### 2. Key Machine Specifications and Capabilities
This type of corrugated hose coil wrapping machine is engineered with specific parameters to handle delicate products effectively:
* **Coil Size Handling:** Capable of wrapping light and small hose coils, including those with inner diameters (ID) down to 150mm. Suitable for a range of outer diameters and widths common in the industry.
* **Wrapping Material:** Designed primarily for use with LLDPE stretch film, providing excellent protection against dust, moisture, and handling abrasion. Other materials like PE film or paper might be applicable depending on configuration.
* **Ergonomic Design:** The machine typically features a working height of around 900mm. This elevation is operator-friendly, simplifying both the loading of unwrapped coils and the unloading of finished packages, reducing physical strain.
* **Control System:** Often utilizes PLC controls for reliable operation, allowing for precise adjustments to wrapping parameters like film overlap, tension, and the number of wrap layers.
* **Wrapping Method:** Employs orbital wrapping technology, where the packaging material revolves around the stationary coil, ensuring complete coverage.
### 3. Operational Insights and Best Practices
Achieving optimal results with automated hose coil wrapping involves attention to detail:
* **Film Tension:** Proper stretch film tension is vital. Too little tension results in a loose wrap, while excessive tension can deform the coil or lead to film breaks. The machine allows for adjustable tension control to match the specific hose type and coil size.
* **Overlap Adjustment:** Consistent overlap between film layers ensures complete protection. This is typically adjustable via the control panel to provide anywhere from 10% to 90% overlap as needed.
* **Coil Centering:** Ensuring the coil is properly centered on the support rollers before starting the cycle is crucial for a uniform wrap. The press-down device assists, but initial placement matters.
* **Handling Corrugations:** The packaging must conform to the corrugated surface without damaging the structure. The combination of appropriate film tension and the gentle pressure from the holding device achieves this.
### 4. Advantages for Industrial Distribution
Automating the wrapping of corrugated hose coils offers several benefits for manufacturers and distributors:
* **Enhanced Product Protection:** Provides a secure, sealed package protecting hoses from environmental factors and handling damage during transit and storage.
* **Improved Package Consistency:** Automated wrapping ensures every coil is packaged uniformly, enhancing professionalism and brand image.
* **Increased Efficiency:** Significantly faster than manual wrapping methods, boosting throughput and reducing labor costs.
* **Optimized Material Usage:** Precise control over film stretch and overlap minimizes material waste compared to manual application.
* **Operator Safety & Ergonomics:** Reduces repetitive manual tasks and incorporates user-friendly design features like optimal working heights.
More hose coil packing solutions:
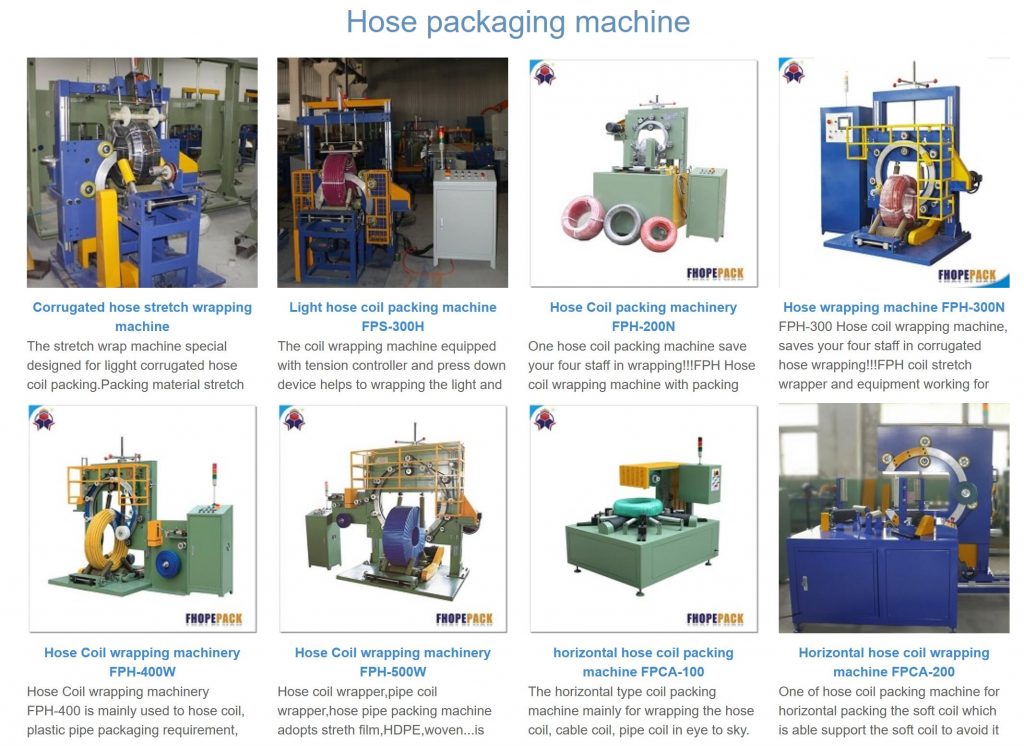