1. How to Optimize PVC Pipe Bagging Machine Performance for Cold Chain Operations?
In cold chain operations, maintaining product integrity is paramount. For PVC pipe bagging machines, optimization is not just about speed but ensuring bagged pipes withstand cold chain rigors. This involves precise adjustments and material considerations to guarantee performance and protection in low-temperature environments.
To optimize PVC pipe bagging machine performance for cold chain operations, focus on temperature-resilient materials, adjust machine settings for low temperatures to prevent brittleness and ensure seal integrity, and implement rigorous quality checks to confirm bagging effectiveness under cold chain conditions. This ensures pipes are securely packaged and protected throughout the cold chain.
Transitioning from general performance to cold-chain specific optimization requires a deeper dive into the critical factors that influence bagging machine efficiency and reliability in low-temperature environments. Let’s explore these aspects to ensure your operations are robust and effective.
2. Material Selection for Cold Chain PVC Pipe Bagging
Choosing the right bagging material is crucial in cold chain operations. Standard PVC bagging films may become brittle and lose their protective properties at lower temperatures. Selecting materials specifically designed for cold environments is the first step in optimizing machine performance.
For cold chain PVC pipe bagging, opt for bagging films formulated for low temperatures, such as specialized polyethylene blends or laminates, which maintain flexibility and strength, preventing tears and ensuring seal integrity even in sub-zero conditions. These materials are engineered to resist cold-induced brittleness, crucial for effective cold chain packaging.
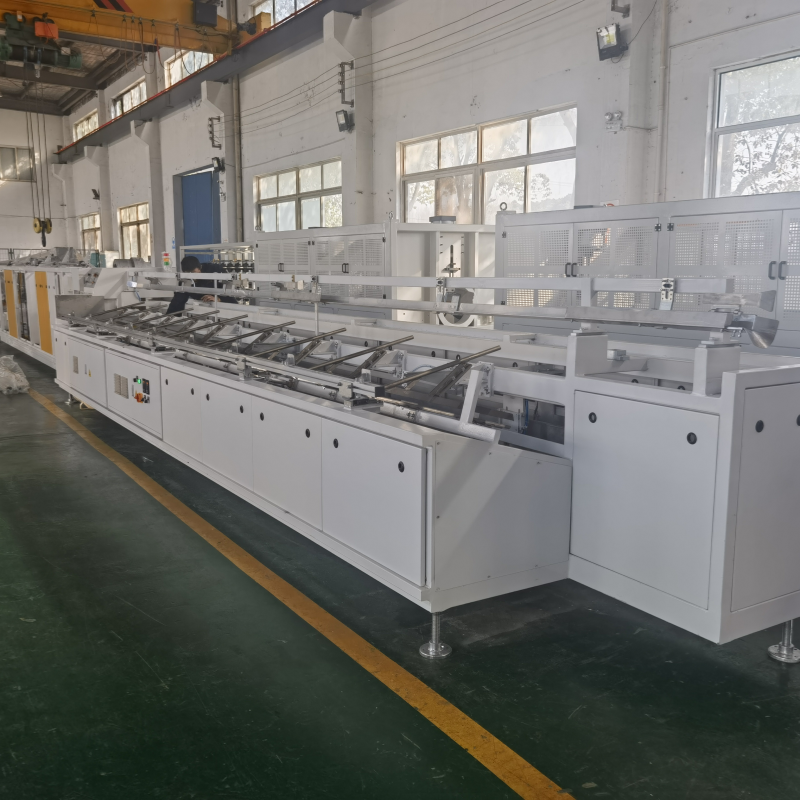
The Impact of Temperature on Bagging Film Properties
Low temperatures drastically alter the characteristics of plastic films. Understanding these changes is vital for material selection and machine adjustment.
Property | Impact of Low Temperature | Consequence for Bagging |
---|---|---|
Flexibility | Decreases, film becomes stiffer and less pliable | Difficult to form bags, increased risk of tearing during sealing |
Tensile Strength | Can increase initially but becomes brittle at extreme lows | Higher chance of film cracking or breaking under stress |
Seal Integrity | Reduced heat sealability, seals become weaker and prone to failure | Compromised package integrity, potential for leaks or breaks |
Impact Resistance | Significantly decreases, film becomes more fragile | Bags more susceptible to punctures and damage during handling |
To counter these effects, specialized cold-resistant films are formulated with additives that maintain flexibility and impact resistance at low temperatures. These films often include:
- Low-Temperature Additives: Plasticizers and polymers that lower the glass transition temperature of the film, keeping it flexible.
- Enhanced Polymer Blends: Combinations of polyethylene (PE), polypropylene (PP), and other polymers tailored for cold conditions.
- Laminated Structures: Multi-layer films with an outer layer for strength and an inner layer optimized for low-temperature sealing.
Selecting the appropriate cold-resistant film is not merely about avoiding breakage; it’s about ensuring the bagging process remains efficient and reliable without compromising the protective barrier essential for cold chain integrity. This upfront material choice directly influences the downstream performance of the PVC pipe bagging machine in cold environments.
3. Machine Adjustments for Cold Chain Bagging Efficiency
Optimizing a PVC pipe bagging machine for cold chain operations extends beyond material selection to include precise machine adjustments. Cold temperatures affect not only the bagging film but also the machine’s mechanical components and their performance.
To ensure PVC pipe bagging machines operate efficiently in cold chain environments, adjust settings like sealing temperature and pressure, film tension, and cycle speed. Lower temperatures may require increased sealing heat and pressure, while film tension needs careful calibration to prevent breakage. Slower cycle speeds can improve seal quality and reduce stress on cold films. These adjustments counteract the effects of cold on materials and machine mechanics.
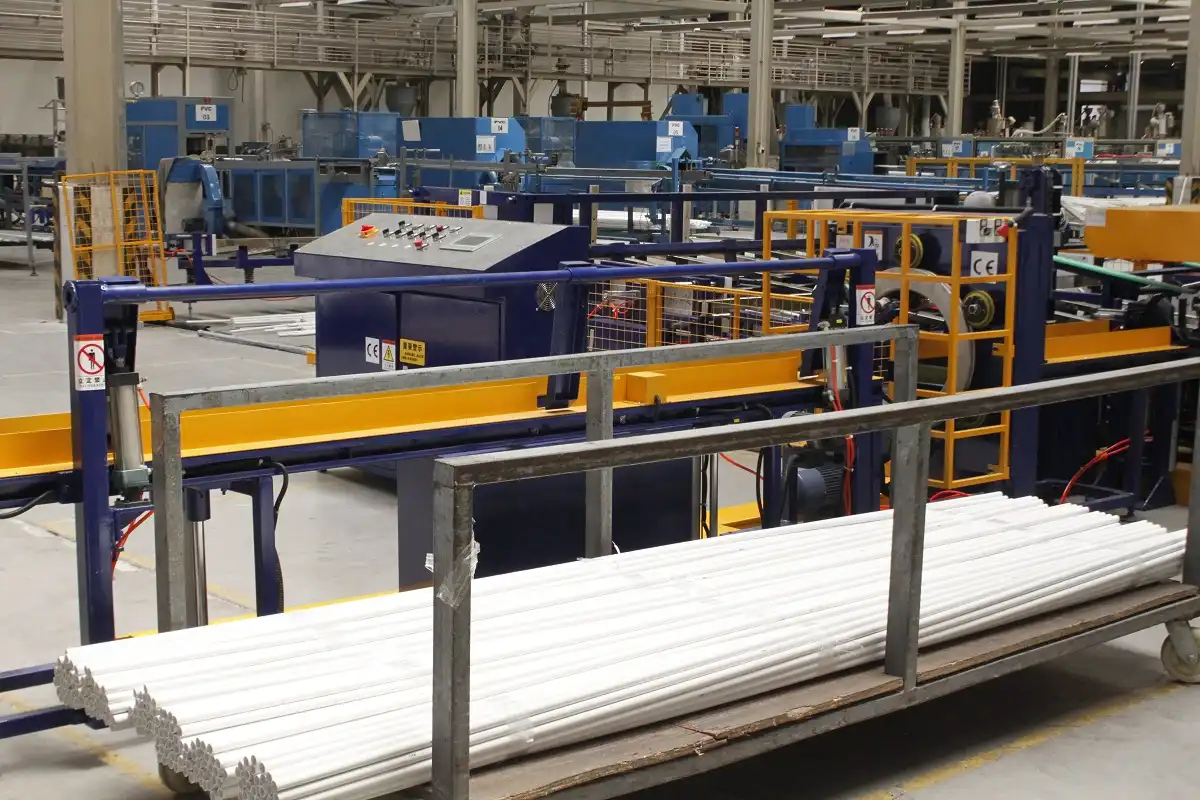
Fine-Tuning Machine Parameters for Cold Environments
Operating bagging machines in cold conditions requires a nuanced approach to machine settings. Generic settings optimized for standard temperatures will likely lead to inefficiencies and potential failures in cold chain scenarios. Key adjustments include:
- Sealing Temperature and Dwell Time: Cold-resistant films may require slightly higher sealing temperatures and longer dwell times to achieve a robust seal. Experimentation and testing are crucial to find the optimal balance. Too much heat can damage the film, while insufficient heat results in weak seals.
- Sealing Pressure: Increased sealing pressure might be necessary to compensate for the reduced conformability of cold films. However, excessive pressure can also lead to film distortion or breakage. Careful calibration is essential.
- Film Tension Control: Cold films tend to be less elastic and more prone to tearing under tension. Reduce film tension settings to prevent breakage during unwinding and bag formation. Precise tension control mechanisms are highly beneficial in cold environments.
- Cycle Speed: Slowing down the bagging cycle speed can improve seal quality and reduce mechanical stress on the film and machine components. While this might slightly reduce throughput, it enhances reliability and minimizes waste due to bagging failures.
- Pneumatic System Adjustments: If the machine uses pneumatic systems, cold air can affect performance. Ensure air lines are insulated and consider using air dryers to prevent moisture buildup and freezing in the system. Lubricants in pneumatic components may also need to be cold-resistant.
By meticulously adjusting these parameters, operators can ensure the PVC pipe bagging machine functions reliably and efficiently, producing consistently sealed and robust bags even under the challenging conditions of cold chain operations. This proactive approach minimizes downtime, reduces material waste, and safeguards product integrity.
4. Operational Best Practices for Cold Chain PVC Pipe Bagging
Beyond material and machine adjustments, operational practices play a vital role in optimizing PVC pipe bagging machine performance in cold chain environments. Consistent procedures and trained personnel are essential for maintaining efficiency and quality.
Effective operational practices for cold chain PVC pipe bagging include pre-warming bagging film before use to improve flexibility, regular machine inspections to detect and address cold-related issues, and training personnel on cold-specific operational adjustments and quality control procedures. These practices ensure consistent performance and minimize disruptions in cold chain bagging.
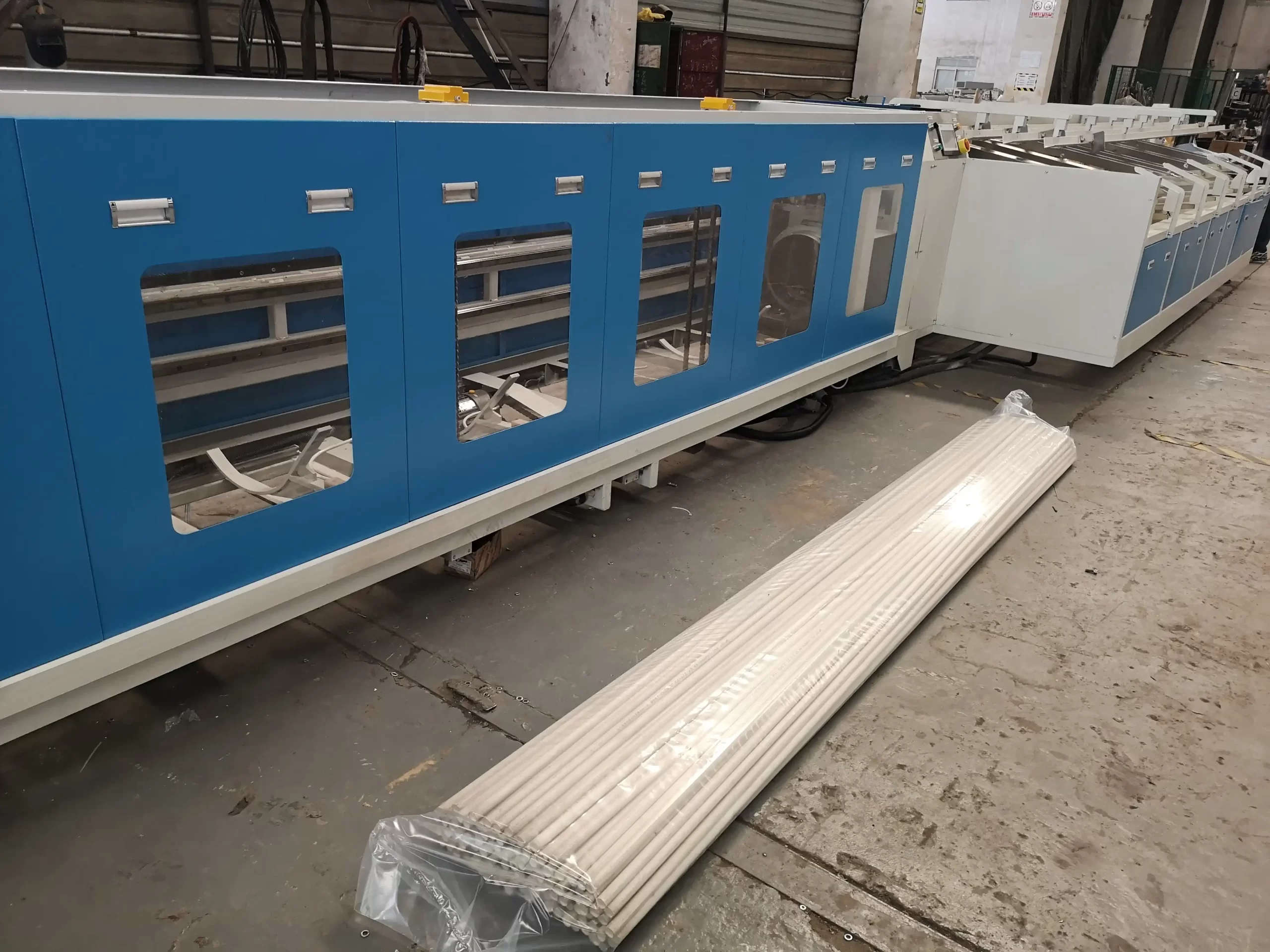
Implementing Cold Chain Specific Procedures
To maintain optimal performance and minimize issues in cold chain PVC pipe bagging operations, consider these best practices:
- Film Pre-Conditioning: Store bagging films in a slightly warmer environment prior to use, if feasible. This can help improve film flexibility and reduce the risk of cracking or tearing during the initial stages of bagging, especially when starting operations after a cold shutdown.
- Regular Machine Warm-up: Before commencing full-speed operations, run the bagging machine at a slower pace for a warm-up period. This allows mechanical components to reach operating temperature gradually, reducing stress and wear, especially on lubricants and moving parts sensitive to cold.
- Increased Frequency of Inspections: Implement more frequent machine inspections, particularly focusing on seals, film tension, and pneumatic systems. Cold can exacerbate minor issues, so early detection is crucial. Check for condensation, ice buildup, and any signs of material fatigue more often than in standard temperature operations.
- Enhanced Quality Control: Increase the rigor of quality control checks on finished bags. Cold seals can sometimes appear visually sound but be weaker. Implement peel tests or burst tests at regular intervals to verify seal integrity.
- Operator Training on Cold Chain Protocols: Train machine operators specifically on the nuances of cold chain bagging. This includes understanding cold-resistant film properties, recognizing signs of cold-related machine issues, and performing necessary adjustments or reporting problems promptly. Training should also cover emergency procedures for cold weather breakdowns.
- Preventative Maintenance Scheduling: Adjust preventative maintenance schedules to account for the increased stress cold environments can place on machinery. More frequent lubrication, inspection of wear parts, and checks on heating elements and sensors may be necessary.
- Environmental Monitoring: If the bagging area is not fully climate-controlled, monitor the temperature and humidity levels. Extreme fluctuations can impact both machine performance and film properties. Consider using localized heating or dehumidification if necessary to stabilize the immediate bagging environment.
By integrating these operational best practices, facilities can significantly enhance the reliability and efficiency of PVC pipe bagging machines in cold chain settings, ensuring consistent packaging quality and minimizing operational disruptions due to cold weather challenges.
5. Maintenance and Monitoring for Sustained Cold Chain Performance
Sustaining optimized performance in cold chain PVC pipe bagging requires a robust maintenance and monitoring regime. Regular upkeep prevents breakdowns, while continuous monitoring allows for proactive adjustments and issue resolution.

Effective maintenance and monitoring are crucial for long-term cold chain PVC pipe bagging machine performance. This includes scheduled maintenance, real-time performance monitoring, and data-driven optimization strategies to ensure consistent and reliable operation.
To maintain optimal PVC pipe bagging machine performance in cold chain operations, implement a rigorous preventative maintenance schedule focusing on cold-sensitive components, utilize real-time monitoring systems to track key performance indicators, and analyze data to identify trends and proactively address potential issues. Regular calibration and timely parts replacement are also essential.
Maintenance Task | Frequency | Cold Chain Focus | Benefit |
---|---|---|---|
Lubrication | Weekly/Daily | Use low-temperature lubricants; check more frequently in extreme cold. | Prevents component wear and ensures smooth operation in cold. |
Seal Bar Inspection | Weekly | Check for wear, damage, and proper heating element function. | Maintains consistent seal quality and prevents seal failures. |
Film Tension System Check | Weekly | Calibrate tension sensors; inspect rollers for wear and free movement. | Prevents film breakage and ensures accurate bag formation. |
Pneumatic System Service | Monthly | Drain moisture traps; check for leaks and proper pressure; inspect air lines. | Ensures reliable pneumatic operation and prevents freeze-ups. |
Sensor Calibration | Quarterly | Calibrate temperature, pressure, and position sensors for accurate readings. | Maintains precise machine control and consistent bagging parameters. |
Electrical System Inspection | Annually | Check wiring, connections, and heating elements for corrosion or damage due to cold. | Prevents electrical failures and ensures safe and reliable operation. |
Beyond scheduled maintenance, real-time monitoring systems can provide immediate insights into machine performance. Key metrics to monitor include:
- Cycle Time: Track cycle times to identify slowdowns that might indicate mechanical issues or material feed problems.
- Seal Temperature Consistency: Monitor seal bar temperature to ensure it remains within the optimal range, especially as ambient temperatures fluctuate.
- Film Breakage Frequency: Record instances of film breakage to identify potential issues with film quality, tension settings, or machine components.
- Downtime Events: Log all downtime events, categorizing them by cause (e.g., mechanical failure, film jams, electrical issues). Analyze downtime data to pinpoint recurring problems and prioritize maintenance efforts.
By combining preventative maintenance with proactive monitoring and data analysis, operators can ensure PVC pipe bagging machines consistently deliver high performance and reliability, minimizing downtime and maximizing efficiency in demanding cold chain operations. This data-driven approach enables continuous improvement and long-term optimization of bagging processes.
6. Conclusion
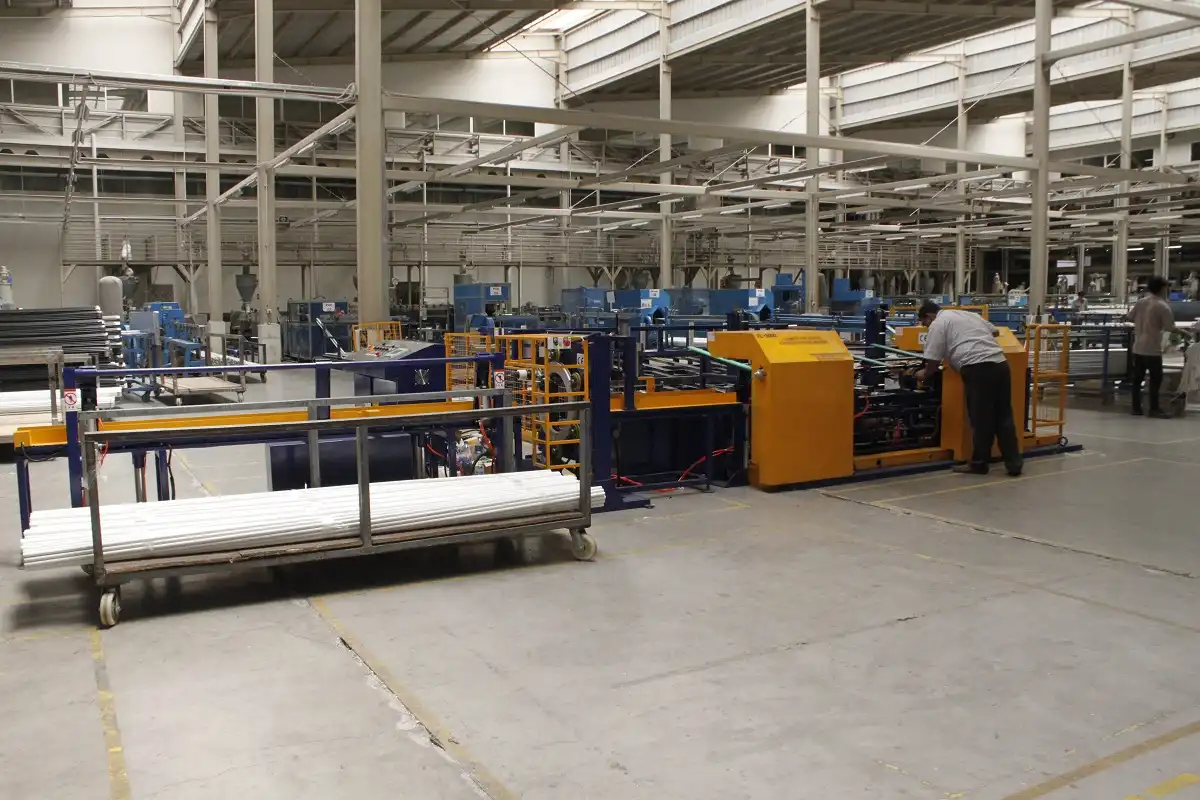
Optimizing PVC pipe bagging machine performance for cold chain operations is a multifaceted endeavor. It demands careful material selection, precise machine adjustments, diligent operational practices, and a robust maintenance regime. By focusing on these key areas, businesses can ensure their bagging processes are not only efficient but also reliably protect PVC pipes throughout the rigors of the cold chain. This comprehensive approach minimizes product damage, reduces operational downtime, and ultimately enhances the overall effectiveness of cold chain logistics for PVC pipe products.