I often notice people worry about lifting heavy coils. They want a safer way to flip them without accidents.
A coil upender flips coils from horizontal to vertical. It does this by clamping the coil, then rotating it smoothly. It speeds up production and prevents damage.
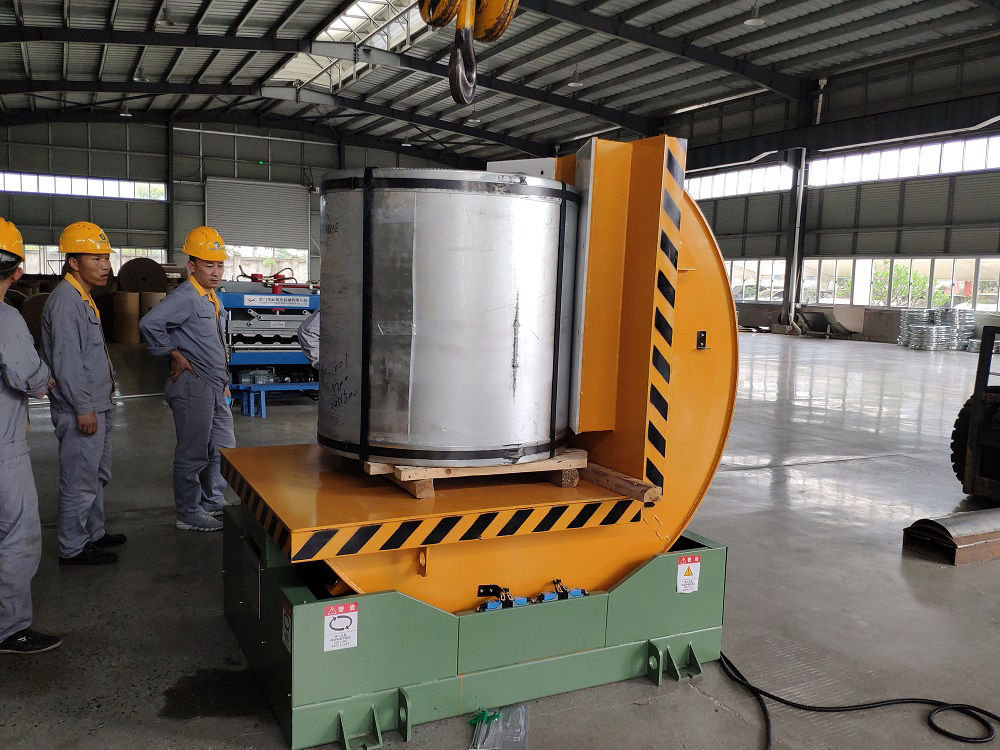
I have seen how this tool improves workflow. I hope to share insights, so we can all handle coils more efficiently.
What Is a Coil Upender?
I see many workplaces that lack specialized tools. Employees try to flip coils by hand. This is risky and time-consuming.
A coil upender eliminates manual flipping. It positions coils securely and rotates them with control. It keeps staff safe and reduces workplace injuries.
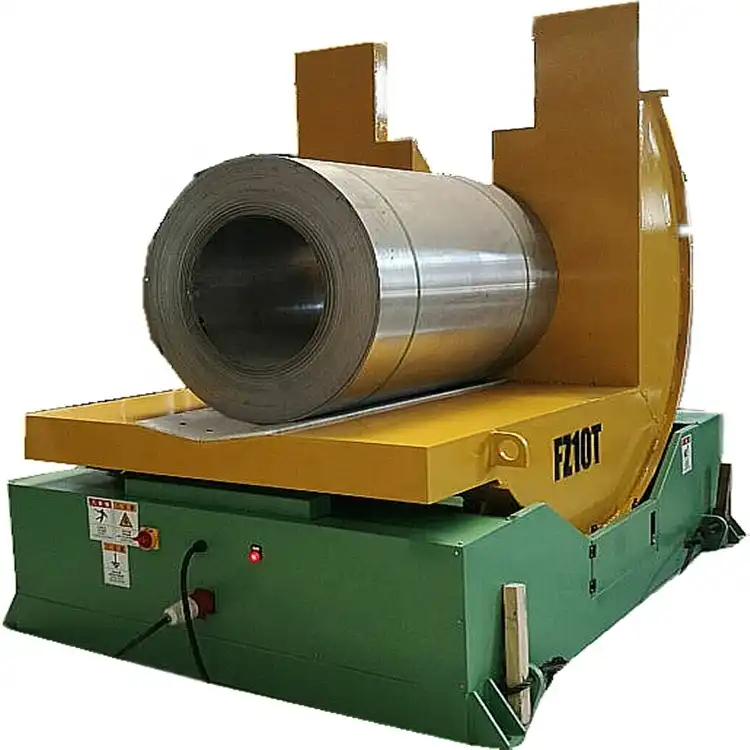
coil upender definition
Dive Deeper into the Basics of a Coil Upender
I believe in giving a clear breakdown. A coil upender usually has a robust frame, a rotating cradle, and a drive system. The drive can be mechanical or hydraulic. You place the coil in the cradle, secure it, and press a button. The machine rotates the coil from lying down to standing upright. This single motion saves labor and minimizes damage risks.
I want to show how it works with a simple flow:
- Position the Coil: Use a forklift or crane to place the coil on the cradle.
- Secure the Coil: Adjust clamps or guides to hold the coil firmly.
- Start Rotation: Activate the machine. The coil rotates slowly to avoid sudden jerks.
- Upright Position: The coil stands upright, ready for loading or further processing.
I also look at how the machine is made. A stable base is critical. The coil can weigh several tons. The cradle must offer enough grip. The motor or hydraulics must produce enough torque to flip the entire load. I focus on clear instructions for the operator. Some machines come with push-button controls. Others have touchscreens or remote controls.
Below is a short table I prepared. It shows some key comparisons between mechanical and hydraulic upenders:
Feature | Mechanical Upender | Hydraulic Upender |
---|---|---|
Torque | Fixed by gear ratio | Adjustable via fluid pressure |
Maintenance | Simpler gear components | Requires attention to seals |
Load Capacity | May be lower for large coils | Often higher for heavy coils |
Cost | Often more affordable | Tends to be higher |
I remind everyone to consider these factors. A mechanical upender can be enough if your coils are lighter. But if you handle huge coils, a hydraulic model might be better.
I see how coil upenders connect with existing systems. Many factories place them near conveyors or wrapping stations. This creates a smooth flow of coils from one process to another. You can automate the entire sequence, reducing manual intervention. This leads to fewer errors and a safer workplace.
I also notice coil upenders improve quality control. When you rotate a coil by hand, you risk denting or scratching its surface. An upender applies uniform support, preventing sudden impact. This is helpful for industries that need perfect coil edges, like automotive or steel service centers.
Upenders also help with space management. Storing coils upright can free up room on the production floor. When coils are vertical, they can be packed closer together. This is especially valuable in smaller facilities. In my experience, every meter of space can matter.
Finally, routine checks keep the coil upender running smoothly. Lubricate moving parts, inspect clamps, and watch for abnormal sounds. If you see leaks in a hydraulic model, fix them before they become serious. If it is mechanical, check gears for wear. Consistent upkeep ensures a long service life and reduces downtime. Over time, a coil upender pays for itself in saved labor, reduced injuries, and boosted productivity.
Why Is a Coil Upender Important?
I have seen managers struggle with manual flipping. They worry about worker safety and product damage.
A coil upender solves these problems. It ensures safe handling, reduces injuries, and prevents coil dents or scratches. It also improves workflow and lowers labor costs.
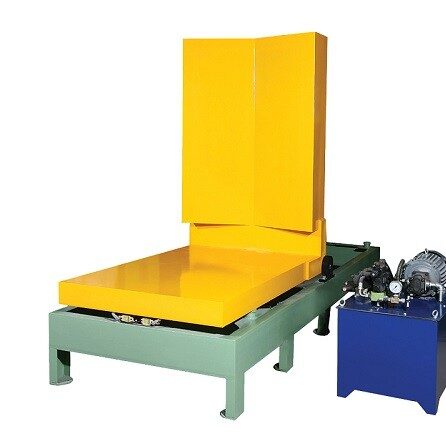
importance of coil upender
Dive Deeper into the Significance of Coil Upenders
I want to highlight how coil upenders add immediate value. The first point is enhanced safety. When I worked on a busy floor, I saw someone strain his back trying to tip a coil. After we installed an upender, that problem vanished. Employees no longer place themselves under heavy loads or awkward angles. They just press a button and let the machine do the heavy work.
Second, a coil upender boosts productivity. Workers do not spend time shifting coils manually. This frees them to focus on more skilled tasks. It also leads to consistent flipping speeds. This consistency can help managers plan production schedules with fewer delays. When you save time at each step, you get more done each day.
Third, there is product protection. Manually flipped coils sometimes slip. A forklift might leave marks on coil edges. An upender cushions the coil during rotation. This keeps surfaces clean and the overall shape intact. In industries like automotive or construction, coil integrity matters. A single damaged coil can harm product reputation. An upender helps lower that risk.
Fourth, coil upenders fit different layouts. Factories can be crowded. An upender that flips coils in a small footprint is useful. Some models feature a tilting platform that does not need extra clearance. Others might rotate coils more widely but offer higher capacity. You pick one that suits your space. This flexibility makes it an attractive investment in many industries.
Fifth, training and operation are simpler than many people think. Most upenders have an easy control panel. Operators can learn the basics quickly. This reduces downtime when introducing new equipment. Some advanced models include sensors to detect coil position. They stop automatically if something is wrong. These safety features let me sleep better at night.
Here is a table that shows reasons why a coil upender is vital:
Key Reason | Explanation | Outcome |
---|---|---|
Safety | Removes need for manual flipping | Fewer injuries and accidents |
Efficiency | Speeds up coil handling | Improved overall productivity |
Product Integrity | Keeps coils secure during rotation | Less damage and fewer rejects |
Space Management | Adapts to various factory layouts | Optimizes floor usage |
Ease of Training | Simple controls and automatic safety features | Quick operator adoption |
Sixth, coil upenders help maintain consistent quality across the board. They remove the guesswork from flipping. In manual handling, coil orientation can vary. With an upender, you get uniform rotation every time. This standardization ensures that the next step in your process goes smoothly.
Seventh, I see how upenders integrate into automated lines. If you have a conveyor system, you can place the coil on the upender via a conveyor. After flipping, another conveyor moves it onward. This reduces the need for human contact. Less human contact means fewer errors and a faster throughput.
Lastly, coil upenders show a commitment to modernizing production. They can reflect well on the company’s branding. Clients who see advanced handling equipment might trust your processes. They may assume you handle all manufacturing steps with the same professionalism. It can become a selling point when pitching to new customers or partners.
How Do I Choose the Right Coil Upender?
I have noticed many different upenders on the market. Some use hydraulic power, some use mechanical gears, and some come with fancy features.
I first look at load capacity. Then I consider coil size, floor space, and how it integrates with other machines. This helps me pick the best fit.
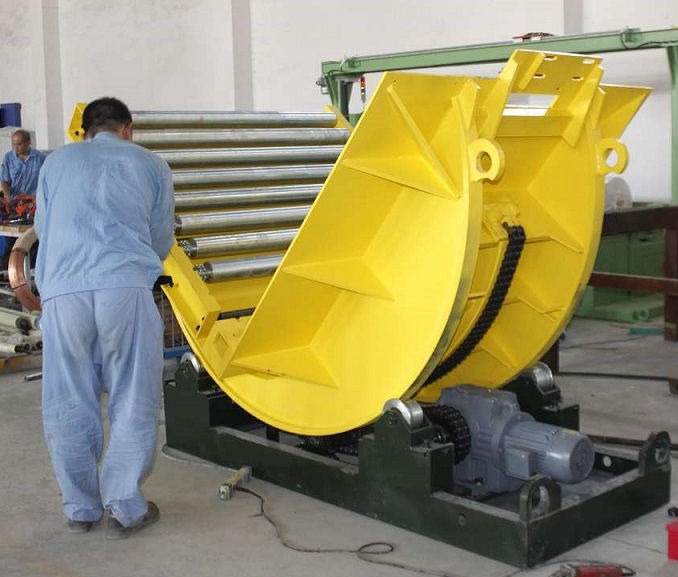
choosing a coil upender
Dive Deeper into Selecting the Ideal Coil Upender
I want to walk through my selection process step by step. First, I consider my typical coil weights. If I handle coils around 5 tons, I aim for an upender with at least a little extra capacity. This buffer ensures safe operation and accounts for slight variations in coil weight. It also prepares me if heavier coils come in the future.
Second, I think about coil dimensions. A wide coil might need adjustable clamps or cradles. Some upenders allow the cradle to expand or contract to match the coil’s diameter. This flexibility prevents me from buying multiple machines for slightly different coil sizes.
Third, power source is important. A hydraulic upender might offer stronger torque but requires extra care with hoses and seals. A mechanical upender might be simpler to maintain and sometimes costs less. I compare both based on my budget and the environment. If my facility has easy access to hydraulic support, then a hydraulic model might be a better fit.
Fourth, control features matter. Some upenders come with a standard control box. Others have advanced PLC-based systems with sensors that detect coil position. When I want more automation, I pick a machine that can link to other parts of the line. It can pause if the next station is not ready. It can also send signals when flipping is done.
Below is a table with factors to consider:
Factor | Why It Matters | Example Outcome |
---|---|---|
Load Capacity | Must match or exceed coil weight | Prevents overloading and breakdowns |
Coil Dimensions | Fits coil diameter and width range | Avoids buying multiple machines |
Power Source | Affects torque and maintenance | Hydraulic vs. mechanical choice |
Controls & Sensors | Automates flipping for efficiency | Better integration with production |
Footprint | Matches your available floor space | Easy to install in tight areas |
Fifth, footprint is a major concern. Some factories already have crowded aisles. I measure the space and think about the flipping arc. If it rotates coils more widely, I leave room for clearance. If the upender has a smaller footprint, I can place it closer to other machines. That might improve flow. I need to plan the layout in advance so I do not block walkways or forklift paths.
Sixth, after-sales support is key. I know that if a component fails, I need swift service. I look for a supplier that offers spare parts, quick troubleshooting, or even remote assistance. FHOPEPACK, where I work, provides these resources for clients, ensuring minimal downtime if something goes wrong.
Seventh, price matters, but I try not to select only based on cost. A cheaper model might have higher maintenance needs. It could break down more often, resulting in lost production. I examine the total cost of ownership, which includes initial price, operational costs, spare parts, and potential upgrades. This helps me choose a machine that gives me the best long-term value.
Eighth, I think about future expansion. If I plan to increase coil throughput, or if I might handle bigger coils, I want an upender that scales. Sometimes, I pick a model with a bit more capacity than I need right now. That way, I do not have to replace it in a year or two.
Lastly, I always gather feedback from operators or maintenance teams. They can point out practical concerns. Maybe the control buttons are too small or the cradle design is tricky for certain coil types. These small details can affect everyday use. By listening to actual users, I pick an upender that meets real-world demands. I believe in striking a balance between capacity, ease of use, and affordability.
Conclusion
I see a coil upender as a vital tool for safe and efficient coil flipping. It saves time, protects products, and makes daily work better.