How to Choose the Right Mold Flipper?
In manufacturing, optimizing workflow is crucial, especially when handling heavy molds. Selecting the right mold flipper is a significant decision that impacts safety, efficiency, and productivity. Understanding the key factors will ensure you choose a machine that meets your specific operational needs and investment goals.
Choosing the right mold flipper involves assessing mold size and weight, rotation requirements (90° or 180°), available space, safety features, and budget. Prioritize robust construction, precise control, and user-friendly operation to enhance safety and efficiency in your manufacturing processes.
Investing in a mold flipper is a strategic move towards streamlining operations. To make an informed decision, let’s delve into the essential aspects to consider when selecting the ideal mold flipper for your facility.
Understanding Your Mold Flipping Needs
Before diving into the features of a mold flipper, it’s crucial to analyze your specific manufacturing requirements. A clear understanding of your needs will guide you to the most suitable and cost-effective solution. Consider the types of molds you handle, the frequency of flipping, and your production environment.
To choose the right mold flipper, evaluate your mold dimensions, weights, and how often you need to flip them. Determine if 90° or 180° rotation is necessary and ensure the flipper integrates with your current workflow and space. Matching the machine to your specific needs maximizes efficiency and safety.

Critical Considerations for Mold Flipper Selection
Selecting the correct mold flipper isn’t just about automation; it’s about optimizing your entire mold handling process. A mismatch can lead to inefficiencies, safety hazards, and unnecessary costs. Therefore, a detailed evaluation of your operational needs is paramount. Let’s break down the critical considerations:
Load Capacity and Mold Dimensions
The primary factor is the weight and size of your molds. Mold flippers come in various capacities, typically ranging from a few tons to upwards of 50 tons. Selecting a machine with adequate load capacity is non-negotiable for safety and performance. Overloading a flipper can lead to mechanical failures and dangerous situations. Furthermore, consider the physical dimensions of your molds. The flipper’s platform size must accommodate the largest molds you handle to ensure secure and stable flipping. Customizable platform sizes are often available to cater to specific mold dimensions.
Rotation Angle: 90° vs. 180°
Mold flippers are generally designed for 90° or 180° rotation. The choice depends on your manufacturing process. 90° flippers are often used when molds need to be tilted for maintenance or specific processing angles. For instance, injection molds frequently require a 90-degree tilt for cleaning and adjustments. 180° flippers, on the other hand, are essential for inverting molds, which is common in die casting and some types of plastic molding where both sides of the mold need to be accessed during production or maintenance. Understanding your process will dictate whether a 90° or 180° rotation capability is necessary. Some advanced machinery offer both options for enhanced versatility.
Space and Integration
Assess the available space in your manufacturing facility. Mold flippers vary in footprint, and some models are more compact than others. Consider the machine’s operating space, including clearance for rotation and access for loading and unloading molds. Integration with existing material handling systems is another crucial point. Will the flipper be a standalone unit, or does it need to integrate with conveyors, cranes, or pallet jacks? Seamless integration minimizes workflow disruptions and maximizes efficiency. For facilities with limited space, vertical mold flippers or pit-mounted installations can be considered to save floor space.
Safety and Operational Features
Safety is paramount when handling heavy molds. Look for mold flippers equipped with comprehensive safety features such as:
- Emergency stop buttons: For immediate halt in case of emergencies.
- Safety interlocks: To prevent operation if safety guards are not in place.
- Displacement restrictors: To ensure controlled and safe rotation within designated angles.
- Non-slip platforms: To secure molds during flipping.
- Smooth and controlled motion: Vibration-free operation minimizes the risk of mold damage and instability.
Operational features that enhance usability and efficiency include:
- User-friendly controls: Simple and intuitive operation minimizes training time and reduces operator errors.
- Adjustable rotation speed: Allows for fine-tuning the flipping speed based on mold sensitivity and operational needs.
- Automatic stop: Ensures the machine stops precisely at the desired rotation angle.
- Optional sliding tables: Facilitate easier loading and unloading of molds.
- Durable construction: Robust build quality ensures longevity and minimizes downtime due to maintenance.
By carefully evaluating these critical considerations, you can select a mold flipper that not only meets your operational needs but also enhances safety and productivity in your manufacturing environment.
Key Features to Look for in a Mold Flipper
Once you’ve defined your needs, the next step is to understand the key features that differentiate mold flippers and determine which features are most critical for your application. These features directly impact the machine’s performance, reliability, and safety. Focus on robust construction, control precision, and ease of maintenance.
Essential features of a mold flipper include a sturdy build, smooth and controlled rotation, precise positioning, comprehensive safety mechanisms, and user-friendly controls. Low maintenance requirements and durable components ensure long-term reliability and minimize downtime, contributing to overall operational efficiency.
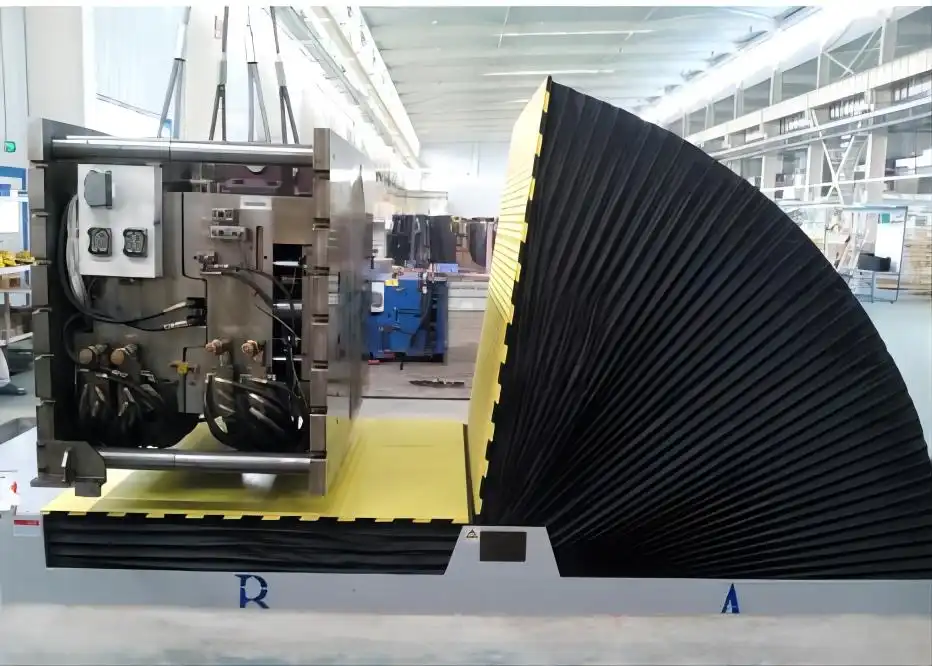
Delving into the Technical Details
Choosing a mold flipper involves understanding the technical specifications and how they translate into real-world performance. Let’s explore some key technical aspects in detail:
Drive System: Hydraulic vs. Electric
Mold flippers typically utilize either hydraulic or electric drive systems. Each has its own set of advantages and considerations:
-
Hydraulic Systems: Known for their high power and ability to handle extremely heavy loads, hydraulic systems are robust and reliable. They offer smooth and controlled motion, making them suitable for heavy and bulky molds. However, hydraulic systems can be more complex to maintain, may have higher energy consumption, and pose a potential risk of oil leaks.
-
Electric Systems: Electric drive systems are generally cleaner, quieter, and more energy-efficient. Modern electric systems, especially those using servo motors and frequency inverters, offer precise control over rotation speed and positioning. They are often easier to maintain than hydraulic systems and are suitable for a wide range of mold weights. However, for extremely heavy loads, hydraulic systems might still be preferred due to their raw power.
The choice between hydraulic and electric depends on your specific needs, load requirements, and operational preferences. For lighter to medium loads and applications prioritizing energy efficiency and precision, electric systems are often ideal. For very heavy loads and demanding industrial environments, hydraulic systems may be more appropriate.
Control Systems and Automation
The control system is the brain of the mold flipper, dictating its operational precision and ease of use. Modern mold flippers often incorporate Programmable Logic Controllers (PLCs) and Human-Machine Interfaces (HMIs).
-
PLC Control: PLCs provide robust and reliable control over the flipping process. They allow for precise programming of rotation angles, speeds, and safety sequences. PLC-based systems are highly customizable and can be integrated with other automation systems in the manufacturing line.
-
HMI Interface: A user-friendly HMI simplifies operation and monitoring. Touchscreen interfaces allow operators to easily set parameters, initiate cycles, and monitor machine status. Advanced HMIs can also display diagnostic information and facilitate troubleshooting.
Automation features further enhance efficiency and safety. Look for features like:
- Automatic stop at pre-set angles: Ensures accurate and repeatable positioning.
- Programmable cycles: Allows for automated sequences of flipping operations.
- Remote control options: Enhance operator safety and convenience, especially for handling very large molds.
Safety Mechanisms: Protecting Personnel and Molds
Safety mechanisms are non-negotiable for mold flippers. These machines handle heavy and valuable loads, and ensuring operator safety and preventing mold damage is paramount. Essential safety features include:
-
Emergency Stop Buttons: Strategically placed emergency stop buttons allow for immediate halting of the machine in case of any anomaly or emergency.
-
Light Curtains or Safety Scanners: These create safety zones around the machine, automatically stopping operation if personnel enter the hazardous area during operation.
-
Mechanical Locks and Interlocks: Prevent unintended movement or rotation during loading and unloading. Safety interlocks ensure that protective guards are in place before operation can commence.
-
Overload Protection: Prevents operation if the mold weight exceeds the machine’s capacity, protecting both the machine and the mold.
-
Smooth Start and Stop: Gradual acceleration and deceleration minimize sudden jolts and stress on the mold and the machine, reducing the risk of damage.
Material and Build Quality
The longevity and reliability of a mold flipper depend heavily on its material and build quality. Look for machines constructed from high-strength steel with robust welding and fabrication. Critical components like rotation bearings, drive motors, and gearboxes should be from reputable manufacturers and designed for heavy-duty industrial use. Surface treatments and coatings should be durable to withstand harsh industrial environments and prevent corrosion. A robust construction translates to a longer lifespan, reduced maintenance, and consistent performance over years of operation.
By understanding these technical details, you can make a well-informed decision and choose a mold flipper that not only meets your immediate needs but also provides long-term value and reliability for your manufacturing operations.
Types of Mold Flippers and Their Applications
Mold flippers are not one-size-fits-all; they come in various configurations designed for specific applications and mold handling requirements. Understanding the different types available will help you narrow down your choices and select the most appropriate machine for your needs. Common types include 90° flippers, 180° flippers, and customized solutions.
Common types of mold flippers include 90° and 180° models, each suited for different applications. 90° flippers are ideal for tilting molds for access, while 180° flippers invert molds completely. Customized flippers cater to unique needs. Choosing the right type depends on your manufacturing process and the specific rotation requirements of your molds.
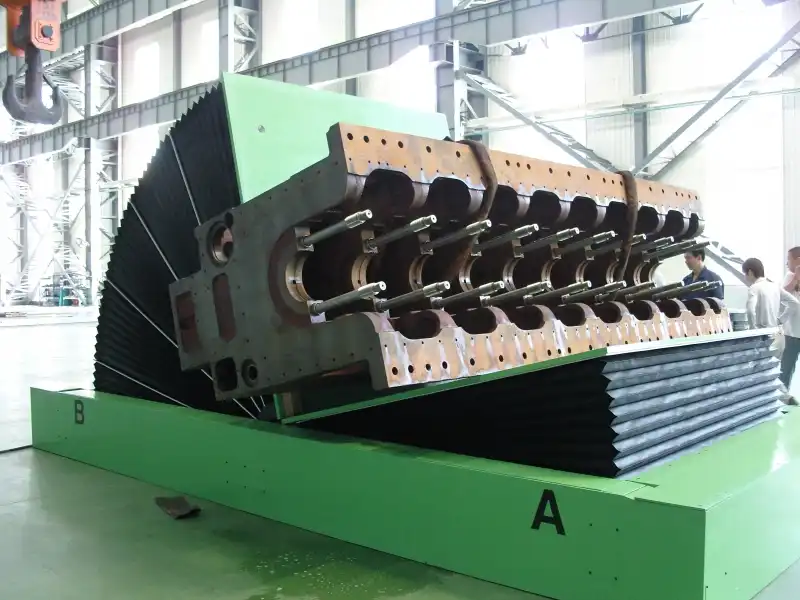
A Comparative Analysis of Mold Flipper Types
The market offers a range of mold flipper types, each with distinct characteristics and suitability for different manufacturing scenarios. Let’s compare the most common types to help you determine which best aligns with your operational requirements.
Type | Rotation Angle | Typical Applications | Advantages | Disadvantages | Example Industries |
---|---|---|---|---|---|
90° Mold Flipper | 90° | Mold maintenance, inspection, and partial access. | Space-efficient, suitable for tilting, easier access to one mold half. | Limited to 90° rotation, not ideal for full mold inversion. | Injection molding, die casting (partial maintenance), general manufacturing |
180° Mold Flipper | 180° | Full mold inversion, accessing both mold halves. | Complete inversion capability, access to both mold halves, versatile. | Larger footprint than 90° flippers, may require more vertical clearance. | Die casting, plastic molding, automotive, aerospace |
Customized Flippers | Variable | Specialized mold handling needs. | Tailored to specific mold sizes and shapes, optimized for unique processes. | Higher initial cost, longer lead times, may require specialized maintenance. | Aerospace, heavy machinery, industries with unique mold handling challenges |
90° Mold Flippers: Tilting for Accessibility
90° mold flippers are designed to tilt molds to a 90-degree angle, essentially turning them on their side. This type is particularly useful for applications where access to one side of the mold is frequently needed, such as for maintenance, inspection, or minor adjustments during production. Their compact design often makes them suitable for facilities with limited floor space. 90° flippers are commonly used in:
- Injection Molding: For cleaning and inspecting mold cavities, ejector pins, and cooling channels.
- Die Casting: For partial mold maintenance and inspection without complete disassembly.
- General Manufacturing: In any process where tilting a heavy component for access is beneficial.
180° Mold Flippers: Complete Mold Inversion
180° mold flippers provide the capability to completely invert molds, rotating them 180 degrees. This is crucial when both halves of the mold need to be accessed, such as during thorough maintenance, repair, or when changing mold inserts. 180° flippers are essential in industries like:
- Die Casting: For complete mold disassembly, cleaning, and maintenance of both die halves.
- Plastic Molding: For processes requiring access to both mold halves for complex mold designs or frequent changes.
- Automotive and Aerospace: Where large and complex molds require regular and thorough maintenance.
Customized Mold Flippers: Tailored Solutions
For highly specialized manufacturing environments or unique mold designs, customized mold flippers offer tailored solutions. These machines are engineered to meet specific requirements that standard models cannot accommodate. Customization can include:
- Unique platform sizes and shapes: To fit нестандартные molds.
- Special rotation angles: Beyond 90° or 180° for specific process needs.
- Integrated features: Such as built-in lifting mechanisms, conveyors, or specialized clamping systems.
- Extreme load capacities: For handling exceptionally heavy molds.
Customized flippers are often found in industries with very specific and demanding mold handling needs, such as aerospace, heavy machinery manufacturing, and specialized research and development facilities. While they offer optimal performance for niche applications, they typically come with a higher upfront cost and may require longer lead times for design and fabrication.
Choosing the right type of mold flipper is a critical decision based on your specific operational needs, mold types, and manufacturing processes. By carefully evaluating the rotation requirements and application, you can select a machine that maximizes efficiency, safety, and productivity.
Integrating a Mold Flipper into Your Workflow
Integrating a mold flipper seamlessly into your manufacturing workflow is as important as choosing the right type of machine. Proper integration ensures that the flipper enhances efficiency without causing bottlenecks or disruptions. Consider space planning, operator training, and workflow adjustments to maximize the benefits of your new equipment.
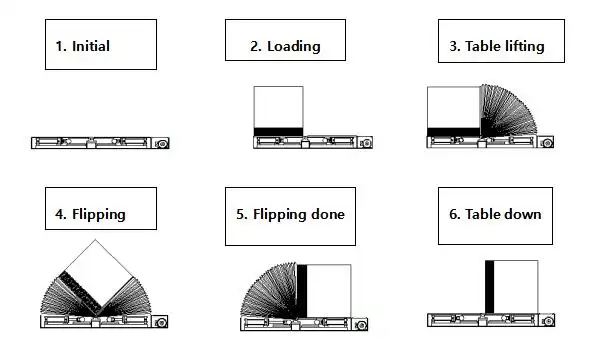
Integrating a mold flipper involves careful planning to ensure it fits seamlessly into your existing workflow. Consider the physical space, power requirements, and operator training. Optimize the flipper’s location for efficient mold transfer and ensure operators are well-trained on safe and effective operation to maximize productivity gains and minimize disruptions.
Successfully integrating a mold flipper into your workflow involves addressing several practical considerations to ensure a smooth transition and optimal performance. Here are key aspects to focus on:
Space Planning and Layout Optimization
Before installation, carefully plan the location of the mold flipper within your facility. Consider the following:
- Footprint: Ensure the chosen flipper model fits comfortably within the allocated space, considering both its operational footprint and maintenance access.
- Clearance: Provide adequate clearance around the machine for safe operation, mold loading and unloading, and operator movement. Account for the maximum rotation radius and any additional space needed for ancillary equipment like pallet jacks or cranes.
- Workflow Integration: Position the flipper strategically within your workflow to minimize material handling distances and optimize the flow of molds through the production process. Ideally, locate it near mold storage, maintenance areas, or production lines where mold flipping is required.
- Floor Load Capacity: Verify that the floor in the chosen location can support the weight of the mold flipper and the heaviest molds it will handle. Reinforcements may be necessary in some cases.
- Power and Utilities: Ensure that the location has access to the required power supply (voltage, phase, frequency) and any other utilities, such as compressed air if needed for certain pneumatic flipper models.
Installation and Commissioning
Proper installation is crucial for the safe and reliable operation of the mold flipper. Follow these steps:
- Professional Installation: Engage qualified technicians or the manufacturer’s installation team to ensure correct setup and alignment. Improper installation can lead to mechanical stress, reduced performance, and safety hazards.
- Leveling and Anchoring: Ensure the flipper is installed on a level surface and securely anchored to the floor to prevent movement or vibration during operation.
- Electrical and Hydraulic Connections: Verify that all electrical and hydraulic connections are made correctly and are secure and leak-free.
- Testing and Calibration: After installation, thoroughly test the machine through its full range of motion and load capacity. Calibrate sensors, safety systems, and control parameters to ensure accurate and safe operation.
- Safety Inspections: Conduct comprehensive safety inspections before putting the machine into regular use to verify that all safety features are functioning correctly.
Operator Training and Safety Protocols
Effective operator training is essential for maximizing productivity and ensuring safe operation. Training should cover:
- Machine Operation: Detailed instruction on how to operate the flipper, including control functions, loading and unloading procedures, and rotation sequences.
- Safety Procedures: Thorough training on all safety protocols, emergency stop procedures, and hazard awareness. Emphasize the importance of adhering to safety guidelines at all times.
- Routine Maintenance: Basic operator-level maintenance tasks, such as lubrication, visual inspections, and cleaning.
- Troubleshooting: Basic troubleshooting steps to identify and resolve minor issues.
- Load Securing: Proper techniques for securing molds on the flipper platform to prevent shifting or falling during rotation.
Develop clear and concise operating procedures and safety guidelines, and make them readily available to all operators. Regular refresher training is also recommended to reinforce safe practices and keep operators updated on any changes or best practices.
Workflow Adjustments and Optimization
Integrating a mold flipper may require adjustments to your overall manufacturing workflow to fully realize its benefits. Consider:
- Mold Handling Procedures: Revise mold handling procedures to incorporate the flipper into the process. Streamline the steps for transporting molds to and from the flipper.
- Maintenance Schedules: Adjust maintenance schedules to take advantage of the flipper for easier and more efficient mold maintenance tasks.
- Production Planning: Incorporate the cycle time of the mold flipper into production planning to accurately estimate throughput and minimize downtime during mold changes or maintenance.
- Process Optimization: Analyze the entire mold handling process to identify opportunities for further optimization. The flipper may enable process improvements that were not feasible with manual handling methods.
By carefully addressing these integration aspects, you can ensure that your new mold flipper becomes a valuable asset that enhances efficiency, safety, and productivity in your manufacturing operations, rather than a source of disruption or underutilized equipment.
Conclusion
Choosing the right mold flipper is a critical investment that significantly impacts manufacturing efficiency and safety. By carefully considering your specific needs, evaluating key features, understanding different types, and planning for seamless integration, you can select a mold flipper that optimizes your mold handling processes. This strategic decision not only streamlines operations but also enhances workplace safety and contributes to long-term productivity gains and cost savings in your manufacturing facility.