Revolutionizing Load Handling: A Deep Dive into Pallet Inverter Technology and Applications
In modern warehousing and logistics, the efficient and safe transfer of goods between pallets is a critical operational bottleneck. Manual methods are labor-intensive, slow, and pose significant ergonomic risks. Enter the pallet inverter – a specialized piece of material handling equipment designed to automate and streamline this process, boosting productivity and enhancing workplace safety. This technology, refined through years of engineering and documented in numerous patents focusing on clamping and rotational mechanisms, offers a robust solution for diverse industries.
Understanding Pallet Inverter Mechanics
At its core, a pallet inverter is an electromechanical or hydraulic machine engineered for load inversion. The fundamental operating principle involves:
- Loading: The palletized load is placed into the inverter, often via forklift or pallet truck.
- Clamping: Secure, pressure-controlled clamps engage the sides (or sometimes top and bottom) of the load, holding it firmly in place. Advanced systems often incorporate sensors to apply appropriate pressure based on load characteristics, minimizing potential damage.
- Rotation: The machine lifts and rotates the clamped load, typically through a 180-degree arc. This inversion is powered by hydraulic or electric drive systems, designed for smooth, controlled movement. Key innovations, often subject of patents, focus on optimizing the stability and efficiency of this rotational process.
- Pallet Exchange: Once inverted, the original pallet is now accessible at the top and can be easily removed and replaced with a new one (e.g., switching from wood to plastic, or replacing a damaged pallet).
- Return & Release: The machine rotates the load back to its original orientation (or maintains the inverted state if required) and lowers it onto the new pallet before releasing the clamps.
The entire cycle, often completed in 30-60 seconds depending on the model and load, drastically reduces the time required compared to manual restacking.
Key Operational Advantages and ROI
The adoption of pallet inverter technology delivers quantifiable benefits, aligning with core objectives often highlighted in manufacturing and logistics publications:
- Enhanced Productivity & Throughput: Automating the pallet exchange process significantly cuts down handling times. Research indicates potential throughput increases of several hundred percent compared to manual methods, directly impacting warehouse efficiency.
- Improved Worker Safety & Ergonomics: Manual pallet handling is a primary source of musculoskeletal disorders (MSDs) in warehouse environments. Pallet inverters eliminate the need for repetitive bending, lifting, and twisting, significantly reducing injury risks and aligning with OSHA guidelines for safe material handling. This translates to fewer workers' compensation claims and a safer work environment.
- Reduced Product Damage: The controlled clamping and rotation provided by pallet inverters minimize the risk of damage that can occur during manual restacking, protecting valuable inventory.
- Operational Flexibility: Pallet inverters are versatile tools used for various tasks beyond simple pallet exchange, including:
- Switching loads to higher quality or sanitized pallets (critical in food/pharma).
- Replacing damaged pallets without destacking goods.
- Transferring goods from containers or slipsheets to pallets.
- Straightening shifted loads.
- Facilitating freezer spacer removal/insertion.
- Significant Cost Reduction: By increasing speed, reducing labor requirements for manual handling, minimizing product damage, and lowering injury-related costs, pallet inverters offer a compelling Return on Investment (ROI), often realized within a short operational period.
Typical Technical Specifications
When evaluating pallet inverters, key parameters include:
- Load Capacity: Ranges typically from 1000 kg (2200 lbs) to over 2500 kg (5500 lbs).
- Rotation Angle: Standard 180 degrees; some models offer 90 or other angles.
- Cycle Time: Generally 30-60 seconds, influencing overall throughput.
- Pallet Size Compatibility: Adjustable for various standard pallet dimensions (GMA, CHEP, EURO).
- Clamping Mechanism: Hydraulic or electric, with adjustable pressure settings.
- Control System: Push-button panels, PLC integration for automated lines.
- Power Requirements: Typically 3-phase electrical power; specific voltage/frequency requirements vary.
- Safety Features: Standard inclusion of safety guarding, light curtains, emergency stops, and hydraulic safety valves, complying with international safety norms.
Industry Applications
Pallet inverters are indispensable in sectors requiring high standards of hygiene, efficiency, and load integrity:
- Food & Beverage: Transferring goods onto plastic or sanitized pallets for cleanroom environments.
- Pharmaceuticals: Ensuring product integrity and compliance with handling regulations.
- Chemical Manufacturing: Safely handling bagged or containerized goods.
- Logistics & Distribution: Optimizing cross-docking, warehousing, and outbound shipping processes.
- Printing & Paper: Handling heavy, sensitive paper stacks.
Conclusion: A Cornerstone of Modern Material Handling
As documented in industry reports and case studies, the pallet inverter is more than just a convenience; it's a strategic asset for optimizing material flow in demanding environments. By addressing critical challenges in speed, safety, and product care, this technology directly contributes to a more efficient, cost-effective, and safer supply chain operation, reflecting the continuous drive for automation and improvement seen across the manufacturing and logistics landscape.
info@fhopepack.com
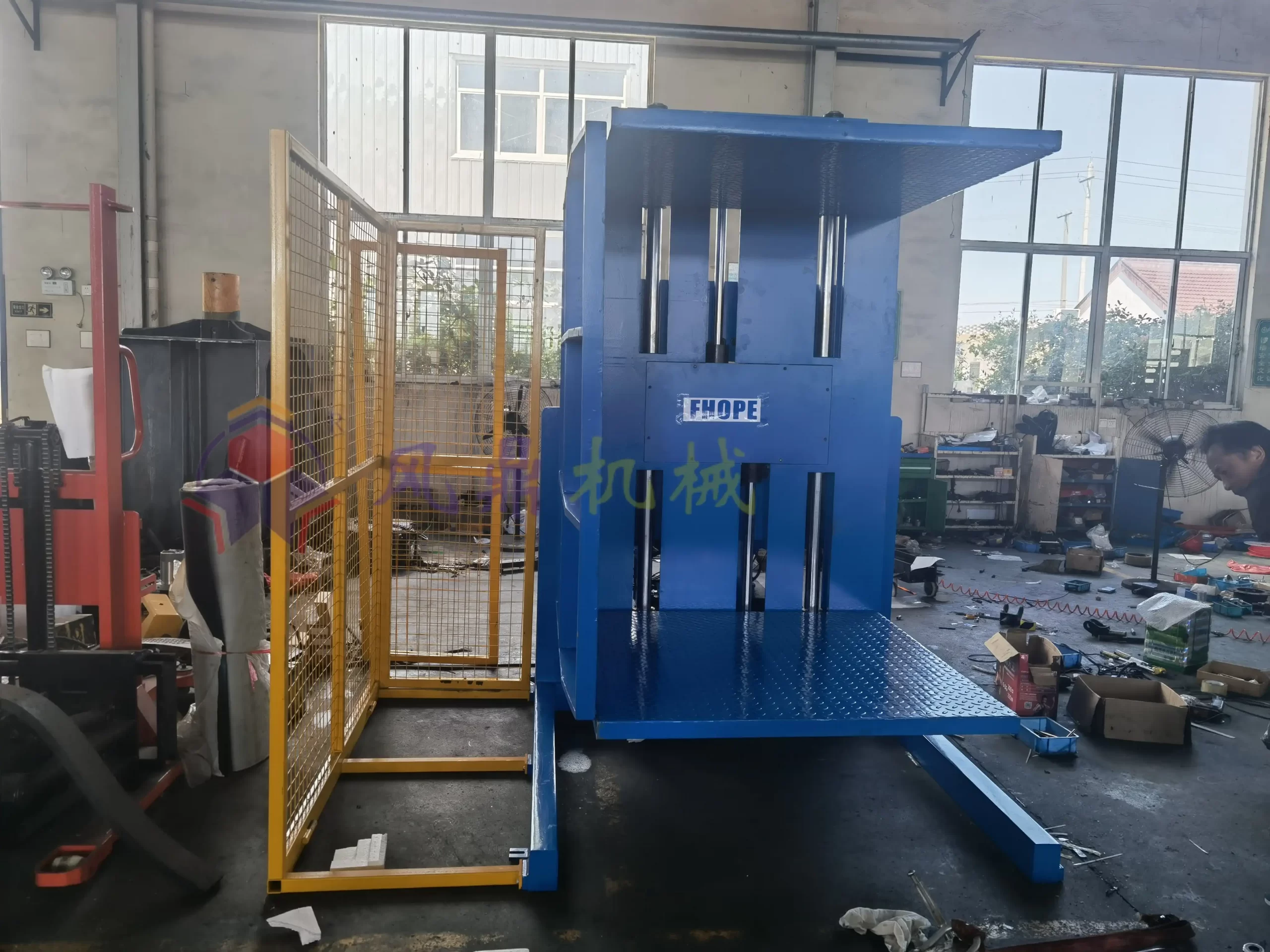
More pallet inverter machines:
https://www.fhopepack.com/Pallet-Inverter-Machines/
https://www.fhopepack.com/pallet-inverter/
More pallet inverters: https://www.fhopepack.com/blog/real-manufacturer-of-the-pallet-inverter/