How to Improve the Efficiency of Mold Flippers?
In today’s fast-paced manufacturing environment, optimizing every process is crucial for staying competitive. Mold flipping, often a manual and time-consuming task, presents a significant opportunity for improvement. By adopting the right strategies and technologies, manufacturers can dramatically enhance the efficiency of their mold flipping operations.
To improve the efficiency of mold flippers, manufacturers should automate the process using mold flipping machines. These machines reduce manual labor, minimize handling time, enhance safety, and ensure consistent and precise mold turning. Integrating these automated solutions streamlines workflows, reduces downtime, and significantly boosts overall production efficiency.
Are you looking to streamline your manufacturing processes and eliminate bottlenecks? Discover how automating your mold flipping can revolutionize your production line and give you a competitive edge. Continue reading to explore proven methods for boosting your mold flipping efficiency.
1. How Does a Mold Flipping Machine Operate in Manufacturing?
Manufacturing often involves handling heavy molds, a task traditionally fraught with inefficiencies and safety concerns. Manual mold flipping is labor-intensive, slow, and prone to errors, hindering overall production. Fortunately, a mold flipping machine offers a streamlined solution, automating this critical process and significantly enhancing operational workflows.
A mold flipping machine operates through automated mechanisms to safely and precisely turn heavy molds 180 degrees. It grips the mold securely and rotates it smoothly, eliminating the need for manual handling. This automation reduces turnaround times, minimizes the risk of human error and workplace injuries, and seamlessly integrates into existing manufacturing setups to boost efficiency.
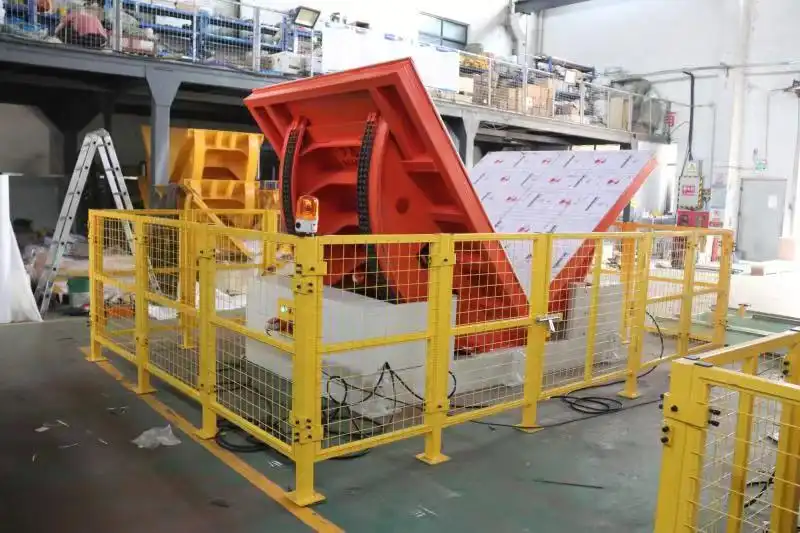
Delving Deeper into Mold Flipping Machine Operations
The integration of industrial mold flippers represents a transformative shift towards achieving operational excellence in manufacturing. To fully appreciate their impact, it’s essential to delve into the mechanics and advantages these machines offer. Let’s break down how these machines function and why they are indispensable in modern manufacturing.
Core Operational Mechanisms
At the heart of a mold flipping machine lies automated technology designed to minimize manual intervention and maximize safety. These machines typically employ hydraulic or mechanical systems to grip and rotate molds. The process generally involves:
- Securing the Mold: The mold is placed onto the machine platform, where clamping mechanisms or vacuum systems securely hold it in place. This secure grip is crucial for handling heavy loads safely and preventing any slippage during rotation.
- Controlled Rotation: Once secured, the machine initiates a smooth and controlled 180-degree rotation. This rotation is powered by hydraulic cylinders or robust mechanical drives, ensuring precision and stability throughout the turning process.
- Precise Positioning: After rotation, the mold is precisely positioned and released, ready for the next stage of the manufacturing process. This precise positioning is vital for maintaining workflow continuity and minimizing downtime.
Benefits of Automated Operation
Automating mold flipping offers a plethora of benefits compared to manual methods. Consider the following advantages quantified in a comparative analysis:
Key Metric | Manual Flipping | Automated Mold Flipping | Improvement |
---|---|---|---|
Time to Flip a Mold | ~30 minutes | ~5 minutes | 83% Reduction |
Labor Risk | High | Low | Significant Reduction |
Consistency of Mold Positioning | Variable | Consistent | Enhanced Precision |
Downtime Reduction | Negligible | Significant | Substantial Gain |
These metrics underscore the significant gains in efficiency, safety, and consistency achieved through automation. The reduction in time and labor risk alone justifies the investment in mold flipping machinery for many manufacturing operations. Furthermore, consistent mold positioning and downtime reduction contribute directly to enhanced product quality and throughput. In essence, mold flipping machines are not merely about speeding up a process; they are about transforming manufacturing hurdles into opportunities for optimization and growth.
2. What Are the Primary Benefits of Using a Mold Flipper?
In the pursuit of manufacturing excellence, efficiency and safety are paramount. Mold flippers emerge as a pivotal solution, offering a range of benefits that directly address these critical needs. Adopting mold flippers is not just about modernization; it’s a strategic move towards operational superiority, significantly impacting productivity and worker safety.
The primary benefits of using a mold flipper include enhanced safety by reducing manual handling, significant improvements in production efficiency through automation, consistent product quality due to precise handling, and substantial time savings in mold turning operations. These benefits collectively contribute to reduced labor costs, minimized downtime, and a more streamlined manufacturing process.
Assessing the Impact of Mold Flippers
To fully appreciate the transformative impact of mold flippers, it’s crucial to evaluate their benefits across various operational aspects. These machines, by automating traditionally risky and labor-intensive tasks, offer quantifiable improvements in safety, efficiency, and overall workflow fluency. Let’s delve deeper into these key areas:
Enhanced Safety in Operations
Manual mold flipping poses considerable safety risks, primarily due to the heavy weight and awkward handling required. Mold flippers drastically reduce these risks by:
- Minimizing Manual Handling: Automation significantly decreases the need for manual lifting and maneuvering of heavy molds, thereby reducing the potential for strains, sprains, and crush injuries.
- Ensuring Controlled Movement: Machines are designed to handle molds with precision and stability, eliminating the unpredictable nature of manual handling which can lead to accidents.
- Promoting a Safer Work Environment: By automating hazardous tasks, companies demonstrate a commitment to worker safety, fostering a more secure and compliant workplace.
The tangible benefits of these safety improvements are substantial, including fewer workplace accidents, reduced injury-related costs, and improved employee morale.
Time Efficiency and Productivity Gains
Efficiency in manufacturing is directly linked to time management. Mold flippers contribute significantly to time savings and productivity increases by:
- Automating Tedious Tasks: Manual mold flipping is time-consuming. Automation drastically reduces the cycle time for mold turning, freeing up valuable production time.
- Streamlining Workflows: Automated systems ensure quicker and more consistent mold handling, leading to smoother production flows and reduced bottlenecks.
- Increasing Throughput: Faster mold turning directly translates to increased production throughput, enabling manufacturers to meet tighter deadlines and handle larger volumes.
Quantitatively, the time saved can be substantial. As highlighted earlier, automated mold flipping can reduce mold turning time from approximately 30 minutes to just 5 minutes. This time saving allows workers to focus on higher-value tasks, further enhancing overall productivity.
Consistent Product Quality
Consistency is a cornerstone of quality manufacturing. Mold flippers ensure consistent product quality through:
- Precise and Repeatable Operations: Automated machines perform mold flipping with consistent precision, eliminating the variability inherent in manual handling.
- Reduced Risk of Damage: Controlled flipping minimizes the chances of molds being damaged during handling, which can impact product quality.
- Improved Mold Longevity: Gentle and precise handling reduces wear and tear on molds, extending their lifespan and maintaining consistent production quality over time.
The consistency afforded by mold flippers translates directly into higher product reliability, fewer defects, and enhanced customer satisfaction. In competitive markets, this consistency is a critical differentiator.
In summary, the adoption of mold flippers is a strategic imperative for manufacturers aiming to enhance safety, boost efficiency, and ensure consistent product quality. These machines are not just productivity tools; they are enablers of operational excellence and sustainable manufacturing practices.
3. How Does 180-Degree Mold Turning Enhance Manufacturing Efficiency?
In the relentless pursuit of manufacturing efficiency, every second saved and every error minimized contributes to a competitive edge. Automating mold turning, specifically 180-degree turns, is a game-changer in this arena. This precise operation is crucial for optimizing cycle times, enhancing precision, and ensuring consistent quality across production lines.
180-degree mold turning enhances manufacturing efficiency by significantly reducing mold handling times and improving precision during production. This automation streamlines the entire manufacturing process, ensures reliable and consistent mold positioning, and improves overall product standards. The efficiency gains achieved make 180-degree mold turning an indispensable component of modern industrial mold flipping.
Delving Into 180-Degree Mold Turning Benefits
To fully grasp the benefits of 180-degree mold turning, it’s essential to examine how these systems augment various production processes and contribute to overall efficiency. These systems bolster manufacturing operations by ensuring molds are flipped accurately and stably, thereby minimizing downtime and enhancing production quality. Let’s explore the key parameters influenced by 180-degree mold turning:
Precision Improvement and Quality Assurance
Precision in mold handling directly impacts product quality. 180-degree mold turning systems ensure:
- Exact Flipping Angles: Automated systems guarantee precise 180-degree turns, maintaining mold form and alignment critical for product accuracy.
- Minimized Human Error: Eliminating manual handling reduces the risk of errors in mold positioning, which can lead to defects and inconsistencies.
- Consistent Product Dimensions: Precise mold handling contributes to consistent cavity filling and uniform part dimensions, reducing variations and improving overall quality.
The outcome of this enhanced precision is a significant reduction in defects, ensuring higher product quality and consistency. This is particularly crucial for industries with stringent quality standards, such as aerospace, medical devices, and high-end electronics.
Cycle Time Reduction and Throughput Enhancement
Time is of the essence in manufacturing. 180-degree mold turning systems contribute to cycle time reduction by:
- Automating Time-Consuming Tasks: Manual mold turning is slow and labor-intensive. Automation drastically reduces the time required for this step, speeding up the overall production cycle.
- Optimizing Workflow: Faster mold turning eliminates bottlenecks and streamlines workflows, allowing for quicker transitions between production stages.
- Increased Throughput: Reduced cycle times directly translate to higher production throughput, enabling manufacturers to produce more parts in less time.
Consider the comparative impact on cycle time:
Parameter | Manual 180-Degree Turn | Automated 180-Degree Turn | Time Savings |
---|---|---|---|
Average Time per Turn | 30 minutes | 5 minutes | 25 minutes/turn |
Turns per Shift (Estimate) | 10 | 60 | 50 additional turns |
Potential Throughput Increase | Baseline | 6x Baseline | Significant Gain |
This table illustrates the dramatic improvement in throughput achievable through automated 180-degree mold turning. The time savings compound over shifts and production cycles, leading to substantial gains in overall production capacity.
Operational Cost Reduction and System Longevity
Efficiency gains extend beyond time savings to include cost reductions and improved system longevity. 180-degree mold turning systems contribute by:
- Minimizing Wear and Tear: Smooth, controlled automated operations reduce mechanical stress on molds and machinery, minimizing wear and tear.
- Lowering Maintenance Expenses: Reduced wear and tear translate to lower maintenance requirements and fewer unexpected breakdowns, decreasing maintenance costs.
- Extending Equipment Lifespan: By minimizing stress and wear, automated systems contribute to a longer lifespan for both molds and handling equipment, representing a significant long-term cost saving.
In conclusion, 180-degree mold turning is not just about flipping molds; it’s about transforming manufacturing processes to achieve peak efficiency, superior product quality, and minimized operational costs. For manufacturers striving for operational excellence and a competitive edge, adopting 180-degree mold turning technology is a strategic imperative.
4. How Can a Mold Flipping Machine Enhance Production Efficiency?
A mold flipping machine can revolutionize your manufacturing process by automating the cumbersome task of mold handling. These machines are designed to safely and efficiently rotate heavy molds, significantly reducing manual labor and the associated risks. By streamlining operations and ensuring precise movements, mold flippers become indispensable tools for enhancing overall production workflows.
A mold flipping machine enhances production efficiency by automating mold turning, which drastically reduces manual labor, speeds up operations, and minimizes downtime. By ensuring precise and consistent 180-degree rotations, these machines optimize workflow continuity, improve safety, and increase overall production capacity. The automation provided by mold flippers directly addresses bottlenecks and elevates the efficiency of the entire manufacturing process.
Diving Deeper: The Mechanics Behind the Efficiency
Understanding how a mold flipping machine enhances production efficiency requires examining its core functionalities and their impact on manufacturing operations. Traditional manual methods of flipping heavy molds are not only labor-intensive but also pose significant risks of worker fatigue and errors. Integrating a mold flipper automates this critical yet repetitive task, leading to substantial improvements across various aspects of production.
Key Components Driving Efficiency
Three main components underpin the efficiency gains provided by mold flipping machines:
-
Automation: The most significant efficiency driver is automation itself. By automating the mold flipping action, manufacturers achieve:
- Reduced Labor Costs: Automation minimizes the need for manual labor, directly cutting down on labor expenses associated with mold handling.
- Minimized Injury Risks: Automating the handling of heavy molds significantly reduces the risk of worker injuries, leading to a safer work environment and lower associated costs from accidents and compensation.
-
Precision and Consistency: Automated systems ensure a level of precision and consistency that manual operations cannot match:
- Exact Mold Positioning: Automated systems guarantee that molds are positioned precisely every time, a level of accuracy difficult to achieve manually. This precision is crucial for consistent product quality and minimizing rework.
- Reduced Error Rates: By eliminating human variability from the mold flipping process, automated machines significantly reduce error rates, leading to fewer defects and higher quality output.
-
Time Efficiency: The speed and reliability of automated mold flipping systems dramatically improve time efficiency:
- Faster Turnaround Times: Mold flipping machines can perform rotations much faster than manual operations, significantly reducing turnaround times for mold-related tasks.
- Increased Production Rates: Faster mold processing directly translates to higher production rates, as more molds can be handled in less time, boosting overall throughput and capacity.
Comparative Analysis: Manual vs. Automated Systems
To quantify the benefits of mold flipping machines, consider a comparative look at manual versus automated systems across key operational aspects:
Aspect | Manual Flipping | Mold Flipping Machine | Efficiency Gain |
---|---|---|---|
Labor Costs | High | Low | Significant Reduction |
Injury Risks | Elevated | Minimal | Substantial Improvement |
Turnaround Time | Slower | Faster | Marked Reduction |
Precision | Variable | High | Enhanced Consistency |
Production Rate | Lower | Higher | Significant Increase |
This comparison clearly illustrates the transformative impact of mold flipping machines on production efficiency. The quantifiable gains in labor costs, safety, turnaround time, precision, and production rate underscore the strategic and financial advantages of adopting automated mold flipping solutions in modern manufacturing environments. Embracing this technology is not just an upgrade; it’s a fundamental shift towards optimized and efficient manufacturing operations.
5. Choosing the Right Mold Flipper for Enhanced Efficiency
Selecting the optimal mold flipper is a pivotal decision that significantly impacts manufacturing efficiency. With a wide array of options available, navigating this choice can seem complex. However, understanding the key considerations will guide you towards the ideal mold flipping device tailored to your specific needs.
When choosing a mold flipper to enhance efficiency, consider factors like mold size and weight capacity, the frequency of mold flipping required, available floor space, and integration with existing systems. Evaluating these aspects ensures you select a mold flipper that streamlines operations, improves safety, and maximizes productivity in your manufacturing environment.
Selecting the right mold flipper involves a detailed assessment of your operational requirements and matching them with the capabilities of different types of mold flipping equipment. Here are key factors to consider:
-
Mold Size and Weight Capacity:
- Assessment: Begin by determining the range of mold sizes and weights you handle. Consider the largest and heaviest molds to ensure the selected flipper can accommodate them safely and efficiently.
- Flipper Specification: Check the manufacturer’s specifications for weight and size limits. Opt for a machine with a capacity that comfortably exceeds your current and anticipated mold dimensions and weights. Overloading a mold flipper can lead to equipment damage and safety hazards.
-
Frequency of Mold Flipping:
- Assessment: Evaluate how often mold flipping is required in your production cycle. High-frequency flipping operations demand robust and reliable machines capable of continuous operation without downtime.
- Flipper Durability and Cycle Time: Look for mold flippers designed for high-duty cycles and offering fast flipping times. Hydraulic systems are generally more durable for frequent use, while faster cycle times directly contribute to increased production throughput.
-
Available Floor Space:
- Assessment: Analyze the available floor space in your manufacturing facility. Some mold flippers are compact and require minimal space, while others are larger and need dedicated areas.
- Flipper Footprint and Design: Choose a mold flipper with a footprint that fits within your allocated space. Consider vertical vs. horizontal designs based on spatial constraints. Vertical mold flippers often save floor space but may require higher ceilings.
-
Integration with Existing Systems:
- Assessment: Consider how the mold flipper will integrate with your current manufacturing processes and systems. Seamless integration minimizes disruptions and maximizes efficiency gains.
- Automation Compatibility and Customization: Opt for mold flippers that can be easily integrated with your existing automation systems, such as conveyors or robotic arms. Inquire about customization options to tailor the flipper to your specific workflow requirements.
-
Safety Features:
- Assessment: Safety should be a top priority. Assess the safety features offered by different mold flippers to protect operators and prevent accidents.
- Safety Standards and Mechanisms: Look for machines equipped with safety sensors, emergency stop buttons, and protective barriers. Ensure the flipper complies with relevant safety standards and regulations.
-
Ease of Use and Maintenance:
- Assessment: Consider the ease of operation and maintenance requirements of the mold flipper. User-friendly machines reduce training time and minimize operational errors.
- User Interface and Maintenance Accessibility: Choose a flipper with an intuitive user interface for easy operation. Ensure that critical components are easily accessible for maintenance and servicing to minimize downtime.
By carefully evaluating these factors, you can select a mold flipper that not only meets your operational needs but also significantly enhances efficiency, safety, and productivity in your manufacturing environment. Investing in the right mold flipping equipment is a strategic step towards achieving operational excellence and maintaining a competitive edge in the market.
Conclusion
Implementing mold flipping machines is a strategic imperative for modern manufacturers aiming to enhance efficiency and safety. By automating mold handling and ensuring precise 180-degree turns, these machines drastically reduce cycle times, minimize manual labor, and improve product quality. The benefits extend to reduced operational costs, minimized downtime, and a safer working environment, making mold flippers indispensable for optimizing manufacturing processes and achieving operational excellence. Embrace mold flipping technology to stay competitive and elevate your production standards.