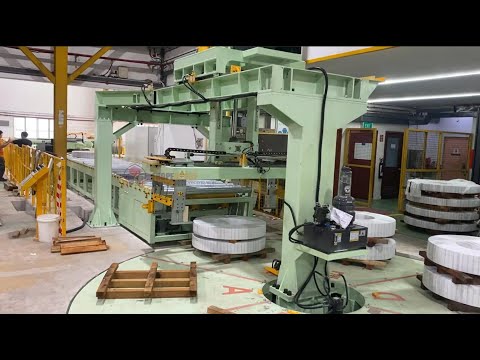
Slit Coil Packaging Line for Slitting Service Center with Automatic Labeling System Connected to ERP
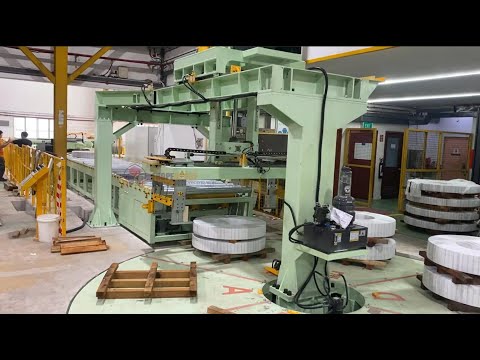
Slitting service centers face numerous challenges when it comes to efficiently packaging and labeling slit coils. Manual packaging and labeling processes are time-consuming, error-prone, and can lead to inconsistencies in the identification and traceability of slit coils. These issues can result in delayed shipments, customer dissatisfaction, and potential quality control problems.
To address these challenges, a slit coil packaging line with an integrated automatic labeling system connected to the company’s Enterprise Resource Planning (ERP) system is essential. The packaging line must be designed to handle slit coils of various sizes, materials, and specifications, ensuring secure and efficient packaging. However, without proper integration and automation, the packaging process can become a bottleneck in the overall operations of the slitting service center.
The automatic labeling system is a critical component of the packaging line, as it is responsible for accurately printing and applying labels to the packaged slit coils. The labels must contain crucial information about the slit coils, such as dimensions, weight, material grade, and customer details. Inaccurate or missing information on the labels can lead to confusion, delays, and potential misidentification of slit coils during storage, transportation, and delivery.
To ensure seamless integration and data consistency, the automatic labeling system must be connected to the company’s ERP system. The ERP system serves as a centralized platform for managing various business processes, including inventory management, order processing, shipping, and invoicing. Without proper integration between the labeling system and the ERP system, manual data entry and updates would be required, increasing the risk of errors and discrepancies.
The lack of automation and integration between the slit coil packaging line, automatic labeling system, and ERP system can lead to several problems. These include:
Inefficient and time-consuming packaging processes
Inconsistent and inaccurate labeling of slit coils
Difficulty in tracking and tracing slit coils throughout the supply chain
Increased risk of errors and delays in order fulfillment
Potential quality control issues and customer complaints
To overcome these problems, the slit coil packaging line must be designed with automation and integration in mind. The automatic labeling system should be seamlessly connected to the ERP system, enabling the automatic transfer of slit coil data from the ERP database to the labeling system. This integration eliminates the need for manual data entry and reduces the risk of errors or inconsistencies in the labeling process.
Furthermore, the packaging line should be equipped with advanced features such as barcode scanning, weight verification, and vision systems to ensure the accuracy and completeness of the packaged slit coils. These features help to identify any discrepancies or quality issues before the slit coils are shipped to customers.
In conclusion, a slit coil packaging line with an integrated automatic labeling system connected to the ERP system is crucial for slitting service centers to overcome the challenges associated with manual packaging and labeling processes. By automating and integrating these systems, slitting service centers can improve efficiency, accuracy, and traceability, ultimately enhancing customer satisfaction and reducing operational costs. However, proper planning, implementation, and maintenance of these systems are essential to ensure their effectiveness and reliability in addressing the problems faced by slitting service centers.