Establishing a robust traceability system for steel coil packing is crucial for operational excellence, risk mitigation, and meeting customer demands in today’s dynamic supply chain. This system ensures every coil’s journey is transparent, from production to delivery.

To establish a quality traceability system for steel coil packing, focus on unique identification, data capture at each stage (production, packing, storage, shipping), and a centralized data management system. Utilize technologies like barcode scanners and RFID to accurately track coils, enhance supply chain visibility, and ensure efficient operations and customer satisfaction.
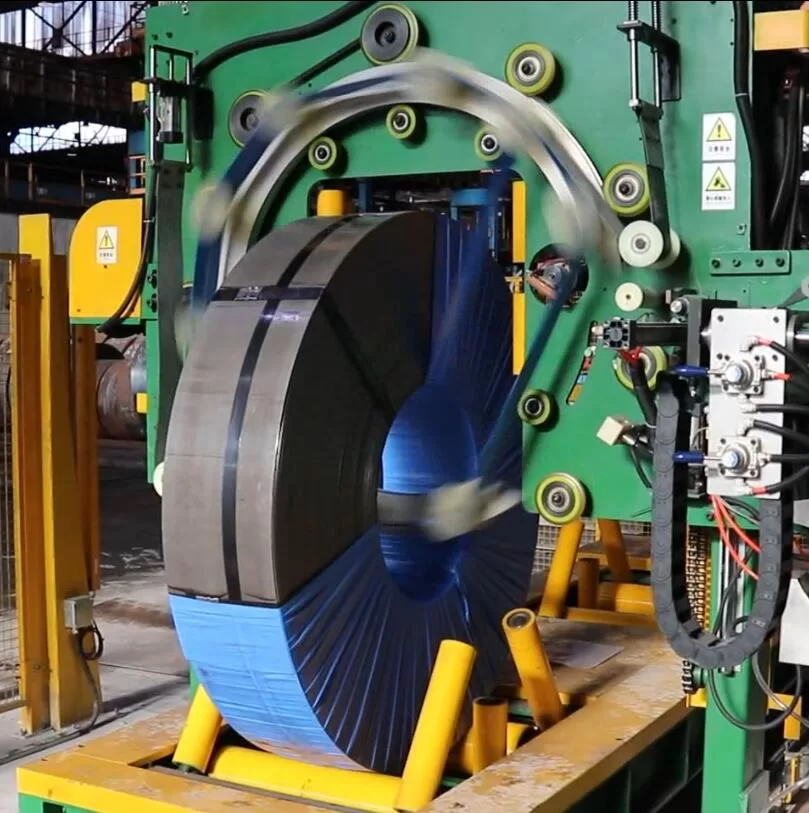
But how do you effectively implement such a system, and what are the critical components to consider? Let’s delve into the essential steps and technologies for building a quality traceability system for steel coil packing, ensuring seamless tracking and enhanced operational control.
2. Defining the Scope and Objectives of Traceability in Steel Coil Packing
Before implementing any traceability system, it’s essential to clearly define its scope and objectives within the steel coil packing process. This involves identifying what needs to be traced, why traceability is necessary, and the desired outcomes for your operations and customers.
A quality traceability system for steel coil packing aims to track each coil from production through packing, storage, and shipment to the end customer. The primary objectives include enhancing inventory accuracy, improving response times to queries, ensuring quality control, and providing verifiable proof of origin and handling, ultimately boosting customer trust and operational efficiency.
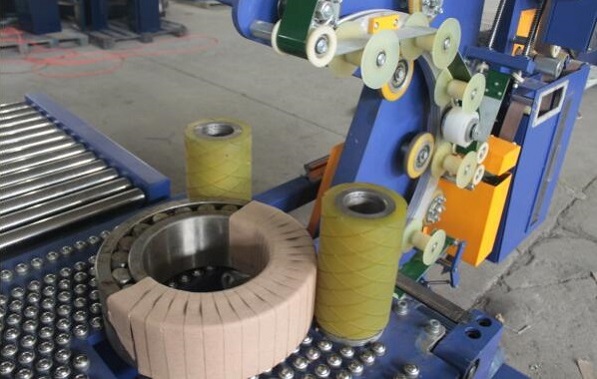
Breaking Down Traceability Objectives for Steel Coil Packing
To effectively define the scope and objectives, consider a critical breakdown of the key areas where traceability adds value. This structured approach ensures that the traceability system is designed to address specific needs and challenges within steel coil packing.
2.1. Enhanced Operational Efficiency
Traceability directly contributes to operational efficiency by streamlining processes and reducing errors.
Efficiency Metric | Without Traceability | With Traceability | Improvement |
---|---|---|---|
Inventory Check Time | Manually intensive, prone to errors, hours | Automated, accurate, minutes | Significant reduction in time and errors |
Order Fulfillment Speed | Delays due to locating coils, potential mix-ups | Quick location and verification, faster processing | Faster order processing, improved customer satisfaction |
Error Rate in Shipping | Higher due to manual tracking, mislabeling | Lower with automated verification, accurate data | Reduced shipping errors, cost savings from returns |
2.2. Improved Quality Control and Risk Mitigation
Traceability is vital for quality control, enabling quick identification and isolation of potentially defective coils.
Quality Control Aspect | Without Traceability | With Traceability | Benefit |
---|---|---|---|
Defect Identification | Delayed, batch-based recalls, wide impact | Immediate, targeted recalls, minimal disruption | Faster response to quality issues, reduced risk |
Complaint Resolution | Lengthy investigation, difficult to pinpoint | Rapid data access, easy root cause analysis | Quicker resolution, improved customer confidence |
Compliance Audits | Time-consuming, manual data collection | Streamlined, digital records, readily available | Easier and faster compliance verification |
2.3. Enhanced Customer Satisfaction and Trust
In today’s market, customers demand transparency. Traceability provides verifiable information, building trust and satisfaction.
Customer Expectation | Without Traceability | With Traceability | Impact |
---|---|---|---|
Proof of Origin | Difficult to verify, reliance on paperwork | Easily verifiable digital record | Enhanced trust, competitive advantage |
Delivery Transparency | Limited updates, reactive communication | Real-time tracking, proactive updates | Improved customer experience, loyalty |
Responsiveness to Queries | Slow, manual checks, delayed responses | Instant data access, quick, accurate answers | Faster, better service, stronger relationships |
By clearly defining these objectives and understanding the benefits across operational efficiency, quality control, and customer satisfaction, businesses can create a traceability system that is not only effective but also strategically aligned with their goals for steel coil packing.
3. Key Components of a Steel Coil Packing Traceability System
A quality traceability system for steel coil packing relies on several key components working in harmony. These include unique identification methods, robust data capture technologies, a centralized data management system, and seamless integration with existing operational workflows.
Essential components of a steel coil packing traceability system are unique identifiers (barcodes, QR codes, RFID tags), reliable data capture tools (scanners, mobile devices), a central database to store and manage traceability data, and system integration with existing ERP and WMS platforms for streamlined data flow and operational visibility.
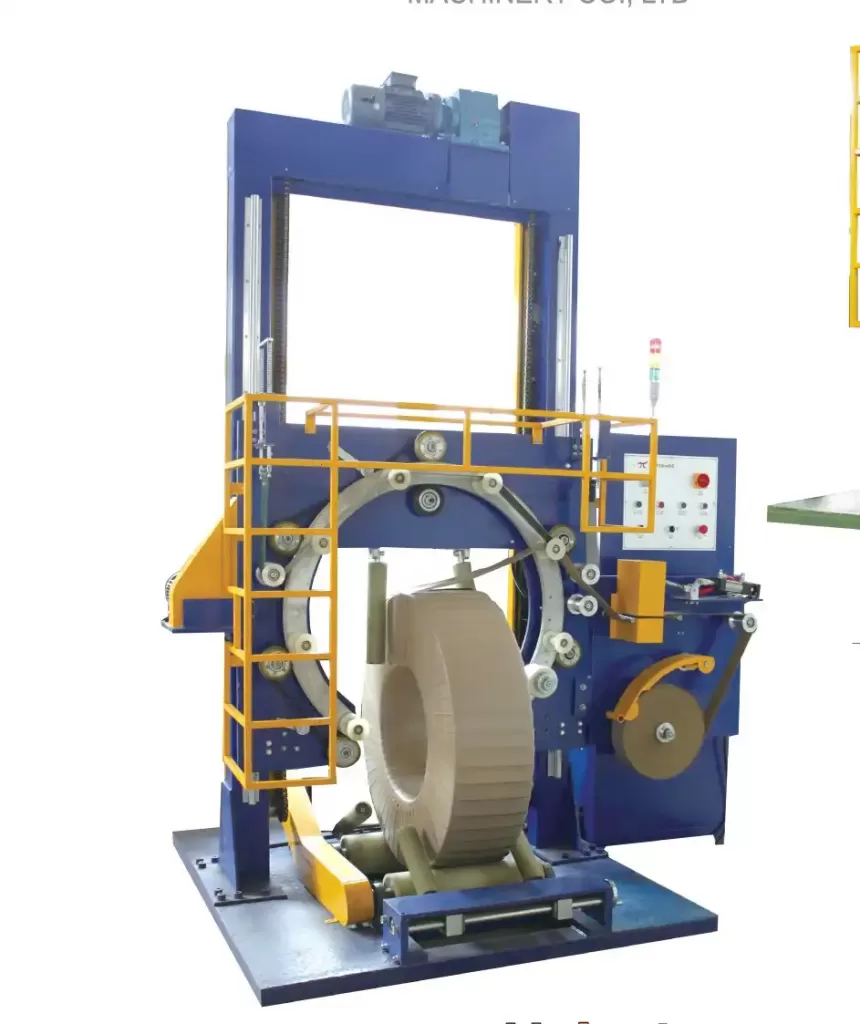
Diving into the Technical Details: Essential Elements for Effective Traceability
To ensure a robust and efficient system, each component must be carefully selected and implemented. Let’s explore the technical aspects of these key elements in detail.
3.1. Unique Identification Methods
The foundation of any traceability system is the ability to uniquely identify each steel coil. Several technologies can be employed:
- Barcodes and QR Codes: Cost-effective and widely adopted, these optical labels can store essential coil information. QR codes offer higher data density and readability from various angles.
- RFID Tags: Radio-frequency identification allows for wireless tracking and reading of tags, even without direct line of sight. Passive RFID tags are economical for coil-level tracking, while active tags can provide real-time location data.
- Direct Part Marking (DPM): For permanent traceability, especially in harsh environments, DPM methods like laser etching or dot peening can directly mark coils with unique identifiers.
3.2. Data Capture Technologies
Accurate and efficient data capture is critical at each stage of the coil’s journey.
- Barcode Scanners: Handheld or fixed scanners can quickly read barcodes and QR codes on coil labels, feeding data into the traceability system.
- RFID Readers: Stationary or mobile RFID readers can automatically capture data from RFID tags, ideal for bulk scanning during receiving, dispatch, or inventory checks.
- Mobile Devices: Smartphones or tablets equipped with scanning apps can empower workers to capture data on the go, enhancing flexibility and real-time updates.
- Automated Data Capture Systems: Integrating scanners and readers with coil packing machines and conveyor systems automates data capture, reducing manual effort and increasing accuracy.
3.3. Centralized Data Management System
A robust database is the backbone, storing and managing all traceability data.
- Cloud-Based Platforms: Scalable and accessible from anywhere, cloud platforms offer centralized data storage, real-time visibility, and enhanced collaboration.
- On-Premise Servers: For organizations with stringent data security requirements, on-premise servers provide greater control over data storage and access.
- Database Features: The system should support:
- Data Integrity: Ensuring accuracy and reliability of data.
- Data Security: Protecting data from unauthorized access and cyber threats.
- Scalability: Accommodating growing data volumes and system users.
- Reporting and Analytics: Generating reports and insights for operational improvements.
3.4. System Integration
Seamless integration with existing systems is crucial for data flow and avoiding data silos.
- ERP Integration: Connecting the traceability system with Enterprise Resource Planning (ERP) systems ensures alignment of production, inventory, and order data.
- WMS Integration: Integration with Warehouse Management Systems (WMS) streamlines warehouse operations, optimizing storage, retrieval, and dispatch processes based on real-time traceability data.
- API Connectivity: Application Programming Interfaces (APIs) facilitate data exchange between the traceability system and other business applications, ensuring data consistency and interoperability.
By carefully considering and implementing these key components – from identification methods to data management and system integration – businesses can build a comprehensive and effective Quality traceability system for steel coil packing, driving operational excellence and customer satisfaction.
4. Implementing a Step-by-Step Traceability System for Steel Coil Packing
Implementing a traceability system is a phased approach, requiring careful planning and execution. A structured, step-by-step methodology ensures a smooth transition and successful deployment.
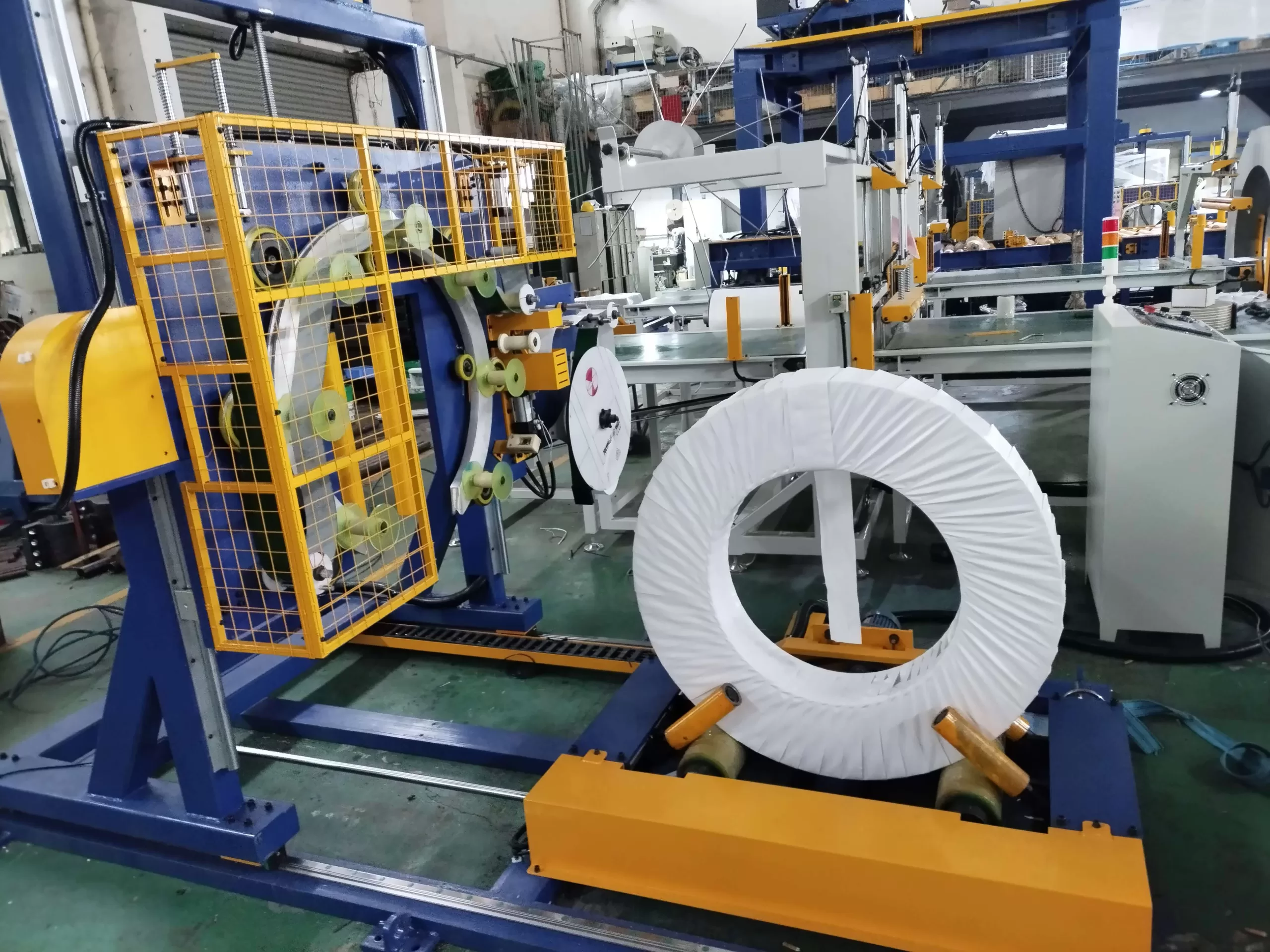
Implementing a traceability system for steel coil packing involves several key steps: assess current processes, define traceability points, select appropriate technology (identification, data capture, software), pilot test the system, train personnel, full-scale deployment, and continuous monitoring and improvement. A phased approach minimizes disruption and ensures effective system integration.
Phased Implementation: A Practical Guide to Traceability Deployment
To ensure a successful traceability system implementation, follow these steps:
- Process Assessment: Conduct a thorough analysis of current steel coil packing processes. Identify critical control points, data collection points, and areas needing improvement. Map the entire coil flow from production to dispatch.
- Define Traceability Points: Determine specific points in the process where data capture is essential. This includes:
- Production Stage: Coil ID generation, production date, batch number, quality data.
- Packing Stage: Packing date, packing material details, operator ID.
- Storage Stage: Storage location, date of entry/exit.
- Shipping Stage: Order details, shipping date, destination, carrier information.
- Technology Selection: Choose appropriate technologies based on your needs and budget. Consider:
- Identification: Barcodes, QR codes, RFID, DPM – select based on environment, data volume, and reading range requirements.
- Data Capture: Scanners, RFID readers, mobile devices, automated systems – choose based on workflow, accuracy needs, and integration capabilities.
- Software: Cloud-based or on-premise, consider scalability, security, integration, and reporting features.
- Pilot Testing: Implement the system in a limited area or for a specific product line. This allows for testing workflows, identifying issues, and refining processes before full deployment.
- Personnel Training: Train operators and staff on new processes and technologies. Ensure they understand the importance of accurate data capture and system usage.
- Full-Scale Deployment: Roll out the system across all steel coil packing operations. Monitor implementation closely and provide ongoing support to users.
- Continuous Monitoring and Improvement: Regularly review system performance, analyze data, and identify areas for optimization. Traceability is not a one-time project but an ongoing process of improvement.
5. Benefits and ROI of a Steel Coil Packing Traceability System
Implementing a quality traceability system for steel coil packing yields significant benefits and a strong return on investment (ROI). These advantages span operational efficiencies, cost savings, risk reduction, and enhanced customer satisfaction.
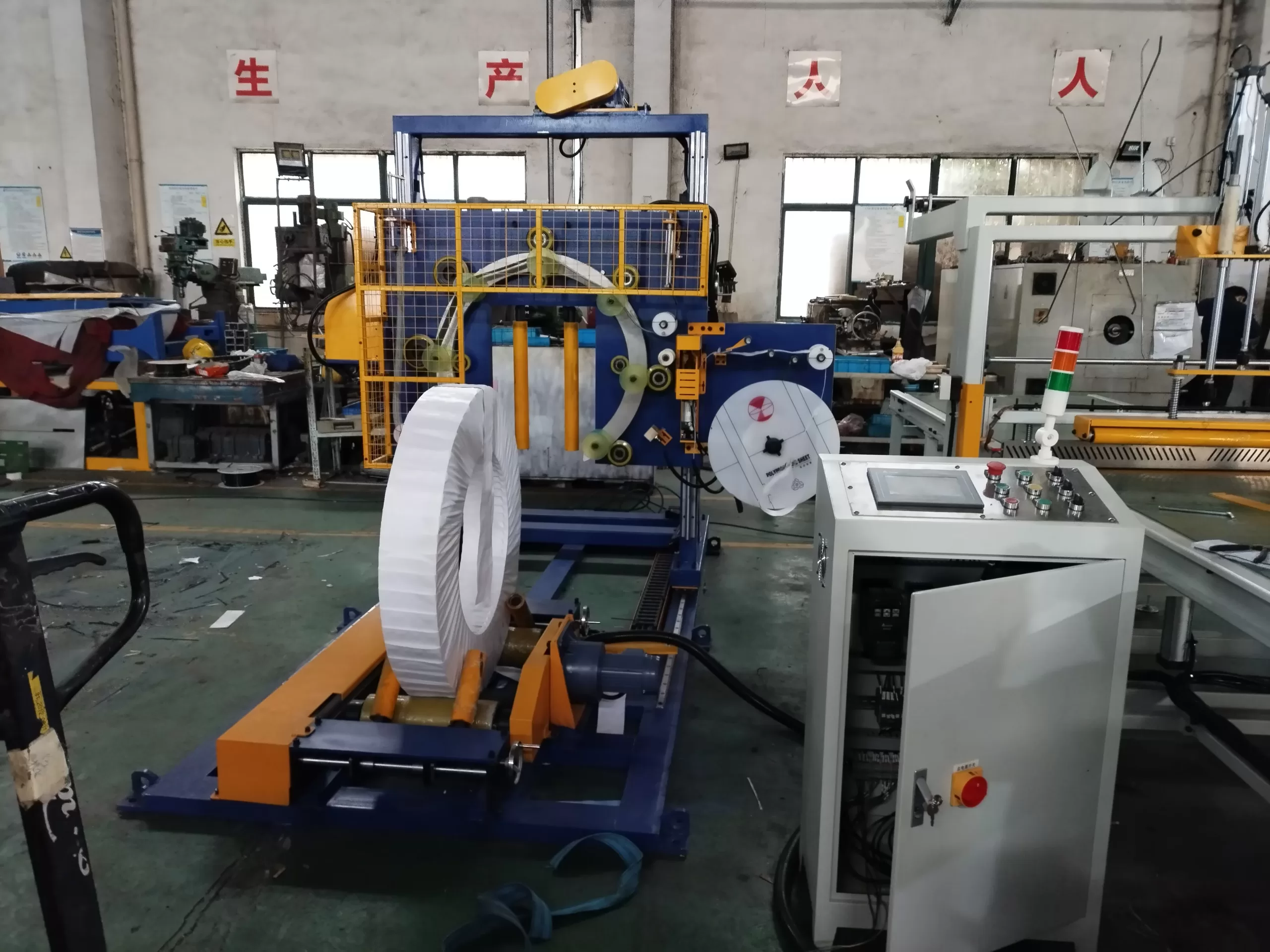
Investing in a steel coil packing traceability system provides substantial ROI through improved inventory management (reduced losses, optimized stock levels), streamlined operations (faster processing, fewer errors), enhanced quality control (minimized defects, quicker recalls), and increased customer satisfaction (transparency, reliability). These benefits collectively drive cost savings and revenue growth.
Conclusion
Establishing a quality traceability system for steel coil packing is a strategic imperative in today’s competitive landscape. By focusing on clear objectives, key components, and a phased implementation, businesses can unlock significant operational efficiencies, enhance quality control, and build stronger customer relationships. The ROI derived from improved processes, reduced risks, and increased transparency makes traceability a valuable investment for any steel coil packing operation aiming for excellence.