Need to speed up and streamline your MDF packing process? Automation is the answer, reducing labor costs and improving efficiency. Say goodbye to manual mistakes and hello to precision.
Automating MDF packing involves using inline solutions to seamlessly integrate machines into production lines. This setup minimizes human intervention, increases speed, and ensures consistent packing quality. An automated process can lead to reduced operational costs and fewer errors, making your packaging both effective and efficient.
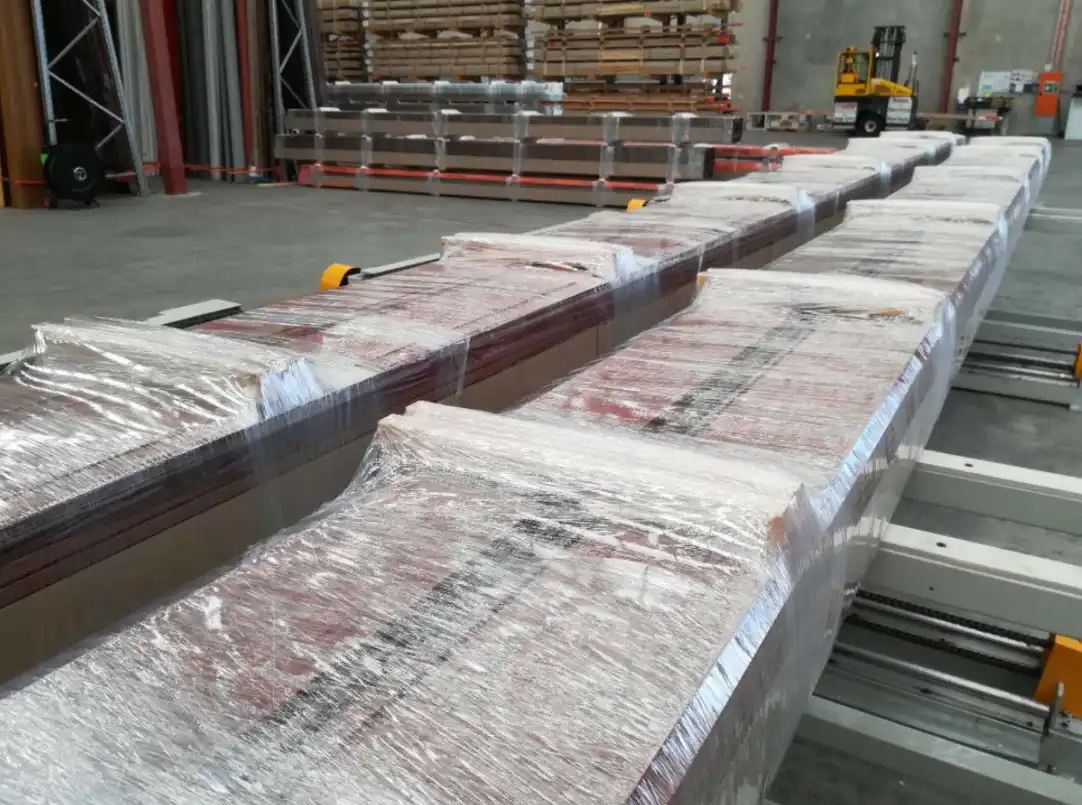
Imagine a world where your MDF packing process operates like a well-oiled machine. With the right inline solution, you can achieve more than just efficiency; you'll gain reliability, speed, and consistency in every package.
1. What is MDF Packing Automation?
MDF production bottlenecks can slow your operation, causing frustration and lost revenue. Automation changes this narrative, offering speed and seamless operation.
MDF packing automation refers to utilizing machines to handle the packing process. This involves automated systems that conduct tasks like wrapping, sealing, and labeling, enhancing productivity and accuracy. An automated packing line reduces dependency on manual labor, providing consistent packaging and increased throughput with minimized errors.
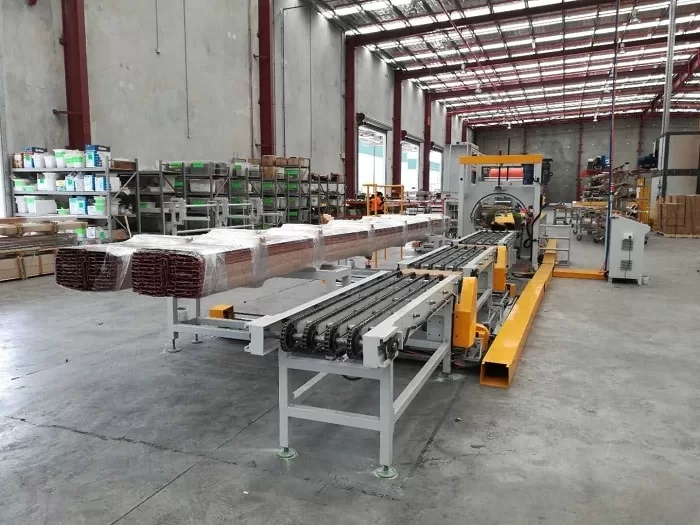
Benefits and Considerations of MDF Packing Automation:
When deciding to automate, several key factors and benefits should be considered to define the right strategy for your business.
Benefits of MDF Packing Automation:
-
Increased Efficiency:
Automated systems eliminate the need for manual packing, leading to faster processes. They maintain a constant pace, optimizing the overall output of the packing line. -
Enhanced Consistency:
Machines operate with precision, ensuring that each package is identical. This uniformity helps maintain quality standards without room for human error. -
Cost Efficiency:
Initially, automation might seem costly, but the long-term savings in labor costs and reduced errors outweigh initial expenses. Automating the line cuts down labor hours required for packing. -
Safety Improvements:
Automating the packing process reduces the physical strain on workers, lowering the risk associated with manual tasks such as heavy lifting. -
Flexibility:
Automated systems can be adjusted to match different packing configurations and sizes, allowing for versatility in handling various products.
Considerations in Automation:
Consideration | Explanation |
---|---|
Initial Investment | High upfront costs for equipment and installation. |
Training Requirements | Staff must be trained to manage and troubleshoot automated systems. |
Space and Integration | Enough space and seamless integration with existing production lines needed. |
In my personal journey automating packaging in different industries, I found the initial implementation challenging. However, the gains in productivity and consistency made it worthwhile. Automation can truly transform your MDF packing process, offering solutions tailored to your business's specific needs. Assess your requirements, calculate ROI, and embark on a path to greater efficiency.## 2. How Does an Inline Solution Work for MDF Packing?
The inconsistency and delays in MDF packing tarnish production flow. Smoother processes? An inline solution could be the answer to seamless production! Take action today.
An inline MDF packing solution integrates automation within the production line. It ensures consistency, reduces labor involvement, and minimizes the risk of damage. Automated systems streamline MDF board handling, packaging, and delivery processes for better efficiency and reliability.
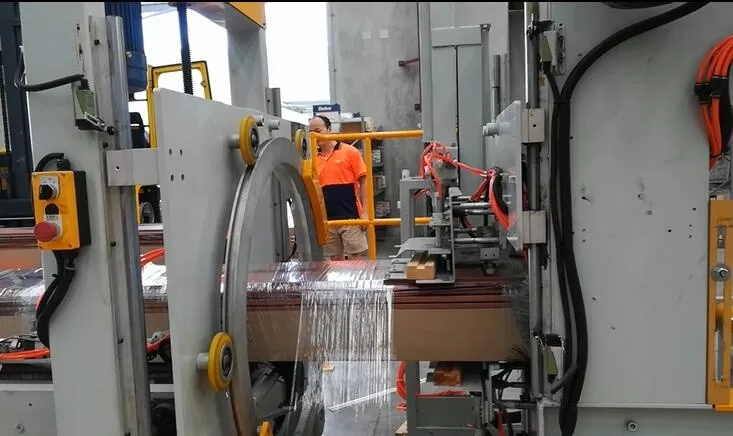
Improved Automation for MDF Handling
When it comes to MDF packing, an inline solution revolutionizes the entire process. Traditional methods often involve high labor costs, inconsistent packing quality, and the risk of human error. Today’s inline systems offer automation that ensures every stage of MDF handling and packaging is standardized and efficient.
Automation minimizes manual intervention, providing consistent and reliable packaging results. This is achieved through meticulously designed systems that handle MDF with precision. By aligning every component of the packing line—from conveyors to wrapping stations—an inline solution reduces waste and delivers optimal productivity.
Furthermore, an inline solution can incorporate advanced technology like sensors and IoT capabilities to monitor the process in real-time. For instance:
Component | Function | Benefits |
---|---|---|
Conveyor Systems | Transport and position MDF boards | Consistency and speed |
Automated Wrappers | Apply packaging materials uniformly | Quality and reduced material use |
IoT Sensors | Monitor packing conditions and performance metrics | Data-driven improvements |
By implementing such innovations, these systems drastically reduce packing times and promote exceptional workflow continuity. As a result, companies benefit from uncompromised efficiency and maximized throughput in their MDF packing operations.
2. How Does an Inline Solution Work for MDF Packing?
The inconsistency and delays in MDF packing tarnish production flow. Smoother processes? An inline solution could be the answer to seamless production! Take action today.
An inline MDF packing solution integrates automation within the production line. It ensures consistency, reduces labor involvement, and minimizes the risk of damage. Automated systems streamline MDF board handling, packaging, and delivery processes for better efficiency and reliability.
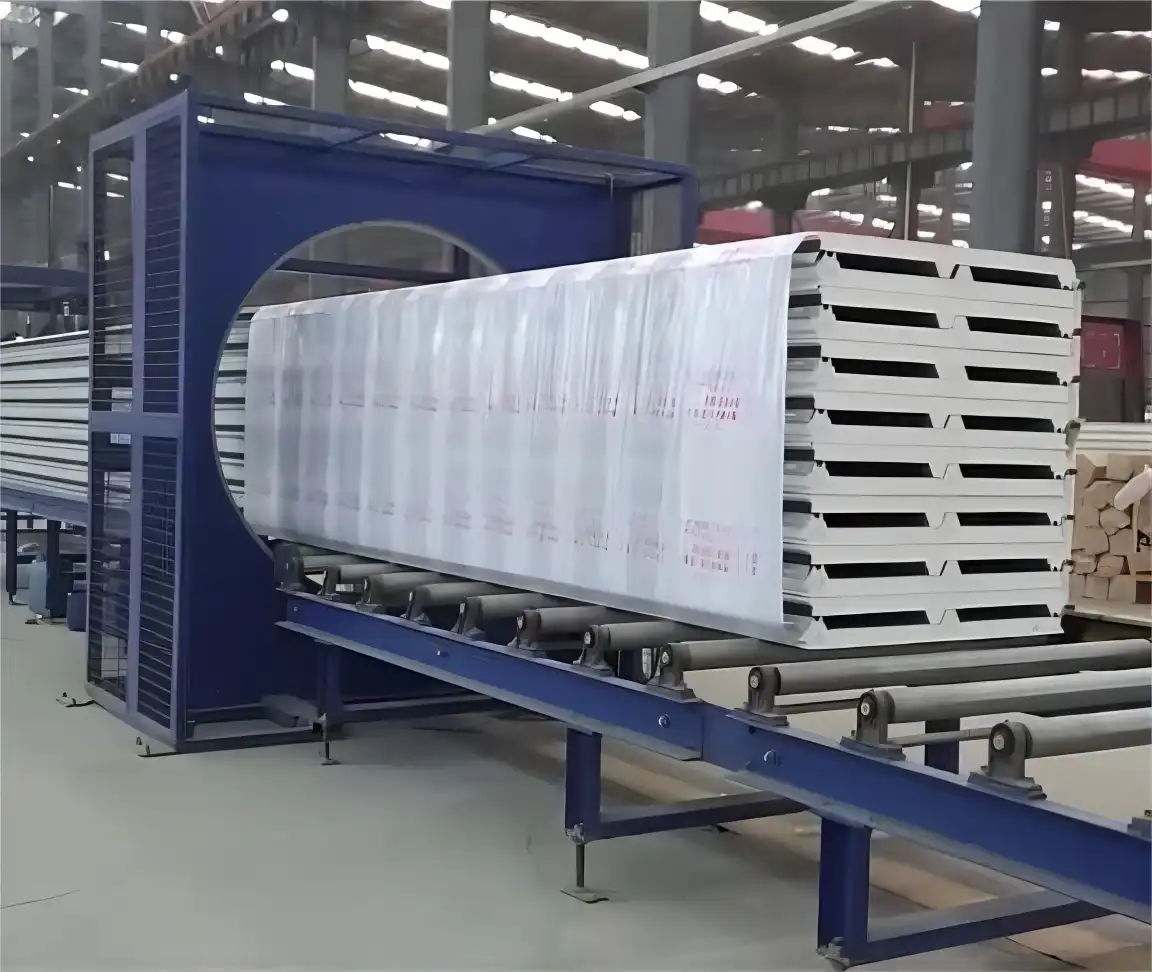
Improved Automation for MDF Handling
When it comes to MDF packing, an inline solution revolutionizes the entire process. Traditional methods often involve high labor costs, inconsistent packing quality, and the risk of human error. Today’s inline systems offer automation that ensures every stage of MDF handling and packaging is standardized and efficient.
Automation minimizes manual intervention, providing consistent and reliable packaging results. This is achieved through meticulously designed systems that handle MDF with precision. By aligning every component of the packing line—from conveyors to wrapping stations—an inline solution reduces waste and delivers optimal productivity.
Furthermore, an inline solution can incorporate advanced technology like sensors and IoT capabilities to monitor the process in real-time. For instance:
Component | Function | Benefits |
---|---|---|
Conveyor Systems | Transport and position MDF boards | Consistency and speed |
Automated Wrappers | Apply packaging materials uniformly | Quality and reduced material use |
IoT Sensors | Monitor packing conditions and performance metrics | Data-driven improvements |
By implementing such innovations, these systems drastically reduce packing times and promote exceptional workflow continuity. As a result, companies benefit from uncompromised efficiency and maximized throughput in their MDF packing operations.
3. What Are the Key Considerations for Implementing an Inline MDF Packing Solution?
Frustrated by inefficient MDF packing methods? Discover essential factors to consider when implementing cutting-edge inline packing solutions that transform productivity standards.
Key considerations for inline MDF packing include evaluating production volumes, determining system compatibility with existing operations, and assessing the cost-effectiveness of the investment. These factors ensure seamless integration and optimized use of resources.
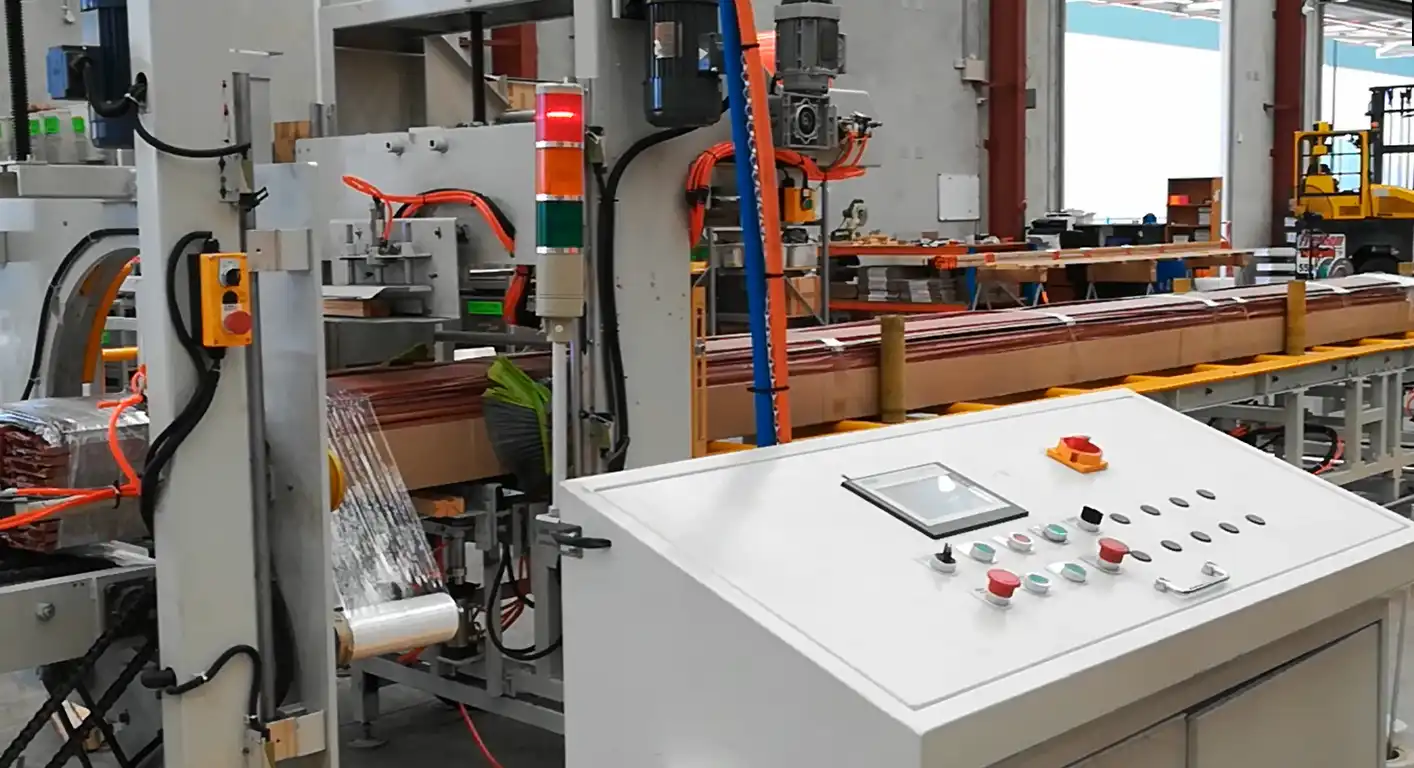
Evaluating Essential Factors for Implementation
Establishing an inline MDF packing solution involves careful consideration of various elements that will dictate its success. Each manufacturing setup presents unique challenges and opportunities. Therefore, identifying specific needs and conditions is crucial.
Production Volumes and Capacity
Manufacturers must evaluate their production volumes to choose a system that accommodates current and future demands. Systems should be scalable and flexible to manage fluctuating production levels efficiently without overextending resources.
Evaluation Aspect | Considerations | Impact |
---|---|---|
Volume Matching | Aligning system capacity with production needs | Prevents bottlenecks and downtime |
Scalability | Ability to adapt to increases or decreases in demand | Long-term operational efficiency |
Resource Allocation | Efficient usage of materials and labor | Cost-effectiveness |
System Compatibility and Integration
Integrative systems must complement existing operations. Evaluating how new technologies mesh with current workflows and machinery is vital to ensure smooth transitions and robust performance.
Assess systems for integration capabilities with existing equipment like conveyors and other automated elements. Compatibility often dictates how easily teams can adopt new technologies, thus impacting the speed of realization of desired efficiencies and improvements.
Conclusion
Automating MDF packing through inline solutions presents numerous advantages that redefine production dynamics. Such systems deliver consistent and high-quality packaging by reducing reliance on manual labor and mitigating risks associated with human error. Automation boosts operational speed and minimizes turnaround time, enabling companies to meet tight production schedules. Besides operational enhancements, inline solutions offer data-driven tools for performance evaluation. Monitoring various metrics allows for proactive maintenance and continuous improvement. Ultimately, these solutions not only optimize productivity and cost-effectiveness but also establish a sustainable, future-focused manufacturing framework.Summarize the potential benefits of automating MDF packing and how an inline solution can revolutionize efficiency in production processes.