How to Improve PVC Pipe Bagging Machine Durability in High-Traffic Operations?
In high-traffic operations, maintaining the durability of PVC pipe bagging machines is crucial for uninterrupted production and cost-effectiveness. These machines, integral to packaging lines, face constant wear and tear. Understanding how to enhance their resilience ensures longevity and minimizes downtime, directly impacting operational efficiency and profitability in demanding environments.
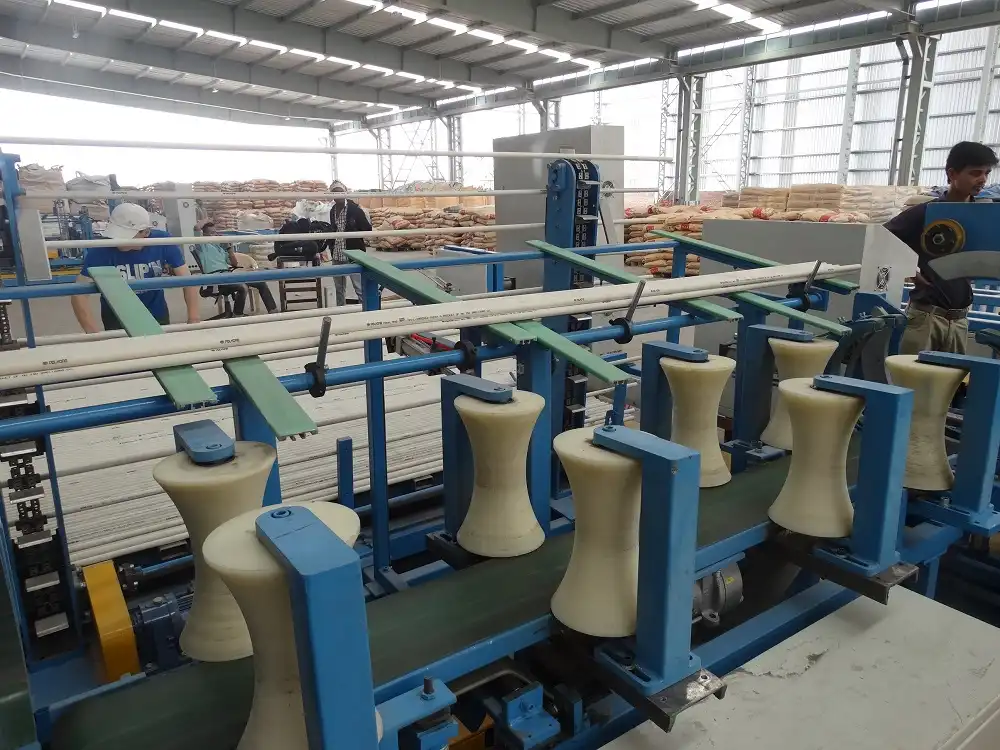
To improve PVC pipe bagging machine durability in high-traffic operations, focus on regular preventative maintenance, use of high-quality components, operator training, and optimizing operational parameters. Implementing predictive maintenance using sensor technology and robust machine design are also key strategies to withstand continuous, heavy-duty use and extend machine lifespan.
To delve deeper into maximizing the lifespan and efficiency of your PVC pipe bagging machines, let’s explore specific strategies. By understanding the critical factors and implementing proactive measures, you can ensure your bagging operations remain robust and reliable, even under the most demanding conditions.
1. Implementing a Robust Preventative Maintenance Schedule for PVC Pipe Bagging Machines
In the realm of high-volume PVC pipe production, bagging machines are the workhorses that ensure product readiness for dispatch. However, continuous operation in high-traffic environments puts immense strain on these machines, making preventative maintenance not just beneficial, but essential.
A robust preventative maintenance schedule for PVC pipe bagging machines in high-traffic operations includes daily inspections, lubrication of moving parts, regular cleaning, timely replacement of wear-prone components, and periodic professional servicing. This proactive approach minimizes unexpected breakdowns, extends machine lifespan, and ensures consistent performance under heavy operational demands.
But what exactly should this schedule entail, and how can it be tailored to the specific demands of high-traffic PVC pipe bagging operations? Let’s break down the critical elements of an effective preventative maintenance program.
Tailoring Your Maintenance Schedule for High-Traffic PVC Pipe Bagging
A one-size-fits-all approach to maintenance simply won’t cut it in high-throughput environments. The key is to create a schedule that directly addresses the stress points of your PVC pipe bagging machine under heavy use. This requires a detailed understanding of machine components and their wear patterns.
Consider these key areas when designing your preventative maintenance schedule:
Maintenance Task | Frequency | Focus Area | Benefits |
---|---|---|---|
Daily Inspection | Daily | Belts, seals, sensors, pneumatic systems | Early detection of minor issues, preventing escalation into major problems |
Lubrication | Weekly | Bearings, gears, chains | Reduced friction and wear, smoother operation, extended component life |
Cleaning | Weekly/Bi-weekly | Bagging mechanism, sealing areas, conveyors | Prevents material build-up, ensures proper function, hygienic operation |
Component Replacement | Monthly/Quarterly | Wear parts (blades, belts, rollers) | Maintains optimal performance, prevents breakdowns due to worn parts |
Professional Servicing | Annually | Full system check, calibration, upgrades | Comprehensive assessment, ensures long-term reliability and efficiency |
By implementing this structured approach, you move from reactive repairs to proactive upkeep, significantly reducing downtime and maximizing the operational lifespan of your [plastic packaging machines].
2. Selecting High-Quality Components for Enhanced Durability
The durability of a PVC pipe bagging machine is intrinsically linked to the quality of its components. In high-traffic environments, where machines are pushed to their limits, skimping on component quality is a false economy that leads to frequent breakdowns and costly replacements.
Choosing high-quality components for PVC pipe bagging machines, such as durable belts, robust sensors, and reliable pneumatic systems, is paramount for longevity in high-traffic operations. Investing in superior materials and manufacturing ensures components can withstand constant stress, reducing wear and tear, minimizing downtime, and extending the machine’s overall lifespan.
But what specific components should you prioritize when aiming for enhanced durability, and how do you ensure you’re selecting for quality?
Key Components for Durability and Longevity
Upgrading or selecting high-quality components translates directly to improved machine lifespan and reliability. Here are some critical areas to focus on:
- Belts and Rollers: Opt for reinforced belts made from durable materials like polyurethane or high-grade rubber. Rollers should be constructed from hardened steel or have wear-resistant coatings to withstand constant friction and load.
- Sensors and Control Systems: Invest in industrial-grade sensors known for their accuracy and robustness. PLC (Programmable Logic Controller) systems from reputable brands offer superior reliability and longevity compared to budget alternatives.
- Pneumatic and Hydraulic Components: Choose cylinders, valves, and hoses from established manufacturers known for their durability and leak-proof performance. Stainless steel components are preferable in humid or corrosive environments.
- Motors and Gearboxes: Select motors with sufficient power and robust gearboxes designed for continuous duty. Consider servo motors for applications requiring precise and repetitive movements, as they often offer greater durability than standard AC motors.
- Sealing Elements: High-quality sealing jaws and heating elements are crucial for consistent bag sealing. Look for materials that can withstand repeated heating and cooling cycles without degradation.
By focusing on these key components and prioritizing quality over initial cost savings, you build a PVC pipe bagging machine that is truly built to last, even in the most demanding high-traffic operations.
3. Operator Training and Best Practices for Machine Longevity
Even the most robust PVC pipe bagging machine can suffer premature wear and tear if not operated correctly. Well-trained operators are crucial for ensuring machines are used within their design parameters, minimizing misuse, and identifying potential issues early on.
Comprehensive operator training on PVC pipe bagging machines is vital for maximizing durability in high-traffic operations. Training should cover proper machine operation, troubleshooting common issues, understanding safety protocols, and performing basic maintenance tasks. Skilled operators reduce machine stress, minimize errors, and contribute significantly to the machine’s long-term reliability and performance.
But what specific training areas are most impactful for enhancing machine durability, and how can you implement effective training programs?
Essential Training Modules for Operators
Effective operator training goes beyond simply showing someone how to start and stop the machine. It involves building a deep understanding of the machine’s operation and fostering a sense of ownership and responsibility. Key training areas include:
- Machine Operation Fundamentals: Thorough instruction on start-up, normal operation, and shut-down procedures. Emphasis on correct loading and unloading techniques to prevent machine stress.
- Troubleshooting and Error Handling: Training on identifying and resolving common error messages and minor malfunctions. Operators should be empowered to address small issues before they escalate.
- Preventative Maintenance Basics: Equipping operators to perform daily inspections, lubrication, and basic cleaning tasks. This fosters a culture of proactive machine care.
- Safety Protocols and Emergency Procedures: Comprehensive training on all safety features, emergency stop procedures, and safe material handling practices. Safety awareness contributes to both operator well-being and machine protection.
- Understanding Machine Limitations: Educating operators on the machine’s design capacity and limitations. This prevents overloading and misuse that can lead to premature wear and breakdowns.
By investing in thorough and ongoing operator training, you not only improve machine durability but also create a more skilled and engaged workforce, ultimately boosting overall operational efficiency.
4. Optimizing Operational Parameters to Reduce Machine Stress
PVC pipe bagging machines, while designed for robust operation, have optimal performance parameters. Exceeding these parameters, especially in high-traffic scenarios, can accelerate wear and tear and shorten machine lifespan. Optimizing operational settings is a proactive step towards enhancing durability.
To optimize PVC pipe bagging machine operations for durability, carefully adjust parameters like bagging speed, sealing temperature, and pressure according to the manufacturer’s recommendations and the specific materials being used. Avoiding unnecessary speed increases, ensuring correct sealing settings, and managing product flow reduces mechanical stress and thermal fatigue, contributing to extended machine life in demanding, high-volume environments.
But what specific operational parameters are most critical for durability, and how can you fine-tune them for optimal performance and longevity?
Critical Operational Parameters for Machine Longevity
Fine-tuning machine settings based on the specific PVC pipes and bagging materials being used is crucial for minimizing stress and maximizing durability. Consider these key adjustments:
- Bagging Speed: Resist the urge to maximize speed at all costs. Running the machine at a slightly slower, optimized speed can significantly reduce mechanical stress on moving parts and extend component life. Experiment to find the sweet spot between throughput and machine strain.
- Sealing Temperature and Pressure: Incorrect sealing settings are a major cause of machine issues. Too high a temperature can damage sealing jaws and film, while too low can result in weak seals. Calibrate temperature and pressure precisely according to the bagging film specifications. Regular checks and adjustments are essential.
- Product Feed Rate: Ensure a consistent and controlled product feed rate. Surges or uneven flow can overload the bagging mechanism and cause jams or misalignments. Implement sensors and controls to maintain a smooth and even product flow.
- Pneumatic Pressure: Optimize air pressure in pneumatic systems. Excess pressure increases stress on cylinders and valves, while insufficient pressure can lead to sluggish operation. Regularly check and adjust pressure settings according to manufacturer guidelines.
- Cooling Time (for sealing): Allow adequate cooling time after sealing. Insufficient cooling can lead to weak seals and film sticking, increasing stress on the sealing mechanism. Adjust cooling time based on film type and thickness.
By meticulously optimizing these operational parameters, you can significantly reduce stress on your PVC pipe bagging machine, leading to fewer breakdowns, reduced maintenance, and a longer, more productive lifespan.
Conclusion
Improving the durability of PVC pipe bagging machines in high-traffic operations is a multifaceted endeavor. It requires a strategic approach encompassing preventative maintenance, high-quality components, skilled operators, and optimized operational settings. By implementing these strategies, businesses can significantly enhance the longevity and reliability of their bagging machines, ensuring consistent production, minimizing downtime, and maximizing their return on investment in [PVC Pipe Packing Line] technology. Proactive measures are key to keeping these essential machines running smoothly and efficiently, even under the most demanding operational conditions.