1. How to Meet Customized Demands for Steel Wire Packing?
Steel wire packing is crucial for ensuring product integrity and efficient logistics. Manufacturers face increasing pressure to customize packing solutions to meet diverse client needs, including varying wire diameters, coil sizes, and packaging materials. Addressing these demands effectively is key to maintaining competitiveness.
Meeting customized demands for steel wire packing involves adopting flexible and automated packaging solutions. This includes investing in machinery that can handle various wire sizes and coil configurations, and offering a range of packaging materials to suit specific client requirements and ensure safe transit and storage.
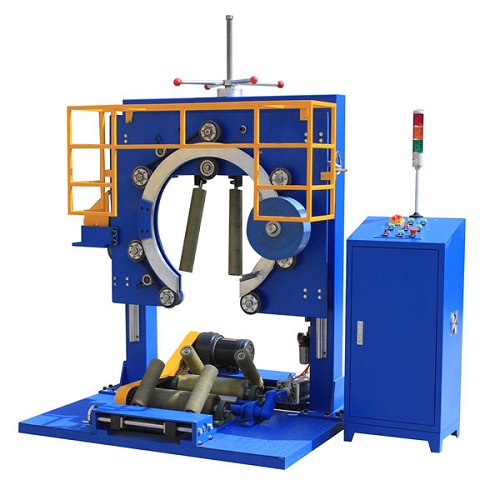
To navigate this complex landscape, steel wire manufacturers need to explore innovative approaches and technologies. This article delves into the strategies and solutions for meeting customized demands in steel wire packing, ensuring efficiency, cost-effectiveness, and customer satisfaction.
2. Understanding the Spectrum of Customized Steel Wire Packing Needs
The steel wire industry is far from monolithic; it encompasses a vast array of applications, from construction and automotive to agriculture and manufacturing. Consequently, the demands for steel wire packing are incredibly diverse, reflecting the specific needs of each sector and end-user. Customization is no longer a luxury but a necessity.
Customized steel wire packing is essential because different clients have unique requirements based on their handling processes, storage conditions, and final applications of the steel wire. Factors like wire gauge, coil weight, environmental exposure, and transportation methods all dictate the ideal packaging solution. Ignoring these nuances can lead to damage, inefficiencies, and ultimately, dissatisfied customers.
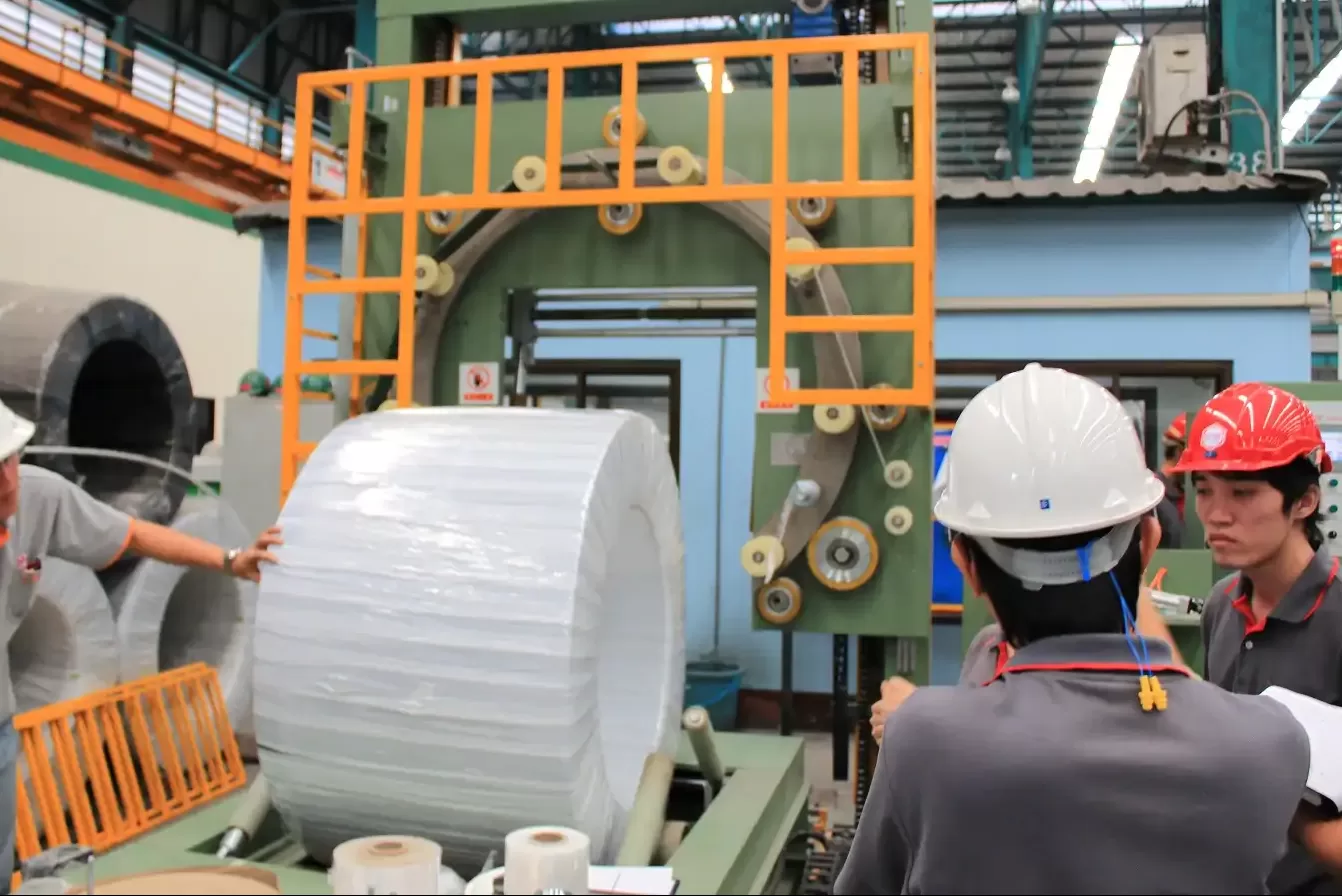
To truly cater to customized demands, manufacturers must move beyond generic packaging and embrace tailored solutions. Let’s examine the key facets of these diverse needs and how manufacturers can effectively respond.
Addressing Varied Wire Dimensions and Coil Sizes
Steel wire comes in a wide range of diameters, from fine strands used in cables to thick gauges for reinforcement. Similarly, coil sizes can vary dramatically, from small, easily manageable coils to massive, heavy coils requiring specialized handling equipment. Packaging solutions must accommodate this dimensional diversity.
Tailoring Packaging to Wire Gauge
The gauge of steel wire directly impacts its flexibility and susceptibility to damage. Finer gauge wires are more delicate and require tighter, more protective packaging to prevent bending, kinking, or breakage during handling and transit. Thicker gauge wires, while more robust, still need secure packing to prevent unwinding and ensure stability.
Wire Gauge Category | Typical Wire Diameter (Approx.) | Packaging Considerations |
---|---|---|
Fine Gauge | < 0.5 mm | High protection, cushioned wrapping, smaller coil sizes |
Medium Gauge | 0.5 – 3 mm | Standard wrapping, moderate protection, medium coil sizes |
Heavy Gauge | > 3 mm | Robust wrapping, strapping, larger coil sizes, secure base |
Accommodating Different Coil Weights and Diameters
Coil weight and diameter are critical factors influencing packaging design. Heavier coils require stronger packaging materials and robust securing methods to withstand the stresses of lifting, moving, and stacking. Larger diameter coils may necessitate specialized wrapping techniques and wider packaging films. Automated wire packing machine solutions offer the flexibility to adjust settings for different coil sizes, ensuring consistent and secure packaging across a product range.
Customizing Packaging Materials for Diverse Client Needs
Beyond dimensions, client needs extend to the types of packaging materials used. Factors like environmental conditions, storage duration, and aesthetic preferences can all influence material selection.
3. Flexible Packaging Machinery: The Cornerstone of Customization
To effectively meet the diverse demands of steel wire packing, flexible and adaptable machinery is paramount. Gone are the days of rigid, one-size-fits-all packaging lines. Modern solutions must offer quick changeovers, adjustable settings, and modular designs to handle a variety of wire types and packaging configurations.
Flexible packaging machinery allows manufacturers to switch between different wire sizes, coil weights, and packaging materials with minimal downtime. This adaptability is crucial for responding to customized orders efficiently and cost-effectively. Machines equipped with programmable logic controllers (PLCs) and servo-driven systems offer the precision and control needed for customized packing processes.
Investing in flexible packaging machinery is not just about meeting current customization demands; it’s about future-proofing operations and gaining a competitive edge in an increasingly dynamic market. Let’s explore the key features and benefits of such systems.
Key Features of Flexible Steel Wire Packing Machines
Flexible steel wire packing machines are characterized by several key features that enable them to handle customized demands effectively. These include:
Quick Changeover Mechanisms
Changeover time is a critical metric in manufacturing. Flexible packaging machines are designed with quick changeover mechanisms to minimize downtime when switching between different wire sizes, coil configurations, or packaging materials. Tool-less changeovers, recipe-driven settings, and modular components all contribute to faster and more efficient transitions.
Adjustable Wrapping and Strapping Parameters
Customization often requires adjusting wrapping tension, overlap, and strapping patterns. Flexible machines allow operators to fine-tune these parameters through user-friendly interfaces, ensuring optimal packaging for each specific wire type and coil size. Servo-driven systems provide precise control over film delivery and strapping force, resulting in consistent and reliable packaging quality.
Modular and Scalable Designs
Modular designs offer inherent flexibility. Packaging lines built with modular components can be easily reconfigured or expanded to accommodate changing production needs or new product lines. Scalability is also important, allowing manufacturers to increase capacity as demand grows without requiring a complete overhaul of their packaging infrastructure.
Benefits of Implementing Flexible Packaging Solutions
The benefits of adopting flexible packaging machinery extend beyond simply meeting customization demands. They contribute to overall operational efficiency, cost savings, and improved customer satisfaction.
Benefit | Description | Impact on Customization |
---|---|---|
Reduced Downtime | Faster changeovers and less setup time between different packaging configurations. | Enables quicker response to customized orders and shorter lead times. |
Increased Efficiency | Optimized packaging processes and reduced manual intervention. | Handles diverse packaging requirements without compromising throughput. |
Improved Packaging Quality | Consistent and precise wrapping and strapping, minimizing damage during transit. | Ensures products arrive in optimal condition, regardless of specific packaging needs. |
Cost Savings | Reduced material waste, lower labor costs, and improved throughput contribute to overall cost reductions. | Cost-effectively manages customized packaging without significant price premiums for clients. |
Enhanced Customer Satisfaction | Tailored packaging solutions that meet specific client needs and ensure product protection. | Builds stronger client relationships through responsiveness and attention to detail regarding their specific requirements. |
4. Automation and Smart Technologies for Enhanced Customization
While flexible machinery provides the foundation for customization, automation and smart technologies take it to the next level. Integrating automation into steel wire packing lines streamlines processes, reduces manual labor, and enhances precision and consistency. Smart technologies, such as sensors, data analytics, and IoT connectivity, further optimize operations and enable proactive adjustments to meet evolving demands.
Automation in steel wire packing reduces reliance on manual labor, minimizes errors, and increases throughput. Smart technologies provide real-time data and insights, enabling predictive maintenance, optimized material usage, and proactive adjustments to packaging parameters based on specific client needs or environmental conditions.
The convergence of automation and smart technologies is transforming steel wire packing, making it more efficient, responsive, and customer-centric. Let’s explore specific examples of how these technologies are being applied.
Examples of Automation in Steel Wire Packing
Automation in steel wire packing encompasses various processes, from coil handling and wrapping to labeling and palletizing. Key areas of automation include:
- Automated Coil Handling Systems: Robotic arms or conveyors can automatically load and unload coils onto wrapping machines, eliminating manual lifting and improving safety and efficiency.
- Automatic Wrapping and Strapping Machines: These machines perform the wrapping and strapping processes automatically, ensuring consistent tension and overlap, and reducing material waste.
- Automated Labeling and Identification Systems: Automated systems can apply labels with customized information, such as client-specific codes or handling instructions, ensuring accurate product identification and traceability.
- Robotic Palletizing Solutions: Robots can automatically stack packaged coils onto pallets in optimized patterns, maximizing space utilization and preparing them for efficient warehouse storage or shipment.
The Role of Smart Technologies in Optimizing Customization
Smart technologies add a layer of intelligence to packaging operations, enabling data-driven decision-making and proactive adjustments. Examples include:
- Sensor-Based Monitoring: Sensors can monitor wrapping tension, film usage, and strapping force in real-time, providing data for process optimization and quality control.
- Predictive Maintenance Systems: Data analytics can be used to predict potential machine failures, enabling proactive maintenance and minimizing downtime.
- IoT Connectivity and Remote Monitoring: Packaging machines connected to the Internet of Things (IoT) can be remotely monitored and controlled, allowing for remote diagnostics, software updates, and performance optimization.
- Data-Driven Customization: Client data and order history can be integrated with packaging systems to automatically adjust packaging parameters and material selection based on specific requirements.
5. Partnering for Personalized Solutions: A Collaborative Approach
Meeting customized demands for steel wire packing effectively often requires a collaborative approach. Steel wire manufacturers should partner with packaging machinery suppliers who understand their specific needs and can offer personalized solutions. This partnership should extend beyond simply purchasing equipment; it should involve ongoing support, consultation, and continuous improvement.
To truly meet customized demands, steel wire manufacturers should seek packaging machinery suppliers who act as partners, offering expertise, tailored solutions, and ongoing support. This collaborative approach ensures that packaging systems are not only flexible and automated but also perfectly aligned with the manufacturer’s unique requirements and long-term goals.
By fostering strong relationships with their packaging partners, steel wire manufacturers can navigate the complexities of customization and build a packaging infrastructure that is both efficient and responsive to evolving client needs.
Conclusion
Meeting customized demands for steel wire packing is no longer optional; it’s a critical factor for success in today’s competitive market. By understanding the diverse needs of clients, investing in flexible and automated packaging machinery, and embracing smart technologies, steel wire manufacturers can create packaging solutions that are both efficient and customer-centric. Partnering with experienced packaging suppliers is crucial to developing and implementing personalized solutions that drive operational excellence and enhance customer satisfaction, ensuring long-term growth and competitiveness in the steel wire industry.