1. How to Apply Technological Advancements in Steel Coil Packing?
Steel coil packing is evolving rapidly, moving beyond basic methods to embrace cutting-edge technology. Integrating the latest advancements is crucial for businesses aiming for efficiency, reduced material waste, and enhanced safety in their operations. By strategically applying these innovations, companies can significantly optimize their coil packing processes.
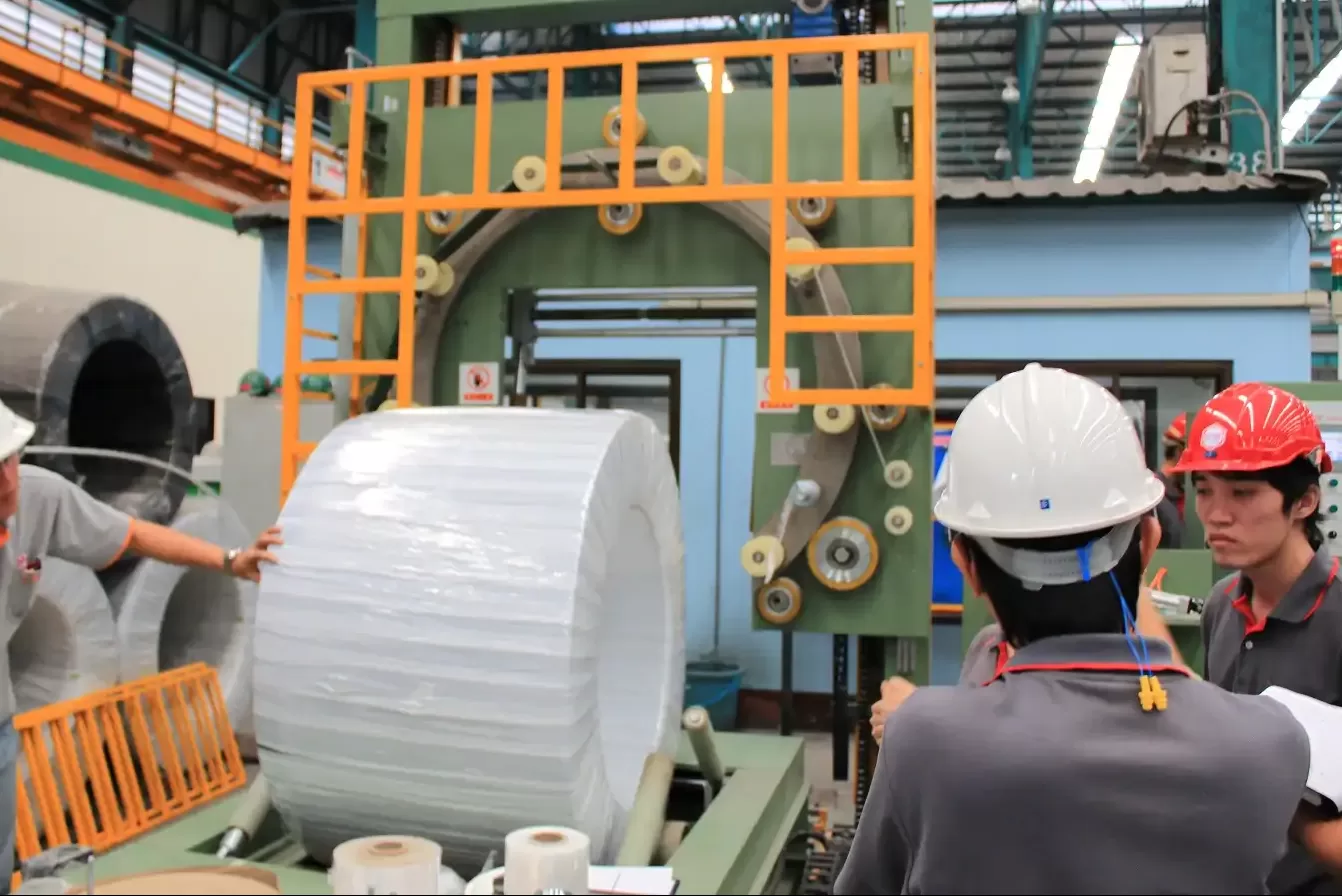
To apply technological advancements in steel coil packing, focus on automation, material innovation, and smart integration. Implement automated coil wrapping machines, utilize eco-friendly and high-strength packing materials, and adopt IoT for real-time monitoring. Embrace predictive maintenance and custom packaging solutions to maximize efficiency and minimize waste, ensuring a future-proof operation.

Let’s delve into the specific technological innovations reshaping steel coil packing and explore how they can be practically implemented to revolutionize your packaging line.
2. Innovations in Steel Coil Packing Technology
The steel coil packing industry is witnessing a transformative phase driven by continuous technological progress. These innovations are not just about speed; they encompass precision, sustainability, and adaptability, redefining how coils are handled, protected, and prepared for shipment.
Key innovations in steel coil packing technology include automated wrapping systems, advanced material utilization, and smart sensor integration. Automated systems increase throughput and consistency, while new materials offer enhanced protection and environmental benefits. Smart sensors provide real-time data for process optimization and predictive maintenance, ensuring seamless and efficient operations. These advancements collectively contribute to a more robust, cost-effective, and sustainable coil packing process.
Diving Deeper into Modern Coil Packing Innovations
To fully grasp the impact of innovation in steel coil packing, it’s essential to break down the key areas and understand how they contribute to overall improvement. Modernization efforts are focused on creating systems that are not only faster but also smarter and more sustainable. Let’s explore the critical components driving this evolution.
2.1. Automated Coil Handling Systems
Automated guided vehicles (AGVs) and robotic arms are revolutionizing material handling within steel coil packing facilities. These systems minimize manual intervention, reducing labor costs and the risk of workplace injuries. AGVs efficiently transport coils through different stages of the packing process, while robotic arms perform precise tasks like wrapping and banding with consistent accuracy.
2.2. Advanced Wrapping Materials
Traditional steel coil packing often relies on basic materials that may not offer optimal protection or environmental responsibility. The industry is now shifting towards advanced materials like high-strength polymer films, biodegradable wraps, and corrosion-inhibiting laminates. These materials provide superior protection against moisture, physical damage, and corrosion, ensuring coils arrive at their destination in pristine condition. Furthermore, the adoption of recyclable and biodegradable options aligns with growing sustainability demands.
2.3. Smart Sensor and IoT Integration
The integration of smart sensors and IoT (Internet of Things) technologies is bringing unprecedented levels of control and visibility to coil packing operations. Sensors embedded in packing machinery can monitor parameters like tension, temperature, and material usage in real-time. This data is then fed into IoT platforms, allowing operators to track performance, identify potential issues proactively, and optimize processes on the fly. Predictive maintenance becomes a reality, minimizing downtime and extending equipment lifespan.
To illustrate the impact of these innovations, consider the following comparison:
Feature | Traditional Packing | Modernized Packing | Benefits |
---|---|---|---|
Material Handling | Manual labor, forklifts | AGVs, Robotic Arms | Reduced labor costs, improved safety, efficiency |
Wrapping Materials | Basic films, tapes | Advanced polymers, biodegradable films | Superior protection, sustainability |
Process Monitoring | Manual checks, periodic | Real-time sensors, IoT | Data-driven optimization, predictive maintenance |
Speed & Throughput | Lower, inconsistent | Higher, consistent | Increased productivity, faster delivery |
Sustainability | Limited consideration | Focus on eco-friendly materials | Reduced environmental footprint, compliance |
By strategically implementing these innovations, steel coil manufacturers and processors can achieve significant improvements across their packing operations, enhancing both efficiency and sustainability.
3. Automation and Robotics Integration for Steel Coil Packing
Automation is no longer a futuristic concept but a present-day necessity in steel coil packing. Integrating automation and robotics enhances efficiency, precision, and safety, addressing key challenges in the traditional packing process.
Automation and robotics integration streamlines steel coil packing by automating repetitive tasks, improving accuracy, and ensuring consistent quality. Robotic arms handle heavy coils with ease, automated wrapping machines apply consistent and secure packaging, and centralized control systems manage the entire process seamlessly. This reduces manual labor, minimizes errors, and significantly boosts throughput in coil packing operations.
Delving into the Technical Aspects of Automation
The successful integration of automation in steel coil packing hinges on understanding the technical details and selecting the right technologies for specific needs. Let’s explore the core components and considerations for effective automation implementation.
3.1. Robotic Arm Applications
Robotic arms are versatile tools in automated coil packing lines. Their applications include:
- Coil Handling: Lifting, rotating, and positioning coils for wrapping or stacking.
- Material Application: Precisely applying wrapping films, tapes, and edge protectors.
- Quality Inspection: Utilizing vision systems to inspect wrapping quality and identify defects.
Choosing the right robotic arm depends on the coil size and weight, required speed, and the complexity of tasks. Collaborative robots (cobots) are increasingly popular for their safety and ability to work alongside human operators.
3.2. Automated Wrapping Machinery
Automated coil wrapping machines are central to increasing packing speed and consistency. These machines can be programmed to apply various wrapping patterns, tension levels, and layers of material, ensuring optimal protection for different coil types and transportation conditions. Advanced features include:
- Automatic Material Changeover: Minimizing downtime for material replenishment.
- Tension Control Systems: Ensuring consistent and secure wrapping without damaging the coil.
- Programmable Logic Controllers (PLCs): Providing precise control over wrapping parameters and integration with overall line management systems.
3.3. Integrated Control Systems
Effective automation requires a centralized control system that integrates all components – robots, wrapping machines, conveyors, and sensors. Supervisory Control and Data Acquisition (SCADA) systems and Distributed Control Systems (DCS) are commonly used to:
- Monitor and Control: Oversee all aspects of the packing line from a central interface.
- Data Acquisition and Analysis: Collect real-time data for performance monitoring, quality control, and process optimization.
- System Integration: Ensure seamless communication and coordination between different automated components.
The benefits of automation are quantifiable. Consider the following data points:
Metric | Manual Packing | Automated Packing | Improvement |
---|---|---|---|
Packing Speed (coils/hour) | 5-10 | 20-30 | 200-300% |
Material Waste (%) | 8-12 | 2-4 | 60-75% |
Labor Costs (%) | 30-40 | 10-15 | 50-75% |
Injury Rate (incidents/year) | 5-8 | 1-2 | 75-85% |
These figures highlight the significant advantages of automation in terms of productivity, cost savings, and safety enhancements in steel coil packing operations.
4. Sustainable Packing Materials and Methods for Steel Coils
Sustainability is a paramount concern across industries, and steel coil packing is no exception. Adopting eco-friendly materials and methods is not only environmentally responsible but also increasingly demanded by customers and regulators.
Sustainable packing materials and methods in steel coil packing involve using recyclable, biodegradable, or reusable materials and optimizing processes to minimize waste and energy consumption. This includes transitioning from traditional plastics to paper-based wraps, biodegradable films, and reusable steel or composite containers. Implementing efficient wrapping techniques and optimizing material usage further reduces environmental impact.
To achieve true sustainability in steel coil packing, a multifaceted approach is required. This includes material selection, process optimization, and life cycle assessment.
4.1. Eco-Friendly Material Options
- Biodegradable Films: Made from renewable resources like corn starch or cellulose, these films decompose naturally, reducing plastic waste.
- Recycled Paper and Cardboard: Utilizing recycled paper for wraps and edge protectors lowers the demand for virgin resources and supports circular economy principles.
- Reusable Steel or Composite Containers: For closed-loop systems, reusable containers eliminate single-use packaging and offer robust protection for coils.
4.2. Waste Reduction Strategies
- Optimized Wrapping Techniques: Employing precision wrapping methods minimizes material usage without compromising protection.
- Material Recycling Programs: Implementing systems to collect and recycle used packing materials within the facility or through partnerships with recycling companies.
- Source Reduction: Designing packaging to use the minimum necessary material while still meeting performance requirements.
4.3. Energy-Efficient Processes
- Energy-Saving Machinery: Investing in modern packing equipment designed for energy efficiency, such as servo-driven systems and optimized heating elements in wrapping machines.
- Process Optimization: Streamlining packing line layout and operations to reduce energy consumption per coil packed.
- Renewable Energy Integration: Powering packing facilities with renewable energy sources like solar or wind to lower the carbon footprint of operations.
By adopting these sustainable practices, companies can significantly reduce their environmental impact and enhance their brand image as environmentally conscious operators.
5. Modernizing and Upgrading Existing Steel Coil Packing Lines
Many steel manufacturers and processors operate with existing packing lines that may lack the efficiency and capabilities of modern systems. Modernization and upgrades offer a cost-effective pathway to enhance performance without completely replacing entire lines.
Modernizing existing steel coil packing lines involves upgrading key components and integrating new technologies to improve efficiency, automation, and sustainability. This can include retrofitting automated wrapping modules, upgrading control systems to PLCs, integrating sensors for real-time monitoring, and replacing outdated components with energy-efficient alternatives. Modernization allows for a phased approach to improvement, maximizing ROI while minimizing disruption to operations.
Upgrading existing lines offers several key advantages:
- Cost Savings: Modernization is typically more cost-effective than complete line replacement, preserving a significant portion of the initial investment.
- Reduced Downtime: Phased upgrades can be implemented with minimal disruption to production, unlike the extensive downtime required for installing a new line.
- Incremental Improvement: Upgrades allow for a step-by-step approach, focusing on the most critical areas first and gradually enhancing other aspects.
- Customization: Existing lines can be tailored to specific needs and space constraints, ensuring optimal integration of new technologies.
- Sustainability Enhancement: Upgrading to energy-efficient components and sustainable material handling systems directly contributes to environmental goals.
Modernization projects can range from simple component replacements to more extensive system overhauls. A typical modernization project may include:
- Control System Upgrade: Replacing outdated relay logic or older PLCs with modern, programmable control systems for improved automation and data acquisition.
- Automated Wrapping Module Integration: Adding automated wrapping heads to existing conveyors to streamline the wrapping process and improve consistency.
- Sensor and Monitoring System Installation: Integrating sensors for tension, temperature, and material usage, linked to a central monitoring system for real-time data and predictive maintenance.
- Drive and Motor Upgrades: Replacing inefficient motors with energy-saving servo drives to reduce energy consumption and improve motion control.
- Material Handling System Enhancements: Integrating AGVs or upgrading conveyors to improve material flow and reduce manual handling.
By strategically planning and executing modernization projects, steel coil packing facilities can significantly enhance their operational efficiency, reduce costs, and improve sustainability, ensuring they remain competitive in a rapidly evolving industry.
Conclusion
Technological advancements are revolutionizing steel coil packing, offering unprecedented opportunities for efficiency, sustainability, and improved operational performance. By embracing automation, adopting innovative materials, and strategically modernizing existing lines, companies can achieve significant gains. The future of coil packing lies in the intelligent integration of these technologies to create robust, efficient, and environmentally responsible operations. Adaptability and a commitment to continuous improvement will be key to thriving in this dynamic landscape.