Understanding the Yellow Jacket Pallet Orbital Wrapper: Features and Operation
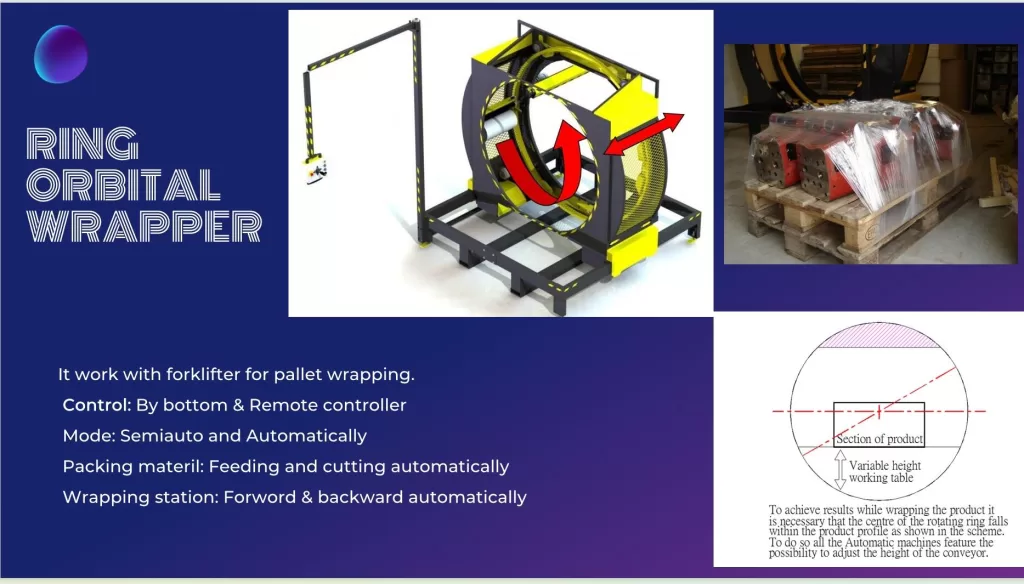
1. Introduction to Orbital Wrapping Technology
Securing palletized loads effectively is crucial for safe transport and storage, minimizing product damage and associated costs. Orbital stretch wrappers offer a robust solution by applying stretch film horizontally around the load, including underneath the pallet skids, creating a secure cocoon that binds the load to the pallet. The Yellow Jacket Pallet Orbital Wrapper is engineered for user-friendliness and operational efficiency, providing reliable load containment. This CE-certified machine ensures adherence to quality and safety standards.
2. Operational Workflow: Step-by-Step Guide
The Yellow Jacket wrapper integrates seamlessly with standard warehouse operations, particularly those involving forklifts. Here’s a breakdown of the wrapping process:
- Load Pallet: Utilize a forklift to position the palletized load onto the designated wrapping area within the machine's structure. The design facilitates easy loading without manual lifting.
- Initiate Wrapping Cycle: Activate the wrapping sequence using the intuitive control interface (touch panel or remote controller). The machine performs an initial check to confirm correct pallet placement before proceeding.
- Automated Wrapping: The orbital ring dispenses and applies stretch film horizontally around the pallet and load. The process is automated for consistent tension and coverage, optimizing film usage.
- Automatic Film Cut and Clamp: Upon cycle completion, the machine automatically cuts the stretch film and clamps it, preparing for the next cycle without manual intervention.
- Unload Secured Pallet: Use the forklift to remove the fully wrapped and secured pallet from the machine.
3. Key Features and Advantages
The Yellow Jacket Pallet Orbital Wrapper incorporates several features designed to enhance packaging efficiency and ease of use:
- Forklift Integration: Designed to work directly with forklifts for loading and unloading, streamlining the workflow.
- Flexible Control Options: Operable via a user-friendly touch panel or a convenient remote controller.
- Automation Levels: Available in semi-automatic or fully automatic configurations to suit different operational needs.
- Automated Film Management: Features automatic film feeding, cutting, and clamping, reducing operator tasks.
- Adaptive Wrapping Station: The wrapping mechanism automatically adjusts its position (forwards and backwards) to accommodate varying pallet dimensions, eliminating the need for manual reconfiguration between different load sizes. This enhances versatility and throughput.
- CE Certification: Meets European standards for safety, health, and environmental protection.
4. Conclusion: Enhancing Packaging Operations
The Yellow Jacket Pallet Orbital Wrapper provides a practical and efficient solution for securing palletized goods. Its user-friendly design, combined with automated features and the flexibility to handle various pallet sizes, makes it a valuable asset in logistics, warehousing, and manufacturing environments. By ensuring loads are tightly and securely wrapped, it contributes to reduced product damage during handling and transit, improving overall operational efficiency.
5. Additional Orbital Wrapper Resources
For visual demonstrations and further information on orbital wrapping technology, explore the following resources:
- Orbital Wrapper General Video
- Horizontal Wrapper for Large Objects
- Horizontal Wrapping with Bottom Timber Support
- Wood Timber Wrapping & Strapping Machine
- Automatic Horizontal Stretch Wrapper for ODM
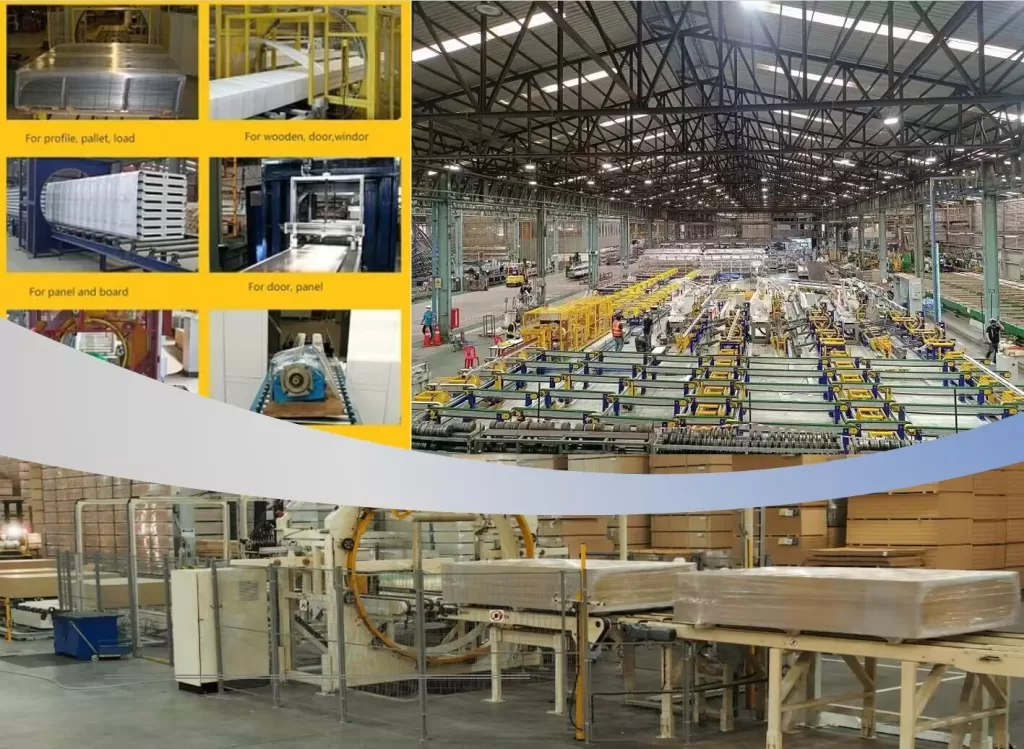