Steel wire packing is crucial for secure transport and storage, yet it faces constant threats from environmental factors and handling stresses. Ensuring durability is paramount to prevent damage and maintain the integrity of the steel wire during its lifecycle.
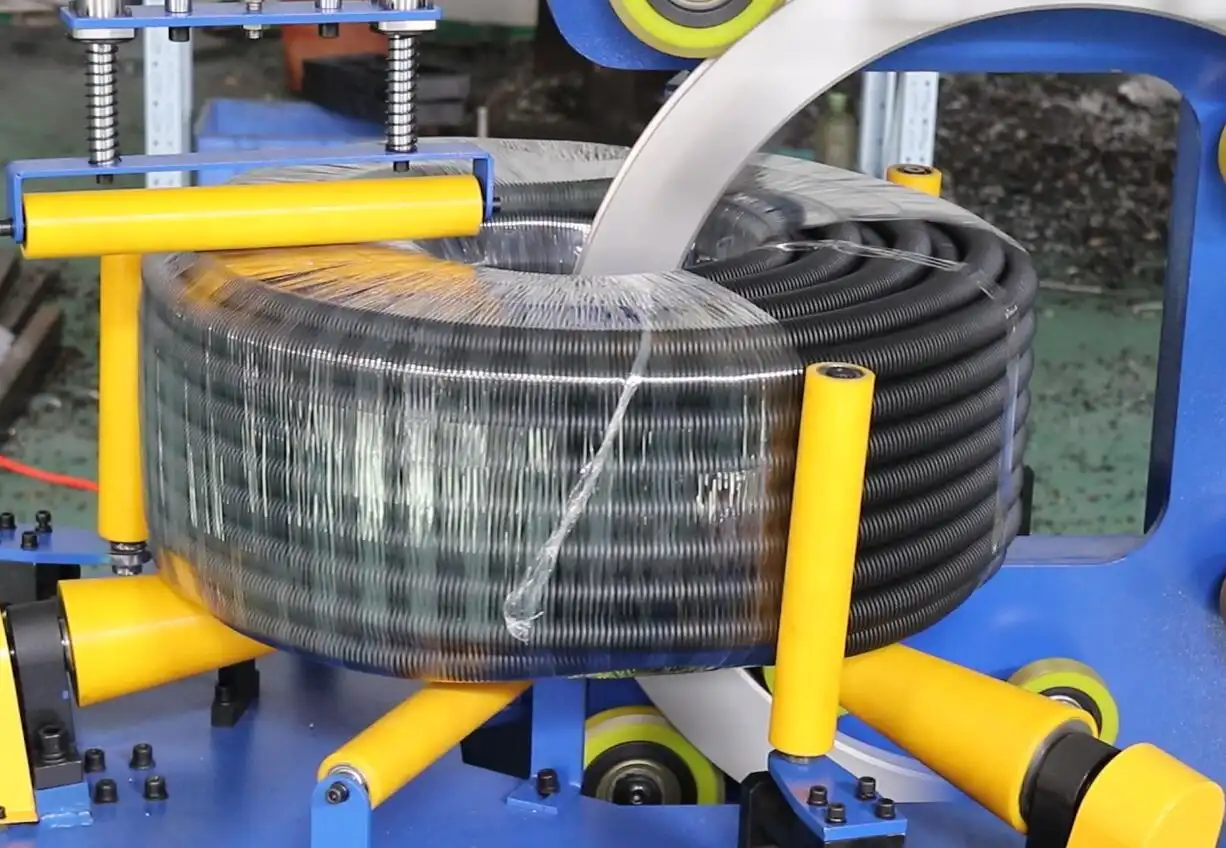
To improve durability in steel wire packing, focus on robust material selection for packaging, optimize the wire packing machine process to minimize stress, implement rigorous quality checks, and consider environmental protection measures like moisture barriers and UV resistance. Regular maintenance of packing equipment and proper handling protocols are also essential for extending lifespan and ensuring package integrity.
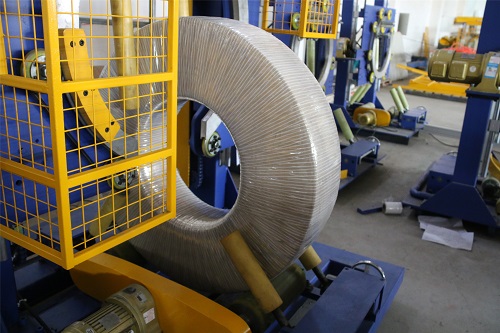
This guide will delve into each of these critical areas, providing actionable insights to enhance the durability of your steel wire packing, reduce material waste, and ensure your products arrive in perfect condition.
2. Selecting Durable Packing Materials for Steel Wire
Choosing the right packing materials is the first line of defense in enhancing the durability of steel wire packaging. The material must withstand the rigors of handling, transportation, and varying environmental conditions to protect the steel wire effectively.

The durability of steel wire packing heavily relies on the material strength of chosen packaging. High-quality materials such as reinforced plastics, heavy-duty cardboard, and specialized wrapping films offer superior protection against physical damage, moisture, and corrosion. Selecting materials with appropriate tensile strength, tear resistance, and environmental resilience is crucial for ensuring the longevity and integrity of the packed steel wire during storage and transit.
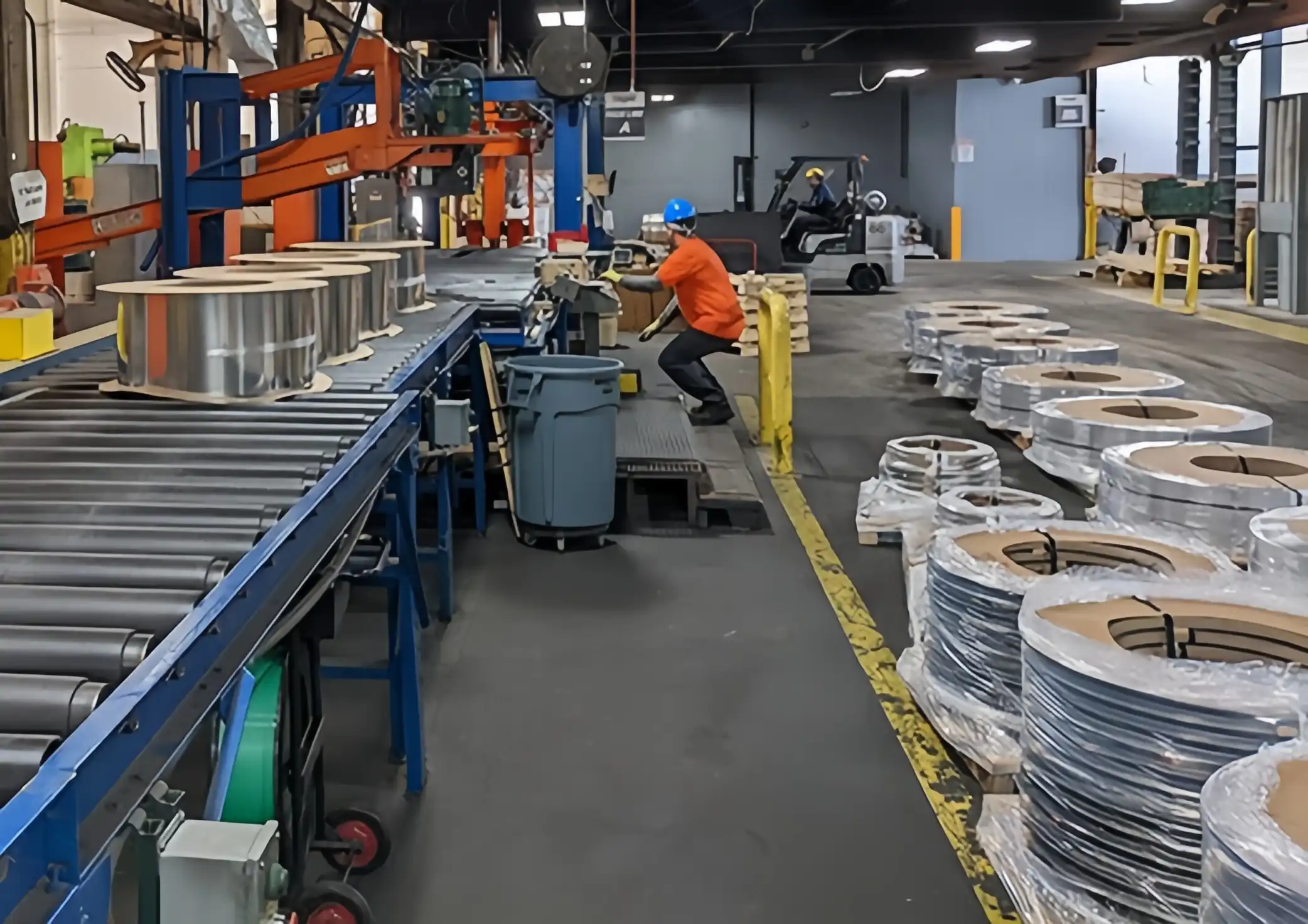
To truly maximize the protective capabilities of your packing materials, it’s essential to understand the specific demands of steel wire packing and how material properties directly correlate with durability.
Understanding Material Properties and Their Impact on Durability
The effectiveness of packing materials isn’t just about thickness; it’s about the inherent properties that make them suitable for protecting steel wire. Let’s break down key material characteristics and their relevance to durability.
Tensile Strength and Tear Resistance
These properties dictate how well a material withstands pulling and tearing forces, crucial during handling and transportation.
Material Type | Tensile Strength (MPa) | Tear Resistance (N/mm) | Durability Level | Common Applications in Steel Wire Packing |
---|---|---|---|---|
Standard Cardboard | 2-5 | 0.1-0.3 | Low | Light gauge wire, short distance transport |
Heavy-Duty Cardboard | 5-10 | 0.3-0.6 | Medium | Medium gauge wire, moderate transport |
Reinforced Plastic Film | 20-40 | 1-2 | High | Heavy gauge wire, long distance, harsh conditions |
Steel Strapping | 500-800 | N/A (Rigid) | Very High | Extremely heavy coils, maximum security |
- Standard Cardboard: Offers minimal protection and is prone to tearing, suitable only for very light and non-demanding applications.
- Heavy-Duty Cardboard: A step up, providing better resistance but still vulnerable to moisture and rough handling.
- Reinforced Plastic Film: Significantly stronger and water-resistant, ideal for protecting against environmental elements and moderate physical stress.
- Steel Strapping: The ultimate in strength, used for securing very heavy coils where material strength is paramount.
Moisture and Corrosion Resistance
Steel is susceptible to rust, making moisture protection critical. Materials should act as effective barriers against humidity and water ingress.
Material Feature | Protection Level | Impact on Steel Wire Durability | Suitable For Environments |
---|---|---|---|
Standard Material | Low | Minimal corrosion protection | Dry, indoor storage only |
Moisture Barrier Coating | Medium | Good moisture protection | Indoor storage with moderate humidity, covered transport |
Waterproof Lamination | High | Excellent moisture protection | Outdoor storage, humid climates, sea transport |
- Standard Material (No Coating): Offers no moisture protection, leading to rapid corrosion in humid conditions.
- Moisture Barrier Coating: Provides a decent level of protection, slowing down moisture penetration.
- Waterproof Lamination: Offers the highest level of protection, creating a complete barrier against water and humidity, essential for long-term storage and harsh environments.
UV Resistance and Temperature Stability
For steel wire stored outdoors or exposed to sunlight, UV degradation and temperature fluctuations can compromise packing material integrity.
Material Property | Benefit | Relevance to Steel Wire Packing Durability |
---|---|---|
UV Stabilizers | Prevents material degradation from sunlight | Maintains material strength and barrier properties |
Temperature Stability | Material retains properties across temp ranges | Prevents cracking or becoming brittle in extreme temps |
By carefully considering these material properties and aligning them with the specific needs of your steel wire packing application, you can significantly enhance the overall durability and protection offered by your packaging.
3. Optimizing the Wire Packing Machine Process
The wire packing machine itself plays a crucial role in ensuring durability. An optimized packing process minimizes stress on both the steel wire and the packaging materials, contributing to extended lifespan and reduced damage.
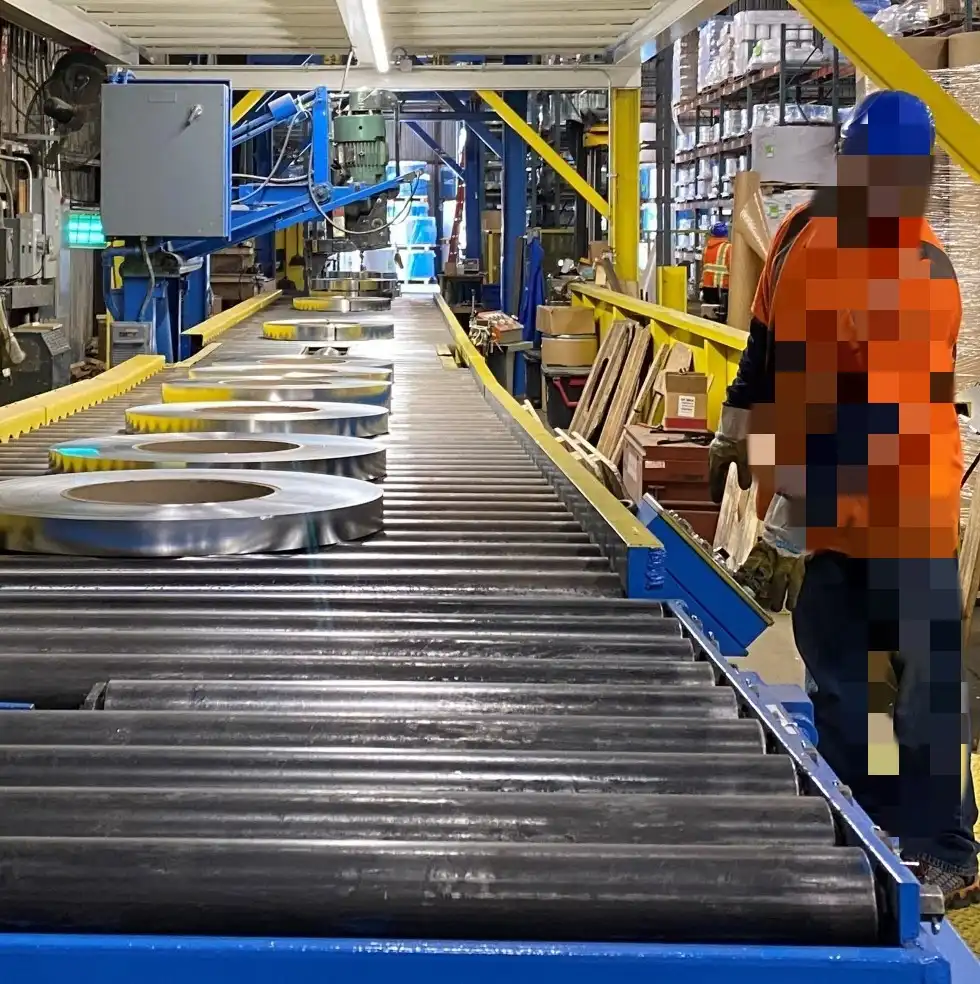
Optimizing the wire packing machine process is essential for durability improvement. Proper tension control during wrapping prevents wire deformation and package loosening. Precise sealing and securing mechanisms ensure package integrity against external forces. Regular calibration and maintenance of the machine guarantee consistent and reliable packing, minimizing stress points and extending the lifespan of both the packaging and the steel wire within.
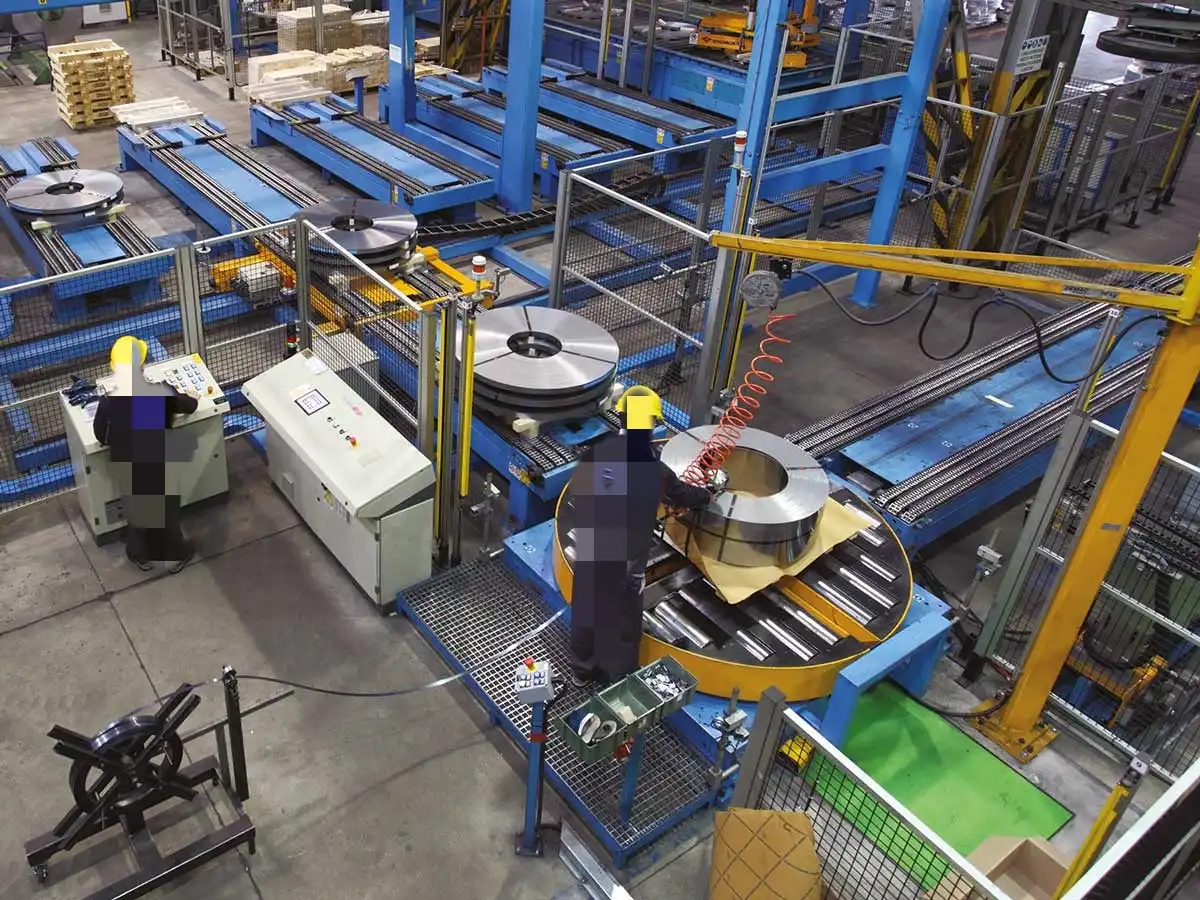
Let’s explore key aspects of process optimization that directly impact the durability of steel wire packing.
Key Optimization Areas for Enhanced Durability
Fine-tuning the machine settings and operational parameters is critical to minimizing stress and maximizing package integrity.
Tension Control and Wire Handling
Consistent and appropriate tension during wrapping is vital to prevent damage to the wire and ensure a secure, durable package.
Parameter | Issue if Not Optimized | Impact on Durability | Solution |
---|---|---|---|
Wrapping Tension | Over-tightening: Wire deformation | Wire damage, reduced material strength | Calibrate tension settings based on wire gauge and material |
Under-tightening: Loose package | Package instability, wire shifting, increased damage risk | Increase tension settings gradually until package is secure but not deforming wire | |
Wire Guiding System | Misalignment, rough guides | Wire scratching, uneven wrapping | Implement smooth, adjustable guides; regular inspection and maintenance |
- Wrapping Tension: Precise control is paramount. Over-tightening can deform the wire, while under-tightening leads to loose, unstable packages.
- Wire Guiding System: Smooth, well-maintained guides are essential to prevent surface damage to the wire during the wrapping process.
Sealing and Securing Mechanisms
The method of sealing and securing the package directly influences its ability to withstand handling and environmental stresses.
Mechanism Type | Advantages | Disadvantages | Best Use Cases |
---|---|---|---|
Heat Sealing | Strong, tamper-evident seal | Requires heat-sealable materials, energy consumption | Plastic films, environments needing high security |
Adhesive Sealing | Simple, cost-effective for some materials | Seal strength can vary with adhesive quality | Cardboard and paper-based packaging, less demanding transport |
Strapping (Steel/PET) | Extremely secure, high tensile strength | Can damage package edges if not applied carefully | Heavy coils, long-distance transport, maximum security |
- Heat Sealing: Ideal for plastic films, providing a strong, water-resistant seal. Requires precise temperature control.
- Adhesive Sealing: Simpler for cardboard but seal strength can be less reliable, especially in varying temperatures and humidity.
- Strapping: Offers the highest level of security for heavy coils, but application needs to be controlled to avoid damaging the package edges.
Regular Calibration and Maintenance
Consistent machine performance is achieved through a schedule of calibration and preventative maintenance.
Maintenance Task | Frequency | Impact on Durability | Benefits |
---|---|---|---|
Tension System Calibration | Monthly | Ensures consistent wrapping tension | Prevents wire damage and package instability |
Sealing Mechanism Check | Weekly | Verifies seal integrity and temperature accuracy | Reduces seal failures, maintains package protection |
Guide and Roller Inspection | Bi-weekly | Checks for wear, damage, and smooth operation | Prevents wire scratching and ensures even wrapping |
Lubrication of Moving Parts | Monthly | Reduces friction and wear on machine components | Extends machine lifespan and ensures consistent performance |
By implementing these optimization strategies and adhering to a rigorous maintenance schedule, you can significantly enhance the durability of your steel wire packing process and the longevity of your equipment.
4. Implementing Quality Control and Handling Best Practices
Beyond materials and machine optimization, robust quality control measures and careful handling protocols are crucial for maximizing the durability improvement of steel wire packing.
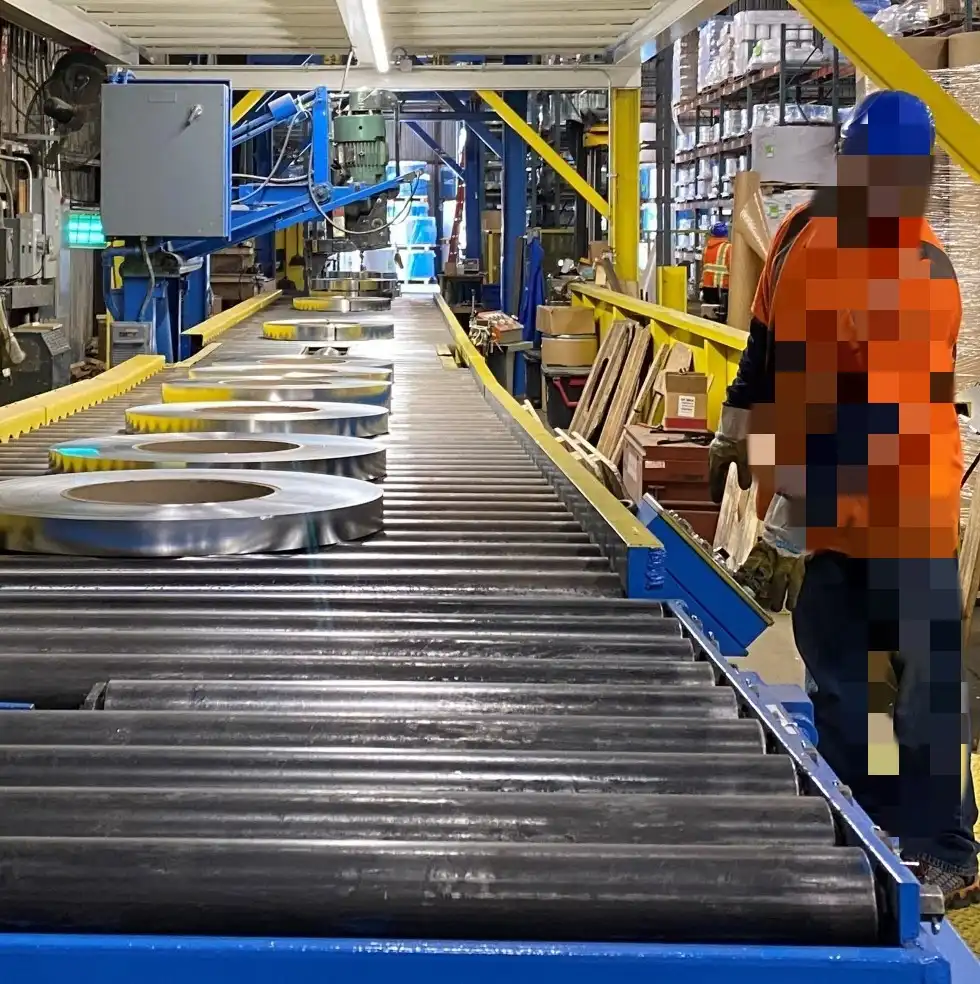
Quality control in steel wire packing involves rigorous inspection of materials, package integrity checks post-packing, and adherence to strict handling protocols. Regular audits of the packing process, coupled with operator training, ensure consistent quality and minimize damage during handling and transit. Implementing these measures is vital for maintaining package integrity and reducing losses due to damage.
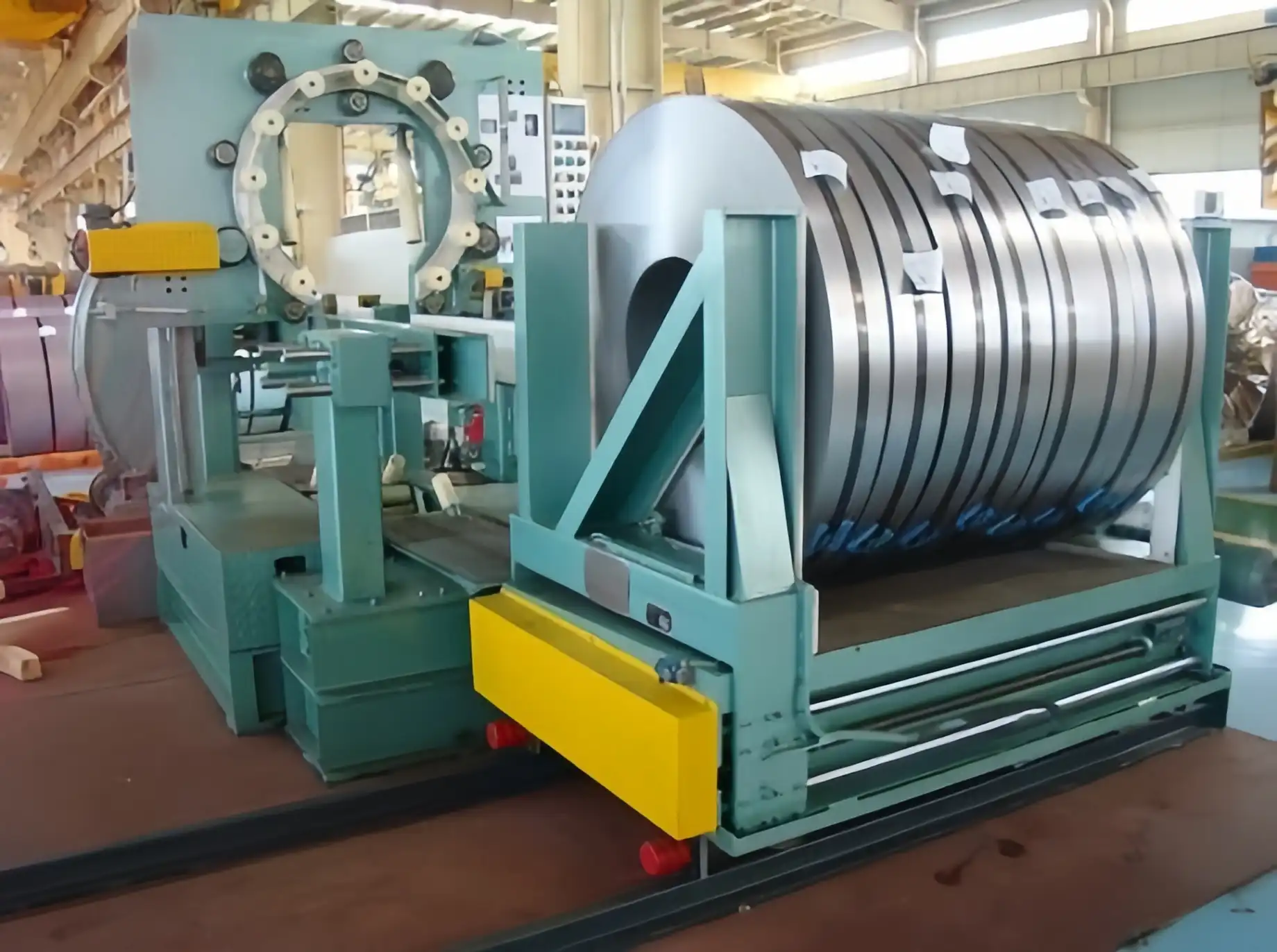
To ensure that your steel wire packing consistently meets the required durability standards, a comprehensive approach to quality control and handling is essential.
Ensuring Consistent Quality and Minimizing Damage
A multi-faceted approach encompassing inspection, training, and standardized procedures is key to maintaining high quality and reducing damage.
Comprehensive Quality Control Measures:
- Incoming Material Inspection: Before packing, inspect all materials for defects (tears, weak seals, incorrect specs). This prevents using substandard materials that compromise package integrity.
- In-Process Checks: Regularly monitor packing parameters (tension, seal quality) during operation. This ensures the machine is functioning correctly and packages are consistently formed.
- Post-Packing Inspection: After packing, check each package for seal integrity, proper wrapping, and any signs of damage. This catches any issues before packages leave the facility.
- Batch Testing: Periodically perform destructive tests on sample packages (drop tests, compression tests) to verify overall durability. This validates the effectiveness of the entire packing process.
Handling and Storage Protocols:
- Trained Handling Personnel: Ensure all personnel handling packed steel wire are trained in proper lifting, moving, and stacking techniques. This minimizes damage from mishandling.
- Designated Storage Areas: Use designated storage areas that are dry, clean, and protected from extreme temperatures and direct sunlight. This prevents environmental degradation of packages.
- Proper Stacking Procedures: Implement clear guidelines for stacking packed wire to prevent crushing or deformation of lower packages. This maximizes storage space while maintaining package integrity.
- FIFO (First-In, First-Out) System: Utilize a FIFO inventory system to ensure older stock is used first, minimizing long-term storage risks and material degradation.
By diligently applying these quality control measures and enforcing best handling practices, you can significantly enhance the durability of your steel wire packing, reduce damage rates, and ensure customer satisfaction through consistent product quality.
Conclusion
Improving the durability of steel wire packing is a multifaceted endeavor, demanding attention to material selection, machine optimization, quality control, and handling protocols. By strategically addressing each of these areas, businesses can significantly enhance the protection of their steel wire products, minimize damage during transit and storage, and ultimately reduce costs associated with material waste and product loss. Investing in durable packing solutions and robust processes not only safeguards product integrity but also contributes to operational efficiency and customer satisfaction, solidifying a commitment to quality and reliability in the steel wire industry.