In industries where steel wire packing is essential, maintaining the integrity of the wire and the efficiency of the packing process are paramount. Magnetic interference can pose a significant challenge, potentially disrupting automated systems and affecting the quality of the packed wire. Understanding and mitigating magnetic resistance is therefore crucial.
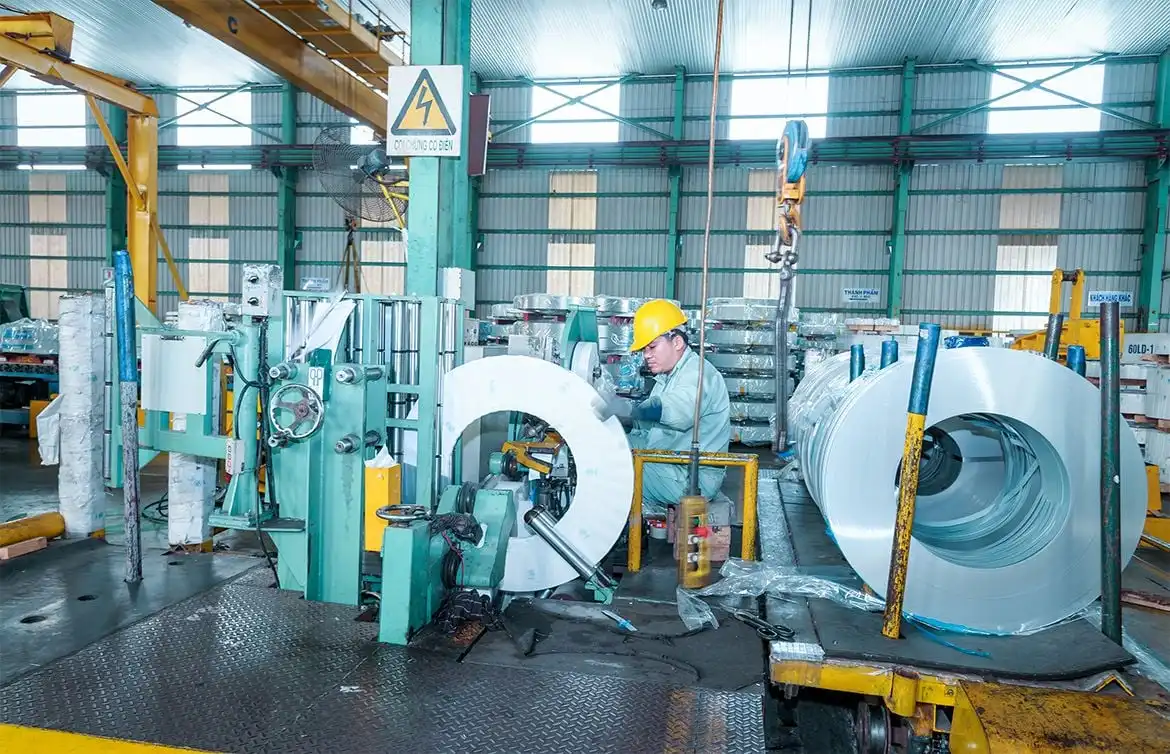
Improving magnetic resistance in steel wire packing involves employing effective shielding methods and selecting appropriate materials. Utilizing Faraday cages, Mu-metal shielding, and strategically grounding equipment are key strategies. Additionally, choosing steel wire with inherent magnetic resistance properties and optimizing the layout of packing machinery can significantly minimize magnetic interference.
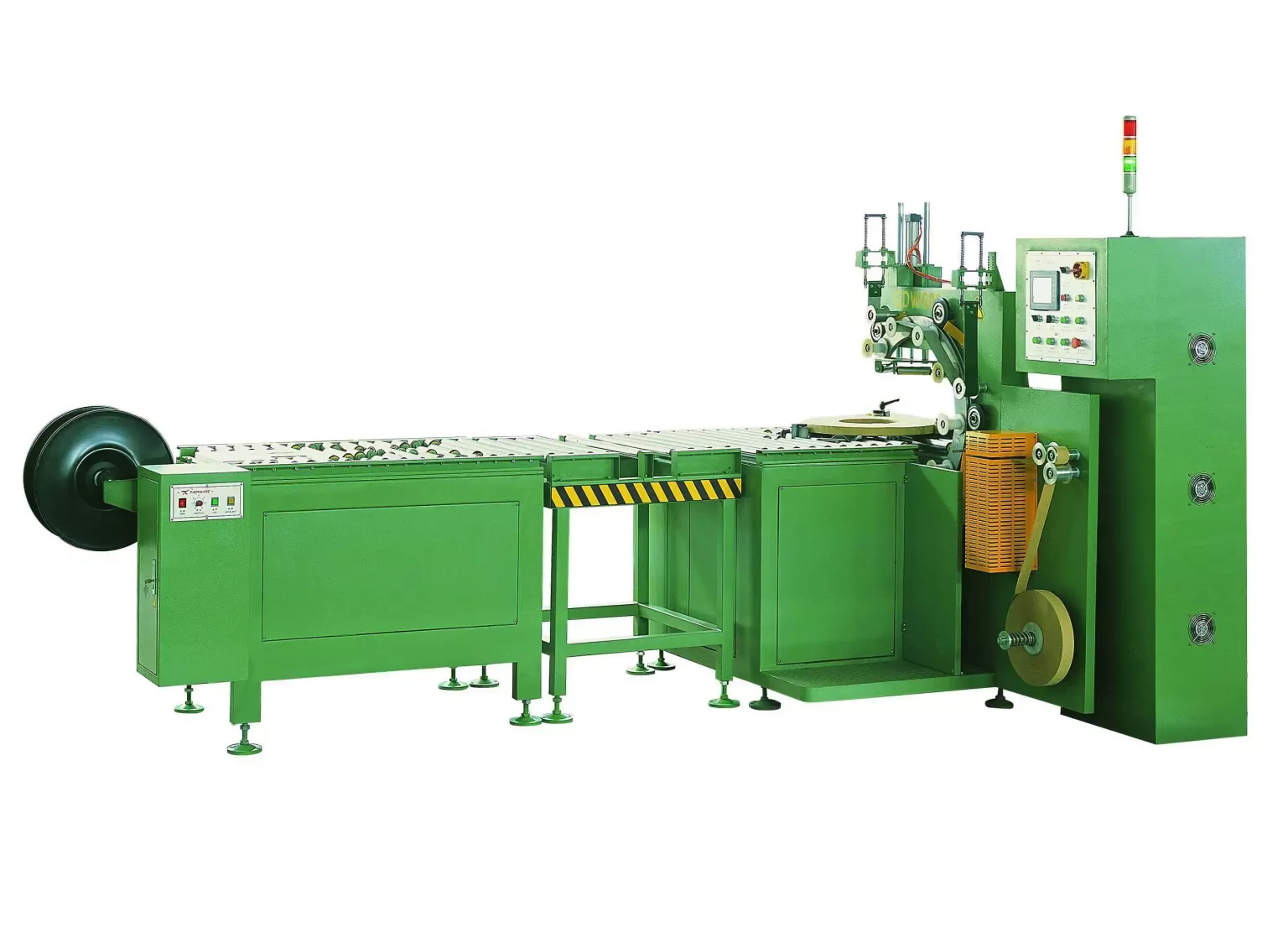
This article delves into practical techniques and material considerations for enhancing magnetic resistance in steel wire packing, ensuring operational reliability and product quality. Let’s explore how targeted shielding and material choices can make a substantial difference.
2. Understanding Magnetic Interference in Wire Packing
Magnetic interference in wire packing facilities can stem from various sources, both natural and human-made. From the powerful motors driving machinery to ambient electromagnetic radiation, these interferences can disrupt sensitive electronic controls and sensors crucial for precise packing operations. Identifying the sources and understanding their impact is the first step towards effective mitigation.
Magnetic interference in wire packing arises from electromagnetic fields that disrupt the normal operation of equipment. Sources include industrial machinery, power lines, and even natural phenomena like lightning. This interference can lead to operational inefficiencies, inaccurate measurements, and potential damage to sensitive electronic components within wire packing systems. Shielding and proper grounding are essential to combat these disruptive forces.

To effectively address magnetic interference, a deeper dive into its types, sources, and shielding methodologies is necessary. By understanding these aspects, we can implement targeted strategies to safeguard wire packing processes.
2.1 Sources of Magnetic Interference in Industrial Settings
Industrial environments are rife with potential sources of magnetic interference. These can be broadly categorized into natural and human-created sources, each requiring different approaches for mitigation.
2.1.1 Natural Sources: The Unseen Background Noise
While often less impactful in controlled industrial settings compared to man-made sources, natural phenomena contribute to the overall electromagnetic background noise.
Natural Source | Description | Impact on Wire Packing |
---|---|---|
Lightning | Powerful electromagnetic pulses during thunderstorms. | Transient disruptions to electrical systems, potential damage if not properly grounded. |
Solar Flares | Bursts of electromagnetic radiation from the sun. | Minor, but can contribute to background noise levels. |
Cosmic Radiation | High-energy particles from space. | Negligible impact on most industrial equipment. |
Geomagnetic Activity | Fluctuations in Earth’s magnetic field. | Very low frequency, generally not a significant concern for typical wire packing equipment. |
2.1.2 Human-Created Sources: The Industrial Landscape of EMI
The modern industrial landscape is a significant contributor to electromagnetic interference. Understanding these sources is crucial for implementing effective shielding and mitigation strategies in wire packing facilities.
Human-Created Source | Description | Impact on Wire Packing | Mitigation Strategies |
---|---|---|---|
Industrial Machinery | Motors, generators, welding equipment, and other heavy machinery. | Significant broadband and narrowband EMI, disrupting sensors, control systems, and automated processes. | Shielding enclosures for machinery, EMI filters, cable shielding, proper grounding. |
Power Lines | High-voltage power transmission and distribution lines. | Continuous EMI, especially at lower frequencies. | Distance separation, underground cabling where feasible, shielding for sensitive areas near power lines. |
Telecommunications | Radio transmitters, cellular towers, and communication devices. | Radiated RF interference, potentially affecting wireless control systems and data transmission. | Faraday cages for sensitive control rooms, RF shielding materials, directional antennas for external communication. |
Wi-Fi and Wireless Devices | Wireless networks and devices within the facility. | Broadband RF interference, potentially affecting network stability and data integrity. | Minimize unnecessary wireless devices, use wired connections where possible, RF shielding for critical network infrastructure. |
Variable Frequency Drives (VFDs) | Used to control motor speed, generate significant EMI due to rapid switching of power electronics. | Broadband EMI, can severely impact nearby electronics if not properly filtered and shielded. | Install EMI filters on VFD outputs, use shielded cables for motor connections, ground VFDs and motors effectively. |
By systematically identifying and addressing these sources, wire packing facilities can significantly improve their magnetic resistance and operational reliability.
3. Shielding Methods for Steel Wire Packing Equipment
Effective shielding is paramount in reducing magnetic interference in steel wire packing environments. Various methods can be employed, each with its own advantages and suitability depending on the specific application and type of interference.
EMI shielding methods for wire packing equipment involve creating barriers to block electromagnetic fields. Faraday cages, constructed from conductive materials like copper or steel, are highly effective for enclosing sensitive areas. Mu-metal offers superior magnetic shielding for specific components. Additionally, cable shielding, conductive gaskets, and shielded vents are crucial for preventing EMI leakage through openings and seams in enclosures.
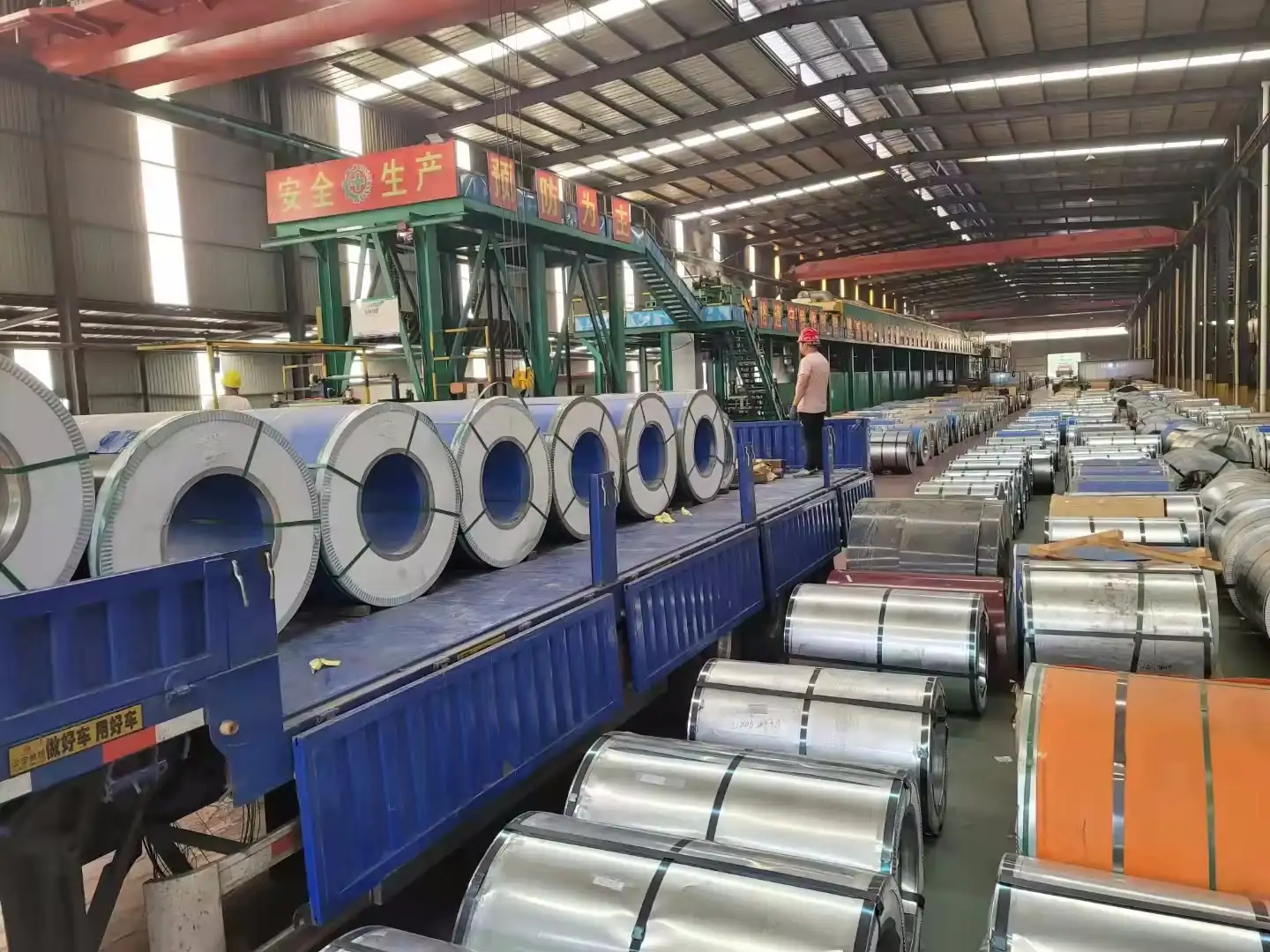
Let’s delve into the most effective shielding methods applicable to steel wire packing machinery and facilities.
3.1 Faraday Cages: The Enclosure Approach
Faraday cages are a cornerstone of EMI shielding, providing robust protection by completely enclosing a space with conductive material. For wire packing, this can range from shielding entire control rooms to enclosing individual pieces of sensitive equipment.
3.1.1 Construction and Materials
Faraday cages for industrial applications are typically constructed from:
- Copper: Excellent conductivity, high shielding effectiveness, and good corrosion resistance, often used for high-performance applications like MRI rooms and sensitive control centers.
- Steel: Provides structural strength and magnetic shielding, often used in conjunction with more conductive materials like copper to enhance overall shielding performance, especially against magnetic fields.
- Aluminum: Lightweight and cost-effective, suitable for less demanding applications where weight is a concern, but less conductive and more susceptible to corrosion than copper.
3.1.2 Implementing Faraday Cages in Wire Packing Facilities
- Control Rooms: Enclosing the entire control room in a Faraday cage provides a shielded environment for sensitive control systems, computers, and operator consoles.
- Equipment Enclosures: Individual machines or sensitive components can be housed within smaller Faraday cages, focusing shielding where it’s most needed.
- Shielded Rooms: For highly sensitive operations or testing areas, dedicated shielded rooms can be constructed as Faraday cages, providing a controlled electromagnetic environment.
3.2 Material-Specific Shielding: Copper, Steel, and Mu-Metal
The choice of shielding material is crucial and depends on the type of interference and the required level of attenuation.
3.2.1 Copper Shielding: High Conductivity for RF and EMI
Copper is a top choice for RF and EMI shielding due to its exceptional electrical conductivity.
Property | Copper | Aluminum | Steel |
---|---|---|---|
Electrical Conductivity | Highest | High | Moderate |
Shielding Effectiveness | Excellent for RF and EMI | Good for RF and EMI | Good for magnetic fields, moderate for RF |
Corrosion Resistance | Excellent | Moderate (forms oxide layer) | Can corrode, pre-tin plating improves |
Weight | Heavier | Lightweight | Heavy |
Cost | Higher | Moderate | Lower |
Typical Applications | High-performance shielding, MRI rooms, Faraday cages | General EMI shielding, aerospace, automotive | Industrial enclosures, magnetic shielding |
3.2.2 Steel Shielding: Strength and Magnetic Field Protection
Steel, particularly pre-tin plated steel, offers a balance of strength, durability, and magnetic shielding capabilities.
- Pre-Tin Plated Steel: Combines the strength of steel with enhanced conductivity and corrosion resistance from the tin plating, suitable for enclosures and areas requiring both EMI and environmental protection.
- Mu-Metal: A nickel-iron alloy with extremely high magnetic permeability, ideal for shielding against low-frequency magnetic fields, often used for sensitive sensors and components within wire packing machinery.
3.3 Component-Level Shielding: Gaskets, Cables, and Vents
Even with robust enclosures, small gaps and openings can compromise shielding effectiveness. Component-level shielding addresses these vulnerabilities.
3.3.1 EMI Shielding Gaskets
Conductive gaskets are used to seal seams, doors, and access panels in enclosures, preventing EMI leakage.
- Conductive Elastomers: Flexible silicone or fluorosilicone loaded with conductive particles (silver, nickel, etc.), providing both EMI shielding and environmental sealing.
- Knitted Wire Mesh: Metal mesh gaskets offering good conductivity and resilience, suitable for doors and panels that require frequent access.
- Finger Stock: Beryllium copper or stainless steel strips with fingers that create a wiping contact, providing excellent conductivity and compression range for doors and panels.
3.3.2 Shielded Cables and Cable Entry Plates
Cables entering or leaving shielded enclosures can act as antennas, conducting EMI. Shielded cables and proper entry plates are essential.
- Shielded Cables: Cables with a conductive braid or foil shield surrounding the conductors, grounded to the enclosure to prevent EMI ingress/egress.
- Cable Entry Plates: Conductive plates with glands or connectors that provide a 360-degree shield termination for cable shields at the enclosure wall.
3.3.3 Shielded Ventilation and Displays
Ventilation and visual monitoring are often necessary in wire packing facilities. Shielded vents and transparent displays maintain shielding integrity while allowing airflow and visibility.
- Honeycomb Ventilation Panels: Waveguide-like structures that allow airflow while blocking electromagnetic waves, essential for cooling equipment within shielded enclosures.
- Transparent Conductive Windows: Glass or acrylic panels coated with conductive materials like ITO (Indium Tin Oxide) or fine wire mesh, providing visibility while maintaining shielding.
4. Practical Steps to Enhance Magnetic Resistance in Steel Wire Packing
Improving magnetic resistance is an ongoing process that involves careful planning, implementation, and maintenance. Here are actionable steps for wire packing facilities.
To improve magnetic resistance, begin with a comprehensive EMI assessment to identify interference sources. Implement Faraday cages around sensitive control areas and machinery. Utilize Mu-metal for shielding particularly vulnerable components. Ensure all equipment is properly grounded to redirect conducted EMI. Select steel wire and packing materials with inherently low magnetic susceptibility. Regularly inspect and maintain shielding integrity, paying attention to gaskets, cable entries, and any openings. Optimize machinery layout to minimize electromagnetic coupling and maintain distance between interference sources and sensitive equipment.
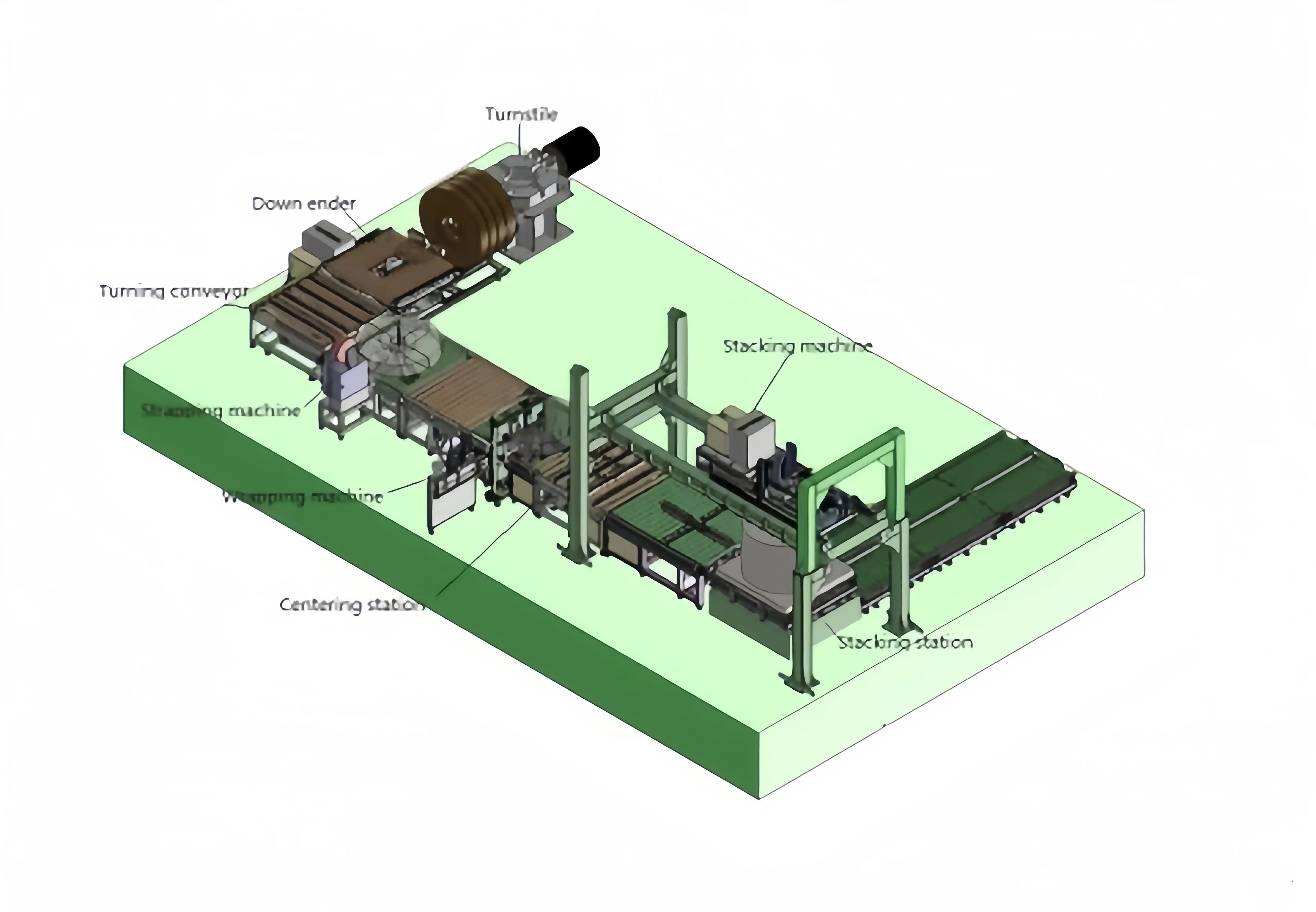
4.1 Conduct a Thorough EMI Assessment
Before implementing any shielding measures, a comprehensive EMI assessment is crucial. This involves:
- Identifying Potential Sources: Pinpoint all potential EMI sources within and around the wire packing facility (machinery, power lines, etc.).
- Measuring EMI Levels: Use spectrum analyzers and EMI meters to measure electromagnetic field strengths at various locations, especially near sensitive equipment.
- Frequency Analysis: Determine the frequency spectrum of the interference to select appropriate shielding materials and methods (low-frequency magnetic vs. high-frequency RF).
- Sensitivity Analysis: Evaluate the susceptibility of wire packing equipment and control systems to different levels and types of EMI.
4.2 Implement Layered Shielding Approach
A layered approach to shielding provides the most robust and cost-effective solution. This involves:
- Source Shielding (Level I): Shield EMI sources at their origin, such as enclosing motors or VFDs in shielded enclosures and using filters on power lines.
- Equipment Shielding (Level II): Shield sensitive wire packing equipment and control cabinets using Faraday cages or conductive enclosures.
- Area Shielding (Level III): Shield entire control rooms or critical processing areas with Faraday cages for maximum protection.
4.3 Material Selection and Grounding Best Practices
Choosing the right materials and implementing proper grounding are fundamental to effective magnetic resistance.
- Optimize Material Choice: Select shielding materials based on the EMI assessment, prioritizing copper or pre-tin plated steel for enclosures and Mu-metal for specific magnetic shielding needs.
- Ensure Continuous Conductivity: Maintain electrical continuity across all shielding materials and enclosure seams using conductive gaskets and proper joining techniques (welding, soldering, conductive adhesives).
- Implement Effective Grounding: Ground all shielded enclosures, equipment, and cable shields to a common grounding point with low impedance paths to redirect conducted EMI safely to ground.
- Regular Inspection and Maintenance: Periodically inspect shielding installations for gaps, corrosion, or damage, and maintain gaskets, cable connections, and grounding points to ensure continued effectiveness.
Conclusion
Improving magnetic resistance in steel wire packing is essential for maintaining operational efficiency, product quality, and system reliability in modern industrial environments. By understanding the sources of magnetic interference, employing effective shielding methods like Faraday cages and material-specific shielding, and implementing practical steps for assessment and maintenance, wire packing facilities can significantly minimize the impact of EMI. Strategic shielding and material choices are not merely preventative measures; they are investments in the long-term success and resilience of wire packing operations, ensuring consistent performance and minimizing costly disruptions. Through careful planning and execution of these strategies, industries can confidently navigate the challenges of electromagnetic interference and optimize their steel wire packing processes.