Automated End-of-Line Solution for Plastic Pipe Bundling and Bagging
In modern plastic pipe manufacturing, efficiency and automation at the end-of-line packaging stage are critical for maintaining throughput and reducing operational costs. Manual or semi-automated processes often create bottlenecks, increase labour dependency, and risk inconsistent package quality. Addressing these challenges, FHOPE presents a fully automated system designed for the demanding environment of plastic pipe production.
Introducing the FHOPE Integrated Pipe Packaging System
FHOPE offers a robust, Full-Automatic Online plastic pipe bundling strapping and bagging packing machine, engineered for seamless integration into extrusion lines. This system provides a turnkey solution for handling, bundling, strapping, and bagging various types of plastic pipes, including:
- Polyvinyl Chloride (PVC)
- Chlorinated Polyvinyl Chloride (CPVC)
- Polyethylene (PE)
- Polypropylene (PP)
- Other extruded profiles
Drawing inspiration from advancements documented in material handling research and patented strapping technologies, this machine optimizes the final packaging steps, transforming them into a streamlined, unmanned operation.
Advanced Bundling and Strapping Technology
The system initiates by automatically collecting pipes exiting the extrusion line or cooling tanks. Precision sensors and actuators ensure gentle handling to prevent surface damage.
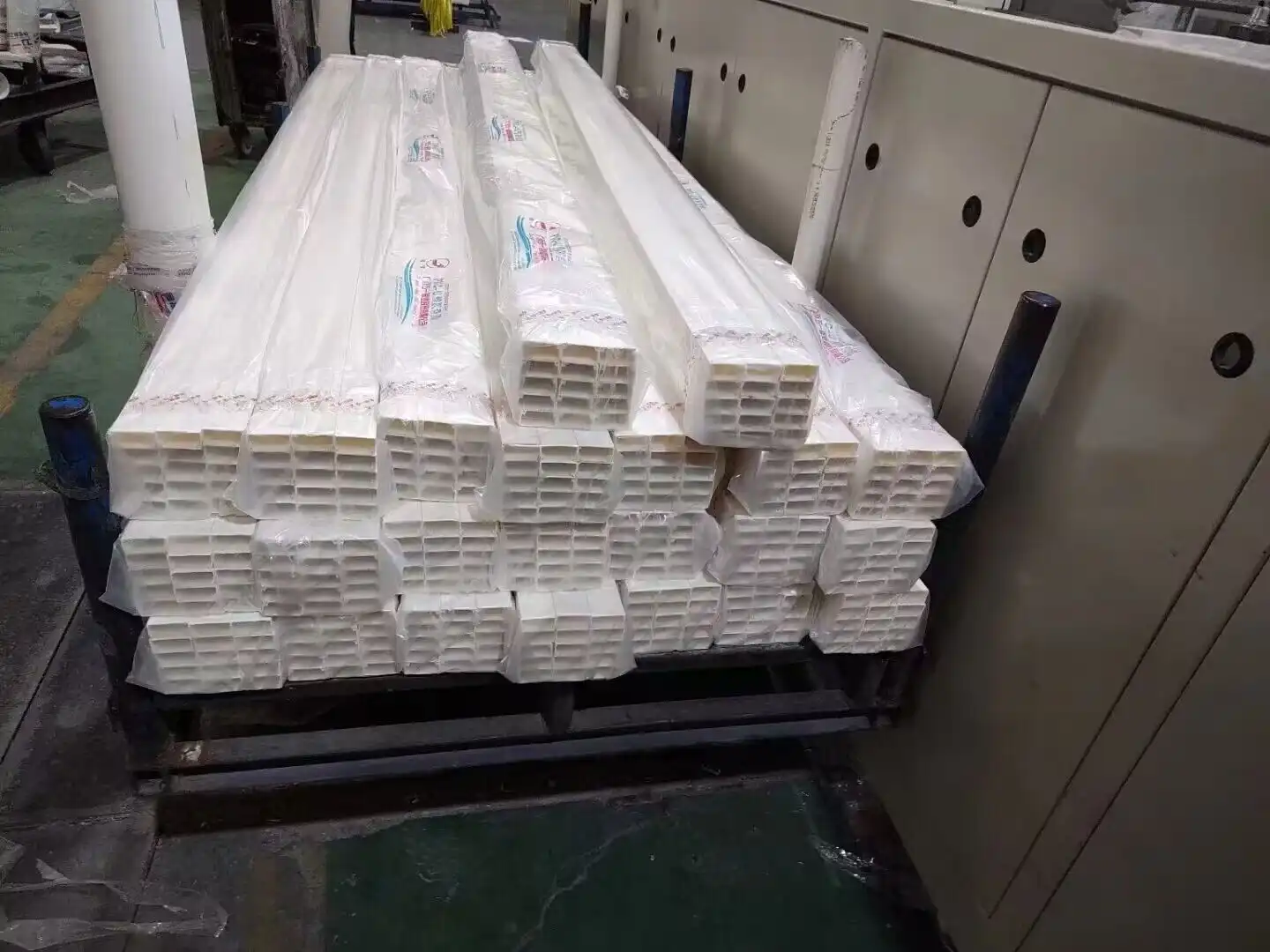
- Bundle Formation: Pipes are collated into pre-defined bundle sizes and shapes (e.g., hexagonal, square). Advanced control algorithms ensure consistent bundle integrity.
- Strapping Mechanism: Incorporating technology similar to that highlighted in recent packaging industry publications, the machine utilizes durable strapping materials (typically Polypropylene or PET). The strapping head applies consistent, precisely controlled tension, securing the bundle without distorting or damaging the pipes. This aligns with findings in material science papers discussing stress limits for various polymers.
- High Throughput: Engineered for performance, the system achieves high cycle rates, capable of processing significant linear meterage of pipe per hour, synchronized with typical extrusion line speeds. Industry benchmarks often cite automated strapping as reducing cycle times by 30-50% compared to manual methods.
Seamless Automated Bagging Module
Following the bundling and strapping phase, the system transitions the secured pipe bundles to the automated bagging station.
- Bag Management: The machine manages a supply of pre-made bags (materials can include heavy-duty polyethylene film, woven PP, or other specified materials based on transport and storage requirements). Research in logistics emphasizes the importance of weatherproof packaging for maintaining product integrity during shipping.
- Automatic Insertion & Sealing: The bagging unit automatically selects, opens, and positions a bag before gently inserting the pipe bundle. Subsequently, the bag is securely sealed (e.g., via heat sealing or stitching), providing environmental protection and containment. This process mirrors automation strategies discussed in publications like Packaging Digest and MM MaschinenMarkt.
- Inline Integration: Designed as an inline solution, the entire process occurs without manual intervention, directly receiving bundles from the strapper and discharging packaged bundles onto accumulation or conveying systems.
Technical Specifications Overview
While specific configurations vary based on customer requirements, typical parameters include:
- Pipe Diameter Range: 16mm – 160mm (customizable ranges available)
- Pipe Length: Standard 3m, 4m, 6m (adaptable)
- Bundle Size: Adjustable based on pipe diameter and customer needs
- Strapping Material: PP or PET strap
- Bagging Material: PE film, Woven PP bags, etc.
- Control System: PLC control with HMI touchscreen interface
- Integration: Profibus/Profinet/Ethernet IP for communication with upstream/downstream equipment
- Power Requirements: Specified based on configuration
- Operating Speed: Synchronized with extrusion line output, capable of handling high production volumes.
Key Advantages and Operational Benefits
Implementing the FHOPE automated pipe packaging system offers significant advantages, often discussed in manufacturing efficiency studies:
- Reduced Labour Costs: Eliminates manual handling, strapping, and bagging, allowing personnel reallocation to higher-value tasks.
- Increased Throughput: Continuous, automated operation prevents bottlenecks and matches high-speed extrusion outputs.
- Improved Package Quality & Consistency: Precise, repeatable bundling tension and secure bagging protect products and enhance brand presentation.
- Enhanced Safety: Reduces risks associated with manual handling of heavy or awkward pipe bundles.
- Material Optimization: Automated control minimizes strap and bag material wastage.
- Data & Integration: Modern control systems allow for data logging, performance monitoring, and integration into plant-wide SCADA or MES systems, aligning with Industry 4.0 principles often featured in MM MaschinenMarkt.
Applications
This automated packaging solution is ideally suited for manufacturers and large-scale distributors involved in the production of:
- Plumbing and drainage pipes (PVC, CPVC)
- Conduit pipes (PE, PVC)
- Irrigation pipes (PE)
- Industrial piping systems
Conclusion
The FHOPE automatic online plastic pipe bundling and bagging machine represents a significant technological advancement for plastic pipe manufacturers seeking to optimize end-of-line operations. By integrating proven technologies highlighted in industry research and patents, this system delivers substantial improvements in efficiency, consistency, cost-effectiveness, and safety, positioning manufacturers for greater competitiveness in the global market. It provides a reliable, high-performance solution aligned with the automation trends shaping modern industrial production.