How to Improve Shock Resistance in Steel Coil Packing?
Protecting steel coils during shipping is paramount to prevent damage and maintain product integrity. Steel coils, while robust, are susceptible to shocks and impacts during transit, which can lead to deformation, surface damage, and rendering the product unusable. Enhancing shock resistance in steel coil packing is not just about reducing losses; it’s about ensuring customer satisfaction and upholding quality standards.
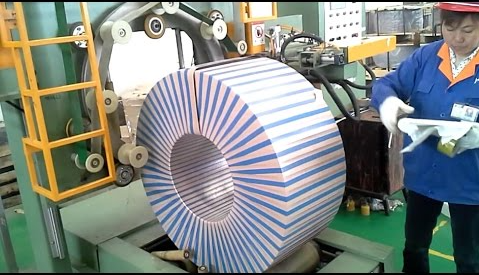
To improve shock resistance in steel coil packing, focus on a holistic approach that includes robust material selection, innovative packaging design, and the integration of protective features. Utilizing high-quality cushioning materials, implementing multi-layered packaging, and employing advanced techniques like floating platforms can significantly enhance protection. Rigorous testing and validation are crucial to confirm the effectiveness of these improvements and ensure damage-free delivery.
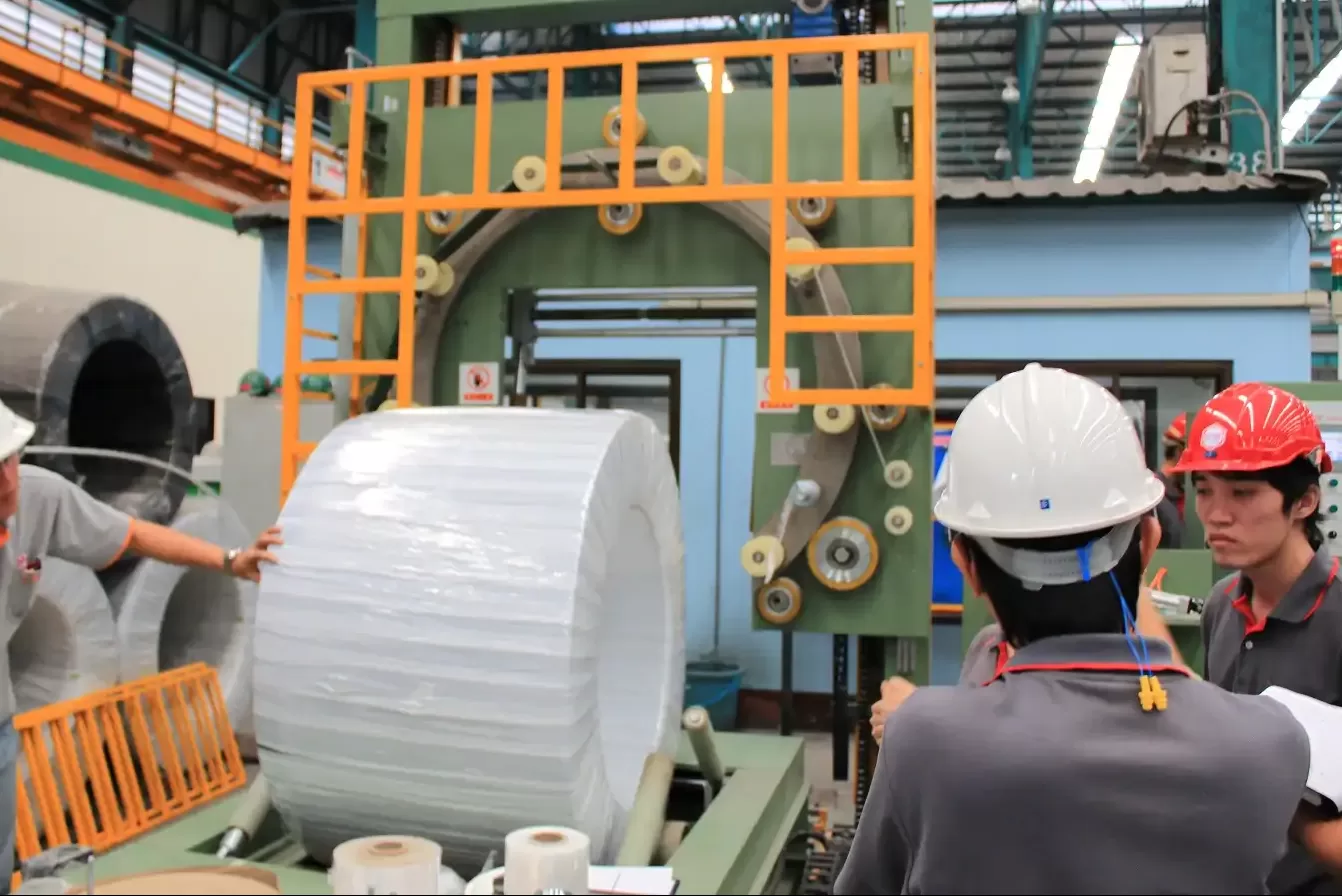
This article delves into practical strategies and advanced techniques to fortify your steel coil packing against shocks, ensuring they arrive in perfect condition. By understanding and implementing these methods, you can significantly reduce transit damage and safeguard your valuable steel products. Let’s explore how to create packaging that truly protects.
1. Selecting Superior Materials for Impact Protection
The foundation of effective impact protection lies in choosing the right materials. Steel coils require packaging that can withstand the harsh conditions of shipping and handling. The selected materials must act as a buffer, absorbing shocks and vibrations to prevent damage to the delicate coil surface and structure.
For optimal impact protection in steel coil packing, a combination of materials is essential. Start with a sturdy base like wooden pallets, then incorporate cushioning materials such as high-density foam, corrugated cardboard, or air pillows to absorb shocks. The outer layer should consist of durable materials like thick plastic films or steel strapping to provide containment and additional protection from external impacts.
To understand material selection more deeply, we need to analyze how different cushioning materials perform under stress. The effectiveness of each material varies based on its inherent properties, thickness, and the specific demands of the steel coil it’s protecting. Let’s examine a comparative analysis of commonly used cushioning materials.
Analyzing Cushioning Material Performance: A Detailed Comparison
Choosing the ideal cushioning material is not a one-size-fits-all decision. It requires careful consideration of factors like coil weight, fragility, transportation conditions, and budget. Here’s a detailed comparison to guide your selection:
Material Performance Matrix
Material Type | Cushioning Ability | Durability | Cost | Best Use Cases |
---|---|---|---|---|
Expanded Polystyrene (EPS) | Excellent | Moderate | Low | Lightweight coils, minimal handling risks |
Polyurethane Foam | Very Good | Moderate | Medium | Medium-weight coils, moderate handling risks |
Corrugated Cardboard | Good | Good | Low | Medium to heavy coils, general protection |
Wood Wool | Moderate | Good | Medium | Heavy coils, robust protection needed |
Air Pillows | Fair | Low | Low | Light coils, void fill, supplementary cushioning |
Deeper Dive into Material Properties
-
Expanded Polystyrene (EPS): EPS is renowned for its exceptional cushioning capabilities due to its cellular structure which effectively absorbs impact energy. Its lightweight nature and low cost make it attractive for large-volume applications. However, EPS is less durable than other options and can be brittle, making it unsuitable for very heavy coils or rough handling conditions.
-
Polyurethane Foam: Polyurethane foam offers a good balance of cushioning and durability. It is more resilient than EPS and provides excellent shock absorption for medium-weight coils. Its moderate cost makes it a versatile option for a wide range of steel coil packing needs. Different densities of polyurethane foam are available, allowing for tailored protection based on the coil’s fragility.
-
Corrugated Cardboard: Corrugated cardboard is a cost-effective and readily available material that provides good cushioning and structural support. Its layered construction offers decent impact resistance, making it suitable for medium to heavy coils. The flute type (A, B, C, E, F) and thickness of the cardboard can be selected to match the protection requirements. It is also a sustainable option due to its recyclability.
-
Wood Wool: Wood wool, composed of long wood shavings, provides moderate cushioning but excels in durability and robustness. It is particularly well-suited for very heavy coils where maximum impact protection is paramount. Wood wool can effectively fill voids and prevent coil shifting within the packaging. While slightly more expensive than cardboard, its superior protection justifies the cost for high-value or extremely heavy steel coils.
-
Air Pillows: Air pillows are primarily used for void fill and supplementary cushioning rather than primary impact absorption. They are lightweight and inexpensive, making them ideal for preventing movement of light coils within the outer packaging. However, their cushioning ability is limited compared to foams or cardboard, and they offer minimal durability against punctures or heavy loads.
The optimal material choice hinges on a detailed assessment of your specific steel coil product, transportation environment, and budget. Carefully weighing the cushioning ability, durability, and cost of each material will ensure you select the most effective and economical solution for shock resistance.
2. Designing Packaging for Enhanced Shock Absorption
Beyond material selection, the design of the packaging itself is crucial for maximizing shock absorption. A well-designed package acts as a system, distributing impact forces and minimizing stress concentration on the steel coil. This involves considering structural elements and incorporating design features that enhance overall protection.
Effective packaging design for shock absorption incorporates multi-layered construction, combining cushioning and rigid layers. Internal supports and dividers prevent coil shifting and distribute weight evenly. External strapping reinforces the structure, while rounded corners on the outer packaging can deflect impacts. The goal is to create a unified, shock-absorbing system that minimizes stress on the steel coil.
To achieve superior shock absorption, especially for sensitive or heavy steel coils, consider advanced packaging design techniques that go beyond basic layering. These methods offer enhanced protection where standard packaging might fall short.
Advanced Packaging Design Techniques: Going Beyond the Basics
For highly sensitive or heavy steel coils, basic layering and strapping may not suffice. Advanced design techniques offer superior shock absorption by precisely controlling coil movement and maximizing cushioning effectiveness.
Advanced Design Feature Breakdown
Design Feature | Function | Benefit | Application Examples |
---|---|---|---|
Floating Platforms | Suspend coil within outer packaging | Isolates coil from direct impacts on the outer box | Delicate wires, sensitive coatings |
Corner & Edge Reinforcements | Strengthen vulnerable points of the package | Prevents crushing and deformation during drops | Heavy coils, long-distance transport |
Customized Inserts | Molded/fitted cushioning for coil shape | Ensures snug fit, prevents movement, maximizes cushioning effect | Coils with irregular shapes, high-value wires |
Pre-compressed Cushions | Materials compressed before packaging | Provides consistent cushioning under load | Heavy coils, predictable shock absorption required |
Coil packing machine Integration | Design packaging compatible with automated lines | Streamlines process, reduces manual handling, improves consistency | High-volume production, automated warehouses |
Detailed Look at Advanced Design Features
-
Floating Platforms: Floating platforms are a highly effective technique for isolating sensitive steel coils. By suspending the coil within the outer packaging, this design feature prevents direct impact forces from reaching the coil. The platform, typically made of rigid material, is supported by cushioning elements, creating a buffer zone that absorbs shocks before they can affect the coil. This is particularly beneficial for delicate wires or coils with sensitive surface coatings that are easily damaged.
-
Corner and Edge Reinforcements: Corners and edges of packaging are inherently vulnerable to damage during handling and drops. Reinforcing these points is crucial for maintaining structural integrity and preventing crushing or deformation. Techniques include using thicker cardboard or plastic at corners, adding protective corner boards, or employing specialized edge protectors made of foam or molded pulp. These reinforcements distribute impact forces away from vulnerable areas, significantly enhancing shock resistance, especially for heavy coils or long-distance transport where packages are subjected to multiple handling events.
-
Customized Inserts: Standard cushioning materials may not always provide optimal protection for coils with irregular shapes or high value. Customized inserts, molded or fitted to the specific coil shape, ensure a snug fit and prevent unwanted movement within the package. These inserts maximize the cushioning effect by providing consistent support and distributing pressure evenly across the coil surface. Materials like molded foam or custom-cut corrugated cardboard can be used to create these tailored solutions, offering superior protection for high-value or uniquely shaped steel coils.
-
Pre-compressed Cushions: For heavy steel coils, maintaining consistent cushioning performance under load is critical. Pre-compressed cushions address this by utilizing materials that are compressed before packaging. This pre-compression ensures that the cushioning material provides predictable and reliable shock absorption even under the weight of the coil. These cushions are particularly useful in applications requiring consistent and predictable shock performance, regardless of load variations.
-
Coil Packing Machine Integration: Designing packaging that is compatible with automated coil packing machine systems offers significant efficiency and consistency benefits. Integrating packaging design with automated lines streamlines the packing process, reduces manual handling, and improves the uniformity of packaging quality. This integration minimizes handling-related shocks and ensures that each package is consistently prepared with the designed shock resistance features, crucial for high-volume production environments and automated warehouses.
Implementing these advanced design techniques, especially floating platforms and customized inserts, provides a significant leap in shock absorption capabilities. By carefully considering these features and integrating them into your packaging design, you can ensure superior protection for even the most sensitive and heavy steel wire coils.
3. Protective Features: Going Beyond Basic Packaging
While material selection and design form the core of shock-resistant packing, additional protective features serve as supplementary safeguards, providing an extra layer of assurance, especially for sensitive steel coil shipments. These features range from simple additions like edge protectors to sophisticated shock monitoring devices.
Protective features for steel coil packing include edge protectors, corner boards, and stretch wrap to reinforce structural integrity. Shock indicators are crucial for monitoring handling during transit, alerting recipients to potential impacts. Vibration dampeners can be incorporated for long journeys, and rust inhibitors protect against environmental factors. These features collectively enhance the package’s ability to withstand and indicate mishandling.
A significant advancement in protective features is the integration of shock monitoring and indicators. These tools provide valuable data about the shocks experienced by the package, enabling accountability and process improvement.
Integrating Shock Monitoring and Indicators: Enhancing Shipment Visibility
Shock monitoring devices and indicators represent a significant step forward in protecting steel coil shipments. They offer real-time or post-transit information about the shocks experienced by the package, allowing for proactive management and continuous improvement of packaging and handling procedures.
Types of Shock Monitoring Devices: A Comparative Overview
Device Type | Functionality | Sensitivity Levels | Cost | Usage Scenario |
---|---|---|---|---|
Shock Indicators | Visual indication of impact exceeding threshold | Pre-set G-levels | Low | General shipments, basic monitoring |
Shockwatch Labels | Tamper-proof visual indicators | Various G-levels | Low-Med | Sensitive goods, accountability for handling |
ShockDot Indicators | Cost-effective, wide range of sensitivities | Broad G-level range | Low | Cost-sensitive shipments, varied fragility levels |
Omni-G Indicators | Resettable, reusable impact detectors | Adjustable G-levels | Medium | Reusable packaging, internal transport |
Data Loggers | Record time, magnitude, duration of shocks | Programmable | High | High-value shipments, detailed impact analysis |
Detailed Functionality and Applications
-
Shock Indicators: Shock indicators are simple, cost-effective devices that provide a visual indication when an impact exceeds a pre-set threshold. These indicators typically change color or activate in some visible manner when subjected to a shock of a certain G-force level. They are ideal for general shipments where basic monitoring is needed and provide immediate visual confirmation of mishandling.
-
Shockwatch Labels: Shockwatch labels are tamper-proof visual indicators that offer a higher level of accountability. Once activated by an impact exceeding the specified G-level, the label provides irreversible evidence of mishandling. Available in various sensitivity levels, Shockwatch labels are well-suited for sensitive goods where clear accountability for handling is required.
-
ShockDot Indicators: ShockDot indicators offer a cost-effective solution with a wide range of sensitivity levels. Their broad G-level range makes them adaptable to various fragility levels and shipment types. These indicators provide a balance of cost-effectiveness and monitoring capability, suitable for cost-sensitive shipments with varied fragility requirements.
-
Omni-G Indicators: Omni-G indicators are resettable and reusable impact detectors, offering a sustainable and versatile monitoring solution. Their adjustable G-levels allow for customization based on the specific sensitivity needs of each shipment. These indicators are particularly beneficial for reusable packaging systems and internal transport applications where repeated monitoring is needed.
-
Data Loggers: Data loggers provide the most comprehensive shock monitoring, recording not only whether an impact occurred but also the time, magnitude, and duration of each shock event. These devices are programmable and offer detailed data for in-depth impact analysis. Data loggers are ideal for high-value shipments where detailed monitoring and analysis are crucial for understanding the conditions experienced during transit and for optimizing packaging and handling processes.
Choosing the right shock monitoring device depends on factors such as the value of the steel coil, its sensitivity to shock, the level of monitoring detail required, and budget considerations. Integrating these protective features enhances not only the safety of the shipment but also provides valuable data for continuous improvement in packaging and handling procedures.
4. Testing and Validation of Shock Resistance
Theoretical design and material selection are essential, but rigorous testing and validation are the final, critical steps in ensuring shock resistance. Real-world testing confirms the packaging’s effectiveness by simulating the shocks and stresses encountered during transportation, ensuring the packaging performs as intended.
Validating shock resistance requires standardized testing procedures. Drop tests from varying heights simulate handling impacts. Vibration tests assess package resilience during transit. Compression tests ensure structural integrity under stacking loads. Impact tests, both horizontal and inclined, mimic transportation shocks. These tests, often guided by ASTM or ISTA standards, provide quantifiable data on packaging performance.
Comprehensive testing procedures, guided by standards like ASTM or ISTA, are vital to validate the shock resistance of steel coil packaging. These procedures provide quantifiable data, confirming the packaging’s ability to protect coils under various stress conditions.
Conclusion
Improving shock resistance in steel coil packing is a multi-faceted process that directly impacts product safety and customer satisfaction. By carefully considering material selection, implementing advanced packaging designs, incorporating protective features like shock indicators, and rigorously testing packaging performance, manufacturers can ensure their steel coils arrive in optimal condition. This comprehensive approach minimizes damage, reduces costs associated with returns and replacements, and ultimately enhances the reliability and reputation of steel coil suppliers in the market. Investing in robust shock-resistant packing is not merely an expense, but a strategic investment in product integrity and customer trust.