Choosing the right type of steel coil upender can be challenging. With manual and automated options available, each offers unique advantages. Understanding these options can help improve efficiency and reduce risks in your operations. Let’s explore how FHOPEPACK’s cutting-edge technology can enhance your industrial processes with the right upender.
When choosing between manual and automated steel coil upenders, consider your operational needs, budget, and safety requirements. Manual upenders may be suitable for small-scale operations with lower budget constraints but pose higher labor and safety risks. Automated upenders, while requiring a higher initial investment, offer efficiency, reduced labor costs, and improved safety, making them ideal for larger operations.
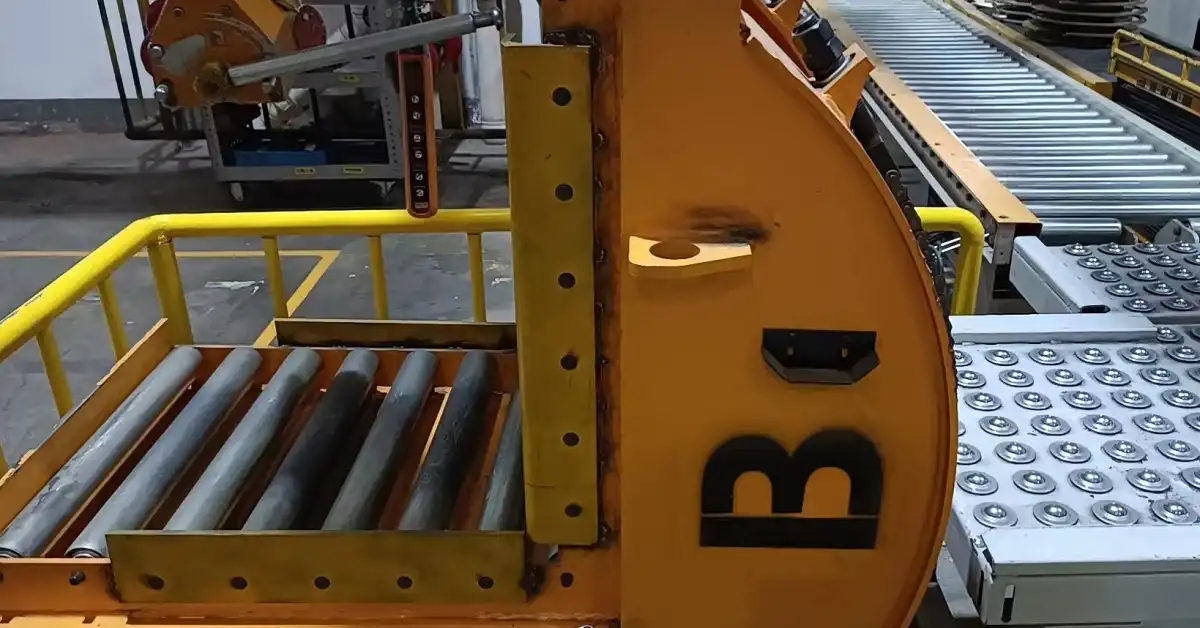
Transitioning from manual to automated systems can seem daunting, but the long-term benefits often outweigh the challenges. Automation not only maximizes productivity but also enhances safety, which is crucial in handling heavy steel coils. As you ponder over these options, remember that choosing the right system aligns directly with your company’s growth and safety priorities.
1. What Are the Key Differences Between Manual and Automated Steel Coil Upenders?
Understanding the key differences between manual and automated steel coil upenders is essential for making the right investment. Traditionally, manual systems demand more human effort, leading to increased labor costs and safety risks. Alternatively, automated systems are designed to meet high efficiency and safety standards, reducing the need for manual interventions.
Manual upenders are labor-intensive and present higher safety risks, requiring significant human effort. In contrast, automated upenders improve efficiency by reducing manual labor and enhancing safety features. They are programmed to handle a variety of coil sizes and weights, offering flexibility and consistency. The choice depends on your operational scale and safety requirements, balancing initial investment with long-term benefits.
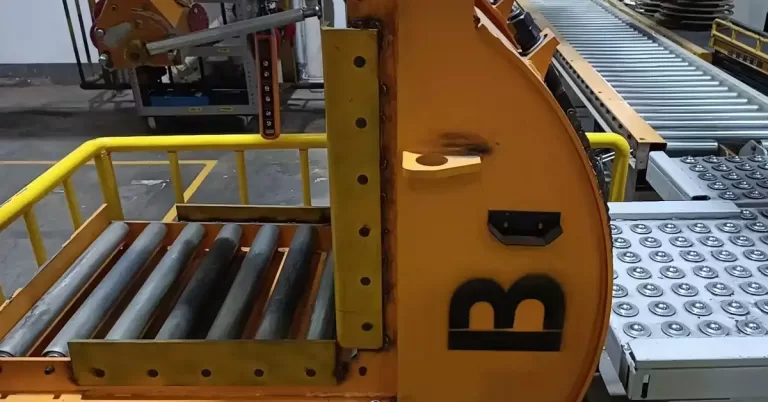
1.1. Factors Influencing the Choice of Steel Coil Upenders
When deciding between manual and automated upenders, several factors come into play. Let’s consider budget, operation scale, and safety. Manual systems are typically less expensive upfront, making them appealing for small operations. However, they require more physical labor, leading to potential safety issues. An automated system, though costly initially, offers reliability and efficiency. They come equipped with advanced safety features, reducing human error and enhancing workplace safety.
Factor | Manual Upenders | Automated Upenders |
---|---|---|
Initial Investment | Lower Cost | Higher Cost |
Efficiency | Lower Productivity | High Productivity |
Safety Concerns | High Risk | Enhanced Safety Features |
Operational Scalability | Limited | Highly Scalable |
In my experience, the decision often boils down to weighing short-term costs against long-term benefits. Investing in automated systems can lead to significant savings over time by minimizing downtime and reducing labor costs. The safety advantage alone justifies the investment for many companies. Remember, integrating automation into your processes not only boosts productivity but also safeguards your workforce, ultimately supporting sustainable growth in your operations.
2. How Does Efficiency and Cost-Effectiveness Impact Your Choice?
Choosing the right packaging machinery can be overwhelming, given the many factors to consider. Efficiency and cost-effectiveness are critical in this decision-making process. Using machines that can do more with less can give companies a competitive edge in the marketplace, leading to long-term success and sustainability.
Efficiency and cost-effectiveness directly impact your choice of packaging machinery. Efficient machines can reduce energy consumption, minimize downtime, and increase output. Cost-effective solutions maintain high quality while lowering operational costs. Balancing these elements helps businesses remain competitive, improve profitability, and ensure consistent product delivery.
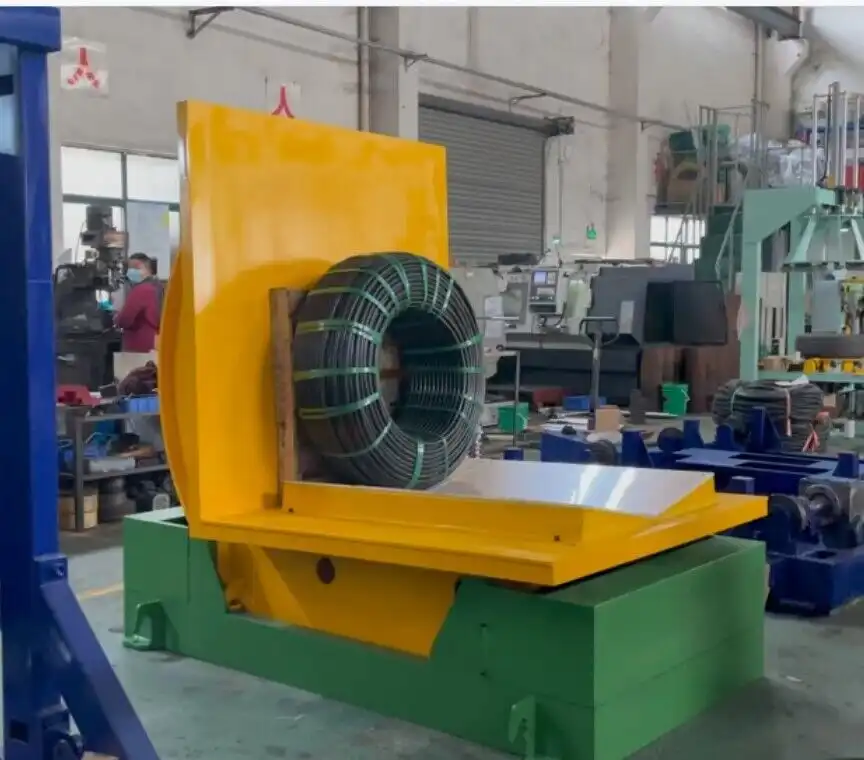
Balancing Efficiency and Cost-Effectiveness
In choosing packaging machinery, efficiency and cost-effectiveness need careful evaluation. Efficiency focuses on operational speed and reliability. Cost-effectiveness addresses initial investments and ongoing maintenance costs. To achieve a successful balance, analyze the requirements and specifications of each machine to meet production goals.
Factor | Efficiency Focus | Cost-Effectiveness Consideration |
---|---|---|
Speed | High throughput for productivity | Lower energy consumption |
Reliability | Minimal downtime for smooth operations | Lower maintenance costs |
Flexibility | Supports various packaging needs | Easily adaptable for future needs |
Efficiency in machinery allows for higher throughput and consistent quality, reducing errors and waste. For instance, coil wrapping machines are designed to quickly wrap products. They help maintain a streamlined workflow without manual handling that can lead to bottlenecks.
Cost-effectiveness, on the other hand, is about getting the most out of your investment. Initial purchase costs might be high, but when weighed against the reduced labor expenses, energy conservation, and fewer repairs, the long-term financial benefits are clear. It’s essential to look beyond the price tag and evaluate how the equipment will support overall business goals.
Choosing the right balance between efficiency and cost will ultimately affect your bottom line, impacting both immediate operations and long-term plans. Investing in quality machinery offers dividends by conserving resources and increasing productivity, proving itself invaluable in competitive markets.
3. Which Operational Factors Should Be Considered When Choosing an Upender?
Navigating the world of upenders can be a complex process, but understanding operational factors can guide smart decisions. Selecting the right upender means paying attention to factors that influence how products are handled and positioned, ensuring you meet your business’s unique needs.
When choosing an upender, consider capacity, safety features, and system integration. Capacity determines load handling ability, while safety features ensure operator protection. System integration examines how well the upender fits into existing workflows. These factors directly affect efficiency, productivity, and cost management in handling operations.
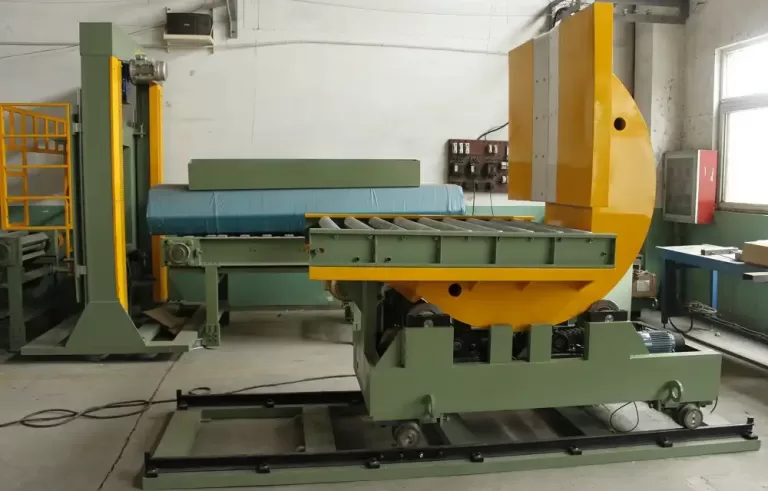
Key Factors in Upender Selection
When evaluating upenders, the critical factors include capacity, safety, and system integration. Each of these aspects plays a vital role in ensuring that the upender will not only perform as needed but also enhance the current operation setup.
Factor | Detail | Impact |
---|---|---|
Capacity | Load weight and dimension limits | Influences efficiency and safety |
Safety Features | Alarms, emergency stops, safeguarding | Prevents accidents and injuries |
System Integration | Compatibility with existing systems | Smooth operation and workflow |
Capacity is crucial in determining the types of loads an upender can safely handle. Understanding your operational requirements will help you match the right machine to the job, ensuring that the equipment won’t be strained and risks of damages and downtimes are minimized.
Safety features, such as emergency stop buttons and alarms, protect operators during operation. These features not only meet safety regulations but also promote a safe working environment, minimizing the risk of accidents.
Finally, an upender that integrates well with existing systems can simplify installation and training times. When a new machine blends seamlessly into your workflow, it preserves productivity while avoiding unnecessary disruptions.
By analyzing these factors meticulously, you ensure the chosen upender fulfills operational demands efficiently and safely, safeguarding investment in enhancing productivity and safety.
Conclusion
In summary, choosing the right steel coil upender depends on understanding your operational needs, efficiency requirements, and budget constraints. Evaluating efficiency and cost-effectiveness ensures higher return on investment. Meanwhile, considering operational factors like capacity, safety, and integration keeps the workflow fluid and safe. These insights equip you for informed decision-making in this critical area of material handling.
In summary, choosing the right steel coil upender depends on understanding your operational needs, efficiency requirements, and budget constraints.