Are you tired of the tedious and labor-intensive process of manually winding and packing cable wires? Imagine the frustration of tangled wires, inconsistent coiling, and the sheer manpower required to handle cable wire after extrusion. But what if there was a way to automate this entire process, seamlessly linking your cable extruder to an efficient winding and packing system?
Automating cable wire winding and packing with a cable extruder involves integrating an automatic cable coiler and packing machine directly with your extrusion line. This eliminates manual handling, ensures consistent coil quality, and significantly boosts production efficiency. It’s a game-changer for cable manufacturers looking to streamline operations and reduce costs.
Transitioning from manual cable handling to automation is a significant leap, and understanding the intricacies of this process is crucial. Let’s delve deeper into how you can effectively implement automatic cable wire winding and packing in conjunction with your cable extruder.
Streamlining Cable Production: The Benefits of Automation
Are you struggling with bottlenecks in your cable production line due to manual winding and packing? Cable manufacturers often face challenges with maintaining consistent quality and meeting production demands when relying on manual labor for post-extrusion processes. Imagine the impact of eliminating these bottlenecks and achieving a smooth, continuous production flow.
Automating cable winding and packing offers significant advantages, including increased production speed, reduced labor costs, improved consistency in coil quality, and minimized material waste. By integrating an automatic system, manufacturers can achieve a more efficient and profitable cable production process.
To fully appreciate the transformative power of automation, let’s break down the specific benefits and explore how they address common challenges in cable manufacturing.
Enhanced Efficiency and Throughput
Manual cable winding and packing are inherently slow and prone to inconsistencies. Automated systems, on the other hand, operate at a consistent pace, significantly increasing throughput.
Feature | Manual Winding & Packing | Automatic Winding & Packing |
---|---|---|
Speed | Slow, variable | Fast, consistent |
Consistency | Inconsistent | Highly consistent |
Labor Costs | High | Low |
Material Waste | Higher | Lower |
Throughput | Lower | Higher |
Operational Errors | More Frequent | Less Frequent |
Scalability | Limited | Highly Scalable |
As the table illustrates, automation offers a clear advantage across multiple operational metrics. The increased speed and consistency directly translate to higher production volumes and faster order fulfillment, giving businesses a competitive edge. Moreover, reduced operational errors minimize downtime and ensure smoother production runs. For businesses aiming for scalability and consistent output, automatic cable winding and packing is not just an upgrade—it’s a strategic imperative.
The Automatic Cable Winding Process: Step-by-Step
Tired of manually coiling cables and struggling to maintain uniformity? The manual cable winding process is not only time-consuming but also often results in inconsistent coil sizes and shapes. Imagine a process where cables are perfectly coiled every time, without the need for manual intervention.
Automatic cable winding involves a series of precise steps initiated immediately after cable extrusion, using a specialized cable winding machine to create uniform coils. This process typically includes cable guiding, tension control, precise length measurement, and automated coiling mechanisms, ensuring consistent and high-quality cable coils.
Let’s break down the automatic cable winding process to understand each stage in detail.
Precision and Control in Every Coil
Automatic cable winding machines are engineered for precision and consistency. They incorporate sophisticated controls to manage tension, length, and coil diameter, ensuring each coil meets exact specifications. The automation sequence typically involves:
- Cable Infeed and Guiding: The cable from the extruder is fed into the winding machine, often guided by rollers and sensors to ensure proper alignment.
- Tension Control: Maintaining consistent tension is crucial for uniform coils. Automated tension control systems adjust dynamically based on cable type and winding speed.
- Length Measurement: Precise encoders and measuring systems accurately determine the length of cable being coiled, ensuring coils are of the specified length.
- Coiling Mechanism: Rotating arms or turntables smoothly coil the cable into a predetermined diameter. Different winding patterns can be programmed for various coil types.
- Coil Take-off and Transfer: Once a coil is complete, automated systems remove it from the winding station and transfer it to the next stage, typically packing.
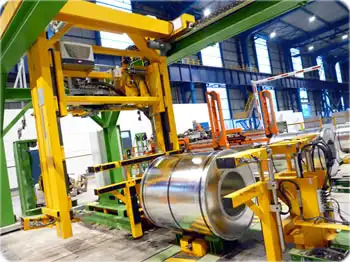
By automating these steps, manufacturers eliminate the variability inherent in manual winding, achieving consistent coil quality and reducing material waste. The ability to precisely control each parameter ensures that every coil meets the required specifications, contributing to overall product quality and customer satisfaction.
Automatic Cable Packing: Securing and Preparing Coils for Shipment
Are you looking for a way to streamline your cable packing process and ensure your products are securely prepared for shipping? Manual cable packing is often labor-intensive, slow, and can lead to inconsistencies in packaging quality. Imagine a system that automatically wraps, straps, and prepares your cable coils for dispatch, saving time and resources.
Automatic cable packing machines take the consistently coiled cables and efficiently prepare them for shipment through automated strapping, wrapping, and labeling processes. This ensures secure packaging, reduces the risk of damage during transit, and streamlines the final stages of production.
Let’s explore the key stages involved in automatic cable packing and how they contribute to efficient and secure product delivery.
Ensuring Secure Transit and Efficient Logistics
Automatic cable packing systems are designed to optimize both product protection and packing efficiency. The typical steps include:
- Coil Feeding: Automated conveyors or robotic arms transfer coiled cables from the winding station to the packing area.
- Strapping/Banding: Machines automatically apply straps or bands around the coil to secure it and maintain its shape during handling and shipping.
- Wrapping (Optional): For added protection against dust, moisture, or damage, coils can be automatically wrapped in film or other protective materials.
- Labeling and Identification: Automated labeling systems apply barcodes or identification tags for inventory management and tracking.
- Discharge and Palletizing: Packed coils are automatically discharged and can be further palletized by robotic systems for efficient warehousing and shipping.
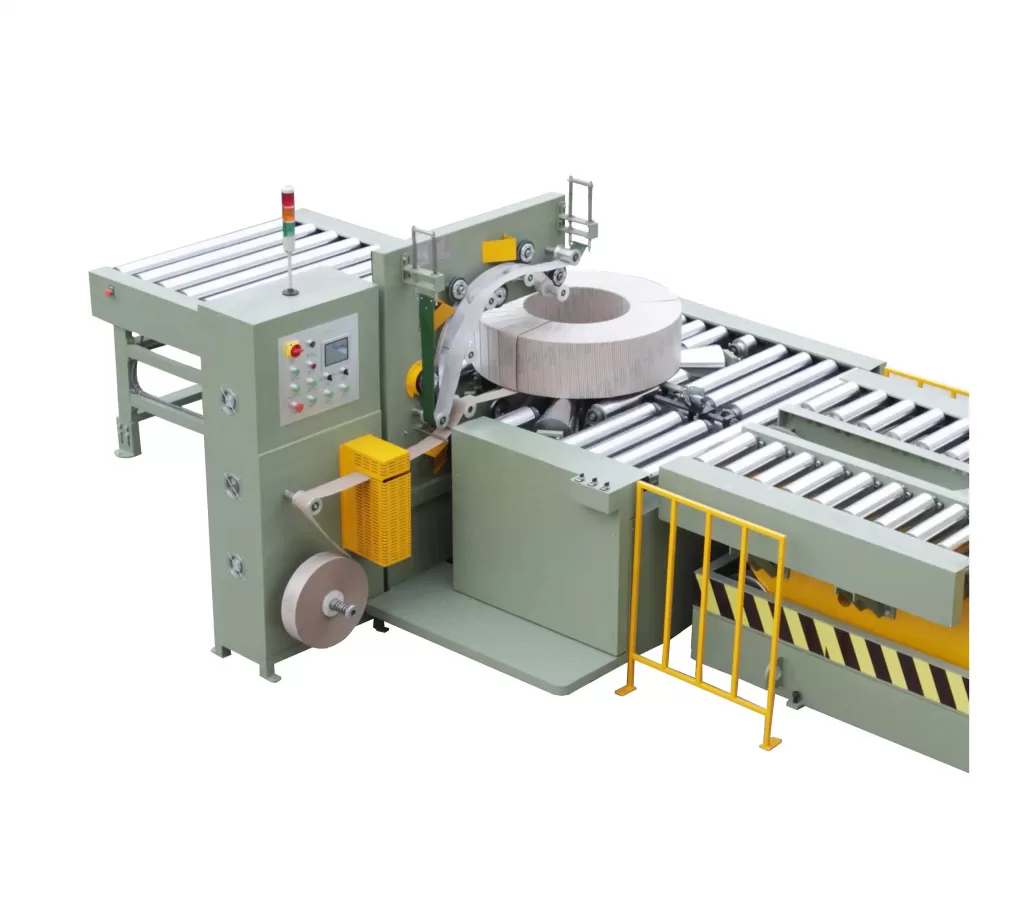
By automating these packing steps, manufacturers significantly reduce labor costs, minimize the risk of product damage during transit, and improve overall packing consistency. The speed and precision of automatic packing systems ensure that products are efficiently prepared for shipment, contributing to faster order fulfillment and enhanced customer satisfaction. Moreover, consistent and professional packaging enhances brand image and reinforces product quality.
Integrating Cable Extruders with Automated Winding and Packing Lines
Are you seeking a seamless, end-to-end solution for your cable manufacturing process, from extrusion to final packaging? Integrating individual machines can lead to compatibility issues and inefficiencies. Imagine a fully synchronized system where the cable extruder works in perfect harmony with the winding and packing machinery.
Integrating a cable extruder with automated winding and packing lines creates a continuous, synchronized production system, maximizing efficiency and minimizing manual intervention. This integrated approach ensures a smooth flow of cable from extrusion to packed coil, optimizing production speed and reducing handling costs.
The integration of these systems is crucial for achieving peak efficiency. Let’s examine the key considerations and benefits of a fully integrated cable production line.
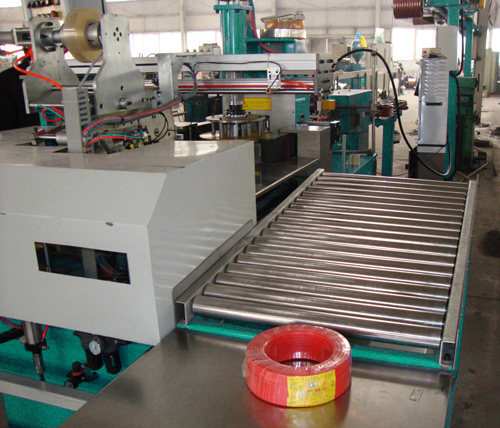
For businesses seeking to optimize their cable manufacturing process, integrating cable extruders with automated winding and packing lines is a strategic imperative. This holistic approach not only streamlines operations but also significantly enhances overall productivity and profitability. By eliminating manual bottlenecks and ensuring a continuous, synchronized production flow, manufacturers can achieve a competitive edge in today’s demanding market. Investing in an integrated cable packing line is a forward-thinking decision that yields long-term benefits and positions businesses for sustained success.
Conclusion
Automatic cable wire winding and packing solutions represent a significant advancement in cable manufacturing technology. By automating these critical post-extrusion processes, manufacturers can achieve unprecedented levels of efficiency, consistency, and cost-effectiveness. Embracing cable packing line automation is no longer just an option but a necessity for staying competitive in the modern cable industry.
Explore the possibilities of wire packing automation and revolutionize your cable production process today.