ShowCase: Solving Pallet Handling Challenges with Pallet Inverters and Wrapping Machines
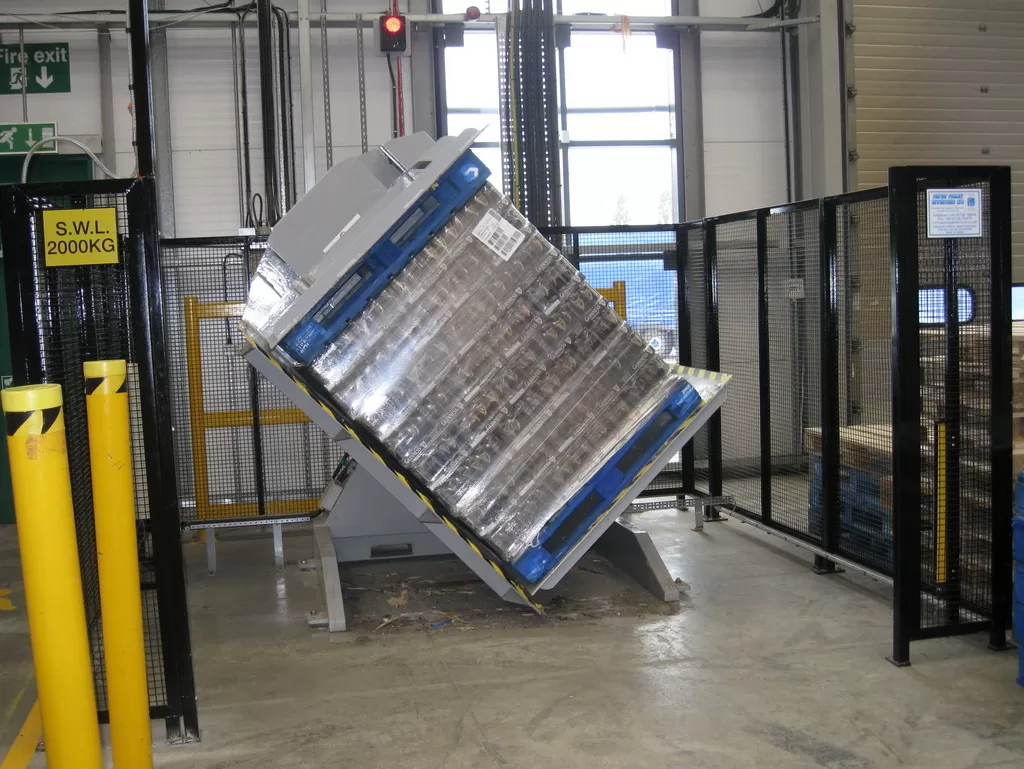
Introduction
Efficient pallet handling is a crucial component in warehousing and logistics operations across various industries. From large-scale manufacturing to distribution centers, pallets are the backbone of the supply chain. As companies look for ways to streamline processes and reduce downtime, pallet handling presents several unique challenges, particularly in the areas of pallet turning and pallet changing.
In Moscow, where the logistics sector is rapidly growing, businesses face persistent issues such as inefficient fork operations, manual labor intensity, product damage, and the loss of pallet shape. Addressing these common challenges is vital to optimizing productivity and reducing costs.
Problem-Solution Framing
In the warehousing and logistics industries, inefficiencies in pallet management can severely impact overall operations. Russian businesses in Moscow are often hindered by slow fork operations that make manual pallet changes both time-consuming and dangerous. Workers are exposed to high-risk tasks, and the manual handling of pallets leads to increased labor strength requirements, leaving employees fatigued and vulnerable to injuries.
Moreover, the improper handling of pallets results in product breakages, which not only leads to financial loss but also disrupts supply chains. Additionally, pallets lose their shape over time due to repeated mishandling, further exacerbating these challenges.
The ideal solution to these problems is the adoption of a pallet inverter. By integrating a pallet inverter into daily operations, businesses can greatly improve the efficiency of pallet handling while addressing safety concerns. A pallet inverter minimizes the need for manual intervention, automating the pallet turning process and ensuring that products are securely handled during the exchange. This leads to significant improvements in productivity, worker safety, and product protection.
Customization for Solution
One of the most compelling aspects of pallet inverters is their ability to be customized to meet specific operational requirements. For instance, the pallet inverter can be designed to handle pallets with dimensions of L1200 x W1250 x Height 1000-2200mm, making it suitable for a wide range of products and applications.
The machine's 180-degree turning capability and dual clampers allow for secure and efficient pallet exchanges, preventing product displacement or damage during the process. This degree of customization ensures that the pallet inverter can cater to various industries, whether it’s food and beverage, pharmaceuticals, or retail, highlighting its versatility in handling diverse types of goods.
Furthermore, the solution can be paired with a pallet wrapping machine to hold the pallet securely during the turning process, adding an extra layer of product protection. This combination ensures that both pallet integrity and product safety are maintained throughout the handling process. Businesses that require specific configurations, such as the handling of fragile or oversized goods, will find the pallet inverter's customization options indispensable for addressing their unique operational challenges.
Key Features and Benefits
The pallet inverter comes equipped with several features designed to enhance the efficiency of pallet handling. The 180-degree turning capability allows for complete inversion of pallets, which is particularly useful in situations where products need to be transferred between different pallets or when a damaged pallet must be replaced without disrupting the load. The dual clamping system ensures that the pallet and its load are securely held in place during the inversion process, reducing the risk of product movement or breakage.
In terms of benefits, the pallet inverter significantly reduces the time required for manual pallet handling, leading to time savings and increased throughput. By automating the process, businesses can reduce their reliance on manual labor, translating into cost-effectiveness as fewer workers are needed to manage pallet exchanges.
Another major benefit is the improvement in worker safety, as the pallet inverter eliminates the need for employees to physically lift and handle heavy loads, reducing the risk of injury. Additionally, the machine helps maintain the integrity of both the pallet and the product, preventing damage and ensuring that goods remain in optimal condition throughout the logistics process.
Real-World Examples
A Moscow-based logistics company recently integrated pallet inverters into their warehouse operations and reported significant improvements in efficiency. Prior to adopting the pallet inverter, the company faced frequent delays due to the slow pace of manual pallet handling. Their workers often struggled with the physical demands of the job, leading to high labor costs and a noticeable decline in employee productivity. After implementing the pallet inverter, the company saw a 40% reduction in handling time, which allowed them to process more orders in less time.
In another case, a Russian manufacturer that regularly handles fragile goods such as glass and ceramics was experiencing a high rate of product breakage due to improper pallet handling. By using a pallet inverter with a customized dual clamping system, the manufacturer was able to reduce product damage by 50%, resulting in significant cost savings.
The improved handling process also minimized the strain on workers, lowering the risk of workplace injuries and improving overall morale. These real-world examples demonstrate how pallet inverters can transform warehousing operations, offering tangible benefits in terms of efficiency, safety, and cost reduction.
Visuals and Video Demonstration
To truly understand the value of a pallet inverter, seeing the machine in action is essential. Embedding videos or images that showcase the machine's 180-degree turning capability and dual clampers can provide potential buyers with a clear visual representation of how the equipment operates.
These demonstrations can illustrate the machine's speed, precision, and ability to handle a variety of pallet loads. Videos showing before-and-after comparisons—highlighting how the pallet inverter reduces product breakage and speeds up pallet exchanges—can be particularly persuasive, helping customers visualize the benefits for their own operations.

Call to Action
Are you ready to take your warehousing and logistics operations to the next level? Contact us today to learn more about how a pallet inverter and pallet wrapping machine can revolutionize your pallet handling processes. We offer customized quotes based on your specific requirements and invite you to schedule a demonstration to see the machine in action.
Our team is ready to work with you to develop a tailored solution that will improve efficiency, reduce labor costs, and enhance product safety. Don’t wait—reach out now to explore how the pallet inverter can transform your business.
FAQs
1. What types of pallets are compatible with the pallet inverter?
Our pallet inverter is compatible with a wide range of pallet sizes, including those with dimensions of L1200 x W1250 x Height 1000-2200mm. The machine can be customized to handle different sizes and types of pallets, making it versatile for various industries.
2. How long does installation take?
Installation is quick and seamless, with our team of experts managing the entire process. Depending on the size and complexity of your operations, installation can typically be completed within a few days, allowing you to integrate the equipment with minimal disruption to your workflow.
3. What kind of maintenance is required?
Pallet inverters are designed to be low-maintenance, requiring only regular checks and basic servicing to ensure optimal performance. Our team provides full support, including maintenance training for your staff to keep the equipment running smoothly.