Mastering Coil Handling: A Deep Dive into the 90-Degree Coil Tilter with Rotatable Base
In modern manufacturing and logistics, the efficient and safe handling of heavy materials like metal or paper coils is paramount. Manually maneuvering these bulky items poses significant risks to personnel and can lead to product damage. The 90-degree coil tilter, particularly one equipped with a rotatable base, emerges as a sophisticated engineering solution designed to streamline these operations. As demonstrated in the video above, this machine offers precision, safety, and versatility in coil repositioning.
1. Understanding the 90-Degree Coil Tilter's Functionality
At its core, a 90-degree coil tilter, also known as a coil upender or downender, is specialized material handling equipment designed to safely tilt coils between horizontal and vertical orientations. This capability is crucial for various stages in production, storage, and transportation, such as preparing coils for slitting lines, packaging, or palletizing.
The addition of a rotatable base significantly enhances its utility. This feature allows the entire tilting structure, along with the loaded coil, to be rotated (often up to 360 degrees) around a vertical axis. This eliminates the need for additional equipment or complex maneuvers to align the coil for subsequent processes or for loading/unloading from different directions.
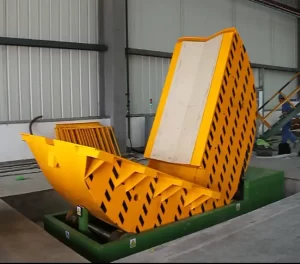
2. Key Design Elements and Structural Components
The effectiveness of this machine stems from its well-engineered design, typically incorporating the following components:
- Robust Tilting Platform: This is the V-shaped or flat saddle where the coil rests. It's engineered to securely hold the coil during the tilting motion, often lined with protective material (like polyurethane) to prevent surface damage.
- Powerful Tilting Mechanism: Usually driven by hydraulic cylinders or electromechanical actuators (like screw jacks), this system provides the force needed to smoothly and controllably tilt loads that can weigh several tons. Precision control ensures gradual movement, minimizing stress on the coil and the machine.
- Integrated Rotatable Base: This turntable mechanism, often gear-driven with a dedicated motor, allows for precise rotational positioning. Its inclusion provides unparalleled flexibility in integrating the tilter into existing production lines or tight workspaces.
- Heavy-Duty Steel Structure: The frame and base are constructed from high-strength steel to withstand the significant forces involved in tilting and rotating heavy loads, ensuring longevity and operational safety in demanding industrial environments.
- Advanced Control System: Operators typically interact with the machine via a pendant control or a fixed control panel. Modern systems include features like variable speed control, soft start/stop functions, and crucial safety interlocks (e.g., preventing rotation during tilting).
3. Technical Specifications Overview
While exact specifications vary based on application requirements, here's a typical range for industrial-grade 90-degree coil tilters with rotatable bases:
- Load Capacity: 1 Ton - 50+ Tons (Tailored to specific needs)
- Tilting Angle: 90 degrees (Fixed)
- Rotation Angle: 0 - 360 degrees (Continuous or indexed)
- Platform Dimensions (L x W): Customizable (e.g., 1200mm x 1200mm to 2500mm x 2500mm or larger)
- Tilting Time: Approximately 40 - 120 seconds (Depending on load and power unit)
- Rotation Speed: Approximately 1 - 3 RPM
- Power Requirements: Typically 380V/415V, 50/60Hz, 3-Phase Industrial Power
- Control Method: Remote Pendant Control / Integrated Control Panel
- Safety Features: Limit switches, emergency stops, hydraulic locking valves, optional safety barriers or light curtains.
4. Operational Workflow and Personal User Experience Insights
Operating the coil tilter typically follows a straightforward process:
- Loading: The coil is placed onto the tilting platform using a forklift, crane, or coil car. Proper positioning is crucial.
- Securing (if applicable): Depending on the design and coil type, securing clamps might be engaged.
- Tilting: The operator initiates the tilting cycle via the control panel. The machine smoothly tilts the coil by 90 degrees.
- Rotating: If orientation change is needed, the operator uses the controls to rotate the base to the desired angle.
- Unloading: The reoriented coil is safely removed using appropriate handling equipment.
Personal Observations: Having observed these machines in operation, the key advantages from a user perspective are the smoothness of motion and the intuitive controls. The rotatable base is a game-changer in facilities with complex layouts or multiple process entry/exit points. It drastically reduces the need for forklift repositioning, saving time and reducing traffic in busy areas. Operator training focuses heavily on load centering and awareness of the machine's operational footprint for maximum safety. The reduction in manual handling effort is immediately apparent and significantly contributes to a safer work environment.
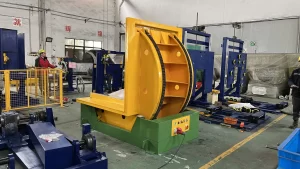
5. Applications Across Diverse Industries
The versatility of the 90-degree coil tilter with a rotatable base makes it invaluable in sectors including:
- Steel and Aluminum Mills: Handling raw and processed coils.
- Metal Service Centers: Repositioning coils for slitting, cutting, or distribution.
- Paper Mills: Managing large paper rolls.
- Cable and Wire Manufacturing: Handling large spools.
- Automotive Stamping: Positioning steel coils for press lines.
- Printing Industry: Handling rolls of printing material.
6. Core Benefits for Operations
Investing in this type of equipment yields tangible benefits:
- Enhanced Safety: Dramatically reduces risks associated with manually tilting or flipping heavy coils.
- Increased Operational Efficiency: Speeds up handling processes and reduces cycle times compared to traditional methods (e.g., using cranes with C-hooks).
- Improved Product Quality: Minimizes damage (dents, scratches) that can occur during manual handling or less controlled tilting.
- Optimized Workflow Flexibility: The rotatable base allows seamless integration into diverse production layouts and facilitates multi-directional loading/unloading.
- Reduced Labor Costs: Less manual intervention required for coil orientation.
- Space Optimization: Can contribute to more efficient use of floor space compared to maneuvering coils with forklifts or cranes alone.
7. Conclusion: A Strategic Asset for Modern Industry
The 90-degree coil tilter with a rotatable base is more than just material handling equipment; it's a strategic asset for industries dealing with heavy coils. By combining robust engineering, precise control, and enhanced flexibility through rotation, it directly addresses critical challenges related to operational efficiency, workplace safety, and product integrity. For any organization looking to optimize its coil handling processes, understanding the capabilities and benefits of this specialized machine is a crucial first step towards a safer and more productive future.