1. How to Ensure Fire Resistance in Steel Coil Packing?
Ensuring fire resistance in steel coil packing is critical for industries where these materials are essential, from construction to manufacturing. Protecting steel coils from fire not only safeguards valuable assets but also ensures operational continuity and personnel safety. This article explores essential strategies to enhance fire resistance in steel coil packing, covering materials, techniques, and safety standards.

To ensure fire resistance in steel coil packing, a comprehensive approach is necessary. This includes using fire-resistant packing materials and coatings, implementing proper packing techniques to minimize fire spread, and rigorously adhering to safety standards. Integrating fire-resistant cables and conducting regular fire safety assessments are also crucial steps to protect steel coils from fire hazards and maintain structural integrity.
Understanding the methods and materials for fire resistance is paramount for preventing catastrophic losses and ensuring compliance with safety regulations. Let’s delve into the key aspects of fire resistance in steel coil packing and how to implement effective protection measures.
2. Understanding Fire Resistant Cables in Steel Wire Packing
Fire-resistant cables are a fundamental component of safety systems in environments utilizing steel wire packing. These specialized cables are designed to maintain their functionality during a fire, ensuring that critical systems continue to operate when they are needed most. Selecting the correct type of fire-resistant cable is the first step in enhancing the fire safety of steel wire packing systems.
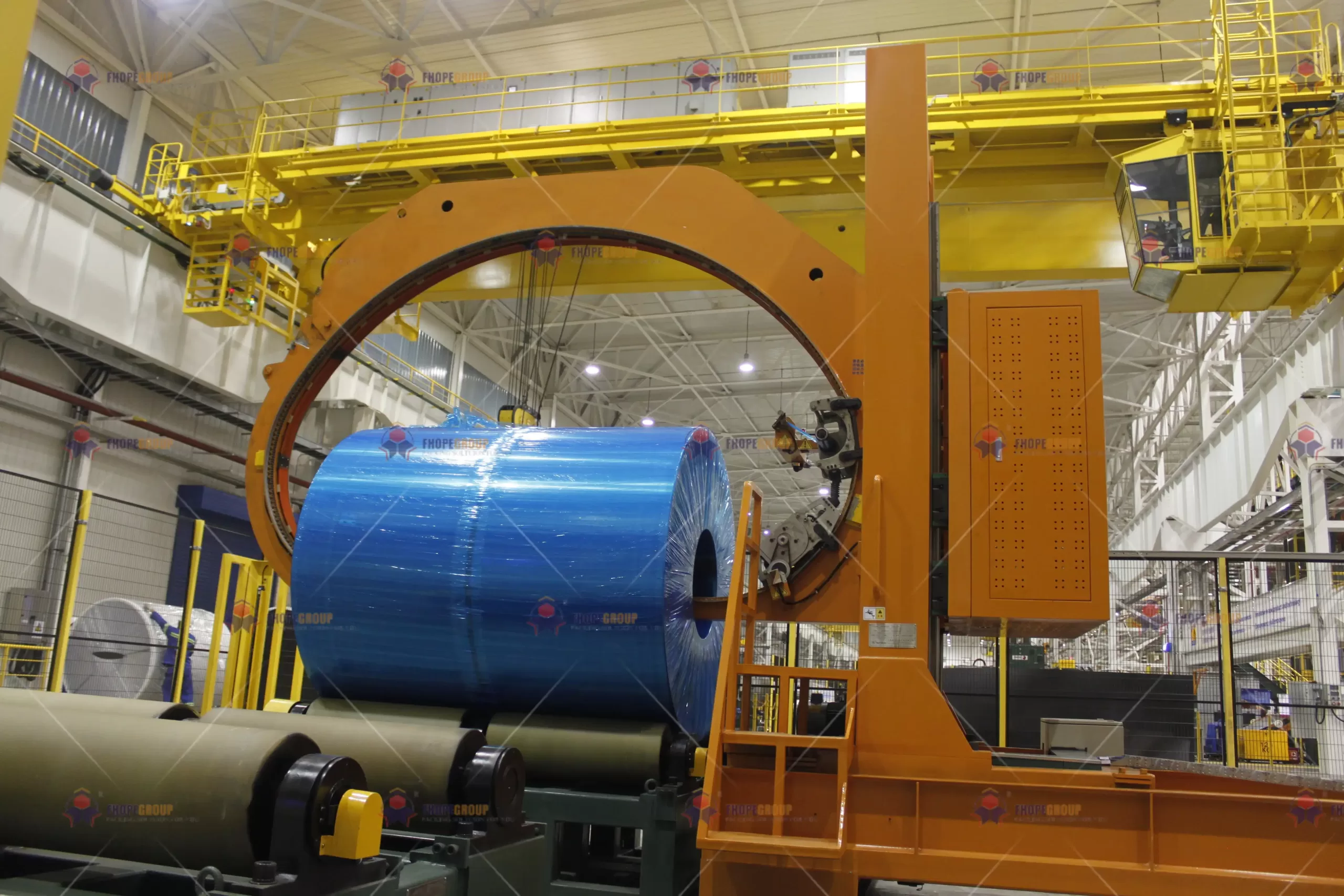
Fire-resistant cables are distinct from flame-retardant cables. While flame-retardant cables slow down the spread of fire, fire-resistant cables are engineered to maintain circuit integrity during fire exposure. Key types include flame retardant, Low Smoke Zero Halogen (LSZH), and true fire-resistant cables with mica tape insulation. Choosing the appropriate cable type depends on a careful assessment of the specific fire risks and operational needs of the steel wire packing application, balancing both cost and safety considerations.
To fully grasp how to ensure fire resistance, it is essential to differentiate between cable types and understand the standards that govern their performance. This knowledge is vital for making informed decisions that significantly improve safety and prevent potential system failures in fire situations.
Delving Deeper into Fire Cable Standards: IEC vs. UL and Beyond
The realm of fire-resistant cables is governed by a complex network of standards, each defining specific performance criteria and testing methodologies. Navigating these standards is crucial to ensure that the selected cables and packing methods meet the required safety levels. Let’s examine some key standards and their implications for steel wire packing applications.
Two primary sets of standards dominate the fire-resistant cable industry: IEC (International Electrotechnical Commission) and UL (Underwriters Laboratories). Although both aim to ensure safety, they differ in their testing approaches and regional prevalence. IEC standards are globally recognized, while UL standards are predominantly used in North America. Beyond these, British Standards (BS) also play a significant role, especially in regions adhering to UK regulations.
Understanding the nuances of these standards is not merely about compliance; it’s about implementing a robust fire safety strategy for steel wire packing installations. Proper specification guarantees that in a fire event, essential circuits remain operational, facilitating safe shutdowns, emergency responses, and minimizing damage.
Standard Body | Standard Designation | Focus | Key Tests | Geographical Focus |
---|---|---|---|---|
IEC | IEC 60332-1 | Flame retardancy of single cables | Single cable vertical flame test | International |
IEC | IEC 60332-3 | Flame retardancy of bundled cables | Bundled cable vertical flame test | International |
IEC | IEC 60331 | Fire resistance – circuit integrity | Fire survival test at specified temperatures and durations | International |
UL | UL 910 (CMP) | Plenum cables – highest fire safety | Steiner Tunnel Test, smoke density | North America |
UL | UL 1666 (CMR) | Riser cables – commercial grade | Riser Flame Test | North America |
UL | UL 1581 (CM/CMG) | Commercial/General Purpose Cables | Vertical Tray Flame Test | North America |
BS | BS 8434 | Enhanced Fire Resistance | Modified fire tests with impact, water spray, realistic fire curve | UK |
BS | BS EN 50200 | Fire Resistance for Data/Signal Cables | Flame test at 842°C for durations PH15, PH30, PH60, PH120 | UK/Europe |
BS | BS 8519 | System Approach to Fire Resistance | Code of Practice for system selection and installation | UK |
Critical Differences and Considerations:
- Flame Retardancy vs. Fire Resistance: IEC 60332 primarily addresses flame retardancy (preventing fire spread), whereas IEC 60331 and UL/BS fire-resistance ratings (like PH ratings in BS EN 50200) focus on maintaining circuit integrity during a fire. The choice depends on the application’s safety priorities. For critical infrastructure using steel wire packing, fire resistance is often paramount.
- Smoke and Halogen Content: Standards like IEC 61034 (smoke density) and IEC 60754 (halogen content) consider hazards beyond flames. Low Smoke Zero Halogen (LSZH) cables are increasingly favored for enclosed spaces due to reduced toxic fumes and smoke, enhancing evacuation safety.
- Performance Levels: Fire-resistance standards specify performance levels, often indicated by time (e.g., PH30, PH60, PH120 in BS EN 50200), showing how long a cable maintains circuit integrity under fire conditions. Higher ratings offer greater safety but may increase costs.
- System vs. Component Certification: Cable certifications are often component-level. BS 8519 emphasizes system-level fire performance, considering installation and all components, not just cables in isolation. This holistic approach is vital for real-world fire safety in steel wire packing systems.
3. Flame Retardant Measures for Steel Wire Packing
Beyond fire-resistant cables, implementing specific flame retardant measures directly on the steel wire packing itself provides an additional and critical layer of protection. These measures are designed to prevent ignition, slow the spread of flames, and effectively contain fires within the packing area.
Several effective flame retardant measures can be applied to steel wire packing. These include utilizing fire retardant coatings on packing materials, applying fireproof wraps, and using blocking materials to seal gaps. Properly sealing cable penetrations and installing fire barriers within packing areas are also crucial. Collectively, these measures significantly minimize fire risks associated with steel wire packing and enhance overall safety.
Let’s explore the technical details and best practices for implementing these flame retardant measures effectively, ensuring comprehensive fire protection for steel wire packing installations in various industrial settings.
Technical Details of Flame Retardant Coatings and Wrappings for Steel Coils
Flame retardant coatings and wrappings are direct and powerful interventions to enhance the fire resistance of steel wire packing. These materials act as a barrier, effectively delaying ignition and slowing down the propagation of flames. Understanding the different types of materials available and the best application techniques is key to maximizing their protective effectiveness.
Types of Flame Retardant Coatings:
- Intumescent Coatings: These coatings are exceptionally effective. Upon exposure to heat, they undergo a chemical reaction that causes them to expand and char, forming a thick, insulating layer that protects the underlying steel and packing material. Intumescent coatings are particularly suitable for steel coil packing because they can be applied to complex shapes and provide excellent thermal insulation, significantly delaying heat transfer.
- Cementitious Coatings: Typically thicker than intumescent coatings, cementitious coatings offer robust fire protection. They are less flexible but provide superior fire resistance and physical protection against impact and abrasion. Cementitious coatings are ideal for areas where steel wire packing requires a more rigid and impact-resistant fire barrier, such as in high-traffic industrial environments or areas prone to physical stress.
- Ablative Coatings: Ablative coatings function by absorbing heat and dissipating it through a controlled decomposition process. As the coating ablates (sacrifices its surface layer), it absorbs energy and releases it, preventing heat from reaching the steel coil packing. These coatings are particularly effective in long-duration fires and are frequently used in demanding industrial environments where prolonged fire exposure is a significant risk.
Application Techniques for Coatings:
- Spraying: Spray application is highly efficient for covering large areas of steel wire packing quickly and uniformly. Airless sprayers are commonly used for applying thicker coatings like intumescent and cementitious types, ensuring an even and consistent layer of protection over large surface areas.
- Brushing and Rolling: These methods are best suited for smaller areas or for detailed applications requiring precision. Brushing and rolling allow for more controlled application, making them useful for touch-ups, intricate packing configurations, or areas with limited access.
Fireproof Tapes and Wraps:
- Mica Tape: Mica tape, crucial for fire-resistant cables, is also valuable for wrapping steel wire packing bundles. It offers excellent electrical insulation and exceptional fire resistance, capable of withstanding extremely high temperatures. Mica tape maintains its structural integrity even as surrounding materials burn away, providing continued protection.
- Silicone Rubber Tapes: These tapes offer a combination of good flexibility and fire resistance. They are often used for wrapping cable joints and splices within steel wire packing, creating a fire-resistant seal at vulnerable connection points. Silicone rubber tapes are effective in maintaining insulation and preventing fire spread through cable systems.
- Fiberglass Tapes with Fire Retardant Coatings: These tapes combine the inherent strength of fiberglass with added flame retardant properties. They are durable and provide mechanical protection in addition to fire resistance. Fiberglass tapes are suitable for applications requiring both fire and physical protection, such as in harsh industrial environments.
Best Practices for Coatings and Wrappings:
- Surface Preparation: Ensure the steel wire packing surface is thoroughly clean, dry, and free of rust, oil, or other contaminants before applying any coating or wrapping. Proper surface preparation is critical for ensuring adequate adhesion and long-term performance of the fire retardant materials.
- Correct Thickness: Apply coatings and wrappings to the thickness recommended by the manufacturer. Applying too thin a layer may compromise fire resistance, while excessive thickness can be unnecessarily costly and may not provide additional benefit. Adhering to recommended thicknesses ensures optimal performance.
- Overlap and Sealing: When using tapes and wraps, ensure sufficient overlap at joints and seams to prevent fire from penetrating through gaps. Seal edges and terminations properly to maintain continuous fire protection across the entire packed area, eliminating weak points.
- Compatibility: Verify that coatings and wrappings are chemically compatible with the steel wire packing materials and cable jacketing. Incompatibility can lead to degradation of the materials over time, reducing the effectiveness of the fire protection system and potentially causing damage to the packing or cables.
By carefully selecting and correctly applying flame retardant coatings and wrappings, and by diligently adhering to best practices, you can significantly enhance the fire resistance of steel wire packing. These measures, combined with the use of fire-resistant cables, form a robust and comprehensive fire safety strategy, crucial for protecting industrial facilities and infrastructure.
4. Safety Standards and Testing for Fire Resistance in Steel Wire Packing
Safety standards and rigorous testing are the essential verification backbone for ensuring fire resistance in steel wire packing. Compliance with recognized standards ensures that materials and methods meet established safety benchmarks. Testing validates performance and provides quantifiable proof of fire resistance capabilities, building confidence in safety systems.
Adherence to safety standards and thorough testing are paramount for verifying fire resistance in steel wire packing. Key standards include IEC 60331, UL 910, and BS 8434, each specifying test methods and performance criteria. Testing procedures typically involve direct flame exposure, temperature monitoring, and circuit integrity checks during fire conditions. Compliance and rigorous testing ensure that fire resistance measures are effective and reliable, providing essential confidence in safety systems designed to protect steel coil packing.
Let’s delve deeper into the specific standards and testing methodologies that are critical for ensuring fire-resistant steel wire packing, emphasizing the importance of certification and ongoing quality control to maintain safety and reliability over time.
Comparative Analysis of Fire Resistance Standards and Regulations for Steel Coil Packing
Navigating the landscape of fire resistance standards necessitates a comparative understanding of different regulations and their testing methodologies. While we previously touched upon IEC and UL standards, expanding our analysis to include British Standards (BS) offers a more comprehensive perspective on fire safety in steel wire packing. A comparative approach is crucial for selecting the most appropriate standards based on geographical location, industry-specific requirements, and risk assessment.
Key Fire Resistance Standards Comparison:
Standard | Focus Area | Key Tests | Application Context | Strengths | Limitations |
---|---|---|---|---|---|
IEC 60331 | Circuit Integrity during Fire | Flame test (750°C or 830°C, varying durations), impact, water spray | General fire resistance for cables | Widely recognized internationally, comprehensive testing options | Component level testing, system performance not directly addressed |
UL 910 (CMP) | Plenum Cable Fire Safety | Steiner Tunnel Test, flame spread, smoke density | Cables in air plenums (ventilation spaces) | Stringent smoke and flame spread requirements, high safety level | Primarily North American standard, may be over-specified for some applications |
BS 8434 | Enhanced Fire Resistance | Modified fire tests incorporating impact and water spray, realistic fire curve | Enhanced fire safety for critical life safety systems | Realistic fire scenario testing, considers mechanical and environmental stresses | Primarily UK standard, may require specific equipment for testing |
BS EN 50200 | Fire Resistance for Data/Signal Cables | Flame test (842°C, durations PH15, PH30, PH60, PH120) | Fire resistance for small diameter cables, data/signal circuits | Specific to data and signal cables, performance levels defined by time | May not be as stringent as BS 8434 for power cables in critical applications |
BS 8519 | System Approach to Fire Resistance | Code of Practice for selection and installation of fire-resistant systems | Overall fire safety of installed cable systems | System-level focus, considers installation and components together | Not a product standard, guidance for system design and installation; requires integration with product standards |
Implications for Steel Wire Packing:
- Choosing the Right Standard: The selection of standards should be application-driven. For critical life safety systems within buildings, BS 8434 or BS 8519 (system approach) are highly relevant. For general industrial applications, IEC 60331 provides a widely accepted benchmark. UL 910 is essential for plenum spaces where stringent smoke control is paramount to ensure safe evacuation routes.
- Testing Beyond Standards: While standards provide a vital framework, consider supplementary testing based on specific risks present in your operational environment. For instance, if steel wire packing is subjected to vibration, chemical exposure, or extreme temperatures, incorporate these factors into customized testing protocols to simulate real-world conditions accurately.
- Certification and Third-Party Verification: Seek third-party certification from reputable bodies to validate compliance with chosen standards. Independent certification provides an unbiased assurance of product performance and quality, enhancing credibility and trust in your fire safety measures.
- Regular Audits and Inspections: Fire resistance is not a one-time achievement. Implement regular audits and inspections as part of a proactive maintenance program to ensure that fire protection measures remain effective over time. Routinely check coatings, wrappings, cable installations, and fire barriers for any signs of damage, degradation, or wear that could compromise their protective capabilities.
By thoroughly understanding and diligently applying these standards, and by rigorously testing materials and assemblies, you can build substantial confidence in the fire resistance of your steel wire packing systems. This proactive and standards-driven approach minimizes risks and maximizes safety in fire-critical environments, protecting both assets and personnel.
5. The Role of Coil packing machine in Enhancing Safety
While seemingly indirectly related to fire resistance, wire packing machines play a significant role in enhancing the overall safety, including fire safety, of steel wire packing installations. Efficient and consistent packing contributes directly to cable integrity, reduces physical damage, and facilitates organized installations, all of which have positive implications for fire safety.
Wire packing machines significantly enhance safety by ensuring consistent and secure packing of steel wires. This minimizes physical damage to cables during handling and transportation, thereby preserving their fire-resistant properties. Organized packing also leads to neater and more accessible cable installations, reducing congestion and potential fire hazards. Automated packing processes improve both efficiency and consistency, contributing substantially to overall safety and reliability in steel wire systems.
Let’s explore in detail how the automation and precision offered by wire packing machines indirectly but effectively contribute to improved fire safety in steel wire applications, highlighting the benefits beyond just packing efficiency.
Wire packing machines, though not directly applying fire retardant materials, contribute to fire safety in several critical ways through their operational advantages:
- Damage Prevention: Manual packing processes can often lead to cable bending, kinking, and abrasion, potentially damaging the cable jacketing and critically compromising the fire-resistant layers beneath. Wire packing machines, on the other hand, ensure gentle and controlled handling of cables. This automated, precise handling minimizes physical stress on cables, effectively preserving their structural and fire-resistant integrity from manufacturing through installation. Undamaged cables are inherently less susceptible to electrical faults and the initiation of fires, enhancing overall safety.
- Consistent Packing Density: Uniform packing density, consistently achieved by automated machines, significantly reduces air gaps within cable bundles. Air gaps can act as channels that facilitate rapid fire propagation, allowing flames to spread quickly through cable runs. Denser, machine-packed bundles are less likely to support rapid fire spread due to the reduced oxygen availability within the packed structure, effectively slowing down or preventing fire progression.
- Organized Cable Management: Wire packing machines are instrumental in facilitating neat and highly organized cable coiling and packing configurations. This leads to tidier and more structured cable installations in trenches, tunnels, and within buildings. Organized cable runs substantially reduce congestion, improve airflow (preventing heat buildup that can contribute to fire risk), and make it significantly easier to access and maintain cables for inspections or repairs. Improved cable management directly translates to a reduced fire risk and enhanced operational safety.
- Efficient Application of Protective Wraps: Advanced wire packing machines can be integrated with automated systems designed to apply fire retardant wraps or tapes directly during the packing process. This automation ensures consistent and efficient application of these crucial protective layers, directly enhancing fire resistance as an integral part of the packing operation. Automated application reduces variability and ensures every bundle receives uniform protection, improving overall system reliability.
- Reduced Human Error: Automated machines inherently minimize the potential for human error in packing processes. Consistent tension during wrapping, proper coiling techniques, and accurate application of protective wraps are all ensured by the machine’s precision and programmed parameters. This reduces variability and potential flaws that could compromise fire safety, offering a higher degree of reliability compared to manual processes which are prone to inconsistencies.
- Improved Traceability and Quality Control: Modern wire packing machines are often equipped with integrated data logging and quality control systems. This allows for detailed tracking of packing parameters, ensuring consistency across all packed bundles, and providing comprehensive records for quality audits and compliance verification. Traceability is crucial for demonstrating and verifying that fire safety standards are consistently met in every packed bundle, enhancing accountability and quality assurance.
In essence, wire packing machines, through their precision, consistency, and potential for automation, establish a solid foundation for enhanced fire safety in steel wire applications. By minimizing damage, ensuring organized installations, and facilitating the efficient and reliable application of protective measures, these machines play a vital, albeit indirect, role in fire prevention and mitigation strategies within industrial and commercial settings.
Conclusion
Ensuring fire resistance in steel coil packing is a multi-faceted endeavor that demands a combination of fire-resistant materials, proactive safety measures, rigorous testing protocols, and meticulous attention to installation practices. From the initial selection of appropriate fire-resistant cables and the careful application of flame retardant coatings, to stringent adherence to safety standards and effectively leveraging fire resistance enhancing technologies like wire packing machines, a comprehensive and integrated approach is absolutely essential. By consistently prioritizing fire safety at every stage of the process, industries can significantly mitigate potential risks, protect critical infrastructure investments, and most importantly, safeguard both lives and property from the devastating effects of fire.