Choosing the right horizontal wrapping machine can optimize industrial workflows, but without understanding key considerations, businesses might face inefficiencies. Let's explore the crucial factors involved in making the right choice.
When selecting a horizontal wrapping machine, key considerations include load stability, machine compatibility with materials, speed, durability, automation level, and costs. Optimizing these factors ensures improved efficiency, reduced labor, and enhanced safety in packaging processes.
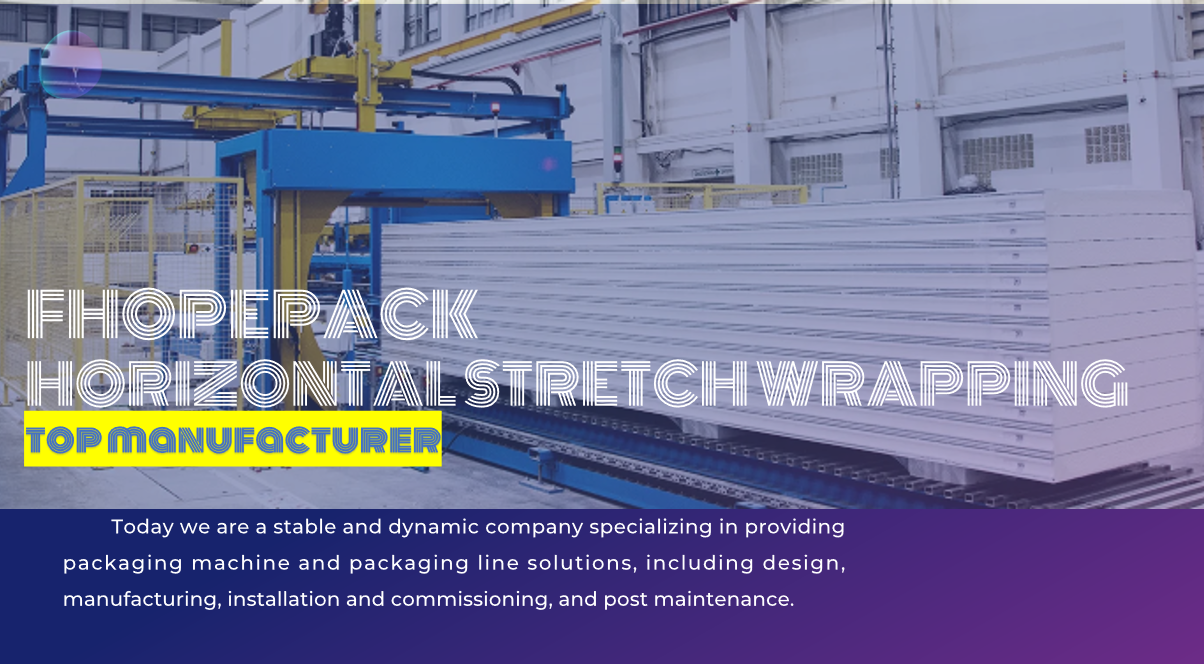
For any business, choosing the perfect horizontal wrapping machine isn't just a purchase decision—it's a strategic move. Understanding machine efficiency and applicability matters.
1. How to Evaluate the Operational Efficiency of the Machine?
In the quest for optimal packaging, determining the machine's operational efficiency is key. Companies who master this can gain a competitive edge and maximize productivity.
Evaluate a machine's operational efficiency by examining throughput speed, energy consumption, maintenance needs, and downtime frequency. Balancing these parameters ensures seamless operation and high productivity, leading to cost effectiveness and improved business outcomes.
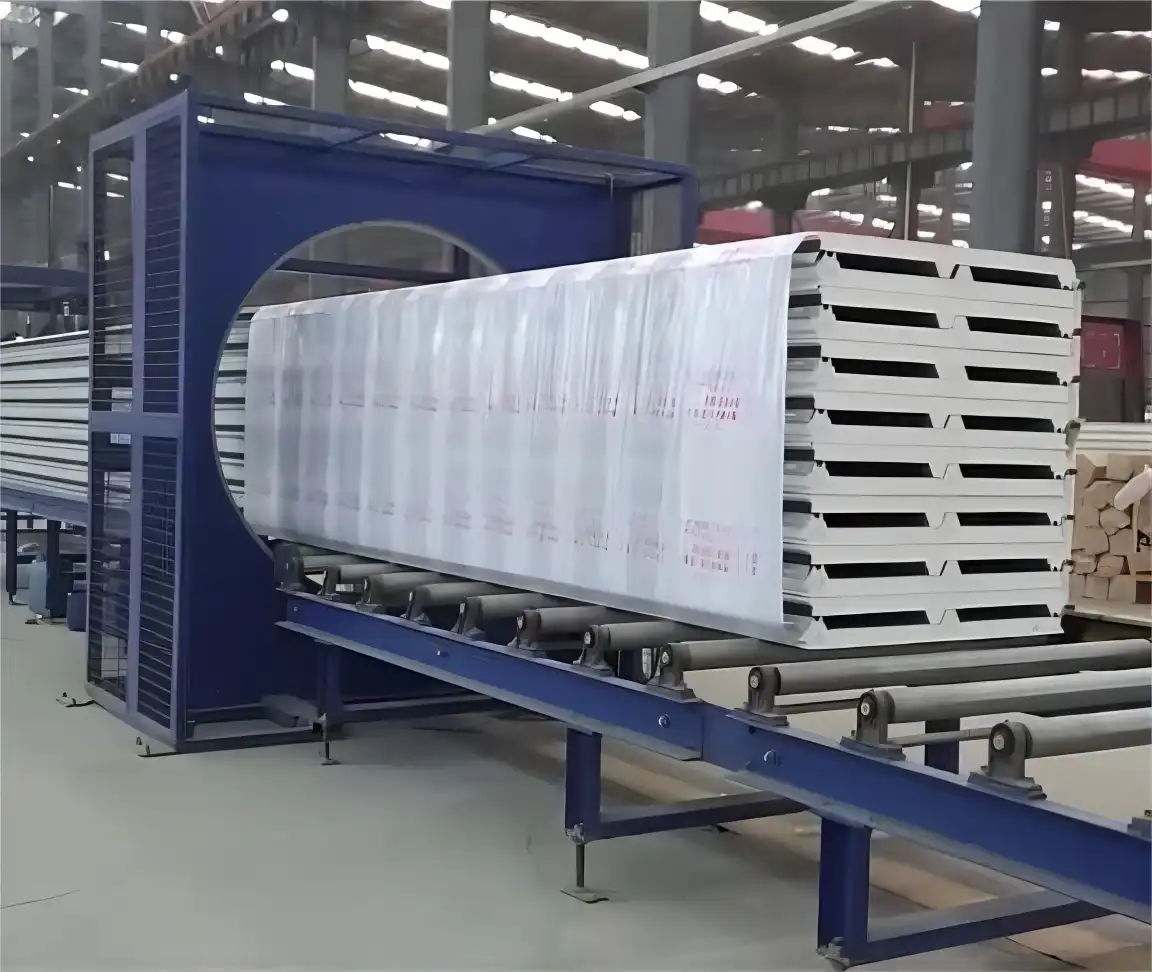
Evaluating Performance Metrics in Depth
Several critical performance metrics need assessment when evaluating a wrapping machine’s operational efficiency. Each of these plays a role in the total investment and achievable returns.
Metric | Explanation | Importance |
---|---|---|
Throughput Speed | Measures how fast a machine can process items. | Higher speeds often lead to increased productivity. |
Energy Consumption | Amount of energy utilized for operations. | Lower consumption can mean cost savings. |
Maintenance Needs | Frequency and complexity of required maintenance tasks. | Less frequent maintenance can increase uptime. |
Downtime Frequency | Measures how often a machine is non-operational. | Minimizing downtime is crucial for maintaining productivity. |
From my decades of experience in manufacturing, I’ve learned the importance of selecting a machine that balances these factors. One project comes to mind where we overlooked energy consumption and found our costs skyrocketing. That taught me to closely consider not only immediate operational efficiency but ongoing costs too.
Ultimately, a comprehensive evaluation of these performance metrics ensures businesses select a machine that suits their needs both in the short and long term. Investigating these factors in detail helps in forecasting the total cost of ownership, which plays a decisive role in business planning and budget allocation.## 2. What Compatibility Factors Should be Considered?
- In the world of automated packaging, selecting the right equipment can be challenging. Understanding compatibility factors is key to maximizing productivity and ensuring seamless integration.
Choosing compatible packaging equipment requires evaluating production needs, material properties, and system integration capabilities. These factors determine how well the equipment fits into existing workflows and its long-term effectiveness.

Analyze Production Requirements
When considering equipment compatibility, it’s important to analyze various aspects of your production line. Start by evaluating the specific products that need wrapping or handling. For instance, coil wrapping machines should match the size and shape of the coils you're dealing with. You’ll also want to consider future scalability. Will your chosen machine adapt to changing product lines or volumes?
The next aspect is system integration. How does the new equipment mesh with existing conveyors, labeling machines, or pallet systems? Mismatched interfacing can lead to operational hiccups. I recall a time when we introduced a new pallet stretch wrapper that didn’t sync correctly with our conveyor speeds. We had to recalibrate the entire line to ensure smooth operation.
Automation level is another crucial factor. David, a mid-sized manufacturing company specialist, often grapples with this. His experience shows that fully automated equipment demands better integration capabilities compared to semi-automated options. Here’s a table to summarize key compatibility considerations:
Compatibility Factor | Consideration Description | Impact |
---|---|---|
Product Specifications | Assess size, shape, and material of items being packaged | Mismatch can lead to inefficiency or product damage |
System Integration | Ensure equipment synchronizes with existing systems | Operational disruptions if equipment is not synchronized |
Automation Level | Determine suitability for your automation needs | Over- or under-automation can affect workflow performance |
2. What Compatibility Factors Should be Considered?
-In the world of automated packaging, selecting the right equipment can be challenging. Understanding compatibility factors is key to maximizing productivity and ensuring seamless integration.
Choosing compatible packaging equipment requires evaluating production needs, material properties, and system integration capabilities. These factors determine how well the equipment fits into existing workflows and its long-term effectiveness.
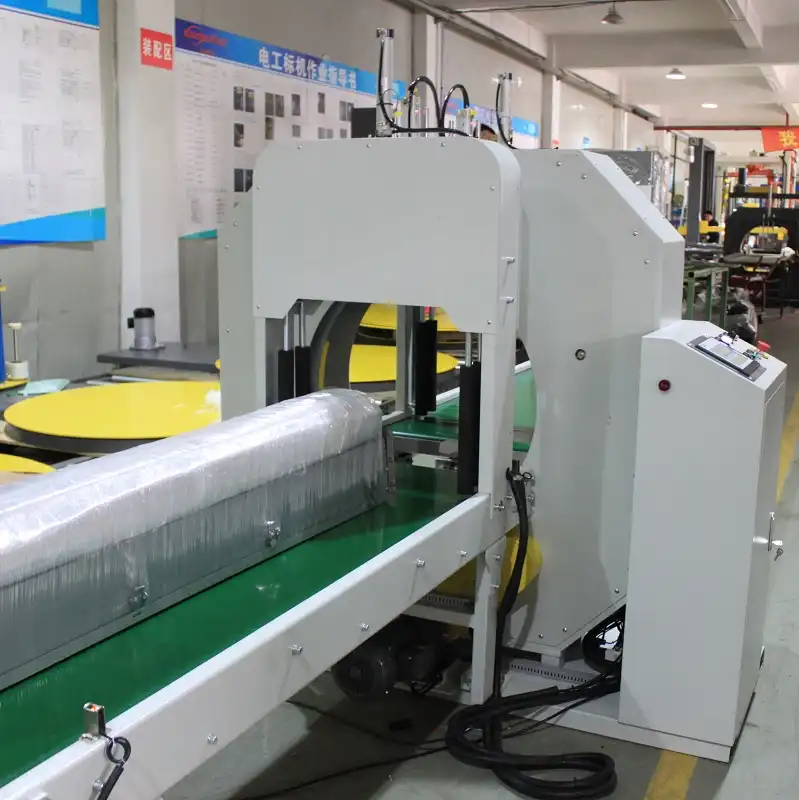
Analyze Production Requirements
When considering equipment compatibility, it’s important to analyze various aspects of your production line. Start by evaluating the specific products that need wrapping or handling. For instance, coil wrapping machines should match the size and shape of the coils you're dealing with. You’ll also want to consider future scalability. Will your chosen machine adapt to changing product lines or volumes?
The next aspect is system integration. How does the new equipment mesh with existing conveyors, labeling machines, or pallet systems? Mismatched interfacing can lead to operational hiccups. I recall a time when we introduced a new pallet stretch wrapper that didn’t sync correctly with our conveyor speeds. We had to recalibrate the entire line to ensure smooth operation.
Automation level is another crucial factor. David, a mid-sized manufacturing company specialist, often grapples with this. His experience shows that fully automated equipment demands better integration capabilities compared to semi-automated options. Here’s a table to summarize key compatibility considerations:
Compatibility Factor | Consideration Description | Impact |
---|---|---|
Product Specifications | Assess size, shape, and material of items being packaged | Mismatch can lead to inefficiency or product damage |
System Integration | Ensure equipment synchronizes with existing systems | Operational disruptions if equipment is not synchronized |
Automation Level | Determine suitability for your automation needs | Over- or under-automation can affect workflow performance |
3. Are There Any Cost Considerations to Keep in Mind?
- Investing in new packaging machinery requires careful analysis of costs. Understanding the total financial impact ensures efficient resource allocation and avoids budgetary surprises.
Cost considerations entail upfront purchase price, operational efficiency, and long-term maintenance. Evaluating these elements ensures that investments align with financial goals and operational needs.
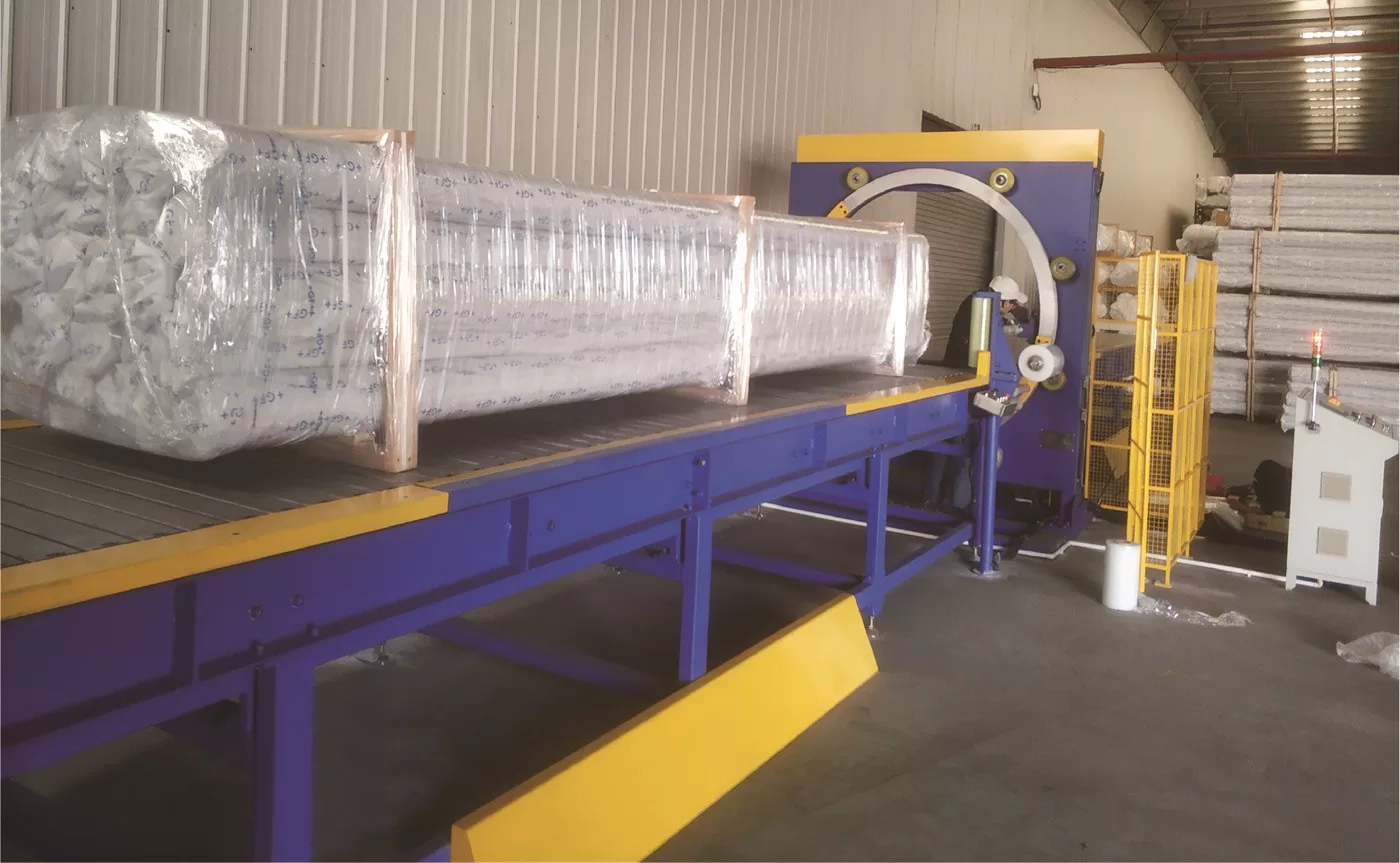
Breakdown of Cost Elements
Cost analysis should begin with the initial purchase price. While cheaper options can be tempting, remember that quality often correlates with price. Higher upfront costs might include advanced features that improve efficiency, like faster wrapping speeds or energy-saving operations.
Next, consider operational costs. This includes energy consumption, labor expenses, and downtime. A machine that uses less power reduces energy bills. Automation might cut labor costs in the long run, even if the initial outlay is higher. David’s move towards adopting advanced automation illustrates this point. He found it worthwhile to trade higher initial costs for long-term savings and error reduction.
Maintenance and repair costs are long-term considerations that could impact overall budget. Regular maintenance keeps machines running smoothly but consider the availability of spare parts and technician expertise. Here’s a detailed look at the cost considerations:
Cost Element | Consideration Description | Financial Impact |
---|---|---|
Purchase Price | Initial cost with potential trade-offs for advanced specifications | High initial outlay mitigated by feature and efficiency gains |
Operational Costs | Energy, labor, and potential downtime expenses | Affects daily operational budget and long-term utility costs |
Maintenance and Repair | Routine services and availability of parts | Predicts maintenance schedule costs and potential disruptions |
Conclusion
In conclusion, key aspects like operational efficiency, system compatibility, and cost-effectiveness are crucial when selecting a horizontal wrapping machine. Proper assessment ensures optimal performance and financial benefits.In conclusion, key aspects like operational efficiency, system compatibility, and cost-effectiveness are crucial when selecting a horizontal wrapping machine. Proper assessment ensures optimal performance and financial benefits.