapping materials with exceptional precision. Unlike traditional methods that may involve overlapping and excessive material use, ring-type wrappers dispense materials directly and uniformly around the coil. This targeted application significantly reduces material waste by ensuring that every layer serves a purpose without unnecessary redundancy.
Tension Control for Preventing Over-Wrapping
Proper tension control is another critical factor in material optimization. When tension is not adequately managed, operators may over-wrap coils to ensure stability, leading to significant material wastage. Implementing advanced tension control systems ensures that the wrapping film is applied at the optimal tightness—enough to secure the coil but not excessively, which minimizes material consumption and prevents film breakage that would necessitate re-wrapping.
Material Selection: Choosing Sustainable Options
The choice of material itself plays a vital role in waste reduction. Traditional materials, especially laminated or VCI paper, are often less recyclable and contribute more to landfill waste. Switching to eco-friendlier alternatives like polyethylene (PE) and polypropylene (PP) offers a sustainable advantage. These materials are not only recyclable but also can be optimized for ring-type wrapping to further reduce waste. The table below compares different material types and their environmental attributes:
Material Type | Recyclability | Environmental Impact of Production | Waste Potential | Optimal Use Case |
---|---|---|---|---|
Polyethylene (PE) | High | Moderate | Low | Superior flexibility, moisture resistance |
Polypropylene (PP) | High | Lower | Low | Enhanced rigidity, lower production impact |
VCI Paper | Low | High (Chemical Processing) | Medium | Traditional rust protection |
Laminated Paper | Very Low | High (Multi-material) | High | Less sustainable option |
By focusing on precision application, tension control, and sustainable material selection, businesses can create a coil packing process that is not only cost-effective but also environmentally responsible, significantly reducing waste at every stage.
2. Embracing Eco-Friendly Materials
Selecting the right materials is paramount in reducing waste and enhancing the sustainability of steel coil packing. The materials used directly impact recyclability, the overall environmental footprint, and the amount of waste generated. Shifting towards eco-friendly options is a crucial step for modern, environmentally conscious operations.
Eco-friendly materials for steel coil packing primarily include recyclable polymers like polyethylene (PE) and polypropylene (PP), especially for ring-type wrapping. These materials offer significant advantages over traditional options like laminated or VCI paper due to their higher recyclability and lower environmental impact. Choosing between PE and PP depends on specific application needs; PE provides better flexibility and tear resistance, while PP offers enhanced rigidity and potentially lower production environmental impact. By transitioning to these materials, industries can substantially reduce waste and contribute to sustainable practices.
Delving Deeper into Sustainable Material Choices
To make informed decisions about eco-friendly materials, it’s important to understand the nuanced differences and benefits of options like polyethylene (PE) and polypropylene (PP). Beyond just recyclability, factors such as material attributes, production impacts, and the potential for circularity play significant roles in creating a truly sustainable packing process.
Polyethylene (PE) vs. Polypropylene (PP): A Detailed Comparison
While both PE and PP are superior choices compared to traditional laminated materials, their subtle differences can influence environmental performance and suitability for specific applications. Understanding these differences is key to making the most sustainable material selection.
Attribute | Polyethylene (PE) | Polypropylene (PP) | VCI Paper | Laminated Paper |
---|---|---|---|---|
Strength | High | High | Low-Medium | Medium |
Flexibility | High | Medium | Medium | Low |
Moisture Resistance | Excellent | Good | Poor | Fair |
Recyclability | High | High | Low | Very Low |
Production Impact | Moderate | Lower | High (Chemical Processing) | High (Multi-material) |
Cost-Effectiveness | Generally Cost-Effective | Generally Cost-Effective | Moderate Cost | Higher Cost |
Best Use Cases | Moisture-sensitive coils | Rigidity-prioritized coils | Traditional rust prevention | Basic protection, low recyclability |
As the table indicates, PE excels in flexibility and moisture resistance, making it ideal for coils needing robust protection from the elements and physical stress. PP, while also strong, offers enhanced rigidity, which might be preferred for applications where maintaining shape and structural integrity is paramount. Choosing between them involves balancing these properties with the specific demands of the steel coil and the environmental priorities of the operation.
The Role of Recycled Content and Circularity
Beyond the type of polymer, incorporating recycled content is crucial for maximizing sustainability. Using recycled PE or PP reduces the demand for virgin plastics, directly decreasing reliance on fossil fuels and lowering greenhouse gas emissions associated with plastic production. Furthermore, designing packaging for circularity—ensuring it can be easily recycled again after use—is essential. This means considering the entire lifecycle, from material sourcing to end-of-life management, to truly minimize environmental impact and close the loop in material usage. The future of sustainable coil packing lies in maximizing recycled content and optimizing for closed-loop systems.
3. Ensuring Proper Tension Control
Effective tension control during coil wrapping is not just about ensuring package integrity; it’s also a critical environmental consideration. Improper tension leads to material wastage, either through over-wrapping or package failure that necessitates re-wrapping. Optimizing tension is therefore both an economic and environmental imperative.
Proper tension control in coil wrapping directly minimizes material waste and energy consumption. Techniques such as regular machine calibration, using consistent quality materials, and implementing real-time tension adjustment systems are essential. These methods prevent over-wrapping, reduce material breakage, and ensure optimal utilization of wrapping films, directly contributing to environmental sustainability by reducing material throughput and waste generation.
Advanced Techniques for Tension Management and Resource Efficiency
Achieving optimal tension control goes beyond basic adjustments; it requires integrating advanced technologies and methodologies to ensure both package security and environmental responsibility. Exploring these techniques reveals how precision in wrapping directly translates to ecological benefits.
Precision through Technology: Real-Time Adjustment Systems
Modern coil wrapping machines equipped with real-time tension adjustment systems are at the forefront of minimizing material waste. These systems use sensors to continuously monitor film tension and automatically adjust wrapping parameters on-the-fly. This technology ensures consistent tension without excessive film usage, adapting to variations in coil size and material properties. The precision significantly reduces material consumption compared to manual or less sophisticated systems.
Training and Best Practices: The Human Element
While technology is vital, operator training and adherence to best practices are equally important. Well-trained operators can identify potential issues early, ensure correct machine setup, and minimize material waste through careful monitoring and adjustments. Implementing standard operating procedures (SOPs) for tension control and material handling further contributes to consistent and environmentally conscious wrapping processes. Combining advanced technology with skilled operation provides a holistic approach to minimizing waste and maximizing resource efficiency in coil packing. The table below outlines key techniques for tension control and their benefits:
Technique | Description | Environmental Benefit | Operational Advantage |
---|---|---|---|
Real-Time Adjustment Systems | Sensors and feedback loops dynamically modulate tension | Prevents over-wrapping, reduces film consumption | Consistent wrapping quality, less operator intervention |
Regular Machine Calibration | Periodic inspection and calibration of machinery | Ensures accurate tension application, minimizes errors | Reduced material breakage, lower downtime |
Consistent Material Quality | Using uniform quality films | Predictable tension behavior, less need for adjustment | Stable wrapping process, improved efficiency |
Operator Training | Comprehensive training on tension control best practices | Minimizes human error, reduces re-wrapping needs | Enhanced operator skill, reduced material wastage |
By integrating these advanced techniques and focusing on both technological solutions and human expertise, businesses can achieve superior tension control, significantly reducing material waste and enhancing the sustainability of their coil packing operations.
4. Coil Packing Machine Certifications and Regulatory Compliance
Navigating the landscape of coil packing machine certifications is essential for ensuring compliance with both safety and environmental regulations. These certifications serve as benchmarks, validating that machinery meets established standards and promotes responsible operation. Understanding these certifications is key to demonstrating a commitment to quality, safety, and environmental stewardship.
Coil packing machines require certifications to ensure safety, quality, and environmental compliance. Key safety certifications include CE Marking, ISO 9001, and UL Certification, ensuring operational safety and quality management. Environmental certifications like ISO 14001, ENERGY STAR, and RoHS compliance validate eco-friendly operation, energy efficiency, and restricted use of hazardous substances. These certifications are vital for legal operation, market access, and demonstrating a commitment to responsible manufacturing and environmental protection. Investing in certified machinery not only ensures regulatory adherence but also positions companies as responsible and forward-thinking in an increasingly environmentally conscious world, enhancing brand image and market credibility.
Deciphering Essential Certifications for Sustainable Operations
The array of certifications can seem complex, but each plays a crucial role in validating different aspects of machine performance and environmental impact. Breaking down these certifications into categories helps clarify their importance and guides businesses in ensuring comprehensive compliance. Certifications can be broadly categorized into safety, quality management, and environmental performance. Each category addresses distinct but interconnected aspects of responsible machine operation, as detailed below:
Certification Category | Certification Example | Focus | Environmental Relevance | Business Benefit |
---|---|---|---|---|
Safety | CE Marking | Health, Safety, Environmental Protection (EEA) | Ensures machine meets EU environmental directives | Legal market access in EEA, reduced risk of accidents |
UL Certification | Electrical Safety (North America) | Minimizes electrical hazards, indirectly reducing risks | Assurance of safety, enhanced reputation, market access | |
Quality | ISO 9001 | Quality Management Systems | Consistent product quality, efficient processes | Improved operational efficiency, customer trust, quality assurance |
Environmental | ISO 14001 | Environmental Management Systems | Comprehensive environmental management, resource efficiency | Enhanced environmental performance, regulatory compliance, image |
ENERGY STAR | Energy Efficiency | Reduced energy consumption, lower carbon footprint | Lower operating costs, energy savings, sustainability image | |
RoHS Compliance | Restriction of Hazardous Substances | Minimizes hazardous materials in machine components | Safer manufacturing, compliance with environmental directives |
Conclusion
Reducing waste in steel coil packing is a multifaceted endeavor that yields significant environmental and economic benefits. By optimizing material usage, embracing eco-friendly materials, ensuring proper tension control, and adhering to machine certifications, industries can achieve substantial waste reduction and enhance their sustainability. These practices not only minimize environmental impact but also improve operational efficiency, reduce costs, and build a stronger, more responsible brand image in the global marketplace. Embracing these strategies is crucial for businesses aiming to thrive in an increasingly sustainable and competitive world.