1. How to Prevent Corrosion in Steel Wire Packing?
Steel wire packing, essential for securing and transporting goods, is vulnerable to corrosion, especially when exposed to harsh environmental conditions. Rust can compromise the integrity of the wire, leading to package failure and product damage. Understanding how to prevent corrosion is crucial for maintaining the quality and safety of packed items. Implementing effective strategies can significantly extend the lifespan of steel wire packing and protect against costly replacements.
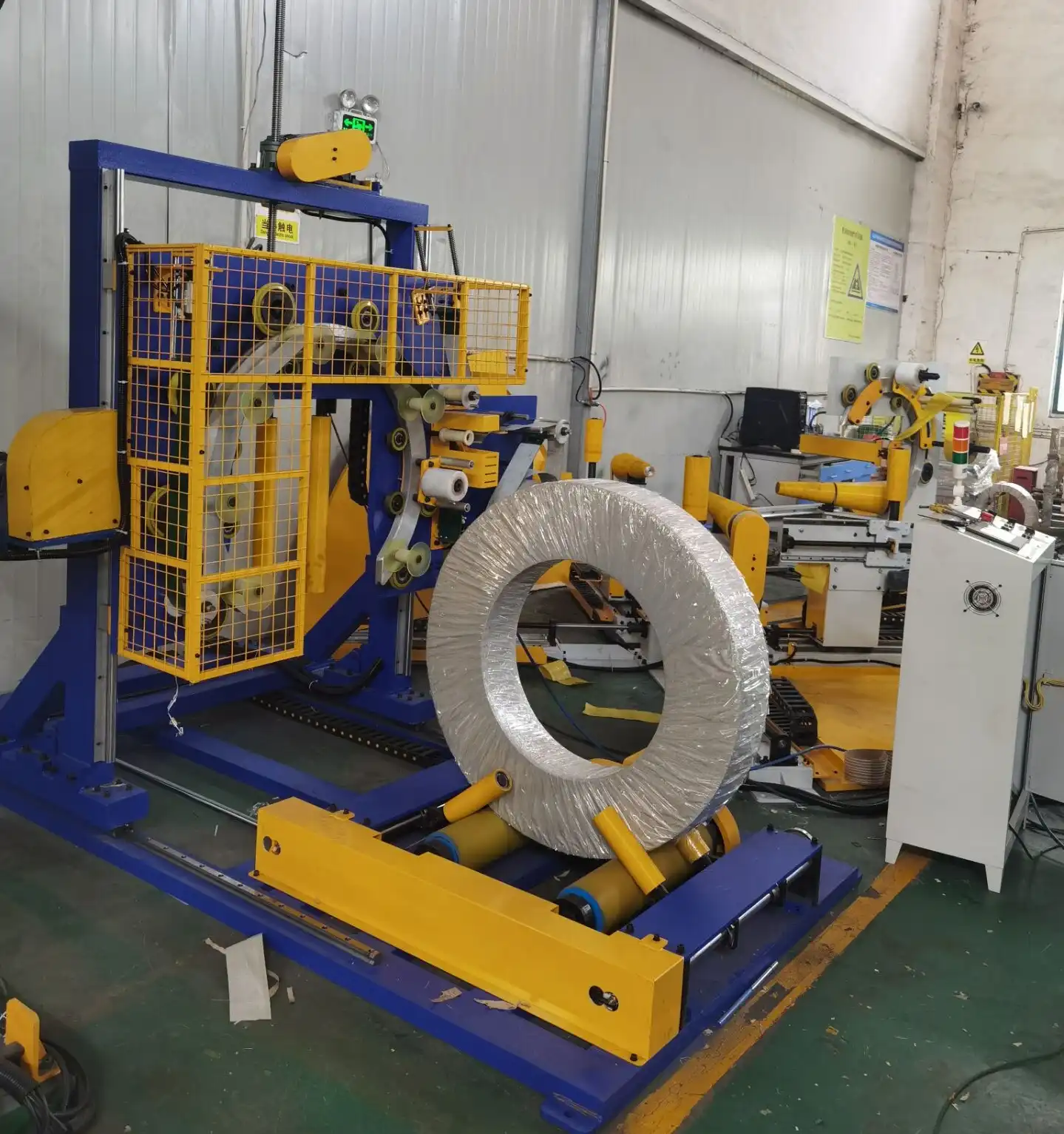
To prevent corrosion in steel wire packing, apply protective coatings such as rust inhibitors or paints, ensure proper storage in dry environments, and use vapor corrosion inhibitors (VCIs) within the packaging. Regular inspection and maintenance of the wire packing are also vital. Selecting corrosion-resistant steel alloys for the wire itself offers a proactive, long-term solution against rust and degradation.
Effective corrosion prevention in steel wire packing not only safeguards the packaged goods but also contributes to operational efficiency. By proactively addressing corrosion risks, businesses can minimize downtime, reduce material waste, and ensure the reliable delivery of their products. Let’s delve into the essential methods and best practices for keeping your steel wire packing corrosion-free.
2. Understanding the Causes of Corrosion in Steel Wire Packing
Steel wire packing, while robust, is susceptible to corrosion due to several interacting factors. Moisture is a primary culprit, acting as an electrolyte to facilitate the electrochemical reactions that lead to rust. Exposure to oxygen, another key element in the corrosion process, further exacerbates the issue. Environmental pollutants, such as acid rain or industrial fumes, can accelerate corrosion by introducing aggressive chemicals.
Corrosion in steel wire packing is primarily caused by exposure to moisture and oxygen, which triggers oxidation. Environmental factors like humidity, salt spray in marine environments, and chemical pollutants significantly accelerate this process. Dissimilar metals in contact can also induce galvanic corrosion. Understanding these causes is the first step in implementing effective prevention strategies to protect steel wire packing and maintain its structural integrity.
To effectively combat corrosion, a comprehensive approach is necessary, addressing each of these contributing elements. This involves not only selecting appropriate protective measures but also understanding the specific environmental challenges that the steel wire packing will face.
Delving Deeper: The Electrochemical Nature of Corrosion and Its Accelerants
Corrosion in steel is an electrochemical process. It requires an anode (where oxidation occurs), a cathode (where reduction occurs), an electrolyte (a conductive medium like water), and a metallic path for electron flow. In the case of steel, iron acts as the anode, losing electrons and forming iron ions (rust).
Factors Accelerating Corrosion
Factor | Description | Impact on Steel Wire Packing |
---|---|---|
Humidity | High levels of moisture in the air increase the electrolyte availability, speeding up the corrosion process. | Promotes rust formation, especially in poorly ventilated storage areas or during humid seasons. |
Salt Spray | Chloride ions from salt, particularly in marine environments or road salt applications, are highly corrosive to steel. | Severely accelerates rust, making steel wire packing in coastal areas or used for shipping susceptible to rapid degradation. |
Chemical Pollutants | Industrial pollutants like sulfur dioxide and nitrogen oxides react with moisture to form acids, increasing the corrosivity of the environment. | Acid rain and chemical fumes can aggressively attack steel, leading to pitting and weakening of the wire packing. |
Temperature Fluctuations | Temperature changes can cause condensation, leading to moisture accumulation even in seemingly dry environments. | Daily temperature cycles, especially in outdoor storage, can create condensation inside packaging, fostering corrosion. |
Galvanic Corrosion | Occurs when dissimilar metals are in electrical contact in the presence of an electrolyte. The more active metal corrodes preferentially. | If steel wire packing is in contact with more noble metals (like copper or brass fittings) in a moist environment, the steel will corrode faster at the contact points. |
Understanding these factors allows for targeted prevention strategies. For instance, in high-humidity environments, dehumidification or barrier coatings become more critical. In marine applications, specialized coatings resistant to chloride attack are essential. By addressing the root causes and accelerants of corrosion, we can significantly enhance the longevity of steel wire packing.
3. Effective Methods for Corrosion Prevention in Steel Wire Packing
Preventing corrosion in steel wire packing requires a multi-faceted approach, incorporating material selection, protective barriers, and environmental controls. The chosen methods should align with the specific application and environmental conditions the wire packing will encounter. From applying coatings to employing advanced packaging techniques, numerous effective strategies exist.
Several methods effectively prevent corrosion in steel wire packing. Applying protective coatings like paints, oils, or specialized anti-rust compounds creates a barrier against moisture and oxygen. Utilizing Vapor Corrosion Inhibitors (VCIs) within packaging releases corrosion-inhibiting vapors. Proper storage in dry, well-ventilated areas and regular maintenance, including cleaning and inspections, are also crucial for long-term corrosion prevention.
Selecting the most appropriate combination of these methods depends on factors such as the duration of storage or transit, the environmental severity, and cost considerations. Let’s explore these methods in detail to determine the best approach for your specific needs.
Exploring Protective Strategies: Coatings, Inhibitors, and Environmental Controls
A robust corrosion prevention strategy typically involves a combination of the following approaches:
3.1 Protective Coatings
Coatings form a physical barrier between the steel and the corrosive environment. Various types are available, each with specific advantages:
- Barrier Coatings: Paints, varnishes, and lacquers are common barrier coatings. They are cost-effective and can provide good protection in mildly corrosive environments. For enhanced performance, consider epoxy or polyurethane-based paints, known for their durability and chemical resistance. These coatings are directly applied to the steel wire packing.
- Metallic Coatings: Galvanizing (zinc coating) and plating with metals like chromium or nickel provide excellent corrosion resistance. Galvanization is particularly effective as zinc acts as a sacrificial anode, corroding preferentially to protect the steel. Metallic coatings are typically applied during the wire manufacturing process.
- Conversion Coatings: Phosphate and chromate conversion coatings react with the steel surface to form a protective layer. These are often used as pretreatments before painting to improve adhesion and corrosion resistance.
3.2 Corrosion Inhibitors
Corrosion inhibitors are substances that reduce the rate of corrosion when added to an environment. In steel wire packing, Vapor Corrosion Inhibitors (VCIs) are particularly useful.
- Vapor Corrosion Inhibitors (VCIs): VCIs release chemicals that create a protective layer on the metal surface, inhibiting electrochemical reactions. They are available in various forms like papers, films, emitters, and liquids. VCIs are ideal for enclosed packaging, protecting even hard-to-reach areas. The wire packing machine can be used to apply VCI films or papers during the wrapping process for efficient and consistent protection.
3.3 Environmental Controls
Controlling the environment surrounding the steel wire packing is crucial in minimizing corrosion.
- Humidity Control: Maintaining low humidity levels is paramount. Dehumidifiers in storage areas and desiccants within packaging can effectively reduce moisture.
- Temperature Management: Avoiding extreme temperature fluctuations minimizes condensation. Insulated storage or temperature-controlled environments can be beneficial.
- Ventilation: Proper ventilation prevents the build-up of humidity and corrosive fumes. Well-ventilated storage spaces are essential, especially in enclosed warehouses.
- Cleanliness: Keeping the steel wire packing clean and free from contaminants like dirt, salts, and industrial residues reduces corrosion initiation sites. Regular cleaning before storage or shipment is advisable.
By strategically combining these protective coatings, corrosion inhibitors, and environmental controls, a comprehensive corrosion prevention plan can be tailored to the specific demands of steel wire packing applications, ensuring long-term protection and reliability.
4. Implementing a Corrosion Prevention Plan for Steel Wire Packing
Creating and implementing a robust corrosion prevention plan for steel wire packing involves several key steps, from initial assessment to ongoing monitoring. A well-structured plan ensures consistent protection and minimizes the risk of corrosion-related failures. This proactive approach saves costs in the long run and maintains product integrity.
To implement a corrosion prevention plan for steel wire packing, first assess the environmental risks and storage conditions. Select appropriate corrosion prevention methods like coatings or VCIs based on the assessment. Train personnel on proper handling and storage procedures. Regularly inspect wire packing for signs of corrosion and maintain protective measures. Documentation and record-keeping are essential for tracking effectiveness and making adjustments as needed.
A successful plan is not static; it requires regular review and adjustments based on performance and changing environmental conditions. Let’s outline the critical stages in developing and executing such a plan.
Key Steps in a Corrosion Prevention Plan:
-
Risk Assessment:
- Identify Corrosion Risks: Analyze the environment where the steel wire packing will be stored and transported. Consider factors like humidity, temperature variations, exposure to salt spray, chemical pollutants, and duration of storage/transit.
- Assess Sensitivity: Determine the criticality of corrosion prevention based on the value of the packed goods and the potential consequences of corrosion damage.
-
Method Selection:
- Choose Protective Coatings: Based on the risk assessment, select appropriate coatings (barrier, metallic, or conversion coatings). Consider factors like cost, durability, application method, and environmental regulations.
- Select Corrosion Inhibitors: Decide if VCIs are necessary and choose the appropriate type (papers, films, emitters) and concentration based on packaging volume and protection duration.
- Environmental Controls: Outline measures for humidity control, temperature management, ventilation, and cleanliness in storage and handling areas.
-
Implementation:
- Coating Application Procedures: Establish standardized procedures for applying coatings, ensuring proper surface preparation, coating thickness, and curing times.
- VCI Deployment: Integrate VCI application into the packing process, ideally using automated systems like wire packing machines for consistency.
- Environmental Control Measures: Set up dehumidifiers, ventilation systems, and temperature monitoring devices in storage areas. Implement cleaning schedules and protocols.
- Training: Train personnel on proper handling procedures, application of protective measures, and identification of corrosion signs.
-
Monitoring and Maintenance:
- Regular Inspections: Implement a schedule for inspecting steel wire packing for signs of corrosion. Document inspection findings, including location and severity of rust.
- Maintenance Procedures: Establish protocols for addressing minor corrosion issues promptly, such as cleaning and re-application of coatings. Replace severely corroded wire packing.
- Performance Evaluation: Periodically review the effectiveness of the corrosion prevention plan. Analyze inspection data, customer feedback, and any instances of corrosion-related issues to identify areas for improvement.
-
Documentation and Record-Keeping:
- Plan Documentation: Document the entire corrosion prevention plan, including risk assessment, method selection, implementation procedures, monitoring schedules, and maintenance protocols.
- Inspection Records: Maintain detailed records of all inspections, including dates, findings, and corrective actions taken.
- Material Tracking: Keep records of coatings, VCIs, and other protective materials used, including batch numbers and application dates.
By systematically following these steps, businesses can establish a proactive and effective corrosion prevention plan for steel wire packing, safeguarding their products and operational efficiency.
Conclusion
Preventing corrosion in steel wire packing is an essential aspect of maintaining material integrity and operational efficiency. By understanding the causes of corrosion and implementing effective prevention methods, businesses can significantly reduce the risk of damage and extend the lifespan of their wire packing. From selecting appropriate protective coatings and utilizing vapor corrosion inhibitors to controlling environmental factors and establishing a robust prevention plan, a comprehensive approach is key. Investing in these strategies not only safeguards products but also contributes to long-term cost savings and enhanced reliability in packaging and transportation processes.