1. How to Improve Corrosion Resistance in Steel Coil Packing?
Steel coil packing is crucial for various industries, serving as the initial step in manufacturing processes. Ensuring these metal coils remain free from corrosion is paramount to maintain their structural integrity and prevent costly losses. Implementing effective strategies to enhance corrosion resistance is not just an operational necessity but also a financial imperative.
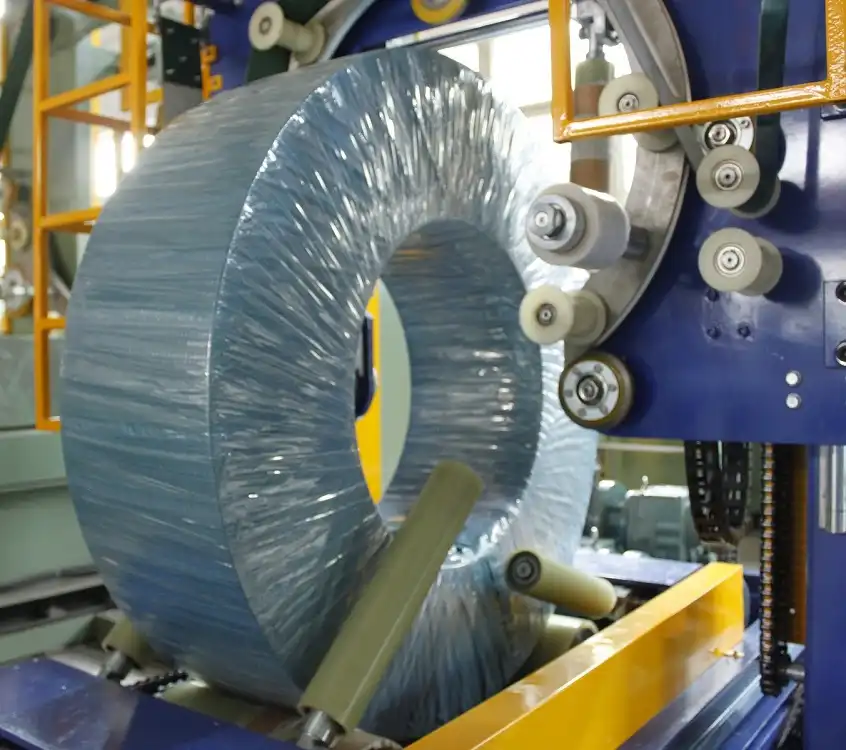
Improving corrosion resistance in steel coil packing involves several key strategies. Primarily, applying protective coatings acts as a vital barrier against moisture and oxygen. Utilizing advanced coil wrapping machines ensures tight, secure packing, minimizing exposure to corrosive elements. Regular maintenance and proper storage in controlled environments further enhance protection, significantly extending the lifespan of steel coils and reducing potential damage.

Let’s delve deeper into the critical factors and practical methods that can significantly improve corrosion resistance in steel coil packing, ensuring longevity and optimal performance.
2. Understanding the Root Causes of Rust and Corrosion in Steel Coil Packing Systems
The degradation of metal coils due to rust and corrosion poses a significant challenge in packaging systems. Identifying the primary factors that contribute to these issues is the first step in developing effective prevention strategies. Understanding these root causes allows for targeted interventions that protect metal coils from deterioration.
Rust and corrosion in steel coil packing systems are mainly triggered by environmental factors and operational practices. Moisture, oxygen, and contaminants are primary culprits, initiating oxidation and chemical reactions on metal surfaces. Fluctuations in temperature and humidity, coupled with improper storage, accelerate these corrosive processes. Addressing these underlying causes is essential to mitigate corrosion effectively and maintain coil integrity.
To truly combat corrosion, a detailed examination of these root causes is necessary. By breaking down the factors and their impacts, we can formulate robust strategies for enhanced corrosion resistance.
Deconstructing Corrosion: A Detailed Look at the Culprits
Corrosion in steel coil packing is not a singular issue but a result of multiple interacting factors. To effectively prevent it, we need to understand each factor and its specific impact on metal degradation. Let’s break down the primary causes and explore mitigation strategies in detail.
Moisture Exposure: The Prime Catalyst
Moisture is perhaps the most significant factor in rust formation. When steel is exposed to moisture, it triggers an electrochemical reaction with oxygen, leading to the formation of iron oxide, or rust. In packaging environments, moisture can come from various sources, including humidity, rain, and condensation.
Factor | Impact on Metal Coils | Mitigation Strategy |
---|---|---|
Humidity | High humidity levels increase moisture contact. | Use dehumidifiers in storage areas. |
Rain/Water Leaks | Direct water exposure accelerates rusting. | Ensure waterproof packaging and storage. |
Condensation | Temperature changes cause moisture to condense on coils. | Maintain stable temperature conditions in storage. |
Oxygen Levels: Fueling Oxidation
Oxygen is another essential element for rust formation. While eliminating oxygen entirely is impractical in most packaging scenarios, reducing exposure can significantly slow down the oxidation process.
Factor | Impact on Metal Coils | Mitigation Strategy |
---|---|---|
Air Exposure | Direct contact with air provides ample oxygen for rust. | Use airtight packaging materials. |
Ventilation | Poor ventilation traps humid air, increasing oxidation. | Ensure adequate ventilation in storage facilities. |
Contaminants: Accelerating Degradation
Various contaminants can exacerbate corrosion by introducing corrosive agents or accelerating electrochemical reactions. These contaminants can range from industrial pollutants to salts and acids.
Factor | Impact on Metal Coils | Mitigation Strategy |
---|---|---|
Industrial Pollutants | Sulfur dioxide and nitrogen oxides in industrial environments accelerate corrosion. | Store coils away from industrial areas or use air purification systems. |
Salts | Chloride ions from salts are highly corrosive, especially in coastal areas. | Use salt-resistant coatings and store coils inland. |
Acids/Alkalines | Chemical agents can react aggressively with steel, causing rapid corrosion. | Protect coils from chemical exposure and use pH-neutral cleaning agents. |
Temperature Fluctuations: Weakening Protective Barriers
Temperature changes can cause expansion and contraction of both the steel and any protective coatings. This stress can lead to cracks and failures in the coatings, exposing the steel to corrosive elements.
Factor | Impact on Metal Coils | Mitigation Strategy |
---|---|---|
Thermal Expansion/Contraction | Temperature variations cause stress on coatings, leading to cracks. | Use flexible coatings that can withstand temperature changes. |
Extreme Temperatures | Very high or low temperatures can degrade coating materials and accelerate corrosion. | Maintain moderate temperature ranges in storage. |
Improper Storage and Handling: Negligence Multiplier
Incorrect storage and handling practices can significantly increase the risk of corrosion. Stacking coils directly on the ground, storing them outdoors without protection, or rough handling that damages protective layers all contribute to accelerated corrosion.
Factor | Impact on Metal Coils | Mitigation Strategy |
---|---|---|
Ground Contact | Direct contact with the ground exposes coils to ground moisture and contaminants. | Store coils on pallets or elevated platforms. |
Outdoor Storage | Unprotected outdoor storage exposes coils to all weather elements. | Use covered storage or weather-resistant packaging. |
Handling Damage | Rough handling can scratch or chip protective coatings. | Implement careful handling procedures and protective packaging. |
By meticulously addressing each of these root causes with appropriate mitigation strategies, businesses can significantly reduce the incidence of rust and corrosion in steel coil packing systems, ensuring material longevity and minimizing losses. Investing in quality coil packing machine and proper storage facilities is a proactive step towards long-term protection and cost savings.
3. Effective Methods for Preventing Rust and Corrosion in Steel Coil Packing
Preventing rust and corrosion is not merely about addressing the causes; it requires a proactive and multifaceted approach. Implementing effective prevention methods is crucial for safeguarding metal coils, ensuring their longevity, and maintaining operational efficiency. A combination of advanced packaging systems, protective coatings, and diligent maintenance is key to success.
Effective rust prevention in steel coil packing relies on a three-pronged approach. Firstly, utilizing advanced packaging systems like coil wrapping machines to create a secure barrier against environmental elements is essential. Secondly, applying anti-corrosion coatings provides a crucial layer of defense directly on the metal surface. Finally, regular maintenance, including inspections and timely repairs, ensures the continued effectiveness of these protective measures, collectively minimizing corrosion risks.
Let’s explore each of these methods in detail, understanding how they contribute to superior corrosion resistance and long-term coil protection.
Diving into Technical Details: Comprehensive Prevention Strategies
To achieve robust corrosion prevention, a deep dive into the technical aspects of each method is necessary. Understanding the mechanics and application of these strategies allows for optimized implementation and maximum protection.
Advanced Packaging Systems: Creating the First Line of Defense
Modern packaging systems play a pivotal role in minimizing environmental exposure. Coil wrapping machines, in particular, are designed to provide tight and secure wrapping, significantly reducing contact with moisture and air.
Method | Description | Benefits |
---|---|---|
Coil Wrapping Machines | Automatically wraps coils tightly with protective films, creating a sealed barrier. | Minimizes moisture and air exposure, ensures uniform wrapping, increases packaging efficiency. |
Vacuum Packing | Removes air from the packaging before sealing, creating an oxygen-free environment. | Highly effective in preventing oxidation, ideal for long-term storage. |
Modified Atmosphere Packaging (MAP) | Replaces air inside the packaging with inert gases like nitrogen, reducing oxygen content. | Reduces oxidation, maintains product integrity, suitable for coils sensitive to oxygen. |
Pallet Inverters | Allows for easy and safe inversion of pallets, ensuring all sides of the coil are uniformly wrapped and protected. | Facilitates complete wrapping coverage, improves handling safety, ensures stability during packaging. |
Anti-Corrosion Coatings: Direct Metal Protection
Applying anti-corrosion coatings directly to steel coils is a critical step in preventing rust. These coatings act as a barrier, isolating the metal from corrosive elements. Various types of coatings offer different levels of protection and are suited for specific environments.
Coating Type | Description | Benefits | Considerations |
---|---|---|---|
Barrier Coatings (Epoxy, Polyurethane) | Create a physical barrier that prevents moisture and oxygen from reaching the metal surface. | Excellent corrosion resistance, durable, good adhesion, can be formulated for various environments. | Can be susceptible to scratches and abrasion, may require multiple coats for optimal protection. |
Sacrificial Coatings (Zinc-Rich) | Contain zinc, which is more reactive than steel. Zinc corrodes preferentially, protecting the steel beneath. | Provides excellent cathodic protection, even if the coating is scratched, self-healing properties. | May not be as durable as barrier coatings in certain abrasive environments, zinc can be consumed over time. |
Conversion Coatings (Phosphate, Chromate) | React chemically with the steel surface to form a protective layer. | Improves paint adhesion, provides moderate corrosion resistance, cost-effective. | Less durable than barrier or sacrificial coatings, chromate coatings raise environmental concerns. |
Inhibitive Pigment Coatings | Contain pigments that release corrosion inhibitors, slowing down the corrosion process. | Enhances corrosion resistance, can be combined with barrier coatings for synergistic effect. | Effectiveness depends on pigment concentration and distribution, may not be as effective in highly corrosive environments as other coating types. |
Regular Maintenance: Ensuring Long-Term Effectiveness
Even with advanced packaging and coatings, regular maintenance is crucial to ensure sustained corrosion prevention. Inspections, timely repairs, and proper storage practices are essential components of a comprehensive maintenance program.
Maintenance Activity | Description | Benefits | Frequency |
---|---|---|---|
Visual Inspections | Regularly check coils for signs of rust, coating damage, or packaging breaches. | Early detection of corrosion issues, allows for timely intervention before significant damage occurs. | Monthly or quarterly, depending on environment |
Coating Integrity Checks | Periodically assess the condition of coatings, checking for cracks, blisters, or wear. | Ensures coatings are still providing effective protection, identifies areas needing touch-up or recoating. | Annually or bi-annually |
Packaging System Audits | Verify the effectiveness of coil wrapping machines and other packaging equipment. | Ensures packaging systems are functioning correctly and providing adequate protection. | Annually |
Storage Condition Monitoring | Regularly monitor temperature and humidity levels in storage facilities. | Maintains optimal storage conditions, prevents moisture buildup and temperature fluctuations that can accelerate corrosion. | Daily or weekly |
Cleaning and Touch-Up | Clean coils to remove surface contaminants and apply touch-up coatings to damaged areas. | Removes corrosive agents, maintains coating integrity, extends the lifespan of coatings and coils. | As needed, based on inspections |
By integrating these comprehensive prevention methods, businesses can establish a robust defense against rust and corrosion in steel coil packing. Choosing the right protective treatments and implementing a diligent maintenance schedule are investments that yield significant long-term benefits.
4. Long-Term Advantages of Preventing Rust and Corrosion in Steel Coil Packing
Proactive rust and corrosion prevention offers substantial long-term benefits that extend beyond immediate cost savings. These advantages encompass operational efficiency, material longevity, and overall sustainability, contributing to a more robust and profitable business. Investing in prevention today yields significant returns in the future.
Preventing rust and corrosion in steel coil packing delivers long-term advantages across multiple facets of business operations. Extended lifespan of coils reduces replacement frequency and material costs. Decreased maintenance needs lower operational expenses and minimize downtime. Enhanced operational efficiency ensures consistent production flow and improved product quality, ultimately leading to greater profitability and sustainability.
Let’s explore these long-term benefits in detail, understanding how each contributes to a more resilient and efficient operation.
Advantages of Sustained Metal Protection: A Holistic View
The benefits of preventing rust and corrosion are multifaceted, impacting not only the bottom line but also operational effectiveness and environmental responsibility. A holistic view of these advantages reveals the true value of proactive corrosion management.
Extended Lifespan: Reducing Replacement Costs
One of the most direct benefits of corrosion prevention is the extended lifespan of steel coils. By protecting coils from degradation, businesses significantly reduce the need for frequent replacements, leading to substantial savings on material costs over time.
Benefit Category | Impact | Example |
---|---|---|
Reduced Replacements | Fewer coils need to be replaced due to rust damage. | Lower material procurement costs, reduced waste disposal expenses. |
Material Longevity | Coils maintain their structural integrity for longer periods. | Extended usability of existing coil inventory, delayed capital expenditure on new coils. |
Cost Savings | Overall reduction in material expenses over the long term. | Significant financial savings, improved budget predictability. |
Reduced Maintenance Costs: Lowering Operational Expenses
Corrosion prevention minimizes the need for frequent repairs and maintenance associated with rust damage. This translates to lower operational expenses, reduced labor costs, and minimized downtime, all contributing to improved efficiency.
Benefit Category | Impact | Example |
---|---|---|
Minimized Repairs | Less need for rust removal, coil repair, or rework. | Reduced labor costs for maintenance, lower consumption of repair materials. |
Reduced Downtime | Fewer production interruptions due to coil damage or replacement. | Increased production output, minimized delays in delivery schedules. |
Lower Labor Costs | Less manpower required for maintenance and repair activities. | Savings on wages and benefits for maintenance personnel. |
Enhanced Operational Efficiency: Streamlining Production
Protected coils perform more reliably and consistently, ensuring smoother production processes. This enhanced operational efficiency leads to increased output, improved product quality, and greater customer satisfaction.
Benefit Category | Impact | Example |
---|---|---|
Consistent Performance | Coils maintain their structural and functional integrity throughout their lifespan. | Reliable operation of packaging systems, consistent production quality. |
Improved Product Quality | Reduced risk of product contamination or damage from corroded packaging. | Higher product standards, fewer product rejections, enhanced brand reputation. |
Increased Throughput | Uninterrupted production flow due to reliable coil performance. | Higher production volumes, faster order fulfillment, improved responsiveness to market demands. |
Environmental Sustainability: Promoting Responsible Practices
Extending the lifespan of metal coils through corrosion prevention aligns with environmental sustainability goals. Reduced material consumption, lower waste generation, and minimized resource depletion contribute to a smaller environmental footprint and enhanced corporate social responsibility.
Benefit Category | Impact | Example |
---|---|---|
Reduced Material Consumption | Fewer coils are needed over time due to extended lifespan. | Conservation of raw materials, reduced demand on manufacturing resources. |
Lower Waste Generation | Less waste from replaced or corroded coils. | Decreased landfill burden, reduced environmental impact from waste disposal. |
Resource Conservation | Reduced energy and resources required for manufacturing new coils. | Lower carbon footprint, minimized environmental impact from resource extraction and processing. |
Enhanced Reputation | Demonstrates commitment to sustainability and responsible business practices. | Improved public image, enhanced stakeholder trust, potential for attracting environmentally conscious customers. |
In conclusion, investing in robust rust and corrosion prevention strategies for steel coil packing is a strategic decision that yields significant long-term advantages. From direct cost savings and enhanced operational efficiency to improved product quality and environmental sustainability, the benefits are far-reaching and contribute to a more resilient and responsible business model. Prioritizing material longevity is not just good practice; it’s smart business.
5. Choosing the Right Protective Coatings for Steel Coil Packing
Selecting the appropriate protective coating is paramount to achieving effective corrosion resistance in steel coil packing. The right coating acts as a critical barrier, shielding the steel from corrosive elements and extending its service life. However, with a wide array of coatings available, making the optimal choice requires careful consideration of various factors.
Choosing the right protective coating for steel coil packing depends on several key factors. Primarily, consider the environmental conditions the coils will face, including humidity, temperature variations, and exposure to contaminants. Evaluate the required durability and lifespan of the coils. Select coatings based on their type—barrier, sacrificial, or conversion—and their specific properties like chemical resistance, UV protection, and application method. Cost and ease of application are also important factors in making a practical and effective coating choice.
To navigate this selection process effectively, it’s essential to understand the different types of coatings and their suitability for various applications.
A Detailed Guide to Protective Coating Selection
Selecting the ideal protective coating involves a thorough understanding of coating types, performance characteristics, and application considerations. This guide provides a detailed overview to aid in making informed decisions.
Types of Protective Coatings: Understanding the Options
Protective coatings fall into several categories, each with unique mechanisms and benefits. Understanding these types is crucial for matching the right coating to specific needs.
Coating Type | Mechanism of Protection | Key Properties | Best Suited For |
---|---|---|---|
Epoxy Coatings | Barrier protection; forms a dense, impermeable layer that prevents moisture and oxygen ingress. | Excellent adhesion, high chemical resistance, good abrasion resistance, durable, versatile application methods. | General-purpose corrosion protection, industrial environments, applications requiring high durability and chemical resistance. |
Polyurethane Coatings | Barrier protection; creates a flexible, abrasion-resistant layer with good UV resistance. | Excellent flexibility, good abrasion and impact resistance, good UV and weather resistance, high gloss finish options. | Applications requiring flexibility and weather resistance, outdoor exposure, decorative finishes. |
Acrylic Coatings | Barrier protection; provides a fast-drying, cost-effective layer with good color retention. | Fast drying, good color and gloss retention, cost-effective, easy to apply, good UV resistance in some formulations. | Light to moderate corrosion environments, applications where fast drying and aesthetic appearance are important. |
Alkyd Coatings | Barrier protection; traditional oil-based coatings with good penetration and wetting properties. | Good penetration into porous surfaces, good wetting properties, relatively low cost, easy to apply. | Mild corrosion environments, general-purpose applications, cost-sensitive projects. |
Zinc-Rich Coatings | Sacrificial protection; zinc corrodes preferentially, providing cathodic protection to the steel. | Excellent cathodic protection, self-healing properties, effective even in damaged areas, good for severe corrosion environments. | Highly corrosive environments, marine applications, structures requiring long-term corrosion protection, even with potential coating damage. |
Inorganic Zinc Coatings | Sacrificial and barrier protection; combines zinc’s cathodic protection with a dense inorganic binder for enhanced barrier properties. | Superior long-term corrosion protection, excellent abrasion resistance, high heat resistance, solvent resistance. | Extremely corrosive environments, high-temperature applications, demanding industrial and marine environments. |
Performance Characteristics: Matching Coatings to Requirements
Different coatings offer varying levels of performance in key areas. Understanding these characteristics helps in selecting coatings that meet specific application demands.
Performance Characteristic | Epoxy Coatings | Polyurethane Coatings | Acrylic Coatings | Alkyd Coatings | Zinc-Rich Coatings | Inorganic Zinc Coatings |
---|---|---|---|---|---|---|
Corrosion Resistance | Excellent | Excellent | Good | Moderate | Superior | Superior |
Abrasion Resistance | Good | Excellent | Moderate | Moderate | Good | Excellent |
Chemical Resistance | Excellent | Good | Moderate | Moderate | Good | Excellent |
UV Resistance | Fair to Good | Excellent | Good to Excellent | Fair | Fair to Good | Good |
Flexibility | Fair | Excellent | Fair | Fair | Fair | Fair |
Adhesion | Excellent | Good | Good | Good | Excellent | Excellent |
Cost | Moderate | Moderate to High | Low to Moderate | Low | Moderate to High | High |
Application Considerations: Ensuring Effective Coating
Proper application is as crucial as coating selection. Factors like surface preparation, application method, and curing requirements impact the coating’s performance and longevity.
Application Factor | Description | Impact on Coating Performance |
---|---|---|
Surface Preparation | Cleaning and preparing the steel surface to remove rust, oil, and contaminants. | Ensures proper coating adhesion, crucial for long-term corrosion protection. |
Application Method | Techniques used to apply the coating, such as spraying, brushing, or rolling. | Affects coating uniformity, thickness control, and overall finish quality. |
Environmental Conditions | Temperature, humidity, and air quality during application. | Impacts coating drying time, curing process, and final film properties. |
Curing Process | Time and conditions required for the coating to fully harden and develop its protective properties. | Proper curing is essential for achieving optimal coating performance and durability. |
Coating Thickness | The thickness of the applied coating layer. | Adequate thickness is necessary for effective barrier protection and achieving desired performance characteristics. |
By carefully evaluating these factors and aligning coating selection with specific application requirements, businesses can ensure robust and long-lasting corrosion protection for their steel coil packing, maximizing protective treatments effectiveness and material longevity.
Conclusion
Improving corrosion resistance in steel coil packing is a multifaceted endeavor that demands a comprehensive and proactive approach. By understanding the root causes of rust and corrosion, implementing effective prevention methods, and selecting appropriate protective coatings, businesses can significantly enhance the longevity and reliability of their steel coils. The long-term advantages of these efforts extend beyond immediate cost savings, encompassing operational efficiency, material sustainability, and overall business resilience. Investing in robust corrosion prevention strategies is not just a best practice; it is a strategic imperative for sustained success and responsible resource management in industries reliant on steel coil packing.