1. How to Improve PVC Pipe Bagging Machine Efficiency in Multi-Shift Operations?
In multi-shift PVC pipe production, maximizing bagging machine efficiency is crucial for maintaining output and profitability. Consistent performance around the clock requires a strategic approach to machine operation and maintenance.
To improve PVC pipe bagging machine efficiency in multi-shift operations, focus on preventative maintenance schedules, operator training programs, and streamlined material handling processes. Regular maintenance minimizes downtime, skilled operators reduce errors and optimize machine settings, and efficient material flow ensures continuous operation.
Sustaining high efficiency in a multi-shift environment demands proactive measures and continuous improvement. Let’s explore key strategies to optimize your PVC pipe bagging process and keep your production running smoothly.
2. Understanding Bottlenecks in Multi-Shift Bagging Operations
Multi-shift operations place significant demands on PVC pipe bagging machines. Identifying and addressing common bottlenecks is the first step towards enhanced efficiency.
In multi-shift PVC pipe bagging, common bottlenecks include unscheduled downtime due to wear and tear, inconsistent output from varying operator skill levels across shifts, and delays in material replenishment or changeovers. These issues compound over continuous operation, significantly impacting overall efficiency.
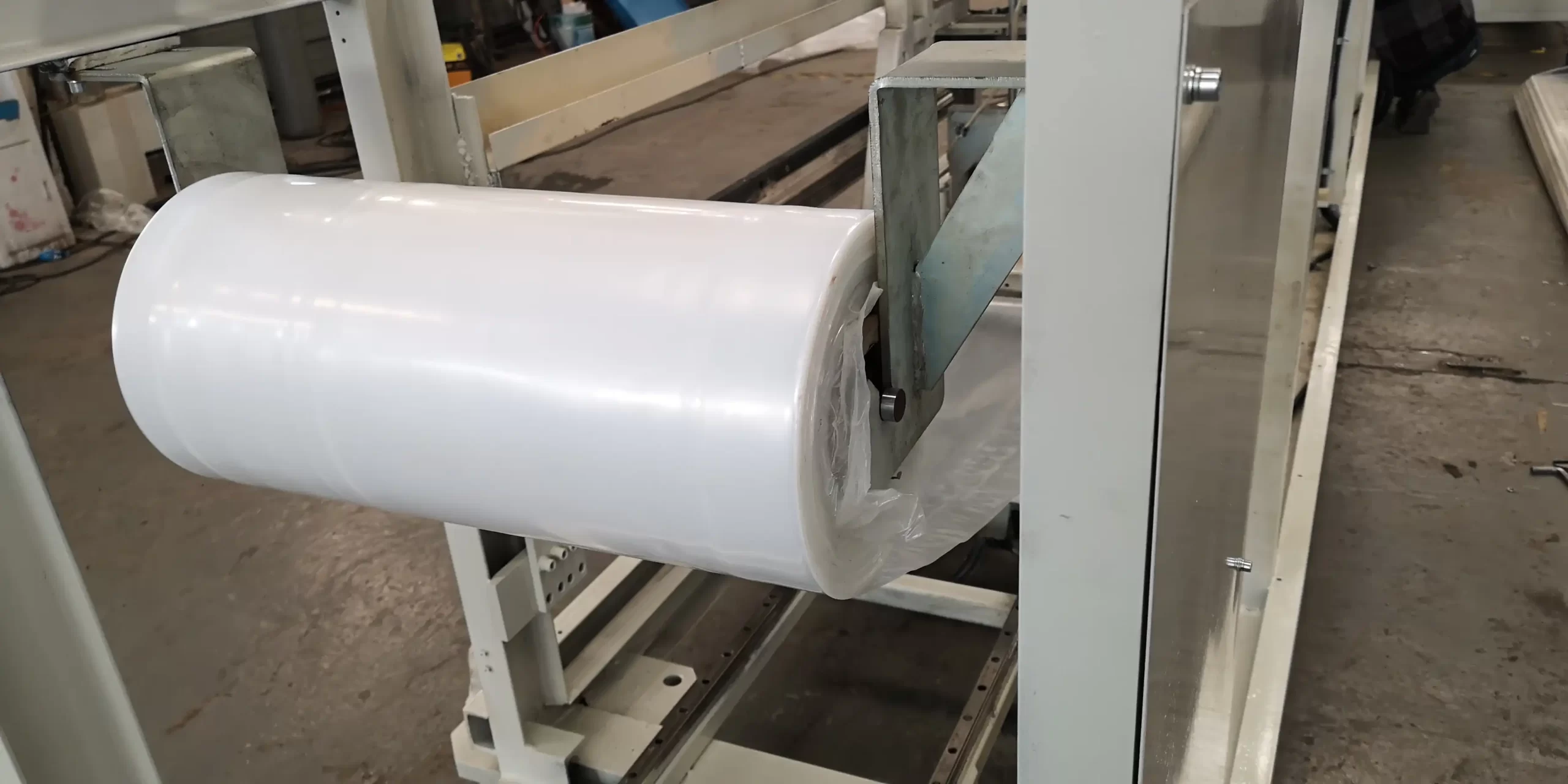
But where exactly are these inefficiencies hiding, and how can we pinpoint them? Let’s delve deeper into data-driven approaches to identify and quantify these hidden losses, paving the way for targeted improvements.
Quantifying Efficiency Losses: Data-Driven Insights
To effectively tackle efficiency challenges, you need to move beyond anecdotal observations and embrace a data-driven approach. This involves implementing key performance indicators (KPIs) and systematically tracking machine performance.
Key Performance Indicators (KPIs) for Bagging Machine Efficiency
KPI | Description | How to Track | Target Improvement |
---|---|---|---|
Overall Equipment Effectiveness (OEE) | A comprehensive metric encompassing Availability, Performance, and Quality. | Automated systems, manual data logging | Aim for 85% OEE or higher |
Downtime | Total time the machine is not operational due to breakdowns, changeovers, etc. | Machine sensors, operator logs, maintenance records | Reduce downtime by 15-20% through preventative actions |
Throughput Rate | Number of bags produced per hour or shift. | Production counters, automated tracking systems | Increase throughput by 5-10% by optimizing settings |
Rejection Rate | Percentage of bags rejected due to errors (sealing issues, incorrect counts). | Quality control checks, automated inspection systems | Decrease rejection rate below 2% |
Changeover Time | Time taken to switch between different pipe sizes or bag types. | Timed procedures, operator logs | Reduce changeover time by 20-30% through standardization |
By consistently monitoring these KPIs, you gain a clear picture of your bagging machine’s performance. Analyzing trends in these metrics will highlight specific areas dragging down efficiency. For example, a consistently low OEE coupled with high downtime points directly to maintenance issues. A high rejection rate might indicate problems with machine calibration or operator errors.
Using Data to Diagnose Issues
Once you’re collecting data, the next step is to analyze it to diagnose the root causes of inefficiencies.
- Pareto Charts for Downtime: Categorize downtime events (e.g., mechanical failures, electrical issues, material jams) and create a Pareto chart. This visually highlights the most frequent causes of downtime, allowing you to prioritize corrective actions.
- Trend Analysis for Throughput: Track throughput rates across different shifts and days. Significant variations might indicate inconsistencies in operator performance or material supply issues.
- Correlation Analysis for Rejection Rates: Investigate if rejection rates correlate with specific operators, shifts, or material batches. This can pinpoint training needs or material quality problems.
By using data to identify and quantify efficiency losses, you can move from reactive problem-solving to proactive optimization. This targeted approach ensures your efforts are focused on the areas with the biggest potential for improvement, leading to tangible gains in PVC pipe bagging machine efficiency in multi-shift operations.
3. Optimizing Preventative Maintenance Schedules
Consistent uptime is paramount in multi-shift operations. A robust preventative maintenance schedule is the cornerstone of minimizing downtime and maximizing bagging machine availability.
For continuous PVC pipe bagging in multiple shifts, a rigorous preventative maintenance schedule is essential. This includes daily checks, weekly servicing, and periodic in-depth inspections. Proactive maintenance reduces unexpected breakdowns, extends machine lifespan, and ensures consistent performance across all shifts.
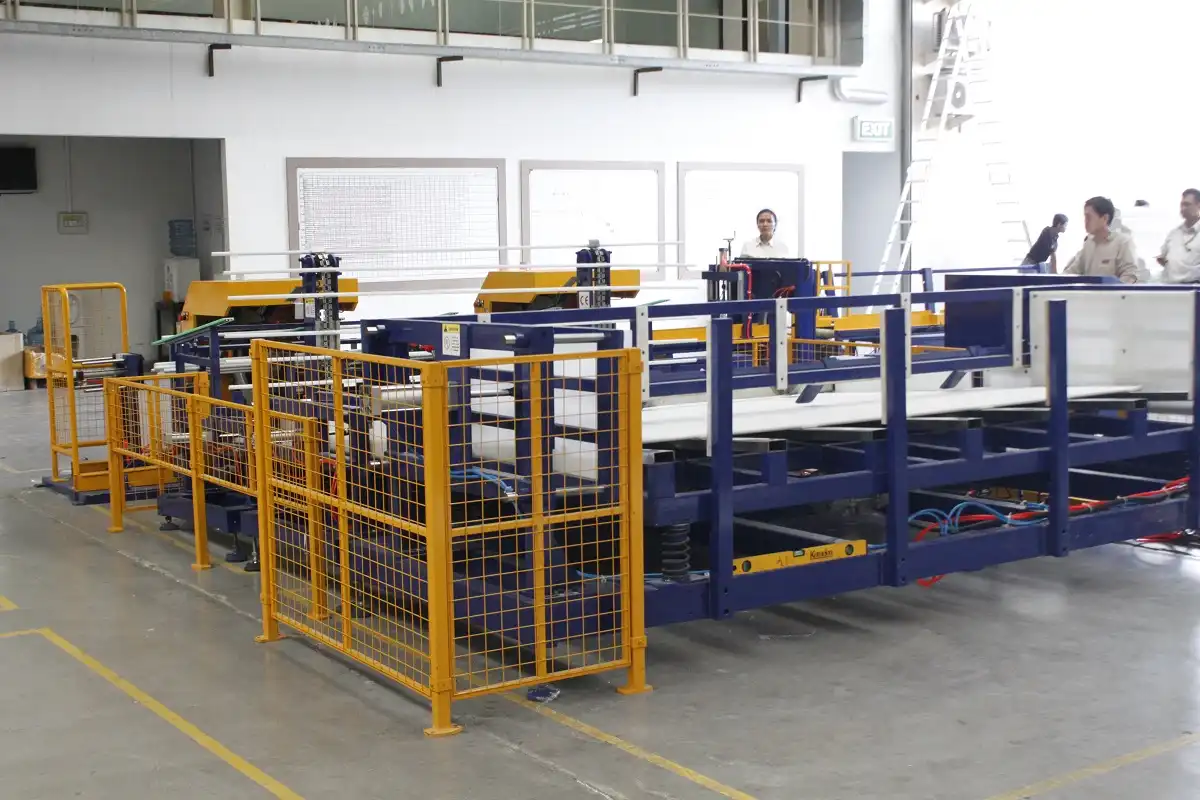
But what exactly should a comprehensive preventative maintenance plan entail? Let’s explore the key components and best practices for keeping your PVC pipe bagging machine running smoothly, shift after shift.
Crafting a Multi-Shift Preventative Maintenance Plan
A truly effective preventative maintenance plan for multi-shift operations needs to be structured, comprehensive, and consistently executed. It should encompass various levels of maintenance, performed at different intervals.
Daily Maintenance (End of Each Shift)
- Cleaning: Remove PVC dust and debris from all accessible machine parts, especially sealing areas, conveyors, and sensors. Use compressed air and brushes.
- Visual Inspection: Check for loose bolts, worn belts, damaged wires, or any signs of wear and tear. Pay attention to critical components like sealing jaws and cutting blades.
- Lubrication (Minor): Apply a light lubricant to designated points as per the manufacturer’s manual, focusing on chains, gears, and moving joints.
- Sensor Check: Ensure all sensors (proximity, photoelectric) are clean and functioning correctly. Test their response if possible.
Weekly Maintenance
- Detailed Cleaning: More thorough cleaning, including removing guards (when safe and permissible) to access less accessible areas.
- Lubrication (Comprehensive): Lubricate all grease points and bearings according to the maintenance schedule, using the correct type of lubricant.
- Belt Tension Check: Verify and adjust belt tension for conveyors and drive systems. Improper tension can lead to slippage and premature wear.
- Chain and Sprocket Inspection: Inspect chains for wear, stretch, and proper lubrication. Check sprocket teeth for damage.
- Pneumatic System Check (if applicable): Drain air filters, check for leaks in hoses and fittings, and ensure proper air pressure.
- Safety System Check: Test emergency stops, safety interlocks, and light curtains to ensure they are functioning correctly. Document the checks.
Monthly/Quarterly Maintenance (Scheduled Downtime)
- In-Depth Inspection: A comprehensive inspection of all mechanical, electrical, and pneumatic systems by trained maintenance personnel.
- Component Replacement (Preventative): Replace wear parts proactively based on usage hours or manufacturer recommendations (e.g., sealing jaws, cutting blades, belts, bearings).
- Calibration and Adjustment: Recalibrate sensors, adjust timing mechanisms, and fine-tune machine settings to maintain optimal performance.
- Electrical System Inspection: Check wiring connections, motor condition, control panel components, and safety grounds.
- Software/PLC Check (if applicable): Verify software versions, backup PLC programs, and check for any error logs.
Key Elements for Success
- Maintenance Schedule: Develop a detailed schedule outlining tasks, frequency, and responsible personnel. Make it readily accessible to all shifts.
- Training: Train maintenance and operator personnel on proper maintenance procedures and the importance of adhering to the schedule.
- Spare Parts Inventory: Maintain an adequate stock of critical spare parts to minimize downtime during repairs or preventative replacements.
- Maintenance Log: Keep a detailed log of all maintenance activities, including dates, tasks performed, parts replaced, and any observations. This helps track maintenance history and identify recurring issues.
- Regular Review: Periodically review the maintenance schedule based on machine performance data and adjust frequencies or tasks as needed.
By implementing a well-defined and diligently followed preventative maintenance plan, you can significantly reduce unscheduled downtime, extend the lifespan of your PVC pipe bagging machine, and ensure consistently high efficiency across all shifts.
4. Empowering Operators Through Targeted Training
Even the most advanced bagging machine relies on skilled operators to maximize its potential. Comprehensive training programs are vital for consistent performance across multiple shifts.
Investing in thorough operator training is crucial for maximizing PVC pipe bagging machine efficiency in multi-shift environments. Well-trained operators can optimize machine settings, quickly troubleshoot minor issues, and perform basic preventative maintenance, leading to increased uptime and consistent output across all shifts.

But what constitutes effective training for bagging machine operators in a multi-shift setting? Let’s explore the key elements of a training program that empowers operators to become efficiency champions.
Building a Multi-Level Operator Training Program
An effective operator training program should be structured, progressive, and ongoing, catering to different skill levels and experience. It should encompass both theoretical knowledge and hands-on practical skills.
Level 1: Basic Operation and Safety (Initial Training for All New Operators)
- Machine Overview: Introduction to the bagging machine components, functions, and overall operation.
- Control Panel Operation: Detailed explanation of the control panel, HMI interface, and all control functions (start, stop, speed adjustment, sealing parameters, etc.).
- Safety Procedures: Comprehensive training on all safety protocols, emergency stops, lockout/tagout procedures, and safe operating practices.
- Basic Troubleshooting: Identification of common error messages and simple troubleshooting steps (e.g., clearing jams, resetting sensors).
- Quality Control Basics: Understanding quality standards for bagged pipes, visual inspection criteria, and rejection procedures.
Level 2: Advanced Operation and Optimization (For Experienced Operators)
- Parameter Optimization: In-depth training on adjusting machine parameters (sealing temperature, pressure, speed, film tension) to optimize performance for different pipe types and bag materials.
- Changeover Procedures: Detailed, step-by-step training on performing efficient and accurate changeovers between pipe sizes and bag types, minimizing downtime.
- Preventative Maintenance (Operator Level): Training on daily and weekly maintenance tasks operators are responsible for (cleaning, lubrication, visual checks).
- Advanced Troubleshooting: Diagnosis and resolution of more complex issues, using machine diagnostics and troubleshooting manuals.
- Data Logging and KPI Monitoring: Training on how to collect production data, monitor KPIs, and identify areas for improvement.
Level 3: Supervisory and Maintenance Skills (For Lead Operators and Potential Technicians)
- Machine Mechanics and Electrics (Basic): Fundamental understanding of machine mechanics, electrical systems, and pneumatic components.
- Advanced Maintenance Procedures: Training on more complex preventative maintenance tasks and basic repairs under supervision.
- Operator Training (Train-the-Trainer): Developing skills to train new operators and conduct refresher training for existing staff.
- Production Management Basics: Understanding production planning, scheduling, and efficiency metrics.
- Inventory Management (Basic): Managing consumables (bags, film) and spare parts at the operator level.
Training Methods and Best Practices
- Hands-on Training: Prioritize practical, hands-on training on the actual bagging machine. Use simulations and real-world scenarios.
- Structured Training Manuals: Provide clear, well-illustrated training manuals covering all aspects of machine operation and maintenance.
- Visual Aids and Videos: Utilize visual aids, diagrams, and training videos to enhance understanding and retention.
- Experienced Trainers: Use experienced operators or technicians as trainers to impart practical knowledge and real-world insights.
- Regular Refresher Training: Conduct periodic refresher training sessions to reinforce skills, update operators on new procedures, and address any performance gaps.
- Performance Evaluation and Feedback: Regularly evaluate operator performance, provide constructive feedback, and recognize high performers.
By implementing a multi-level, comprehensive operator training program, you empower your workforce to become proactive contributors to bagging machine efficiency. This leads to reduced errors, increased uptime, consistent quality, and a more engaged and skilled workforce across all shifts.
5. Streamlining Material Handling and Changeovers
Efficient material flow and rapid changeovers are critical for minimizing downtime and maximizing throughput, especially in multi-shift PVC pipe bagging operations.

Efficient material handling and quick changeovers are not just about speed; they’re about minimizing disruptions to the continuous flow of production. Let’s delve into strategies to optimize these crucial aspects of your PVC pipe bagging process.
Optimizing Material Flow and Changeover Processes
In multi-shift operations, even small delays in material handling or changeovers can accumulate significantly, impacting overall efficiency. Streamlining these processes is key to sustained high performance.
Material Handling Optimization
- Automated Infeed Systems: Implement automated conveyor systems or robotic arms to feed PVC pipes to the bagging machine, reducing manual handling and ensuring a consistent supply.
- Buffer Zones: Create buffer zones for pipes waiting to be bagged and for finished bags, preventing bottlenecks and ensuring continuous machine operation.
- Optimized Layout: Design the bagging machine layout to minimize material travel distances and eliminate unnecessary movements.
- Just-in-Time Material Delivery: Coordinate material delivery to match production schedules, reducing material staging and potential congestion.
- Ergonomic Material Presentation: Ensure that materials are presented to operators (if manual feeding is involved) in an ergonomic manner to reduce fatigue and improve efficiency.
Quick Changeover Techniques
- Standardized Procedures: Develop detailed, step-by-step procedures for changeovers, clearly outlining each task and required tools.
- Pre-Staging and Kitting: Pre-stage all necessary components, tools, and materials for changeovers in kits, ready for immediate use.
- Quick-Release Mechanisms: Utilize quick-release clamps, fasteners, and tooling to minimize the time spent on adjustments and component changes.
- Color-Coding and Labeling: Use color-coding and clear labeling for changeover parts and tools to prevent errors and speed up identification.
- Single-Minute Exchange of Die (SMED) Principles: Apply SMED principles to analyze and reduce changeover times by converting internal changeover tasks (done while the machine is stopped) to external tasks (done while the machine is running).
- Training and Practice: Train operators thoroughly on quick changeover procedures and conduct regular practice sessions to improve speed and accuracy.
- Checklists and Verification: Use checklists to ensure all steps in the changeover process are completed correctly and to verify machine readiness before restarting production.
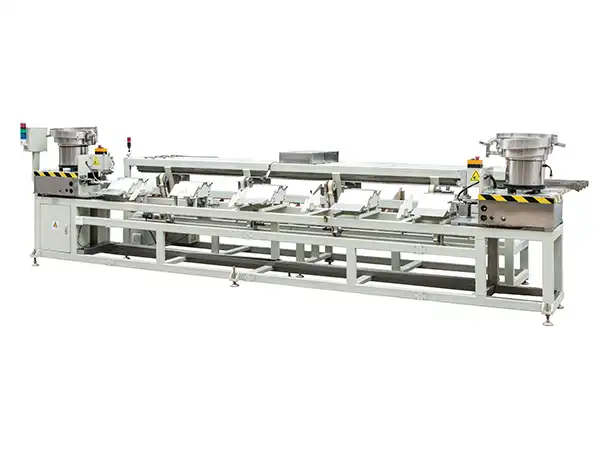
Benefits of Streamlined Processes
- Reduced Downtime: Faster changeovers and efficient material flow directly minimize machine downtime, increasing overall availability.
- Increased Throughput: Continuous material supply and quicker changeovers enable higher throughput rates and increased production volume.
- Improved Operator Efficiency: Streamlined processes reduce operator workload, minimize errors, and improve job satisfaction.
- Lower Material Waste: Efficient material handling minimizes damage and waste, reducing material costs.
- Enhanced Production Flexibility: Faster changeovers enable greater flexibility in production scheduling and the ability to handle smaller batch sizes efficiently.
By focusing on optimizing material handling and implementing quick changeover techniques, you can create a more responsive and efficient PVC pipe bagging operation, maximizing output and minimizing waste in your multi-shift environment.
Conclusion
Improving PVC pipe bagging machine efficiency in multi-shift operations is a multifaceted undertaking. It requires a holistic approach encompassing data-driven analysis, proactive maintenance, skilled operators, and streamlined processes. By implementing the strategies outlined – from meticulous preventative maintenance schedules to comprehensive operator training and optimized material handling – manufacturers can unlock significant gains in efficiency, ensuring consistent output, reduced downtime, and enhanced profitability in their continuous PVC pipe production.